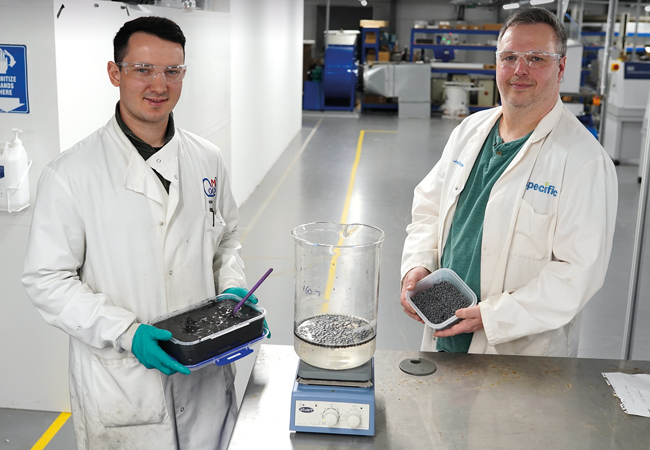
Swansea University’s Jack Reynolds (left) and Jonathon Elvins
Researchers have developed a material for thermal storage, derived from abundantly available seaweed, which they claim is easily scalable and can be sized and shaped to fit multiple applications.
The Specific Innovation and Knowledge Centre and Coated M2A programme at Swansea University collaborated with the University of Bath to develop the material using alginate, an inexpensive, non-toxic seaweed derivative. Sodium alginate is dissolved in water, before expanded graphite is added and one of two methods is chosen to create the material.
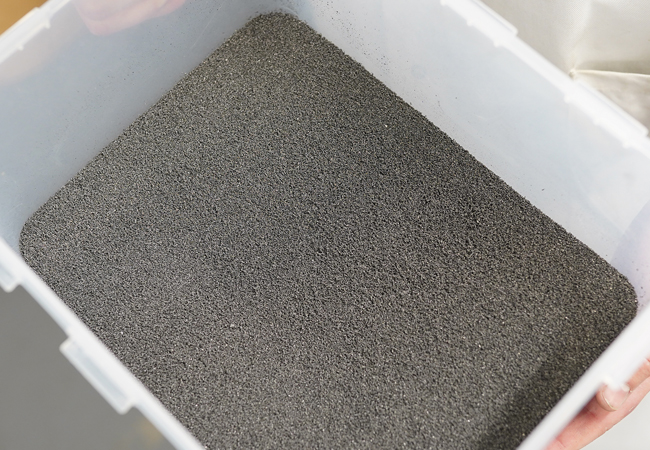
The graphite used in the mix. A few types are being investigated, some which are expanded, some expanded and milled, and others a fine powder
Under the first method, the solution is transferred to a mould for freezing. After being kept at -20°C for more than two hours, beads form and are transferred to a saturated calcium chloride solution. The second method uses a drop-cast technique, with the mixture dropped into thermochemical calcium salt, causing gelation on contact. Once sufficient salt diffusion has occurred, the synthesised beads are filtered and dried at 120°C.
By coupling the store with waste heat recovery or solar thermal generation systems, we are using energy that would otherwise be wasted
Compared with its previous carrier material, vermiculite, the Specific team says the alginate-based beads formed by both methods offer a remarkable improvement in heat-storage capacity. The beads have increased salt capacity and achieve up to four times greater energy density than the vermiculite carrier. This is facilitated by their efficient packing in a fixed bed that maintains good airflow. As a result, the new material can achieve the same heat energy storage capacity in a quarter of the volume.
CIBSE Journal put questions to Jack Reynolds, who led the research as part of his doctorate degree at Swansea University, and Dr Jonathon Elvins, a senior technology transfer fellow and co-author of a paper on the material, published in the Journal of Materials Science.
How does the new alginate-based material compare with other materials in terms of heat storage capacity and efficiency?
The new alginate beads can hold up to three times more salt per unit volume, which will improve the overall energy density of the final system significantly. (The heat is stored in the salt.) This is because the alginate is a binding agent, as opposed to a surface on which the salt can precipitate. This change gives our researchers an opportunity to blend and fine-tune the materials – for example, improving thermal conductivity through the addition of graphite – and reduces the chance of salt being lost through deliquescence [dissolving in moisture from the atmosphere] while in operation. These factors will improve the efficiency of heat capture during the charging cycle and heat release during the discharge cycle, consequently improving the overall material and system efficiency.
How does this material recover and store waste heat?
