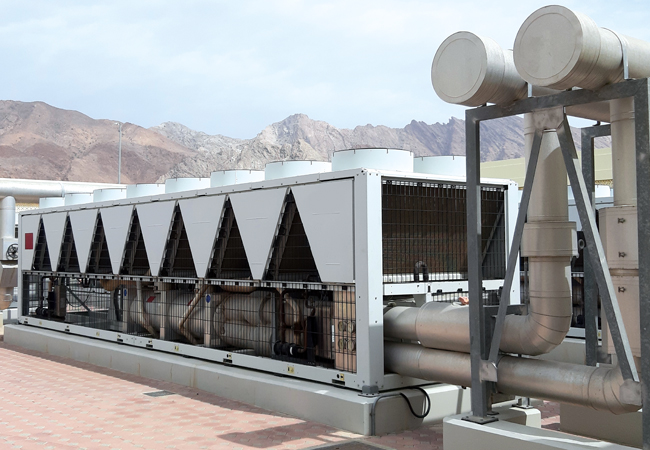
A changing landscape on chiller solutions is inevitable in the Middle East
With the impacts of global warming, the depletion of freshwater resources is accelerating. In Middle Eastern countries, with low rainfall, natural freshwater resources are limited, and desalination of seawater is the primary source of potable water.1 However, desalination consumes energy, so any process that uses potable water generated from desalination will have a high level of embodied energy. The term ‘water-energy nexus’ defines this scenario.
Global building standards, such as ASHRAE 90.1/189.1, and region-specific standards, such as the Dubai Green Building Regulations, consider water-cooled chiller systems as the baseline for energy performance analysis/audits. Water-cooled chillers use cooling towers in which water is evaporated to provide cooling. Even though a water-cooled chiller consumes less electric power to deliver the same cooling compared with an air-cooled chiller, it is important that the in-built energy expenditure of desalinated water used in chilled water production is accounted for in the comparison of chiller energy usage.
Desalinated water
In Dubai, approximately 90% of potable water produced is desalinated, and this is representative of other Middle East regions.
Desalination, storage and distribution of potable water is energy intensive. Each cubic metre of potable water supplied in Abu Dhabi costs 10.41 United Arab Emirates Dirham (AED)2 (£2.35). This corresponds to around 34kWh of electricity, based on the Abu Dhabi municipality rate of 30.5 fils per unit (£0.07 per kWh) of electricity. The rates mentioned here are based on the actual cost of water and electricity production, because most countries in the region are planning to reduce or eliminate subsidies for energy and water.
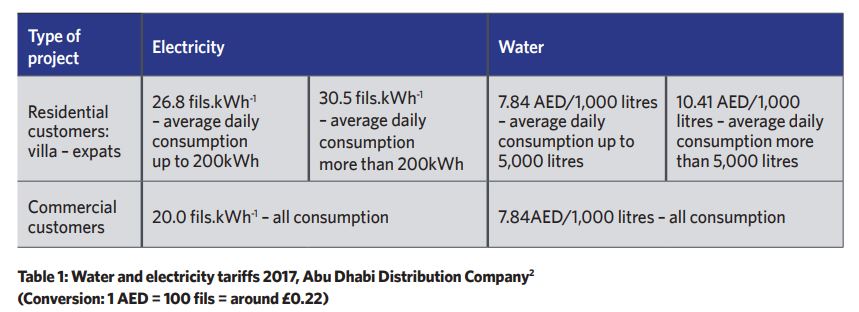
Treated sewage effluent (TSE) may seem like an efficient alternative for potable water in cooling towers in buildings. Each cubic metre of TSE water delivered will typically cost AED 1.3 (£0.28). With the additional cost of treatment required, through a reverse osmosis (RO) plant, the total cost per cubic metre will increase to approximately AED 5 (£1.08) – about 17kWh of electricity, based on the Abu Dhabi municipality rate above.
Chiller plant efficiency
A comparative analysis of air-cooled and water-cooled chiller types in a 1,000-tonne chiller plant is summarised in Table 2. It includes full-load and part-load efficiencies for standard and high-efficiency chillers.
