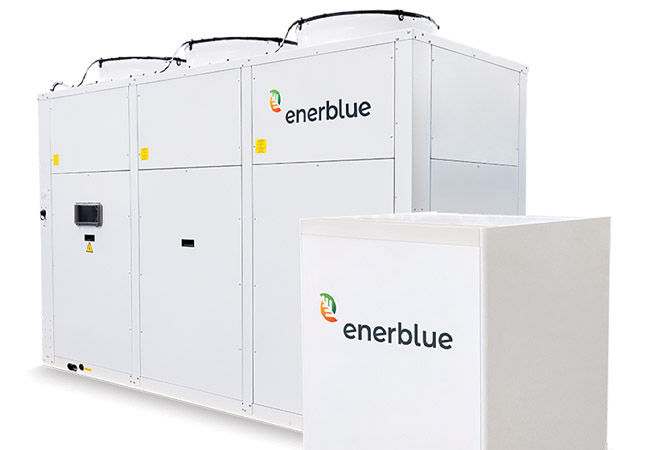
Enerblue’s heat pumps use CO2 as a natural refrigerant and can heat water up to 90°C
A host of different criteria needs to be assessed and balanced to decide which heat pump or chiller technology is right for a particular application. Complicating the picture further for heat pumps are the refrigerant choices; refrigerants are a particular minefield that must be negotiated before a consultant can go any further in specifying HVAC equipment for new projects.
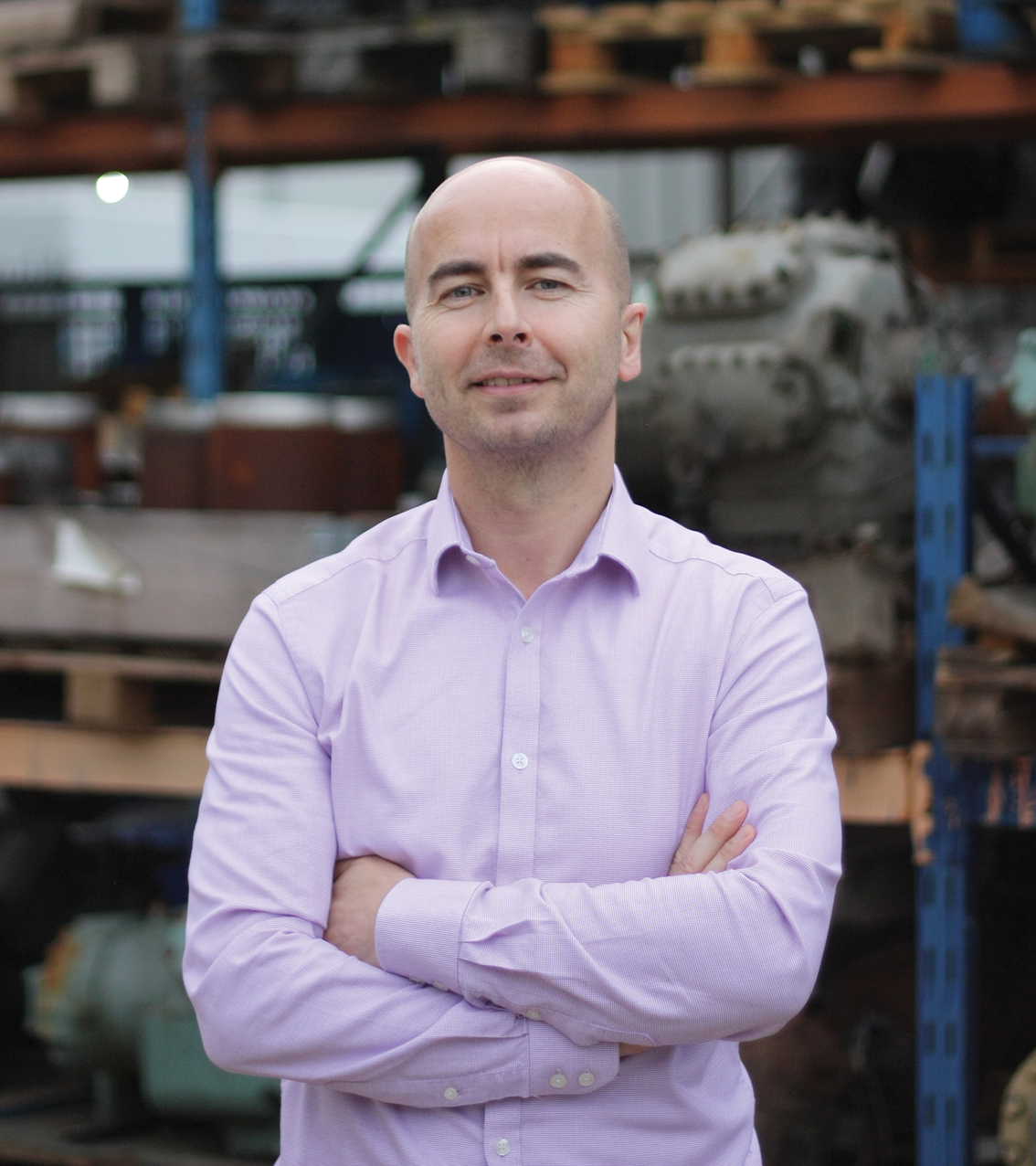
Tim Mitchell says a refrigerant’s embodied carbon must be considered
All the most common hydrofluorocarbons (HFCs) are categorised as A1 and so non-toxic and non-flammable. They are readily available, well understood, and relatively cheap – so why consider using natural refrigerants at all?
There are fundamentally two reasons. The first is application suitability, which has been created by the recent drive to remove the burning of fossil fuels from the built environment. For example, using CO2 as the refrigerant in a heat pump can deliver hot water at boiler-like temperatures and beyond – 90°C is no problem – at much better efficiencies than any HFC. This means that, for modern boiler-replacement projects, it is typically the most applicable option.
A typical air source CO2 heat pump might deliver hot water at 75°C from air at -4°C with a coefficient of performance (CoP) of 2.53 or so, whereas an HFC using the same criteria would give a CoP of around 1.78 and would be at the top of its operating range. However, that is not the end of the story.