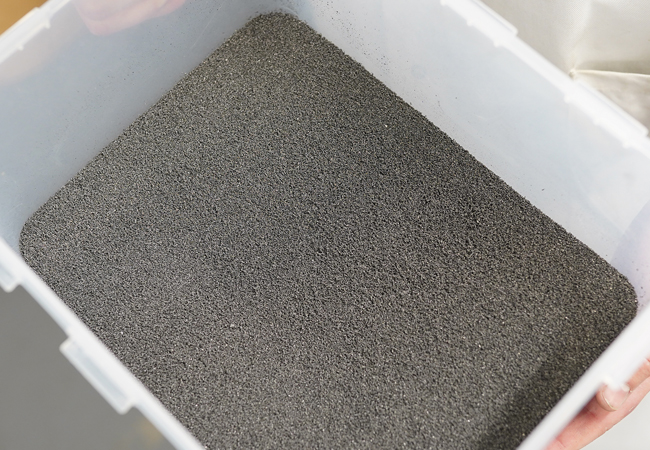
Manual mixing of the alginate/graphite paste to achieve the correct loading level of graphite within the alginate paste. Numerous investigations have been run to assess the viability of differing loading levels
The salt is the work-horse of the system when it comes to heat storage, and the operating principle is quite simple.
Hot air streams are highly energetic. As they pass over the salt, they break bonds that hold moisture within the crystal structure. This results in energy being stored (endothermically) within the salt and the moisture being removed within the airflow. If we can direct a hot industrial wastestream though our materials, a portion of available energy will be stored within the materials via this dehydration process.
Once the moisture is removed, the materials need to be stored in a dry, sealed environment, as there are no energy losses in a perfectly dry atmosphere – and this can be for a substantial period of time; we’re aiming for seasonal storage, ultimately.
To discharge the heat energy, we simply pass a humid airstream over the materials, which results in moisture being collected by the crystal structure and heat being emitted through an exothermic reaction. The heat is transferred into the airstream and transported to the point of use.
For building applications, we would look to develop a modular box where you could add and remove cassettes of material. The primary focus is use in heated air systems.
How might the material be integrated into a building system?
Hot air heating is commonly used in warehouses, arenas and large open-plan buildings, such as shops – these are systems that lend themselves to the operational characteristics of these materials.
Our current thinking is on the development of a modular system that would integrate into an air handling system, very much like a HVAC system providing hot air on demand or a continuous low level ‘background’ heating. We are assessing scaled-up systems to test the effectiveness of this and are getting encouraging results.
The contribution to sustainable heating comes from the reduction in primary energy generation or gas consumption – and by coupling the store with waste heat recovery or solar thermal generation systems, we are also using energy that would otherwise be wasted.
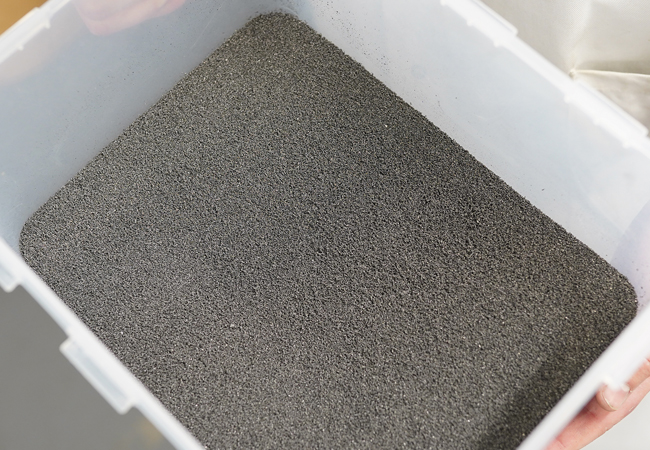
Applying the alginate/graphite paste into silicon mould to create a consistent shape and size of bead
What challenges are there in capturing and using industrial waste heat?
There are a few technical challenges that need to be addressed before these systems become commercially viable. Our focus within the heat recovery developments has been in the low-temperature region, which made sense because this is where traditional heat recovery is technically or economically limited.
The next stages of development will consider the higher-temperature applications and how we can use these materials. We are also looking at the longevity of the materials, determining whether their efficiency on day one is the same as on day 1,000 and beyond, and simple ways to manufacture them in bulk.
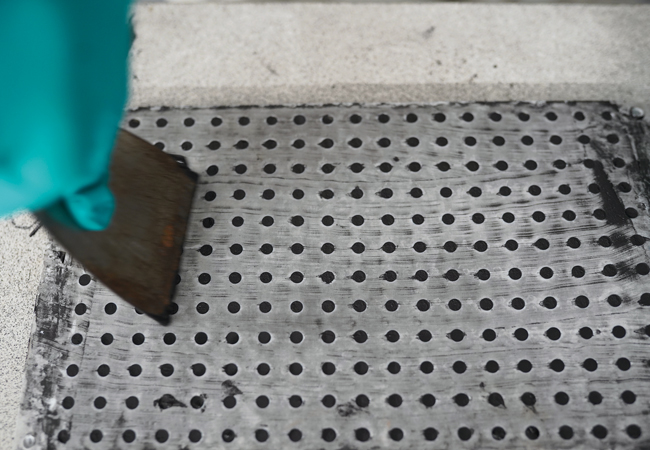
This is a laborious process; the researchers are looking at simple ways to automate it
The commercial infrastructure for this type of heating doesn’t exist yet, and this is where the Specific Innovation and Knowledge Centre can support its development. With strong links to local and national government, we can seek guidance on future pathways and strategies.
