Corrosion in pipework
Pipework corrosion will be caused by oxygen in the presence of water and can be accelerated through galvanic action. If the water contains dissolved salt or is acidic (that would include acid rain), then corrosion will be exacerbated.
Carbon steel and stainless steel contain iron, which, in the presence of oxygen – in both water and ambient air – oxidises, creating rust. The added chromium in stainless steel makes it more corrosion-resistant than carbon steel by producing a thin passive layer of oxide on the surface that prevents further corrosion. Carbon steel does not typically have enough chromium to form this chromium oxide layer, allowing oxygen to bond with the iron, resulting in iron oxide, or rust. However, the cost of billets of stainless steel is approximately five times that of carbon steel, so the use of stainless pipework is typically restricted to specific applications, such as drinking water services or for hygiene-controlled areas.
Steel
Steel is an alloy made from iron and carbon. The percentage by weight of carbon determines the potential strength and ductility of the steel. Other elements, such as tungsten, chromium, cobalt, manganese and molybdenum may also be used as alloys, but in the standards that define ‘carbon steel’, that is also known as ‘mild steel’; the amount of carbon is the key factor, and the amounts of other alloying elements are not specifically defined. As the carbon percentage content rises, steel becomes harder and stronger (with heat treatment), but it also becomes less ductile. Steel with a higher carbon content is less suitable for welding, as the higher carbon content lowers the melting point. Carbon steel for HVAC pipework is typically ‘low carbon’ steel that contains up to 0.3% carbon.
Stainless steel is iron alloyed with a minimum of 10% chromium as well as smaller amounts of other alloys.
A galvanic cell results when two physically connected dissimilar metals are placed in an electrolyte (such as water). Figure 1 shows the electrode potential of metals when in seawater. The potential difference between two metals is the driving force for an accelerated attack on the anode metal, which dissolves into the electrolyte. Metals that are more anodic (towards the top of the chart) will corrode more easily and the metals that are more electronegative – or cathodic – are more resistant to corrosion.
An electrolyte is a solution that contains ions so that it will conduct electricity. Pure water is a weak electrolyte and a very poor conductor, whereas seawater – which contains almost 4% common salt – is a strong electrolyte. As explained more fully by Sperko,1 the fluid conductivity heavily influences the overall corrosion rate. Condensation that collects on the outside surface of a chilled water line inside a building is typically a comparatively low conductivity fluid, so the corrosion rate caused by condensation on the outer surface of an unprotected metal couple in such a pipe will be low. That same condensate on an outdoor pipe in an industrial or coastal environment will be contaminated with salt or chemicals and become highly conductive; not only will a couple corrode at a greater rate, but also the pipe will rust. The farther apart the two metals are on the chart, the greater the reaction to cause corrosion in the more active metal.
