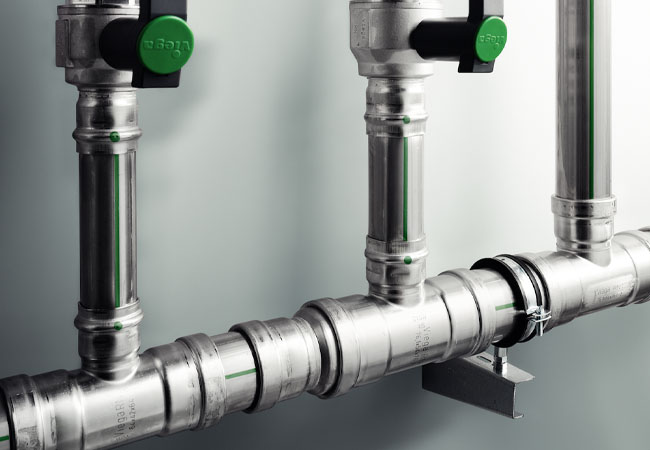
The choice of materials for distribution pipework can have a significant impact on the performance of the system. This is especially crucial for drinking water systems where the safety of building occupants can be compromised if not specified correctly.
Materials typically used for potable water supply pipework include copper, stainless steel and various plastics, including cross-link polyethylene (PE-X), thermoplastic (ABS), medium-density and barrier polyethylene (MDPE), polybutylene and multilayer pipe.
Despite the variety, these materials all have certain properties in common such as non-toxicity and natural corrosion resistance. In addition, copper has long been the material of choice as it is a natural substance that does not pose a risk to health and is non-permeable, meaning it does not absorb anything it comes into contact with, further lowering the risk of contamination.
However, despite the prevalence of copper, the development of modern plastic and multilayer pipe means building service installers have a greater range of solutions and the preferred material may differ depending on the particular application.
Copper or stainless steel pipe may be chosen where fewer fixing points along the pipe length is beneficial or where improved resistance to fire is an advantage. In contrast, multilayer pipe may be preferred where the flexibility to achieve complex routing is an advantage for installation, such as in tight spaces or where very long runs are needed with minimal joints.
Specifiers can also exploit the benefits of each type of material by combining them in a single system. For example, using copper or stainless steel for the underfloor and riser pipes and plastic or multilayer pipe for distribution pipes to the outlets.
Modern press connection technology provides the ideal solution to facilitate this as the versatility allows metal and plastic pipework to be joined simply. The specially designed adapter components not only allow both sides of the connection to be pressed but also integrate with threaded pipe if required.
In addition to the pipe itself, it is important to ensure the other components and materials used in the system do not compromise the quality of the potable water.
For example, the selection of the connection method must be made carefully to minimise the risk of contamination. There are a number of advantages to using press connections for drinking water installations. The cold applied system does not require the use of chemicals or lubricants in the installation process that could contaminate the system, or generate swarf that would need to be flushed out.
However, regardless of the chosen option, it is crucial to ensure that the products have been certified safe for use on drinking water systems. During installation it is important not to mix approved and non-approved products as they may on the surface look very similar. To help installers differentiate between the fittings, manufacturers may colour code their products.
For example, Viega uses a green mark on the outside to denote those suitable for drinking water, with yellow used for gas, white for solar, district heating and low-pressure steam and blue for LABS-free (silicone free) products. Depending on the range, both red and black marks are used to identify Viega connectors that are not suitable for drinking water.
Finally, it is also important to ensure that the products have been handled correctly from the point of manufacture to installation to prevent contamination. For example, wet leakage tests during manufacture can introduce bacteria that can be difficult to eliminate, especially if the conditions the products are stored in allow the bacteria to grow.
A warm environment will enable bacteria such as Pseudomonas Aeruginosa and Legionella Pneumophila to thrive as the optimal breeding temperature range is between 25°C and 45°C. It is always recommended that specifiers look at the product details and select systems that have been dry tested during manufacture. Also, while on-site the pipe, fittings and other components must be kept in a hygienic space to avoid accidental introduction of dirt and contaminants.
Selecting the right materials for use on drinking water systems is vital to protect the health of building occupants. Contamination can occur from the use of unsuitable pipe materials, uncertified fittings and components or even poor handling and storage of approved products. Looking carefully at the product information will help building engineers ensure a safe and compliant system.