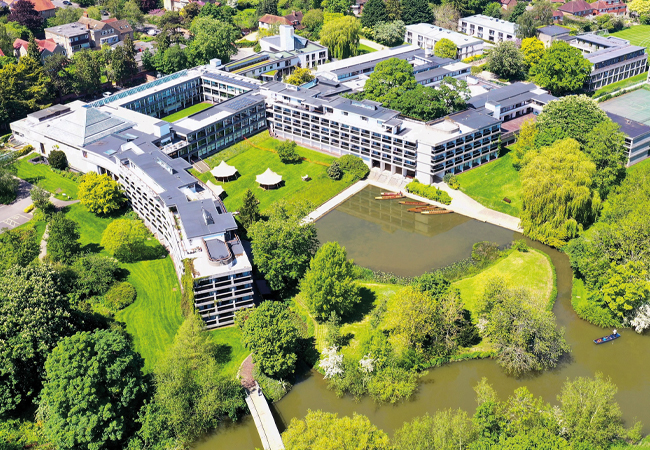
Wolfson College, Oxford
As we strive for decarbonisation of heating and the mass adoption of heat pumps in the UK, it is essential that they are engineered properly.
Ideally, the net zero and decarbonisation heat agenda would depend on sustainable, natural refrigerants rather than synthetic refrigerants, especially in the world of high-capacity heat pumps. There are several natural refrigerants to choose from, including ammonia, the hydrocarbons, and carbon dioxide (CO2). These can cover virtually all applications, but – as with every refrigerant – it is critical to match a refrigerant’s strength to the application.
CO2 as a refrigerant is now a mainstream technology. It is non-toxic and non-flammable, and has a global warming potential of 1, which – combined with its thermodynamic properties – make it a strong contender for higher refrigerant charge applications, such as air source heat pumps (ASHPs), where multiple heat sources feed into a heat network.
Wolfson College, Oxford has taken delivery of two industrial, transcritical CO2 ASHPs that supply 350kW of heating each. Each heat pump sources heat from two fan-powered evaporators located in an open-sided car park, while the heat pumps are in a traditional plantroom.
Max Fordham, the environmental building services engineer who completed the energy audit and decarbonisation plan for the college, established that changing from single glazing and improving insulation will reduce building heat loss by 80%, while replacing gas boilers with CO2 heat pumps will reduce carbon footprint by 75%.
In addition to its sustainability and safety credentials, CO2 is a refrigerant capable of efficiently supplying water at 70°C and above. The ‘transcritical’ CO2 refrigeration cycle delivers heat as the high-pressure, high-temperature refrigerant cools sensibly (as opposed to traditional refrigerants that condense at a lower temperature), and makes a great candidate for retrofitting systems that previously employed traditional heating schemes.
The new heat pumps at Wolfson connect into the original district heating system. However, there have been necessary modifications to adapt the system to efficient heat pump operation, including re-engineering aspects of the heat network to ensure the water return temperatures are significantly lower than they were previously.
Heat pumps become more energy efficient as the inlet (return) water temperature reduces. CO2 heat pumps are no different, and the return temperature must be below 33°C for reasonable efficiency, and lower return temperatures increase efficiency.
The Wolfson project also includes a domestic hot water (DHW) system heated by the CO2 heat pumps. This employs a novel application of buffer tanks, cold mains water and stratification, to optimise efficiency. The heat pumps at Wolfson are engineered with ‘parallel compression’, which reduces the average compression ratio of the compressors and, therefore, the energy consumption.
The six (three per heat pump) compressors are all semi-hermetic reciprocating machines that are largely driven through inverters to enable the heat pumps to dynamically match the given heating demand.
The Wolfson heat pumps are designed for high discharge pressures; the maximum working pressure is 130 bar on discharge side and this pressure is confined to the plantroom. The suction pipework and evaporator devices are rated to 60 bar, while the liquid line is rated to 90 bar, which allows the CO2 heat pumps to ‘stand still’ in the summer months when heating is not required and the heat pumps are inactive.
Source and sink heat exchangers have a fundamental influence on the coefficiency of performance and seasonal energy efficiency ratios, with energy benefits available by maximising the surface area of all heat exchangers. It is a simple equation of capital expenditure versus efficiency and, ultimately, the life-cycle cost.
The evaporators have variable speed airside fan speed, controlled to optimise operating conditions. A bespoke control system, with internet-connected remote access, operates the heat pump and evaporator heat sources, including the defrost systems and integration with the energy meters. Touchscreen interfaces on each heat pump display local operational feedback. The evaporator heat source defrost systems at Wolfson are defrosted using warm glycol; the heat for the defrost is drawn from the return water of the heating network
CO2 can be a natural, long-term, environmentally safe solution when used in high-charge heat pump applications, safely collecting from a site-wide heat source network, and delivering it efficiently to space heating and DHW networks. As a benign refrigerant, CO2 is also not subject to environmental legislation, such as the F-Gas Regulation.
About the author
Daniel Clark is the owner and managing director of Isentra