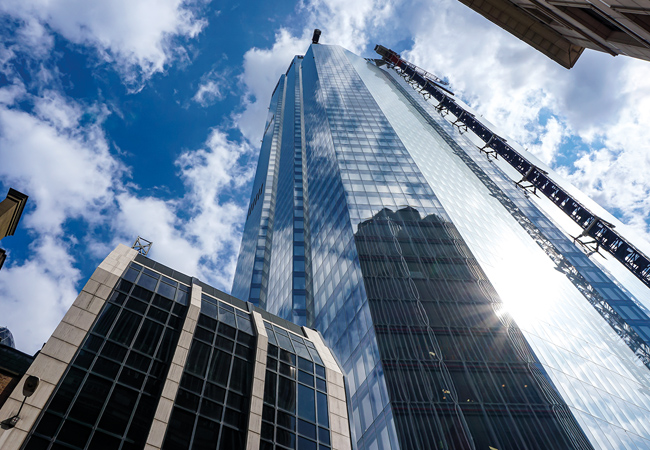
The interest in the effective delivery of heating, ventilation and air conditioning (HVAC) in high-rise buildings has increased in recent years as a result of a combination of coincident issues. This CPD will consider the demand for sustainable tall buildings and will reflect on some of the issues and solutions for supplying chilled water for high-rise developments.
As reported in the CTBUH Journal,1 25 countries completed 200-metre-plus buildings in 2022, and in the UK, the largest number of high-rise projects are in London and Manchester. However, a slowdown in development would not be surprising, owing to a combination of factors created by the pandemic, rising build costs, new safety measures, environmental regulations, and the increased affordable housing obligations of recent years that have imposed greater scrutiny on high-rise development.
Reflecting on 2022 activity for buildings of 20 storeys and over, the 2023 London Tall Building Survey2 reports that this is a time of uncertainty and transition – with higher demands on sustainability. However, the report notes that across London, planning applications that included at least one tall building increased by 72% (to 38) compared with 2021, and planning permissions more than doubled to 20 developments (nine in 2021).
CTBUH1 predicts that globally, at least 155 buildings of 200 metres and higher will complete in 2023, with as many as 205 completing next year, making it likely to be the most prolific year ever for global skyscraper completions.
Buildings that are referred to as ‘tall’ (see boxout ‘How tall is tall?’) have a number of factors that make it challenging to economically create and maintain effective indoor environments that might also be considered sustainable. Stuart Baillie, head of planning at Knight Frank, has remarked2 that energy usage and sustainability are becoming key considerations, and that this ‘can add significant risk to the planning process and cost to the end development. Developers building to invest in a long-term income stream are more likely to buy-in to the sustainability business case.’
How tall is tall?
There is no single standard for designations of high-rise buildings. The Council on Tall Buildings and Urban Habitat (CTBUH)7 has established a convention that is widely adopted.
- Tall – taller than 91m (300 feet).
- Supertall – taller than 300m (984 feet).
- Megatall – taller than 600m (1,968 feet).
To provide some context, the highest UK occupied building, the Shard at London Bridge, is a 72-storey mixed-use high-rise building and, at 309.6m is the UK’s only supertall building. This is often referred to as a ‘skyscraper’ – a term that variously refers to tall buildings over 100m.
Most of the UK’s conurbations are relatively low-rise, where default local planning requirements typically consider buildings that are greater than 18m as ‘tall’. Inner city areas tend to provide more latitude in the definition of ‘tall’, by considering the degree of ‘tallness’ of a building in relation to its context.
Victoria Ormond, head of capital markets research at Knight Frank, recently presented3 the findings of a study into long-term property values in London, UK (related to BREEAM ratings), and Sydney and Melbourne, Australia (related to Nabers ratings), as illustrated in Table 1 and Table 2 (overleaf). The two data sets that considered transactions between 2010 and 2021 were combined, and the data was extensively disentangled from other factors that could otherwise have influenced the property values. Overall, the data suggests that environmentally well-rated buildings provided significant increased value for rental and sales, amounting to rental premia being increased by 3-13% and sales premia by 8-18%.
