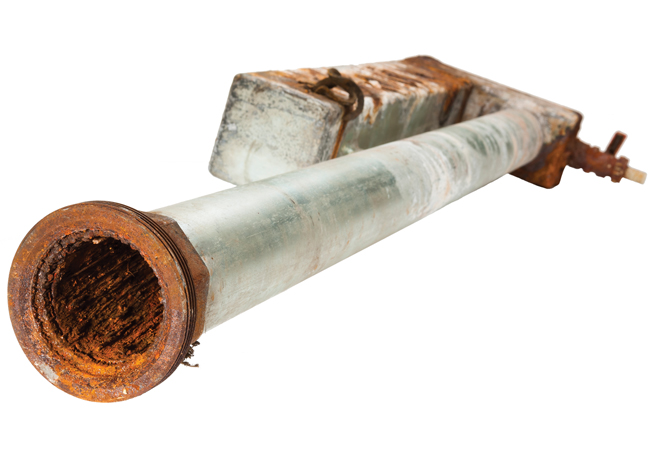
Corroded system parts
Corrosion can have a damaging impact on commercial heating systems, unless there is a comprehensive water-treatment programme in place. Magnetic filters should be part of this strategy because they capture the metal – or magnetite – by-product of this corrosion, which occurs when water circulates through boilers and pipework.
Making up 98% of system debris, magnetite particles can be very small, measuring just eight microns (0.008 mm) in diameter, which makes capture difficult. Their size means they can travel easily around a heating system; particles are deposited in low flow areas, such as heat exchangers, baseboards and radiators. If sludge accumulates in the radiators, it can limit heat output and circulation and, if trapped in the boiler or central heating pump, it can lead to outright failure.
Traditional cast-iron boilers have been replaced by more efficient stainless steel and aluminium models, over the last ten years. The newer boilers cannot match the durability of cast-iron units, unless proper protection is in place. They are smaller in size so heat cells are more prone to magnetite blockages, while the waterways – reduced from 50-60mm to as small as 8mm in some cases – are also susceptible to blockage.
Historically, dirt and air separators have offered protection for commercial systems. However, the mesh used is not fine enough to capture small magnetite particles, leaving sludge to circulate round the system.
As the name suggests, magnetic filtration has magnets at its core – these are usually powerful neodymium magnets that are tolerant to high temperatures. They attract all particles, regardless of size, to the core of the filter, ready for collection and removal.
If sludge accumulates in the radiators, it can limit heat output and circulation, and lead to outright failure
Available in different sizes, depending on system dimensions, the filter can be fitted to the pipework of new and retrofitted heating systems. It will need to be monitored, emptied and serviced, as the sludge collects around the magnets. Some filters offer greater flexibility, with side stream and inline installation possible.
The first step in fitting magnetic filters is to clean the system with a appropriate chemical cleaner that will dislodge any sludge and make it easier to collect. A magnetic filter is then installed, which collects the sludge. This should be serviced once a year to clean the magnets and check performance. A chemical inhibitor should then be added to help protect against corrosion and limescale deposits, before a water test is carried out, with options available for chemical and microbiological testing. Specialist, commercial water-testing services enable engineers to do this easily. It is important to use a UKAS-accredited laboratory and to ensure compliance with the latest BSRIA guidance on closed heating and cooling systems.
System maintenance is essential to ensure it stays correctly dosed (it might need a chemical top-up) and that the filter continues to perform effectively. Some filters include a small sight-glass, which makes it easy to see how much sludge has been collected and whether it needs emptying.
Magnetic filters are proven to be 10 times more effective than traditional filters. Adey is awaiting verification from Gastec on tests that compare capture rates between a commercial magnetic filter and a dirt and air separator of the same size. The test was carried out over a two-hour period and at a constant flow rate of 60m2·h-1. The results showed that the magnetic filter collected 3.29kg of sludge, while the dirt and air separator collected just 0.53kg.
University College London (UCL) is installing magnetic filtration in as part of its boiler-replacement programme. Currently more than 60 commercial filters have been installed ranging in size from 2 to 6in. It had previously had a damaging buildup of black iron-oxide sludge, which had affected water quality and led to cracked casing and heat exchangers. Now, the sludge is collected and removed, which will save UCL time and money in expensive repairs in the future
Keith Thompson is commercial sales director at Adey