CO2 systems are peculiar in the HVAC selection ranges because they operate trans-critically, so require a very wide differential between the leaving and return water temperatures. This characteristic means they are especially suited to sanitary or process applications, for which you consume a lot of very hot water. This makes CO2 stand out among the natural refrigerant options – it has its own application envelope, whereas there are HFCs that have a more complete ‘operational overlap’ with ammonia and propane.
One reason to consider natural refrigerants is sustainability, particularly in relation to their ultra-low GWP
The second reason to consider natural refrigerants is sustainability, particularly in relation to their ultra-low global warming potential (GWP). For example, ammonia’s GWP is 0; CO2 has a GWP of 1 (it is the base for the GWP metric); and propane’s GWP is 3. This compares with the lowest GWP HFC that we currently see in common use for HVAC applications – R32 – which has a GWP of 675.
Some HFC/HFO blends can offer lower GWPs – R513A and R454B have GWPs of 631 and 467 respectively, for example – but none get down into the ultra-low category of natural refrigerants, with the exception of pure hydrofluoroolefins (HFOs) which have environmental issues of their own (the energy needed to produce HFO refrigerants can be problematic, and the by-products from the breakdown of some are acidic).
There is a third metric that specifiers should take into account after application and GWP – ‘embodied’ carbon. A building, for example, can be very efficient in use, but if it is built from traditional concrete, the embodied carbon – the carbon expended in manufacturing the concrete – can be huge.
Refrigerants also have an embodied-carbon element. The metric that takes this and other environmental factors, such as GWP and energy efficiency, into account is called life-cycle climate performance (LCCP). LCCP does not, however, take account of the amount of embodied carbon there might be in, say, a commercially built HFC chiller compared with an industrially built CO2 or ammonia machine.