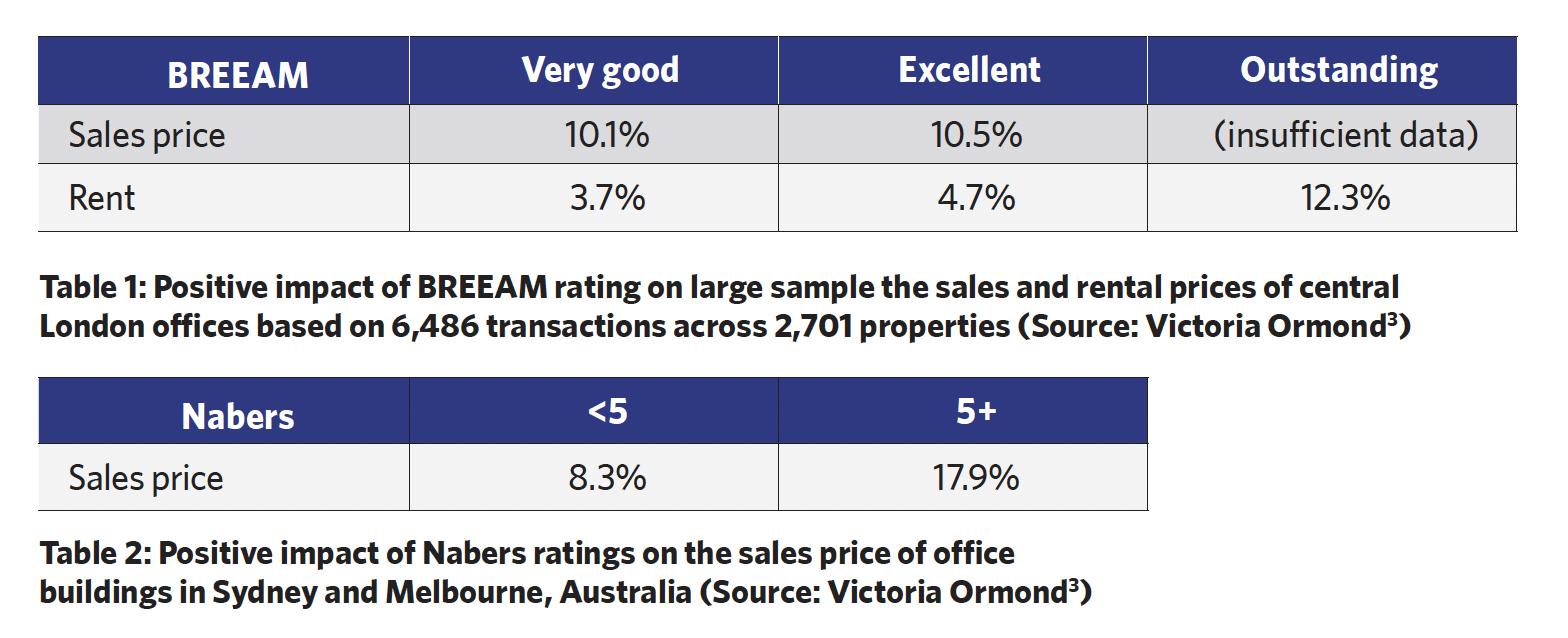
Michael Tobias, founder and principal of New York Engineers, who has extensive experience in global high-rise buildings, writes4 that while an efficient design of HVAC systems minimises costs, the building envelope is also important – an efficient HVAC system reduces heating and cooling costs, but a high-performance building envelope minimises these loads in the first place.
Alongside this, as buildings increase in height, the air pressure differences between the higher and lower floors can make it more challenging to ensure appropriate building ventilation, while the high static head pressures on the heating and cooling services (as well as domestic water, fire and waste water services) will require appropriately considered systems. Reflecting on this, Tobias4 continues: ‘HVAC systems with forced airflow are common in low-rise constructions, but this configuration is unfeasible when long vertical distances are involved. In tall properties, the options are: separating the building into zones with independent HVAC systems, or using centralised equipment with hydronic piping.’
In ASHRAE’s design guide,5 Peter Simmonds notes that in order to minimise plant space, energy usage and resource consumption in high-rise buildings, there are numerous coincident considerations that, in terms of HVAC systems, should aim to maximise reuse of building energy. Where possible, tall buildings should employ passive and renewable technologies, while allowing indoor conditions to fluctuate within comfort limits, and minimise fan and pump energy use, possibly by floor-by-floor service with low-energy terminal devices.
In a paper6 by Mehdi Jalayerian, managing director at Environmental Systems Design in Chicago, which reflected particularly on post-pandemic HVAC system strategies for high-rise office buildings, the author notes that ‘traditionally, many tall office buildings have utilised central air-handling systems with dedicated mechanical floors incorporating large, built-up systems that serve groups of 20 to 30 floors. This approach reduces the mechanical footprint on tenant floors, centralises maintenance, and delivers good energy performance with a cost-efficient HVAC system’.