Are there specific design considerations for integration into building services?
Yes, but we haven’t got that far down the development trail yet. We are designing prototypes to scale up our laboratory-based systems into larger units and assess the performance changes this brings. The investigations will start with standalone units (akin to a 3kW heater) located within a temperature-controlled test chamber, giving information on the consistency of the materials and the impact they would have on a medium-sized room. Then we’ll look at increased room sizes and full-scale integration. This will require designing systems with project partners who are more familiar with large-scale heating systems.
Could you elaborate on its environmental sustainability and its potential for reducing buildings’ carbon footprint?
The alginate market is growing steadily because of its diverse applications in industries such as food, healthcare and cosmetics. Recent life-cycle analyses evaluated its environmental impact and highlighted that improving the processing efficiency will reinforce alginate’s status as a sustainable raw material.
Sugar kelp, composed of approximately 40% alginate, has a lot of promise, and its cultivation offers an efficient means of carbon capture, with substantial upscaling potential. Over approximately six months in the ocean, sugar kelp reaches its maximum CO2 absorption capacity, signalling the optimal time for harvesting.
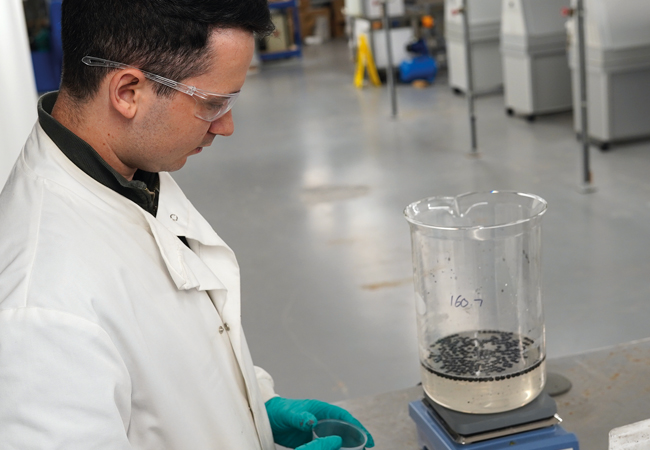
Once the alginate/graphite beads have been frozen, CaCl2, the active ingredient for thermal storage, needs to be added. This is achieved by submersing the beads into a CaCl2 solution. Initially the beads float and then sink as the final product is created
To store the captured carbon effectively, the kelp can undergo pyrolysis, transforming it into a soil-enrichment supplement, securing carbon within the soil. Alternatively, the materials can be stored directly on the deep seabed.
Applying this alginate to sustainable heat storage within building envelopes could yield meaningful results. We are calculating the embodied carbon of these materials and expect to complete this assessment after the upcoming trials. Once we establish the true in situ carbon-capture potential of the process, we’ll have a better understanding of its overall environmental impact.
How will the trial at Tata Steel work?
We have developed a small cage that will be located above a waste exhaust stack from a smelting process. The initial trials will focus on small quantities of material (<10 kg) to gain confidence in the charge times and efficiency. The charged materials will be brought back to our laboratory, where the heat will be discharged and evaluated. Further studies will assess moisture content, salt redistribution, and the overall energy evolved. The trial will help us develop the process for capturing waste heat from the steel plant and using it for space heating.
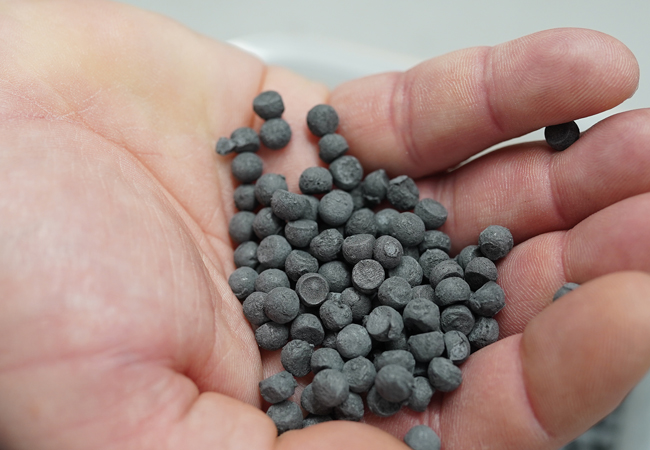
The alginate/graphite beads after being frozen
Are there plans for further research and development?
Plenty! There are plans to: optimise the salt loading to get elevated energy density and maximised cyclic performance; optimise the graphite loading for best thermal conductivity; focus on the best bead size; and look at mixed salt systems. Within building services, we have a PhD candidate investigating the generation of domestic hot water from these and similar materials.