For a 1,000-tonne cooling plant at its full load, a standard air-cooled chiller consumes 1,255kW of electric power, compared with 576kW by a water-cooled chiller. This shows that a water-cooled chiller is 56% more effective at full-load operation. To analyse the total energy impact, however, part-load operation and auxiliary equipment efficiencies should also be considered.
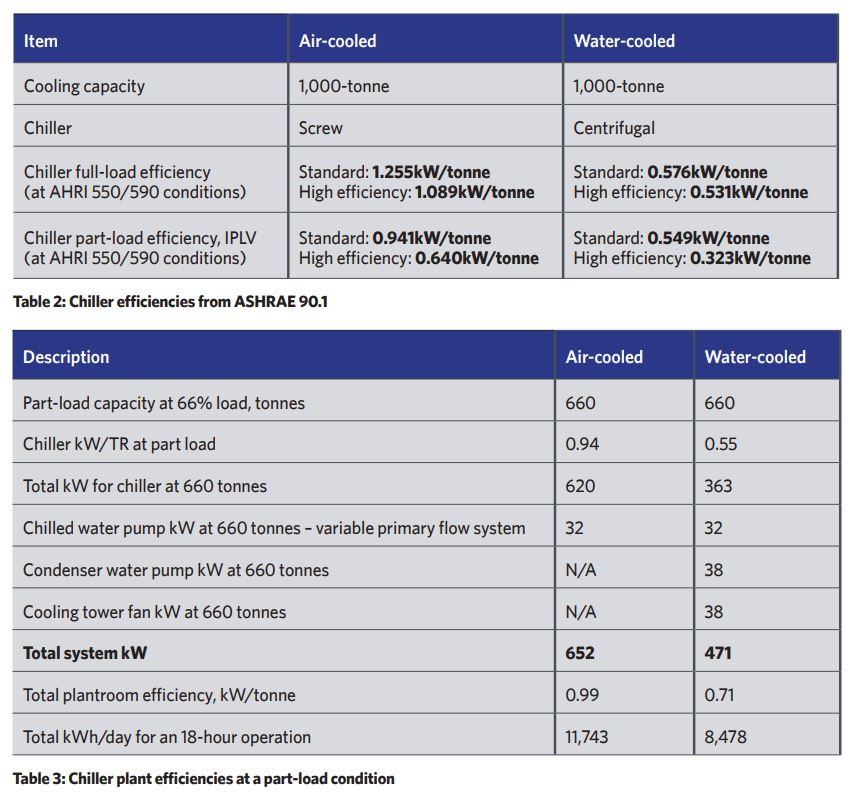
Chillers will operate on a part load for most of the hours in a year. Hence, to assess power consumption, the part-load performance should also be considered. An average of 66% load for an 18-hour operation per day is considered in this assessment. At 66% of full load, the same air-cooled chiller will consume 621kW of electric power, compared with 363kW by a water-cooled chiller. This shows that the water-cooled chiller is 41% more effective, even in part-load operations.
To verify the overall performance of the plant, rather than the chiller, this assessment is enhanced to include power consumption from auxiliary equipment (Table 3). By including auxiliary plant components, the efficiency figures start to come down. This is because a water-cooled chiller uses additional evaporative cooling towers and condenser water pumps for heat rejection. Once these are included, the total efficiency figure for a water-cooled chiller plant is only 28% higher than a similar capacity air-cooled chiller.
To calculate and compare the actual energy consumed in producing each cubic metre of chilled water for a water-cooled system, it is necessary to include the embodied energy of the water that is consumed in the cooling tower. Approximately 106m3 per day of potable water will be consumed by a 1,000-tonne chiller plant, at 66% part-load operation for 18 hours per day. The same plant, by using ‘polished’ TSE, will consume 155m3 of water per day.
Table 4 includes the cost and interpolated energy for potable and polished TSE water, based on cost figures from the region. This embodied energy of water typically will not be considered in building energy analysis. However, if embodied energy from the source of water is also included, the plant efficiency figures show a significant difference.
