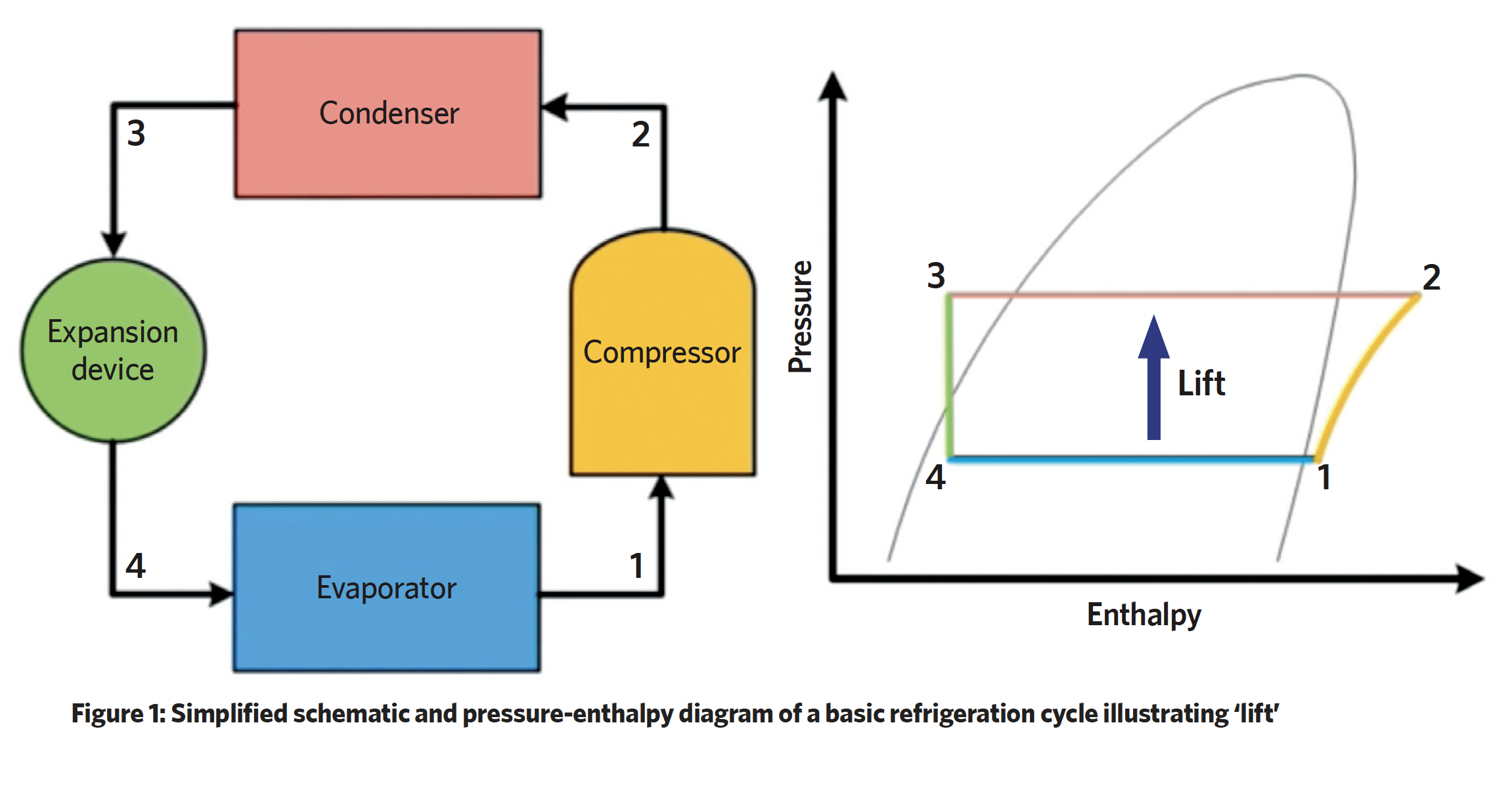
The recent ASHRAE Conference in Atlanta, Georgia, maintained a firm focus on decarbonisation. There were several strategic-level presentations on moving towards a decarbonised future, as well as a diverse selection of seminars offering technical detail that, ultimately, will provide the practical path to net zero.
More than a fifth of the 68 seminars addressed decarbonisation explicitly, including the well-attended CIBSE ASHRAE-supported ‘Accelerating change in building design and operation towards a decarbonised and net zero energy future’, for which CIBSE vice-president Adrian Catchpole provided the introductory presentation on ‘Integrating modern methods for sustainable built environments’.
A great example of how better basic understanding of important, but relatively simple, technical detail can significantly influence the real environmental impact of buildings was delivered by Trent Hunt, of Mechanical Products NSW, Utah.
A key part of his presentation, in seminar 63, illustrated practical considerations to reduce operational energy consumption for chillers. He focused on some key factors that can impact ‘lift’ in a refrigeration cycle significantly – as illustrated in Figure 1, where the condenser and/or evaporator could be shell and tube or direct air heat transfer.
Hunt explained that lift is the difference between liquid condensing pressure and saturation suction pressure, typically converted to temperature – for example, 29.5°C (85°F) liquid condensing temperature (where the heat is rejected) and 4.5°C (40°F) saturated suction temperature (where the cooling is delivered).
By decreasing lift, the work of the compressor is reduced, so decreasing power consumption and emissions – ‘it’s that simple!’ He gave some real-world examples where performance could be impacted significantly. Dirty coils on an air-cooled or scale-coated tubes in a water-cooled condenser, will increase the condensing pressure, so increasing lift.
Conversely, by decreasing the condensing pressure –for example, by lowering water temperature in a cooling tower – lift will be reduced. Other examples given to reduce condensing pressure included: increasing the condenser area; employing ‘adiabatic’ dry coolers (where water is evaporated into the inlet air stream); and, for water-cooled condensers, increasing cooling water flowrate and designing more refrigerant passes through the condenser.
Hunt was keen to highlight a common misunderstanding – that focusing on the condensing temperature alone will ensure efficient operation
However, Hunt was keen to highlight a common misunderstanding – that focusing on the condensing temperature alone will ensure efficient operation. He cited an instance when an incorrect amount of glycol was added to the chilled water circuit; the specification was 30% glycol, but ‘the contractor put in the entire 50-gallon drum of glycol and now, all of a sudden, you have 42% glycol’.
To compensate for the reduction in heat transfer to the now less-conductive chilled water, the saturated, suction temperature (and pressure) needs to be lower (the blue line in Figure 1), so increasing the lift and energy use. Hunt said that a way to reduce lift when cooling requirements are lower (for example, in winter) is to use ‘cold water reset’, allowing the setpoint on the chilled water to rise.
He noted that other options to raise suction pressure can be explored, including: increased evaporator area; more passes across the (liquid) evaporator; more evaporator tubes; and reduced chilled water flow when less cooling is needed. However, he cautioned that care is needed with reducing flow, particularly if there is glycol in the chilled water, as the glycol will increase the water viscosity and the chilled water will move more swiftly to laminar flow, which can lead to local freezing.
Hunt encouraged the audience to carefully consider the impact – and, potentially, unintended consequences – of the various design and operational decisions on the compressor’s lift.
The drive to discuss and interpret the means and method of reducing the impact of buildings and decarbonising HVAC&R was evident across the whole conference.
- Future articles in CIBSE Journal will explore some more of the papers and presentations from the ASHRAE conference. In the meantime, most of them are available (with a paid registration) in the virtual ASHRAE 2023 winter conference at bit.ly/CJMar23TD