However, he contends that high-performing buildings should be designed with the flexibility to effectively respond to future pandemics with systems that prioritise occupant health and wellness. Such systems should minimise or eliminate air mixing between floors, optimise ventilation effectiveness within the space, maximise fresh air volume, and provide economiser/purge capability. He says that an effective solution to achieve this high ‘post-pandemic’ standard of ventilation is to employ decentralised air handling units (AHUs) that supply ventilation air to eliminate air recirculation between floors and still enable air heat recovery and purge capability.
In conjunction with underfloor air distribution, this can deliver high ventilation effectiveness and minimum local mixing. This might, for example, take the form of a displacement ventilation system working in conjunction with thermal beams or radiant ceilings.
In ASHRAE’s design guide,5 Simmonds notes that it is a fundamental decision for the entire project team whether air-conditioning supply systems are based ‘centrally’ serving multiple floors or installed in a separate local floor fan room. Tobias4 reflects that chiller and boiler plants with hydronic piping are a cost-effective option for tall buildings, but they have a flexibility limitation, since to deliver simultaneous heating and cooling for different building zones, concurrent cooling and heating requires separate piping.
He notes that there can be advantage in using heat pump systems that can be employed with a common water loop, to allow some zones to provide cooling while others demand heating. The loop temperature is balanced from plant – either chillers and boilers – or by employing centralised heat pumps that exchange heat with the external environment (or, potentially, district energy networks).
The delivery of chilled water will have a significant impact on the capital and operational cost of the built system such as that summarised in the boxout ‘Recent application of chilled water system to a tall building’. (Various possibilities for chilled water systems are explored in detail, complete with extensive examples, in chapter 11 of ASHRAE’s design guide5 – this has been extensively drawn from for this section of the article.) Systems employing centralised chillers will typically employ a cooling tower for the condenser water, rather than a dry or evaporative cooler.
