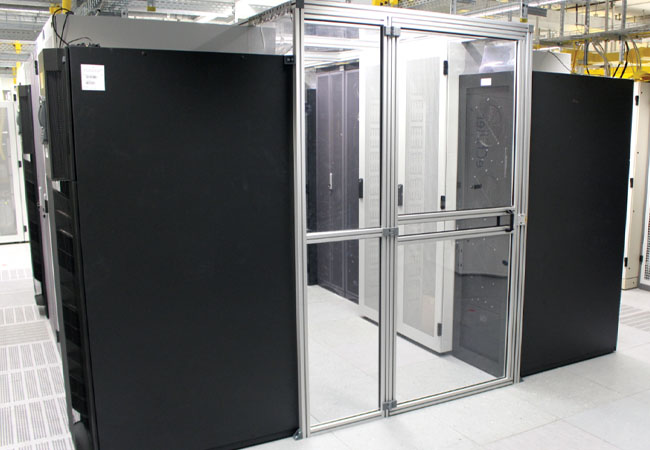
High cooling-density server enclosure
A chiller that uses water as its refrigerant has been launched in the UK, after being deployed for a series of applications in Germany. Organisations such as Siemens and BT have been early adopters of the natural refrigerant-based eChiller, which was introduced at the end of 2014 by German manufacturer Efficient Energy.
The global phase-out of F-Gases means manufacturers have been developing refrigerants – such as ammonia, carbon dioxide and water – that have less of an environmental impact.
According to Efficient Energy, the eChiller is ideal for applications that require chilled water flow temperatures of 16°C and above, such as cooling via chilled beams or cooling for IT equipment rooms. In the UK, the technology is being supported by natural refrigerant specialist Green Thermal Energy.
Operation
The main components of the water chiller are similar to those of chillers that work on the principles of evaporation, compression and condensation. Important differences are that the ‘refrigerant’ used is water – designated R718 – and the chiller functions with a very low operating pressure within the refrigeration system.
As a result of the low operating pressure, refrigeration equipment safety standard EN378 certification is not required – and, because there is no risk of F-Gas refrigerant leaks, no leak-detection equipment or F-Gas monitoring procedure is necessary.
Water enters the evaporator, where around 1% of it evaporates, drawing energy from the remaining water and cooling it down. The pressure inside the evaporator is around 18 mbar (0.26psi). This near-total vacuum is created by the rotating impeller in the unit’s centrifugal compressor.
The pressure in the compressor is then increased to 136mb (1.97psi) and the temperature rises from 16°C to 52°C. The water vapour is cooled, condensed and fed back into the evaporator through the expansion device, to complete the refrigeration cycle.
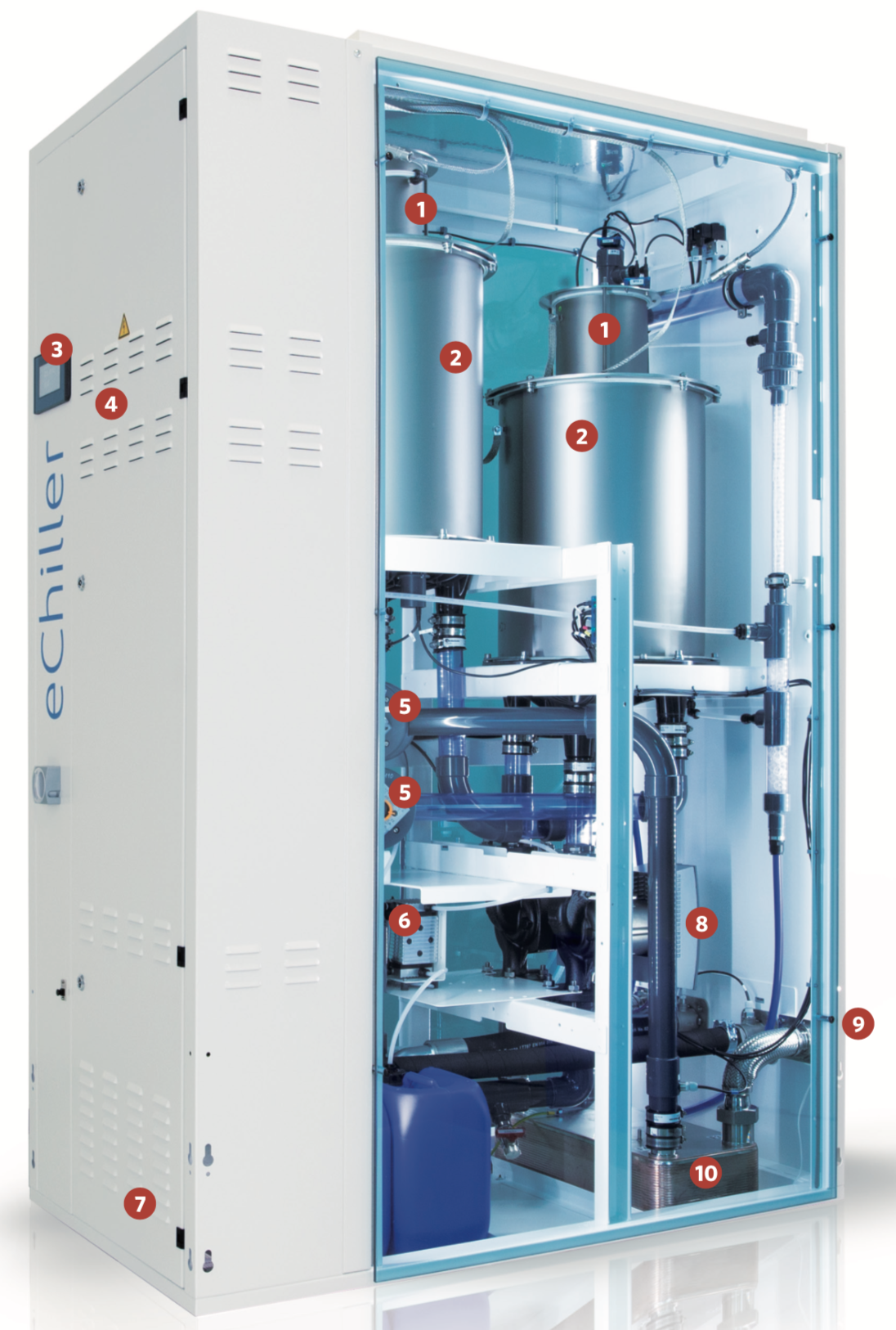
The standard new technology chiller has two cooling modules and two heat exchangers. Key: 1 Compressors 2 Cooling modules 3 Programmable logic controller display 4 Electric cabinet 5 Water valves for operating modes 6 Vacuum pump 7 Chilled water heat exchanger 8 Internal water pumps 9 Hydronic connections 10 Cooling water heat exchanger
As shown in Figure 1, this chiller has two cooling modules and two heat exchangers. All units are also connected to a matched dry cooler, usually placed on the roof of the building. This dry cooler can be an adiabatic cooler or a standard dry cooler, delivered as part of the chiller package. Alternatively, the dry-cooler function could be a centralised condenser loop already installed within a potential application, such as a cooling tower circuit or similar.
