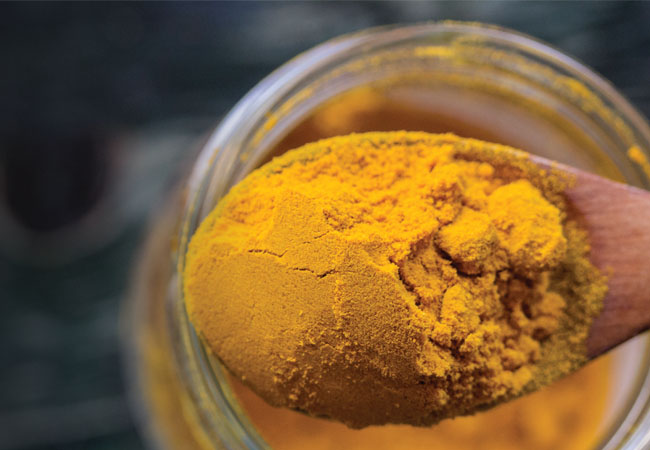
(Credit: iStock credit: Milja Photo)
Kaleesuwari Refinery Private is a large fast moving consumer goods (FMCG) company in India, manufacturing products such as edible oils, pulses, and personal care and household products. The firm, with its headquarters in Chennai, claims group turnover of more than US$500m (£386m) and exports its products to the Middle East, the USA, Sri Lanka, Singapore, Tanzania, Malaysia, the Seychelles and Myanmar.
International engineering firm GSH Group has worked with Kaleesuwari since 2015, managing its refineries across India to produce the steam used for the extraction of oils from nuts, seeds and other raw materials included in its range of products.
Biomass mix
Kaleesuwari takes its environmental responsibilities seriously, with strict policies around waste and power management – including the use of renewable energy – and carbon emissions.
In November 2017, GSH engineers, looking for ways to reduce cost and become more sustainable in their operations, started to mix biomass products – including sawdust, wood-charcoal powder and turmeric – with coal as a fuel for the fluidised-bed combustion boilers in two power refineries at Palani and Chennai, in the state of Tamil Nadu. Over the course of the next six months, the proportion of biomass products used at these refineries increased to 60% and 20%, respectively.
Results have been so positive that GSH is switching over completely to biomass and increasing the range of products it uses
The powdery biomass is mixed with coal and fed under-bed into the boiler’s existing feeding mechanism and burned. Because of the under-bed – rather than modern over-bed – feeding, complete combustion takes place, resulting in the generation of less ash content.
No adverse reaction has been noticed in the boilers and, in fact, the generation of pollutants that form corrosive acids – such as those cited in the Sarbanes-Oxley Act – is negligible with biomass residues. This means that burning biomass will have a positive impact on the lifetime of boiler parts and the facility itself, reducing costs in the long term.
Optimisation and benefits
While slight variations occur in the gross calorific values of the different biomass sources, the GSH engineers ensure the mixed biomass and coal fuel has the correct energy content by conducting random sampling in the onsite laboratory. The engineers then modify the fuel mix and feed-in rate as necessary. This is done by sight by the furnace operatives.
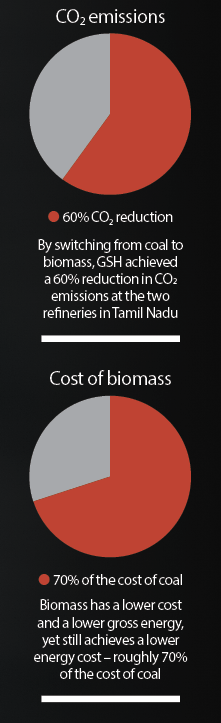
Deciding the optimal fuel blend to ensure minimal fuel use or the maximum steam generation is a skilled job that requires careful management. Mixing the fuels in the right proportion and ensuring the fuel rate through the rotary feeder matches with steam demand is one of the key challenges in this innovative project.
There are also technical benefits to using biomass, which has a higher volatile content and is, therefore, easily combustible. The fuel produces less ash content than coal and contains more oxygen and hydrogen, so it requires less external air. There is also a reduced storage risk compared with coal; stored coal has a propensity to increase in temperature and can self-ignite, whereas biomass has a lower propensity to self-ignite, reducing the associated risks to property and life.
There are challenges in using biomass, however. It is not as easy to handle as coal, and requires more space to store. Its residues also have lower bulk density, so more of it is needed to produce the same level of steam and, therefore, requires more storage capacity.