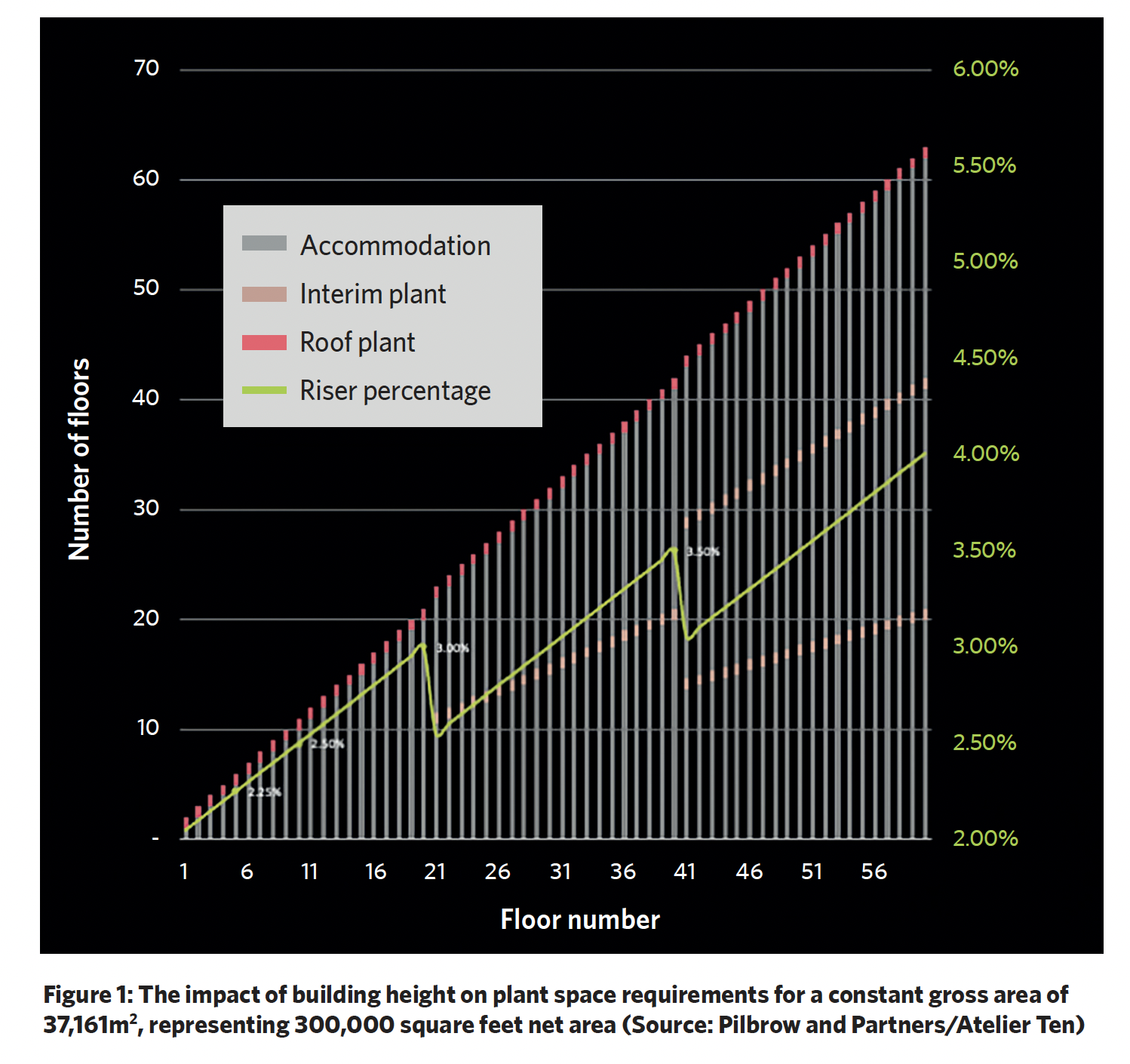
Recent application of chilled water system to a tall building
22 Bishopsgate, the tallest building in the City of London, was completed in 2021. It has 62 storeys and is 278m high, and is designed to accommodate up to 13,000 occupants in 200,000m2 of office space. To moderate the fabric loads, the entirely-glazed façade, of overall U-value of 1.1W.m2.K-1, employs a closed-cavity glazed curtain wall system that includes triple-glazing of selectively coated low-iron float glass to help reduce solar gain while maximising useful light. Motorised venetian blinds are enclosed in the glazing cavity to provide glare control as well as moderating solar gain.
The chilled water system is based on four high-efficiency, variable-speed centrifugal chillers located at a basement level, as shown in Figure 1 – each capable of delivering up to 4MW of cooling. The chillers incorporate a novel dual-stage aerodynamic pair of centrifugal impellers, to accommodate a wide range of temperatures and improve efficiency across the operating ranges.
Automatically adjusted ‘tunnel diffusers’ – which are enhanced developments of a slotted plate – convert much of the kinetic energy in the refrigerant gas to static pressure as it leaves the compressor, and assist in continuously balancing the compressor output to match the load requirements, which contributes to an energy efficiency ratio (EER) of up to 6.8.
Cooling towers were installed on level 58, some 270m above the compressors and evaporators. To reduce the condenser and chilled water static pressures, the systems have been split into two smaller circuits on floor 25, using plate heat exchangers; one circuit serves the upper floors, and one the lower.
The building was awarded a BREEAM Excellent rating, with CO2 emissions targeted to be reduced by 35% compared with the Building Regulation requirements.