The dry cooler, or condenser circuit, also enables the chiller to operate in 100% free-cooling mode. The benefits of free cooling take place at a much earlier point than would be the case with standard free-cooling chillers.
At high ambient temperatures – for example, 35°C – this new chiller operates in mechanical mode, with two compressors operating fully. At these temperatures, it has an energy efficiency ratio (EER) of 3.4.
When the ambient temperature drops, the second compressor modulates, increasing the efficiency. For example, at an ambient temperature of 21°C the EER increases to 7.4.
When the ambient temperature drops to a level where the cooling water from the dry cooler is at least 2K colder than the return water from the chilled water/cooling circuit, the first stage also switches off. This allows the system to direct the water solely through the chiller without mechanical cooling, achieving ‘free cooling’, which delivers an EER of more than 20.
Actual efficiency is subject to the cooling load profile of each individual project. However, this mix of mechanical and free cooling results in a system delivering a very high seasonal EER (SEER) in excess of 11 (in representative northern German climatic conditions).
BT case study
An installation has been operating since 2017 at a BT location in Hamburg. At its data centres, BT offers room-in-room ‘cube’ solutions for high-density server racks, which place gruelling demands on the technical infrastructure because of the concentrated power density.
These ‘cubes’ can be scaled modularly, each in a power range of 40kW to a maximum 100kW IT load. Uniformly water-cooled, in-row chiller units with hot-aisle housing are used for cooling. With temperatures of 22-25°C required on the intake side of the racks (cold aisle), large temperature differences arise between the supply and discharge air at a simultaneously high temperature level.
The ‘cubes’ are connected to existing central DC infrastructures and existing chilled-water or cooling-water systems. Cooling-water networks with adequate capacity are not available for this additional cube load at the locations in Hamburg and Berlin. As such, an additional modular, scalable, chilled-water production system was needed to maximise efficiency, provide fail-safe redundancy and support relatively high system temperatures – the optimal area of application for the new
technology chiller.