Environmental advantages
At the same time, there are clear environmental advantages of not using a fossil fuel. Biomass is carbon neutral, so produces less pollution than coal, and contains less nitrogen and sulphur – making it more environmentally friendly to burn. It uses up agricultural and forestry by-products and reduces India’s dependence on fuel imports – a key economic imperative for the country.
Dust-collection equipment – such as the Multiclone dust collector or bag filter, typically used with coal – are deployed to limit pollutants from the combustion process and to ensure the emissions are kept within the levels specified by pollution-control bodies. Both plants comfortably meet state emission regulations from the Tamil Nadu Pollution Control Board.
After burning, the waste ash is collected and used for making bricks. Biomass ash, with no coal-ash content, is also used for soil enrichment, promoting a circular economy.
The biomass in the Kaleesuwari project is sourced from within a 20km radius of the two plants in Chennai and Palani
What’s essential for this process is that the biomass product is sustainable. There have been examples elsewhere in the world of biomass being harvested unsustainably, potentially creating greater problems than the use of coal, but the biomass in the Kaleesuwari project is sourced from within a 20km radius of the two plants in Chennai and Palani.
The products are typically by-products of other production processes: the sawdust is a by-product of local woodworking; the turmeric waste is a result of the extraction and separation of turmeric; the waste chilli powder is generated from the extraction of colour and capsicum pigment from chillis; corncob is an agricultural residue produced during the harvesting process; and the charcoal is derived from the pyrolysis of wood waste.
Biomass is widely available in India because of the amount of agricultural land in use, ensuring that there is a long-term source of biomass products – even if specific types of biomass are seasonal.
In addition to the benefits to the community of reduced emissions, biomass indirectly generates local employment opportunities that would not be available to the same degree with coal – including fuel-truck drivers, biomass unloading personnel, fuel-blending labourers and fuel testers.
Results
By switching from coal to biomass, GSH achieved a 60% reduction in carbon dioxide (CO2) emissions at the two Kaleesuwari refineries in Tamil Nadu, plus a 15% reduction in the cost of steam. The carbon emissions per tonne were calculated using stoichiometric equations – the quantitative relationship between reactants and products.
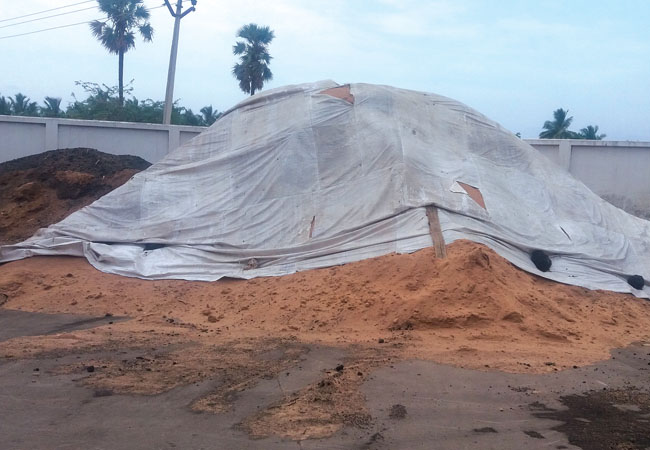
A store of turmeric at one of Kaleesuwari’s refineries
The results have been so positive that GSH is now in the process of switching over completely to biomass and increasing the range of biomass products it uses, including chilli powder.
If both plants were to become entirely fuelled by biomass, the carbon emissions would be on a par with that from coal, but these emissions are treated as carbon neutral because of the CO2 absorbed by plants as they grow. As a result, the biomass combustion systems are treated as nil net carbon emitters.
The Kaleesuwari project won GSH Group India the Environment category at the 2018 Energy Institute Awards, held in London last November. Energy Institute president Malcolm Brinded said: ‘GSH Group should be proud of the inroads it has achieved in reducing the environmental impact of Kaleesuwari’s steam-production process and showing other businesses in India that shifting from coal to alternative fuels can be a viable option.’
Costs
There are many clear benefits of using biomass compared with coal. Coal currently costs around Rs7,000 (£76) per tonne and has a gross calorific value, or gross energy – the amount of heat released by a specified quantity of fuel – of about 5,000kcal per kg. This gives coal an energy cost of Rs1.40 (1.5p) per 1,000kcal. Biomass has a lower cost – Rs4,000 (£43) a tonne – but also a lower gross energy (4,000kcal per kg), yet it still works out at a lower energy cost of Rs1 (1.1p) per 1,000kcal. This is roughly 70% of the cost of coal.
There is seasonal variation on the types of biomass product available – which means price volatility – but, overall, the supply is considered secure because of the large variety of biomass available across India. The price average is also far below that of coal.
■ Anand d G chennai is director of operations at GSH Group