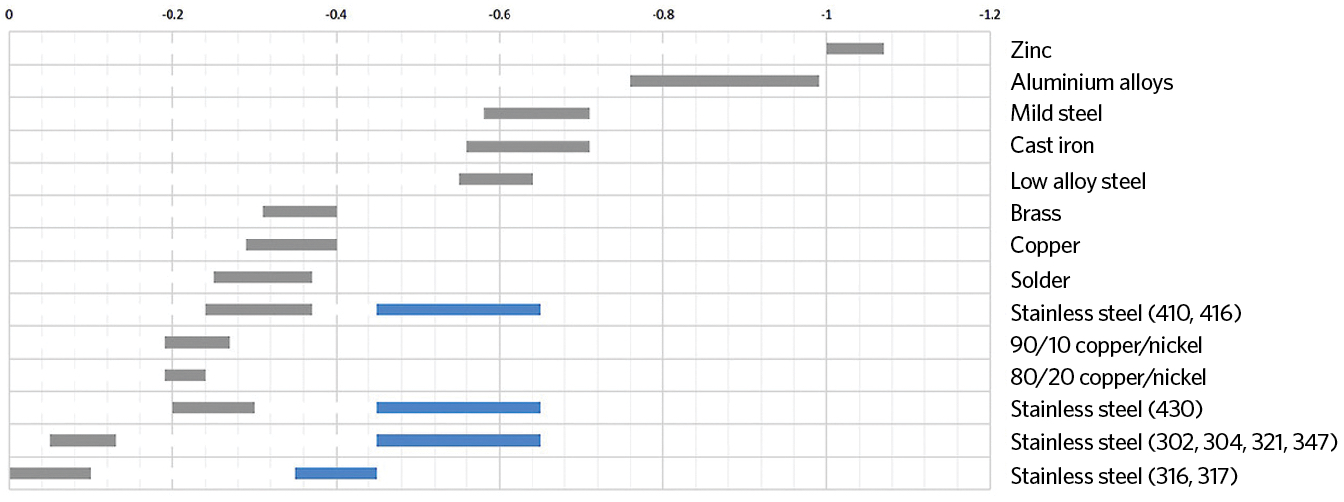
Figure 1: The electrode (galvanic) potential of metals in seawater
Metals close to each other on the scale are safer to use together. The grey bars are the ‘normal’ state of the metal, while the blue lines are where a metal is ‘active’. An ‘active’ variant of a metal shifts position on the galvanic scale, making it more anodic. So, for example, carbon-steel systems with a high proportion of copper can lead to increased galvanic corrosion. As carbon steel is more anodic, the corrosion will be seen here instead of on the copper. However, substituting carbon steel for other materials, such as grade 316 stainless steel, can move the potential problems to a different part of the system. In a system made from mild steel, any free oxygen from the initial fill water is quickly absorbed (as corrosion) into the steel. Removing carbon steel from the pipe system means that the oxygen will react elsewhere.
Thin-wall welded steel piping and press-fittings
Welded pipe is formed by rolling carbon-steel strips through a series of grooved rollers that mould it into a circular shape. The ring of pipe is then passed alongside welding devices that complete the seam. Welded pipe is cheaper than extruded pipe, but its inherent strength is formally taken as being about 20% less (as required by standards). There is little else to choose between modern, good quality welded pipe and extruded pipe, since a quality controlled welded production will effectively produce a completely homogenous tube. Poorer quality tubing can suffer from poor bead removal and finishing (causing dimensional irregularities), as well as pitted seams or inappropriate fill materials that exacerbate risks of corrosion.
Carbon-steel pipes are available in many wall thicknesses at the various nominal sizes. Those with a thinner wall thickness provide lightweight systems that employ less material and are easier to install but, since there is less material in the pipes’ structure, can be more readily perforated where they are not installed or operated appropriately (through corrosion or other physical damage). Such thin-wall pipe – which has a wall thickness of about half that of EN 102552 type L2 ‘light’ pipe – is often joined using roll-grooved or press-fit type fittings that maintain a water seal using captured O-rings. Thin-wall pipe is available with external and internal zinc coatings (created through electroplating), which prevent corrosion of the steel by forming a barrier and acting as a sacrificial anode if that barrier is damaged. (See Sperko’s article1 for more details on protective coatings.) Thin-wall piping is also available with external polypropylene coating to prevent corrosion from ambient moisture and oxygen.