Three chillers per cube feed a buffer tank with chilled water. An energy-management system controls the number of chillers, which should operate in parallel, depending on the load. This ensures evenly distributed operating times and high operational reliability.
The systems are connected to a building-control system for monitoring relevant operating and performance data, while the manufacturer can actively analyse the installation’s process parameters at all times and avoid malfunctions via an installed remote-maintenance interface. In addition to enabling maintenance intervention, the storage of recorded data allows straightforward evaluation of the system operation and its efficiency.
The installation at Hamburg has demonstrated the reliability of this new technology application, stable chilled-water delivery temperatures of 16°C, and maximum efficiency under realistic load conditions.
BT has installed three high-density cube systems using eChillers. The first of these has been running at the Hamburg site for two years, and since commissioning the system has operated fault free.
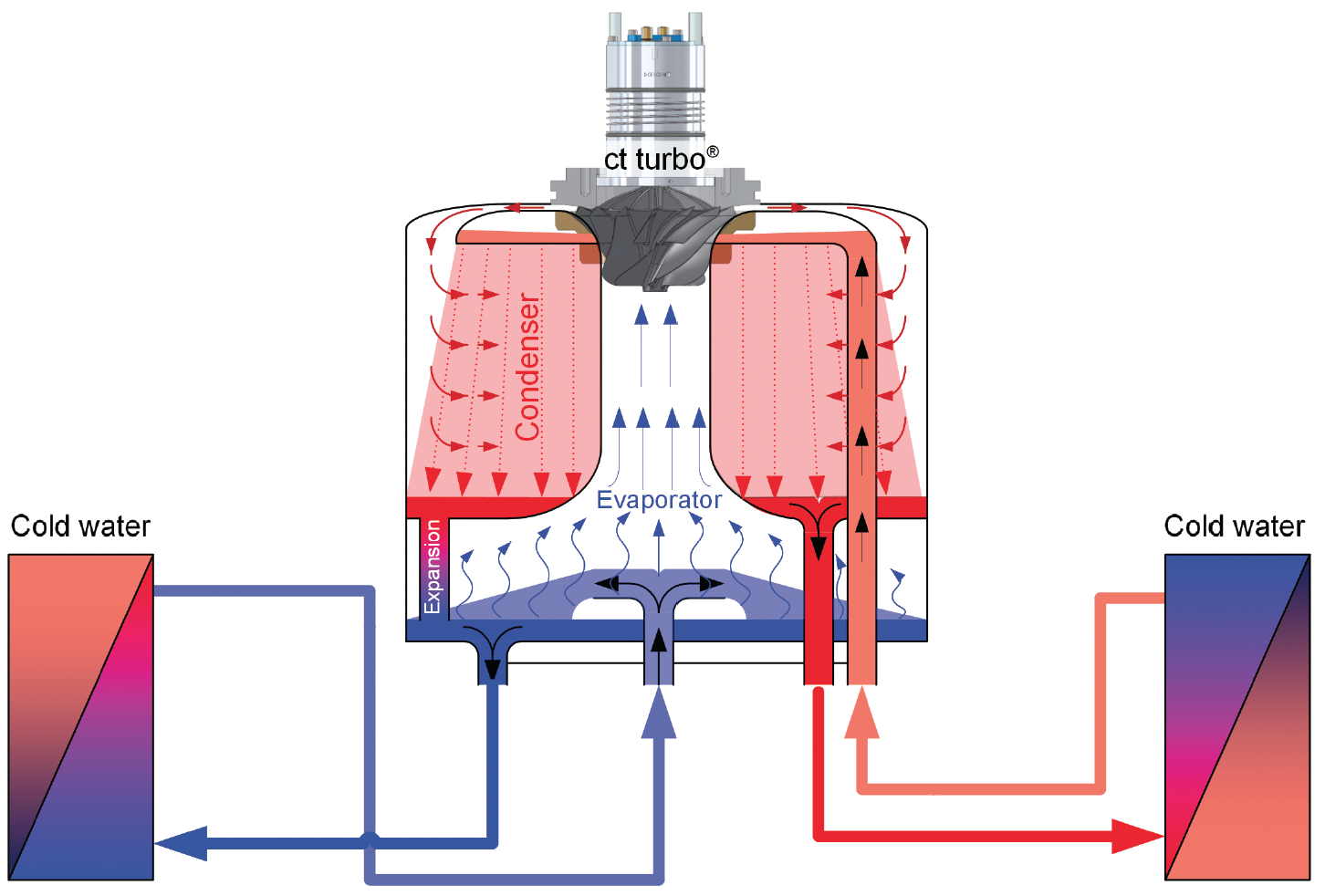
Three chillers per cube feed a buffer tank