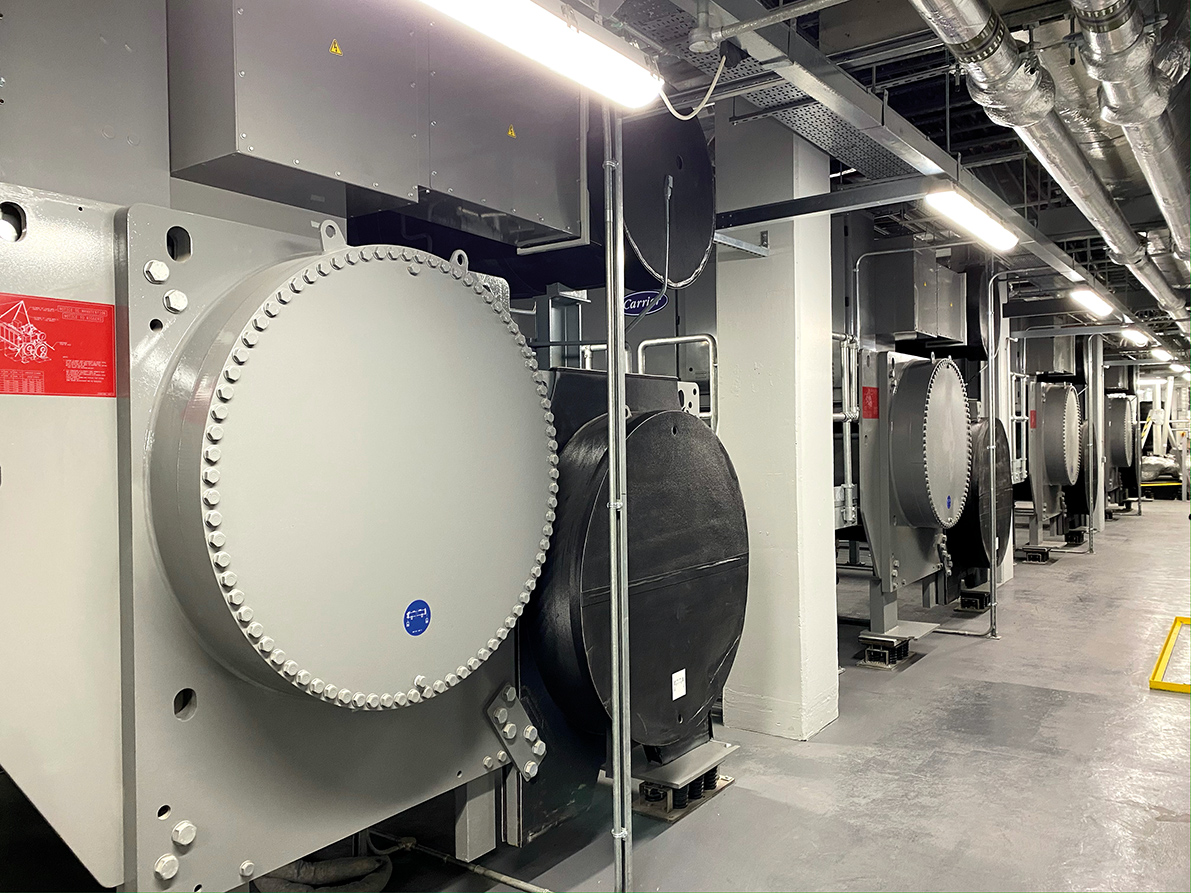
Figure 2: The four centrifugal chillers each deliver 4MW of cooling with an energy efficiency ratio (EER) up to 6.8
A significant consideration is the static water pressure created by the height of the building. That will impact the piping, valves and fittings and equipment installed in the building that will affect the water side of the chiller condenser and evaporator, right through the pumps, cooling coils and – depending on the method of space cooling – room units, radiant ceilings, and chilled beams.
The location of the refrigeration machines and the supporting chilled-water and condenser water pumps can have a cost impact on many of the chilled-water system components, as this will impact the design working pressure.
The refrigeration plant can be located at virtually any level in a building, from a basement mechanical equipment room to one located on the roof. As the chiller becomes more distant from the final load, the chiller outlet temperature will need to be delivered lower (to compensate for distribution system heat gains) – this will reduce chiller efficiency. The cost of the refrigeration equipment will increase as the working pressure on the equipment and piping increases.
The static pressure across the chilled water system in a high-rise can be moderated through the use of flat-plate heat exchangers in interceding floor plant spaces that can then be employed to deliver secondary chilled water within 1K of the primary water (this lowest possible value temperature difference being known as the ‘approach’).
This arrangement does not significantly impact the primary pumping head, but there will be additional need for secondary pumping and controls, and, because of the approach temperature difference, the zone water temperature will be higher, so requiring higher flowrates in secondary zone systems. The primary chilled water temperature must be controlled to accommodate the required approach on each of the intermediate heat exchangers, which is likely to adversely impact the efficiency of the chillers.
A team at the architectural firm Pilbrow and Partners considered the various environmental impacts (including embodied and operational carbon) of increasing heights of a commercial office space while maintaining a specific gross floor area.