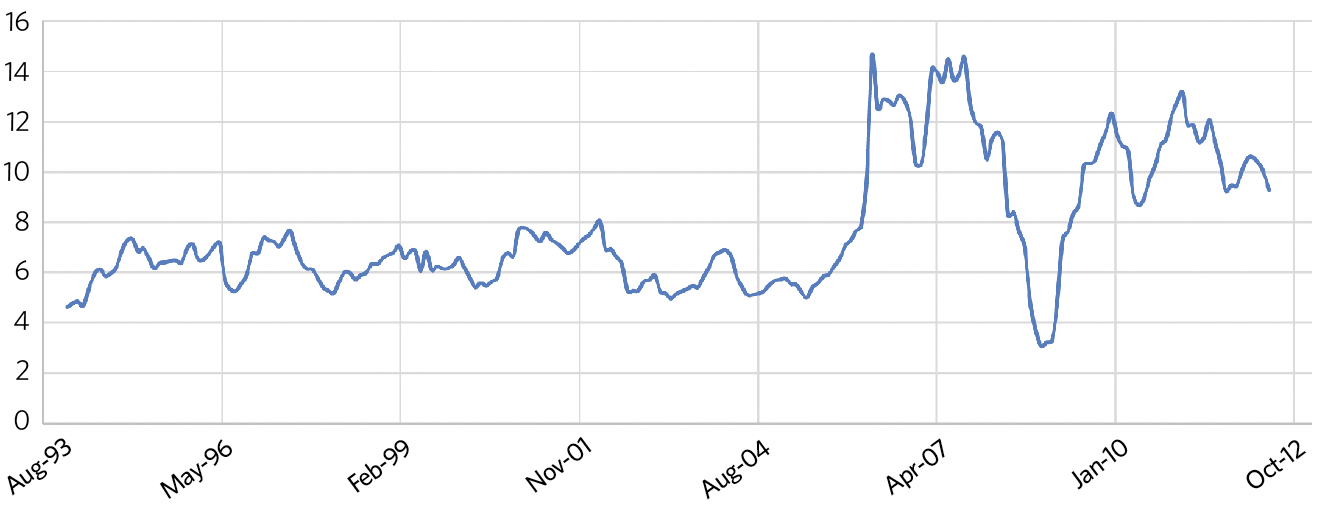
Figure 2: The relative price of copper compared with steel (price of copper divided by steel)
The press-fitting jointing system was initially developed in the 1950s for copper pipes, but it was slow to gain initial acceptance as, reportedly, the trade was reluctant to trust a method of connection that did not involve heat. However, a commercial product was established in the late 1960s, and systems were developed to use with copper, carbon-steel and stainless-steel pipes.
As shown in Figure 2, copper prices increased sharply in 2006 compared with those of steel. Those who had already become experienced in specifying and employing press-fittings on copper pipe (particularly in northern Europe) provided a keen base to use similarly speedy methods with thin-wall carbon-steel pipework. However, unlike copper, there is a more immediate risk of corrosion in steel pipework systems when they are not installed and operated with appropriate care.
Installation and operation of thin-wall carbon-steel pipework systems
Information on how to handle, install and operate thin-wall carbon-steel systems is (and was) readily available from both manufacturers and in industry standard guidelines. But the lack of experiential knowledge meant application and design have not always taken this into consideration. In the post-recession marketplace, carbon-steel sales continued to grow as the industry recovered and businesses re-established. Reportedly, the material was applied inappropriately – being installed outside buildings, in open systems and with excessive water treatment.
An infamous example of the problems arising from inappropriate application is the critical care building at Royal Victoria Hospital in Belfast, Northern Ireland, which was set to open at end of the 2012. Following the £150m investment, reports3 indicated that corroded pipes had delayed the construction project and contractors had to rectify the problem. This led to suspension of the project (the building is still not in full use) and added significant costs – as well as publicising a high-profile ‘failure’ of the ‘new’ press-fitting technology.
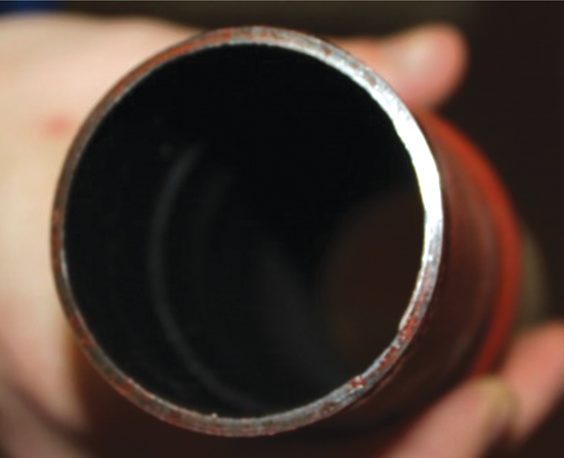
Figure 3: A sample of the thin-wall carbon sampled from the 12-year-old installation at the Mater Hospital (Source: Geberit)
The ensuing bad publicity effectively caused a hiatus in the application of press-fit thin-wall carbon steel in Northern Ireland. However, less than two miles away from the problems at the Royal Victoria Hospital, a 12-year-old press-fit installation was inspected at the Mater Hospital. Here, in comparison, all samples of the polypropylene-coated thin-wall carbon pipework installation were found to be corrosion free, as illustrated in the sample in Figure 3.
