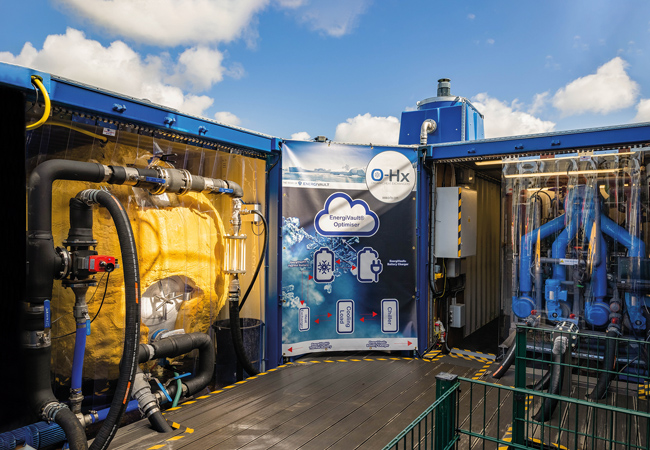
The first installation of EnergiVault at Quotient Sciences, a drug development and manufacturing accelerator, Alnwick
Cooling presents something of a climate change conundrum. Because, while it is crucial to every part of modern life in a warming world – from keeping food fresh, vaccines useable and people healthy and comfortable – it is also energy intensive and environmentally damaging.
According to the Green Cooling Initiative, there are approximately 4bn cooling devices in use around the world and it expects that figure to reach 9.5bn by 2050.
The report, A Cool World, by The Birmingham Energy Institute and the Institute for Global Innovation at the University of Birmingham, stressed that access to cooling is essential for meeting the world’s social and economic goals, but warned that unmanaged growth represents one of the biggest threats to achieving climate targets for CO2 emissions. It added that if cooling is to be sustainable, just improving the efficiency of equipment is not enough.
Cold thermal energy storage (CTES) is one solution that has the potential to reduce the environmental impact of cooling. CTES is capable of storing and delivering significant amounts of thermal energy on demand to reduce the cost of cooling on existing or new-build projects. It can take many forms, but it more commonly features systems that use banks of ice to provide energy transfer. Typically, they are coupled with a ‘charger’ or its own independent chiller for ice generation and can be used to cool produce directly or to cool the heat transfer fluid.
While they can be used in isolation, they are normally found alongside existing chillers. They offer a time of use (ToU) shifting to negate costly electricity tariffs and can avoid energy consumption at high carbon-intensity periods.
As an alternative to storing energy in electrochemical batteries, such as the lithium-ion examples in everyday use, thermal energy batteries do not reduce in capacity over time and therefore avoid the resulting loss in energy capacity.
The rate and control of energy transfer between a CTES system and the fluid or produce it is cooling is essential to its effectiveness. Typical CTES systems use ice as the energy store because of the amount of energy that can be transferred during the latent heat of fusion (phase change from solid to liquid) in relation to the storage volume required if only a sensible (temperature change) phase change material is used.
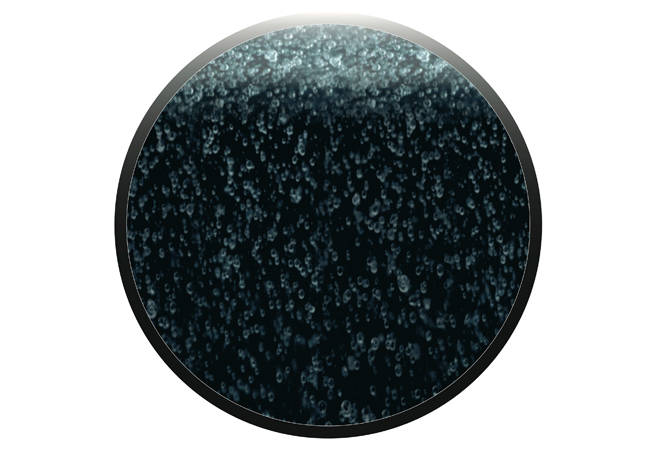
Left: A cross-section example through a horizontal cylinder of the thermal battery shows less dense ice crystals migrating to the top of the flowing working fluid
The rate of energy exchange from the phase change material and the heat transfer fluid (or produce) is in correlation to the difference in enthalpy between the two substances and the surface area where energy exchange can take place. A block of ice would typically have a large volume-to-surface area ratio, which means that the energy exchange rate would be lower than found with multiple shards of ice.
Phase change batteries generally have the limitation of a low discharge rate because of the limited surface-area-to-volume ratio, and, therefore, cannot always meet a required load. The patented EnergiVault CTES system from Organic Heat Exchangers (O-Hx) has been designed to maintain an ice slurry as its thermal store, which increases the possible amount of energy transfer at any given time managing the energy contained in trillions of ice spheres of approximately 0.1 to 1mm diameter.
Each crystal, because of its large surface-area-to-volume ratio, has 66% usable energy in relation to its volume when stored inside the thermal vault, and takes the shape of a spherical crystal to avoid the clumping that is typically found in dendritic crystals. To maintain the separation of the spheres, they are surrounded by a parent fluid formulated with a freezing point below the ice-sphere it supports, inhibiting fusion while in storage.
The thermal store or battery cell design uses a series of horizontal cylinders through which the building’s transfer fluid passes directly, or can be separated by a plate heat exchanger depending on site-specific requirements. These cylinders are chilled by the accompanying charger, or battery, which is calibrated to provide evaporating temperatures set accordingly to the fluid. Its tolerance is set to reduce the temperature and therefore the energy of the heat transfer fluid until ice crystals begin to form, creating the working ice slurry.