There are no wide-ranging studies yet complete in this area, but we are working with the London Energy Transformation Initiative (LETI, www.leti.london) and Rhoss, one of our manufacturing partners, to calculate the embodied carbon in a chiller or heat pump as we make them.
It is hugely complicated to do these calculations, however, and there are lots of places where it is difficult to make direct comparisons – for example, with refrigerant leakage. Which brings us back to where we began – struggling with the knotty problem of what criteria you should apply to accurately assess the benefits and drawbacks of each piece of HVAC technology and the refrigerants it uses.
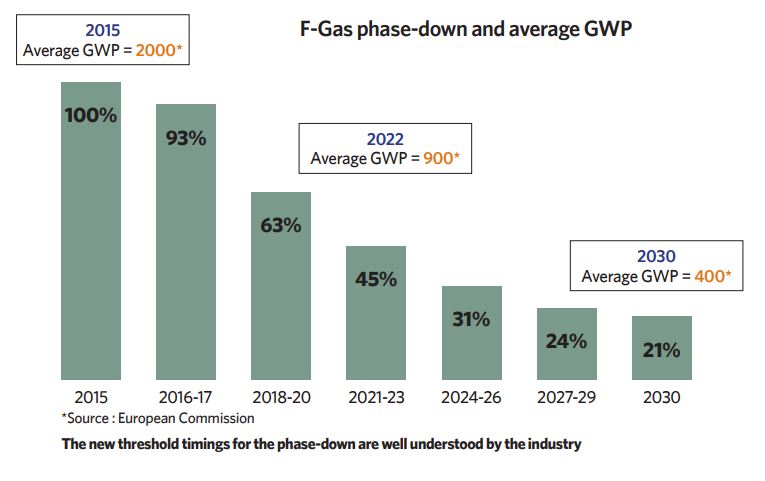
Arguably, the starting point should be to consider the sustainable, ultra-low GWP options first. Beyond that, the application determines the solution. The specification decision really comes down to horses for courses. As a specifier and client’s trusted adviser, all you need to do is decide which horse to back.
IMPACT OF F-GAS REGULATIONS
The latest phase-down in F-Gas regulations was introduced on 1 January (see graph). The new threshold timings have been well understood for years, so the industry has done a lot to ensure the transition does not result in the madness that ensued after the first severe reduction in 2018.
This is partly down to better control of refrigerant leakage, and not treating refrigerant as a consumable. More intelligent design of systems has reduced refrigerant charge.
The most common refrigerants used in heat pumps are HFCs, which have a high GWP compared with natural refrigerants. The GWP metric is based directly on the GWP of 1kg of CO2, itself a useful natural refrigerant. For example, the GWP of R410A, the HFC refrigerant used exclusively in variable refrigerant flow systems for the past decade or so, is 20881 – that is, 2,088 times that of CO2. By definition, the leakage of 1kg of R410A to atmosphere has the equivalent greenhouse effect, over the standard GWP base of 100 years, that 2,088kg of CO2 would have in that same period.
Particular progress has been made in the moves away from higher GWP refrigerants to low and ultra-low ones by manufacturers (for example, from R410A (GWP 2088) to R32 (GWP 675) in splits and small chillers/heat pumps, and ultra-low GWP HFOs and low-GWP HFO blends in larger chillers), supported by more of the component supply chain and as demanded by end users.
There are natural alternatives to HFCs. For chiller and heat pump applications, the common ones are ammonia (R717), propane (R290) and CO2 (R744). The standard classifications for refrigerants revolve around toxicity (A or B – non-toxic or toxic) and flammability (1, 2L, 2 or 3 – non-flammable to highly flammable), as defined in ISO 817. CO2 is an A1 refrigerant, so neither toxic nor flammable. Ammonia (B2L) is toxic, but exhibits low flammability. Propane (A3) is non-toxic, but highly flammable.
About the author: Tim Mitchell is the sales director at Klima-Therm
References: 1 AR4, the Intergovernmental Panel on Climate Change’s Fourth Assessment Report – bit.ly/3qdeRaQ