Thin-wall carbon-steel pipework should only be used in closed water systems with closed expansion tanks and appropriate venting – it should not be employed where it is unprotected and so exposed to weather. In a closed system, the free oxygen in the initial fill of water will be used up in initial light rusting on the internal surfaces and, as long as that water is not replaced, there should be no source of additional free oxygen. As discussed by Munn,4 there are three main ways oxygen can enter a closed water system:
- From aerated water – initial water fill, flushing or fresh make-up water during operation
- From pressurisation problems – negative pressures at the top of systems results in air being drawn in through air admittance valves (AAVs) or seals
- From oxygen diffusion – through the use of non-barrier plastic pipework or inappropriately open cisterns.
The pipework systems should be installed in accordance with the manufacturers’ guidelines by properly trained operatives. The guidance published in BSRIA BG 29/12 Pre-commission cleaning of pipework systems and BSRIA BG 50/2013 Water treatment for closed heating and cooling systems provides key rules that set the systems ready for a potentially long and effective operational life.
Pre-installation pipework and fittings should be protected from moisture and the influence of weather so, for example, it should not be stored directly on the ground, and should be kept under cover when being transported, with protective endcaps remaining on system components until immediately before use. Pipes of dissimilar metals should be stored separately to avoid contact corrosion, and parts of pipe with visible red rust should not be used.
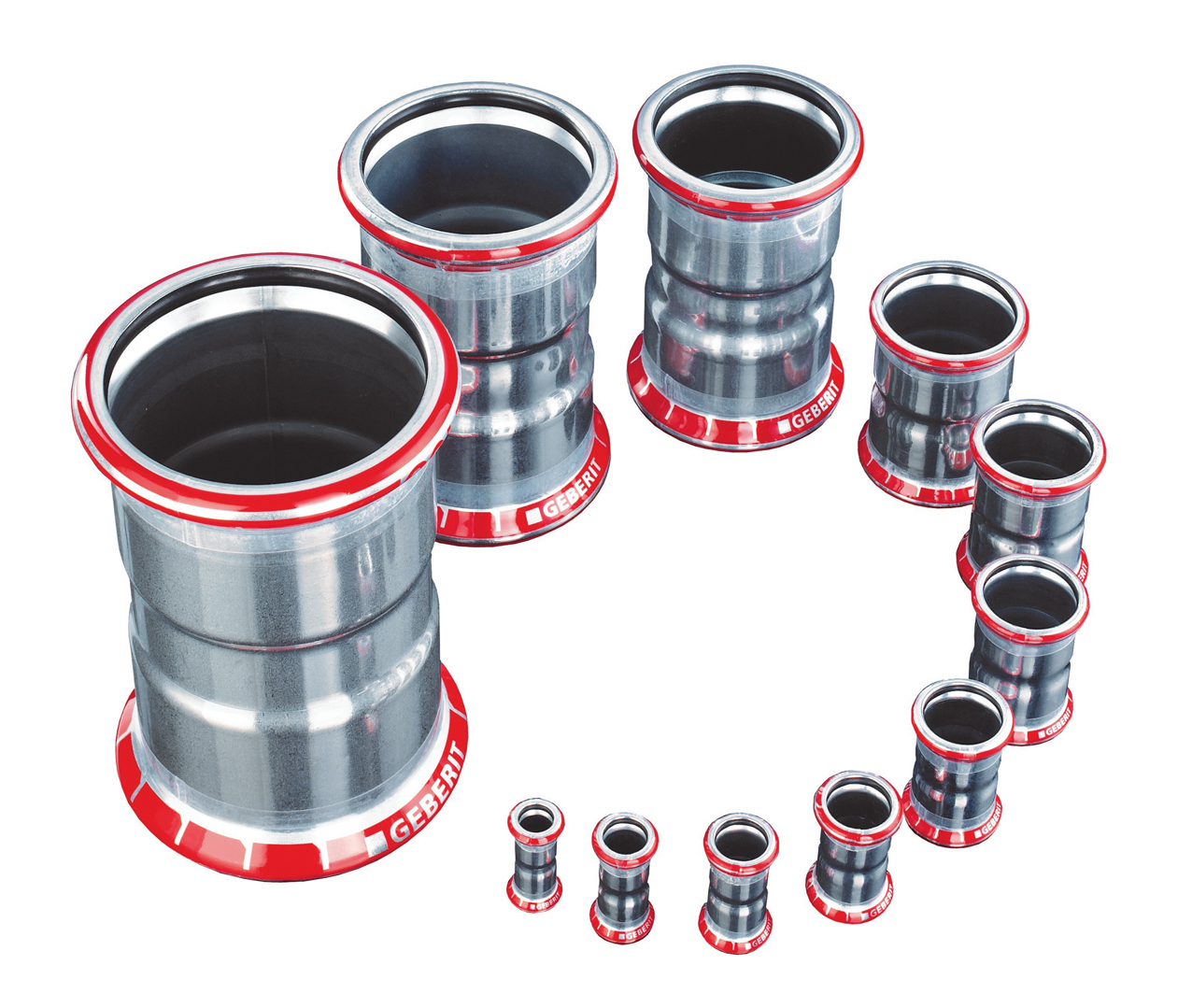
Examples of low carbon steel press-fittings (Source: Geberit)
The outside of installed pipes should be appropriately protected not only thermally, but also to resist the diffusion of moisture from the atmosphere that would cause condensation on pipework surfaces that are below the dewpoint temperature.