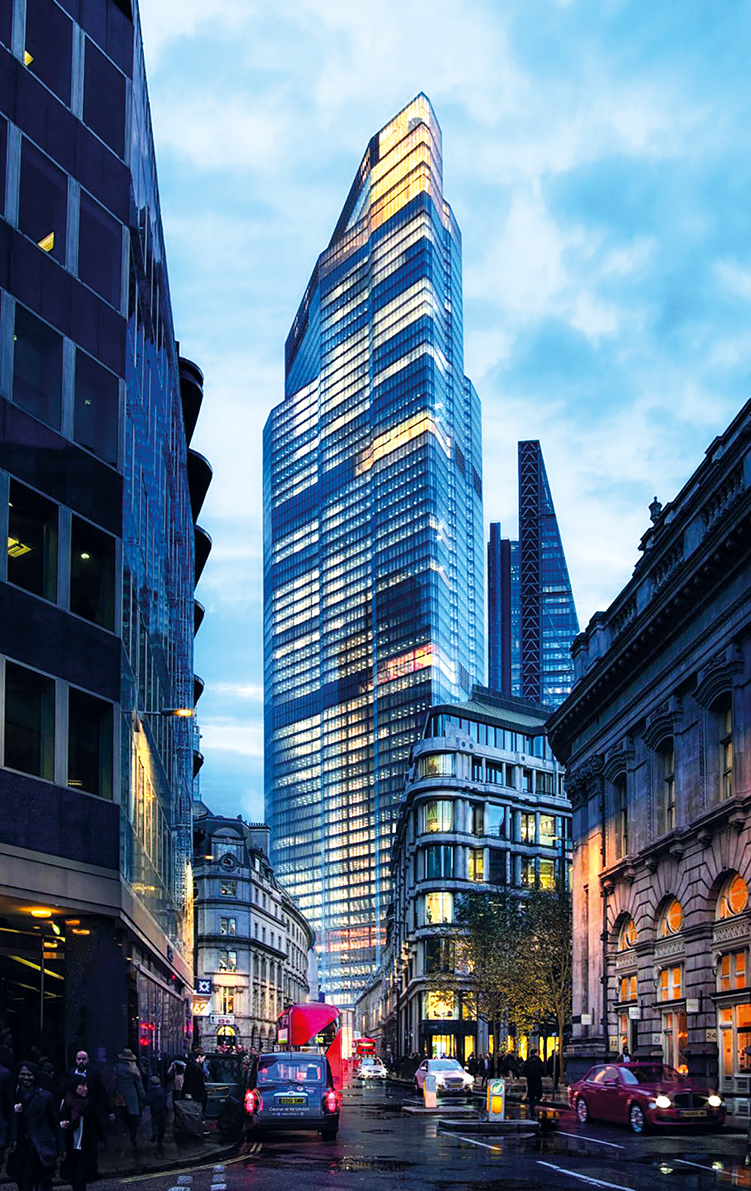
Figure 3: 22 Bishopsgate (Source: CIBSE Journal, November 2021)
This was reported in the Frank Knight online seminar,3 employing additional information provided by environmental engineering firm Atelier Ten that – among other findings – illustrated the impact of building height on indicative mechanical and electrical plant requirements for the building.
As can be seen in Figure 1, in this particular modelled scenario, buildings up to about 20 floors require a progressively larger percentage of riser area but would not typically need any significant plant space on interim floors.
However, in this model, beyond 20 storeys – and then again at 40 storeys – there are break points indicating the typical need for interim plant spaces (each one reducing
the increase in the cumulative required riser space).
The ASHRAE design guide5 highlights that in high-rise applications the capital costs of the piping, valves and fittings can be substantially reduced by using larger temperature differentials at one or both the evaporator and the condenser. The consequent reduction in volume flowrates can reduce required pipe sizes and pumping power. However, this can adversely impact the performance of chillers and requires careful, holistic, consideration.
As noted by ASHRAE,5 while the final choice of system will frequently be ‘predicated on what is being done on competitive projects in the same real estate market and may reflect the bias of one or more of the deciding members of the project team’, the final decisions on tall building systems should be based on objective analysis and discussion that delivers a coordinated compromise, representing best practices from the whole delivery and operation team.
References:
- CTBUH Year in Review: Tall Trends of 2022, CTBUH Journal 2023, Issue I.
- 2023 London Tall Building Survey, NLA, 2023.
- Can tall buildings really be sustainable, Knight Frank webinar, March 2022,
bit.ly/CJJun23CPD1 – accessed 1 May 2023. - Tobias, M, Which HVAC Configuration Offers the Highest Efficiency for Tall Buildings?, CTBUH Journal, Issue 3, 2019.
- Simmonds, P, ASHRAE Design Guide for Tall, Supertall, and Megatall Building Systems, 2nd Edition, ASHRAE 2020.
- Post-Pandemic HVAC Systems Strategies For High-Rise Office Buildings, CTBUH Journal 2020, Issue 4.
- bit.ly/CJJun23CPD2 – accessed 27 April 2023.