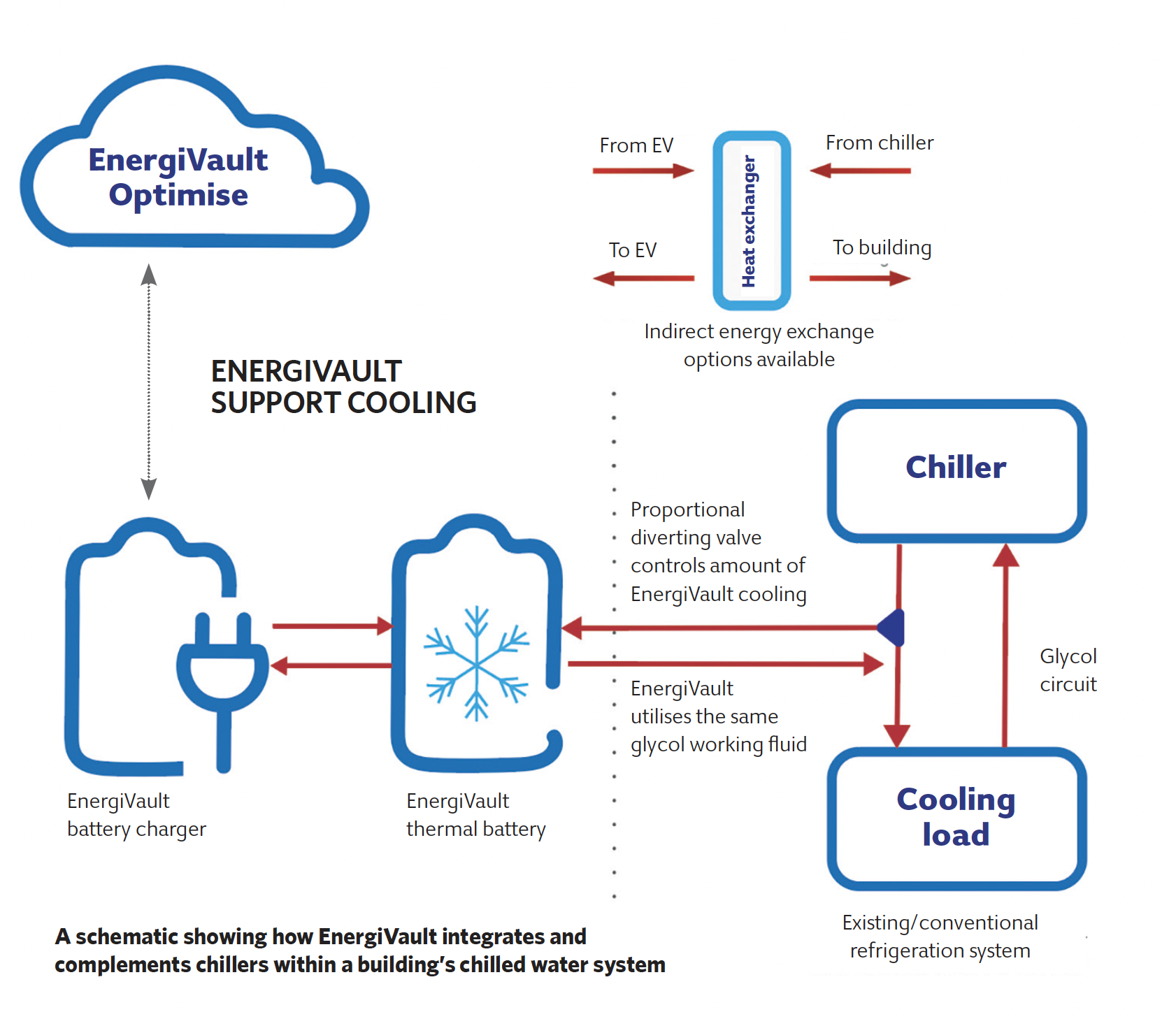
A blending valve allows the integration of the EnergiVault into any existing chiller system. This valve regulates the flow of heat transfer fluid through the thermal store and provides complete load control. A single EnergiVault battery cell can currently support a 1MW discharge rate for short periods of time, surpassing the capabilities of other thermal storage batteries of a similar nature. Its stored capacity is calculated by judging the displacement of the heat transfer fluid from the thermal store as crystallisation begins to occur.
Artificial-led intelligence is a key component of any modern energy-saving device, including CTES systems. Monitoring building load patterns, chiller efficiency under part-load conditions or during staging, and the use of energy when produced at low tariffs or at periods of low carbon intensity are all methods of improving overall system efficiency and environmental impact.
An ongoing test site using the CTES system at the Alnwick facility of drug development and manufacturing accelerator, Quotient Sciences, has already demonstrated significant savings in both operational and environmental costs.
The site’s load is projected to require 500MWh of cooling per year with an associated carbon footprint of 47tCO2e. The installed capacity of EnergiVault is 500kWh and is expected to meet approximately 30% of cooling demand through basic operation using time of use (ToU) shifting.
It has so far provided a 27% operational cost saving primarily from load shifting, avoiding red band high cost electrical tariffs and some incidental chiller efficiency benefits. Furthermore, it has provided cooling support during the breakdown and the organised maintenance shutdown of the existing chillers. When operating at its full potential, O-Hx calculates that savings of up to 69% can be realised against site cooling costs, with up to 64% reduction of CO2 emissions.
About the author
Bob Long is executive chairman of Organic Heat Exchangers (O-Hx)