Manufacturers5 recommend pressure testing with compressed air. However, when testing with water, the correct water quality should be used, and then the systems should preferably be left filled. If unavoidable, refilling should be performed as quickly as possible – preferably within 24 hours. It is important that the building operator is properly trained and understands about possible causes of corrosion and how to avoid them. For example, the systems should be operated at appropriate pressures so that water is not regularly released through pressure-release devices and then replenished with fresh water when the system pressure reduces.
Monitoring for longevity
The rate of corrosion and risk of failure depends on a variety of factors including the chemical and microbiological environment, temperature, flowrate and not least the thickness of the metal.6 Therefore, as well as ensuring appropriate installation techniques, proper maintenance and monitoring is required. Two current tests are typically employed – ultrasonic thickness tests and manual sampling. Ultrasonic thickness tests are useful in determining the current condition of the system but only give a snapshot of the system at that moment. Without regular repetition, finding a problem before it develops into a major failure may simply rely on good fortune. Manual sampling techniques that may be conducted every few months will not necessarily give enough data to understand trends in the system.
Water-monitoring systems are now well established and, with new technologies being developed, the real price of such systems is reducing. As discussed (and detailed) by Munn,4 such systems can check continuously on engineering aspects, water characteristics and corrosion rates. Water monitoring should not be considered simply as a retrofit once a system has gone awry, but properly included as part of the initial design.
References:
- Sperko, WJ, Dissimilar metals heating and AC piping systems, CIBSE Journal, October 2015.
- BS EN 10255:2004 Non-alloy steel tubes suitable for welding or threading.
- Pipework problems delay £150m critical care hospital unit in Belfast, BBC News, accessed 10 August 2018.
- Munn, S, Testing the water – tackling corrosion in pipework, CIBSE Journal, September 2016.
- Geberit CPD presentation Precision carbon steel: how to stop the rot – truth or rumour? – viewed August 2018.
- The hidden menace of corrosion in heating and cooling systems, BSRIA, accessed 10 August 2018.
© Tim Dwyer, 2018.