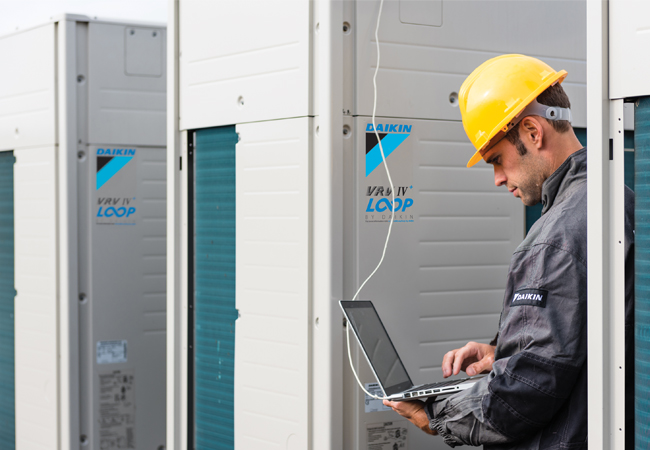
The science is clear; the world is in a state of climate emergency, and we face our greatest challenge yet. The expected rate of warming is 3°C by the end of the century, but we need to reduce this down to below 1.5°C if we want to mitigate serious risks to people and the planet.
We must quadruple the UK’s supply of low carbon electricity if we are going to have any chance of achieving net zero by 2050. Clearly the construction and HVAC industries have a central role to play in adopting a circular economy approach to ensure we meet our net zero obligations and manage F-gas refrigerant supply sustainably.
Circularity is a concept that is gaining increased attention. In simple terms, a circular economy is a model of production and consumption that aims to keep products and materials in use, at their highest value, for as long as possible. For climate control systems, this will be maintaining and refurbishing units to maintain performance and maximise their lifespan. When systems reach the end of their life, an effort should be made to reclaim and reuse the materials. The recovery, reconditioning and reuse of refrigerants is particularly critical the HVAC sector.
The most obvious benefit of a circular economy is that it significantly reduces waste, as materials are not sent to landfill or otherwise disposed of. It also lowers the embodied carbon of a system and of the complete building. This is because in almost all cases it is more efficient to recycle than create the required components from raw materials. Take aluminium for example, it requires 95% less energy to recycle than to smelt new aluminium. It is similar with refrigerants. Studies have shown that the carbon footprint of reclaimed refrigerant is between 72% and 90% lower compared to new production.
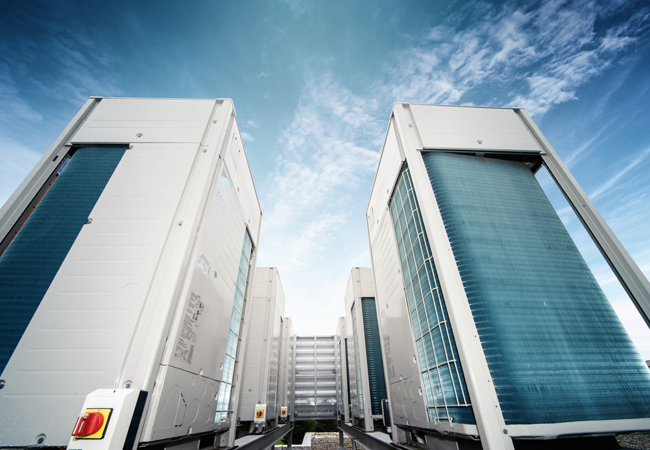
In fact, through the Climate360 and L∞P by Daikin programme – which aim to support the decarbonisation of commercial buildings, refrigerants are recovered from existing systems, before being upcycled and reclaimed to virgin quality. They are then allocated to new VRV systems which are manufactured and sold across Europe. Each year, the quantity of reclaimed refrigerant allocated to these VRV units avoids more than 250,000 tons of CO2eq being generated from virgin refrigerant production.
Perhaps the biggest benefit of circularity regarding refrigerants though, is that it can help the industry to manage the F-Gas phasedown and ensure a robust supply of refrigerants in the coming years. The quota-based reduction introduced by the F-Gas Regulation aims to achieve a significant cut in new hydrofluorocarbons (HFC) placed on the market by 2030 and beyond.
However currently, reclaimed refrigerants are not subject to the phasedown quotas, as under the F-Gas Regulation, reclaimed products are not deemed to have been ‘newly placed on the market’. This means reclaimed products have a crucial role to play in maintaining the supply of refrigerants. Despite the push toward lower global warming potential (GWP) refrigerants, there are still many systems that use the previous generations refrigerants such as R410A.
The weighting of the quota system means that the higher the GWP of a refrigerant, the more of the quota it will use up. As an example, R32 has a GWP that is one third of R410A – 675 compared with 2088. This means suppliers can import three times the volume with the same proportion of the quota used. Therefore, recovery and reclamation of R410A helps boost the volume available for the many systems that use this refrigerant.
Contrary to what is often assumed, contributing to circularity within the sector is not difficult, time consuming or expensive. Regarding refrigerant reclamation, any type can be recovered from any unit during the decommissioning process, regardless of the age or level of contamination and specialist manufacturers can assist with this. Daikin’s Climate360 Reclaim programme (with partner A-Gas) for example, is a fixed fee recovery to recover the refrigerants quickly and cost effectively. Even though there is a cost for this service, it is still often the most cost-effective as the refrigerant will need to be removed anyway. Plus, eliminates the cost of renting cylinders, returning the used refrigerant to the wholesaler and additional labour.
Utilising reclaimed refrigerant is relatively simple. However, there is sometimes confusion about how this is achieved. Due to the nature of refrigerant supply, it will typically be a mix of new and reclaimed product that will be used to charge the system in the factory. To address this, Daikin is committed to utilising reclaimed refrigerant and will administratively allocate the required quantity of previously reclaimed refrigerant to the unit. This means the installer and customer can still be sure of the carbon footprint of the system as well as the zero impact on the F-Gas quota.
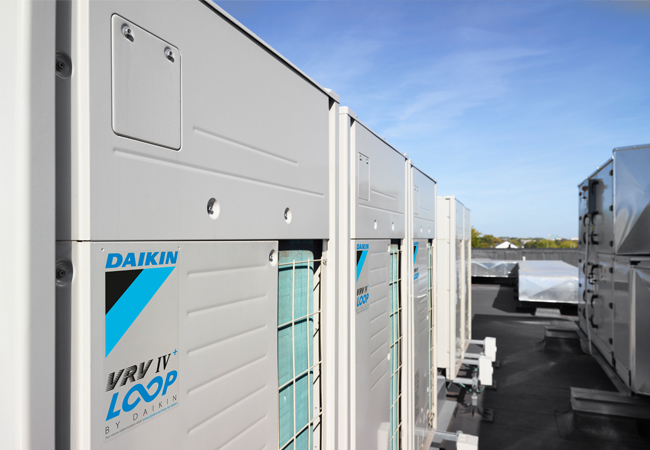
The second element of circularity is the recycling of the climate control equipment and pipework removed from buildings. When managed in the correct way, this ‘waste’ is a valuable resource. Again, by partnering with a specialist, the equipment can be removed and sent to a recycling facility where it will be split it into its components and refined into raw materials before being sold for use in new products.
Establishing a circular economy in our industry is essential to reduce the embodied carbon of building service systems and to ensure a resilient supply of refrigerants as the F-Gas regulation restrictions tighten throughout this decade. While significant advances have already been made, the recovery, recycling and reclamation of materials will become even easier as circularity becomes the norm.
To find out more about the programme please visit Daikin Climate360.
Article by Matteo Dall’Ombra, Commercial Product Manager at Daikin