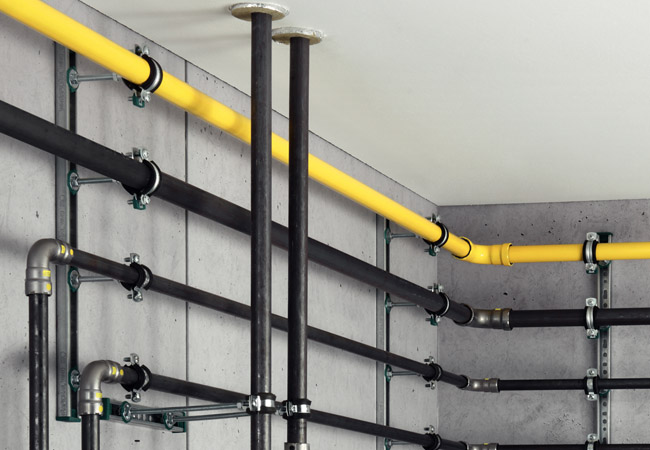
While the focus is often on the quality of installation, the test and commissioning of a system is just as important. Detecting issues with pipework at this stage is crucial, as is ensuring the system remains contaminant free.
As the presence of static water in the system can cause serious contamination it is always advisable to avoid filling the system until the building will be occupied. In addition, pipework that is filled and then drained is more susceptible to corrosion with the potential for long-term issues.
Therefore leak testing with water should only be considered if the system will be made operational immediately and any flushing of the system should take place as close to the handover of the building as possible.
For these reasons, it is recommended that dry testing is utilised where possible. To dry test a system, the pipework should be pressurised with air up to 110 mbar for a defined time. The length of the test depends on the volume of the pipework. For 100 litres of capacity the test should last at least 30 minutes and increase by 10 minutes for every additional 100 litres. If there is a leak, a recordable drop in pressure will occur across the system.
However, the selected of pipe connection method may have an impact on the effectiveness of the testing. A poor-quality joint, either caused by inadequate soldering or an inferior component, may initially hold during testing only to fail later once the building is in use.
Here, press connection technology offers an advantage as the quality of the joint does not vary and once a fitting has been pressed it forms a strong, secure connection. Nonetheless, it is important to select a system that is specifically designed to reliably reveal unpressed connections.
For example, Viega’s SC-Contur technology incorporates a flowpath channel, which is proven to deliver a 100% positive leak during testing if the fitting is left unpressed. It ensures that water will visibly escape from unpressed connections at the full range of pressures between 1 bar and 6.5 bar.
For dry testing with inert gas a measurable drop in pressure will occur between 22 mbar and 3 bar. Where a missed joint is detected, press connections make it simple to correct as there is no need to dry or prepare the joint and it can be pressed immediately.
However, water within the pipework is not the only potential cause of contamination. Any equipment installed as part of the system may represent a possible issue if not handled correctly. For example, wet leakage tests during manufacture can introduce bacteria and allow them to grow, especially if the product is stored in a warm environment.
The optimal breeding temperature range for bacteria such as Pseudomonas Aeruginosa and Legionella Pneumophila is between 25°C and 45°C and once bacteria are established in the system it can be difficult to remove. An example of this is a clinic where the drinking-water installation has had to be continually disinfected with chemicals since 2006 because the newly installed pressure-booster system was contaminated with Pseudomonas Aeruginosa bacteria.
Finally, for large buildings it is often an advantage to divide the pipework into sections to allow areas or floors to be isolated in an emergency or when maintenance and repairs are required. This also has benefits for installation, testing and commissioning as carrying out testing and installation concurrently allows improvements and adjustments to be made to the methodology if issues arise.
Also by keeping the capacities of each section limited, it makes testing more manageable and allows the source of any leaks to be identified easily.
Establishing a robust testing and commissioning process will not only ensure that any issues are detected before the project is complete but will also help protect the system. High-quality press connection solutions can contribute to the efficiency of the process as well as ensuring a quick, clean and reliable installation.
For further information about Viega’s range of solutions visit: www.viega.co.uk