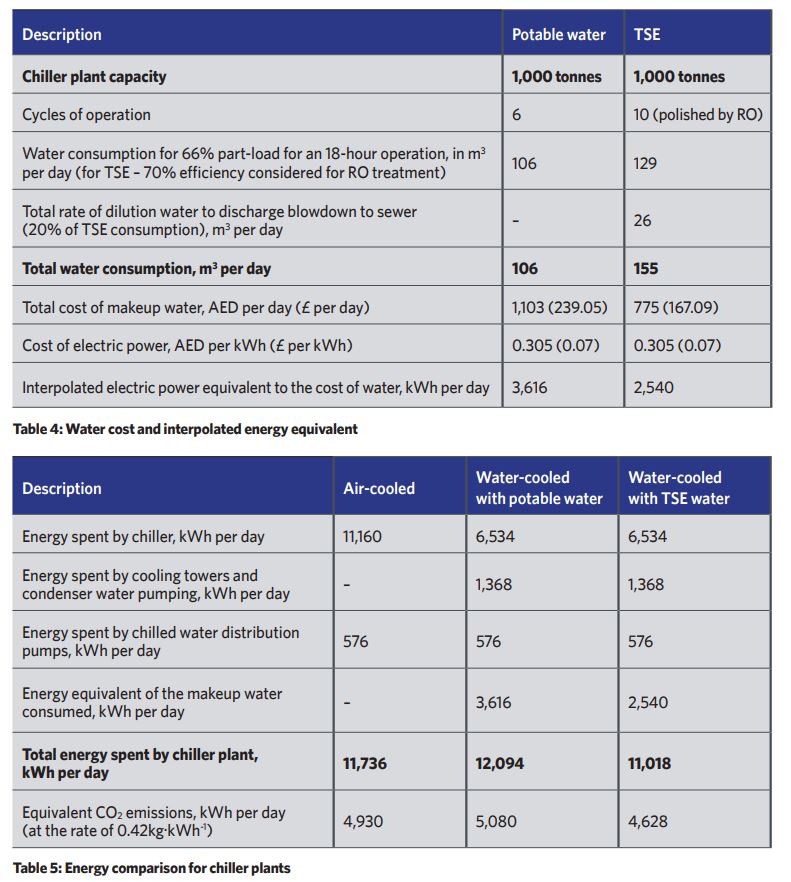
Table 5, over the page, summarises the energy usage from both systems and source. The data indicates that total electrical energy consumed per day by a 1,000TR air-cooled chiller plant will be less than a potable water-cooled chiller plant by 358kWh, if source water embodied energy is considered in the efficiency figures. This is equivalent to 150kg of CO2 emissions per day. By using TSE, the energy consumption is marginally lower than an air-cooled chiller plant. This is not significant when comparing the cost of maintaining a polishing RO plant. A detailed life-cycle analysis will be required to assess the efficiency of polishing RO plants.
Conclusion
Air-cooled chiller installations can offer better efficiency and energy/cost savings than a similar water-cooled installation, if source water embodied energy is considered in the efficiency figures. With a rapidly growing sector of clean energy, the challenge is to reduce the consumption of water, as water becomes more expensive.
ASHRAE Standard 191, Standard for the efficient use of water in building, site, and mechanical systems is expected to explain the modelling compliance paths for water usage in building projects. The public review draft states: ‘If a life-cycle analysis is performed to compare an air-cooled chilled water plant to a water-cooled chilled water plant, the total energy of the air-cooled plant may end up being approximately the same as the total energy that would be used by a water-cooled plant if, for example, the water-cooled plant was evaporating desalinated water that was being delivered to the site.’3
We are working to assess indirect life-cycle costs, as TSE plant component maintenance is expensive, and can have an impact on decision-making. We are also working on the life-cycle cost analysis of all three chiller plant types, over 20 and 35 years, to take into account environmental conditions in the region. As revealed by this stage of the study, the capital cost of water-cooled plant with potable water is only 83% of air-cooled plant, whereas with TSE associated water-cooled plants the capital cost is about 200% that of an air-cooled plant. This is primarily because of the cost of TSE/polished water tanks and RO polishing plant. However, when cost of space is considered, indoor versus outdoor (typically, roof for air-cooled chillers) different scenarios are apparent. These are yet to be fully assessed.
A changing landscape on appropriate chiller solutions is inevitable in the Middle East. Designers should be challenged on their selected cooling source, keeping in mind that the energy consumed at the source of water also impacts on the efficiency of the system. and overall CO2 emissions.