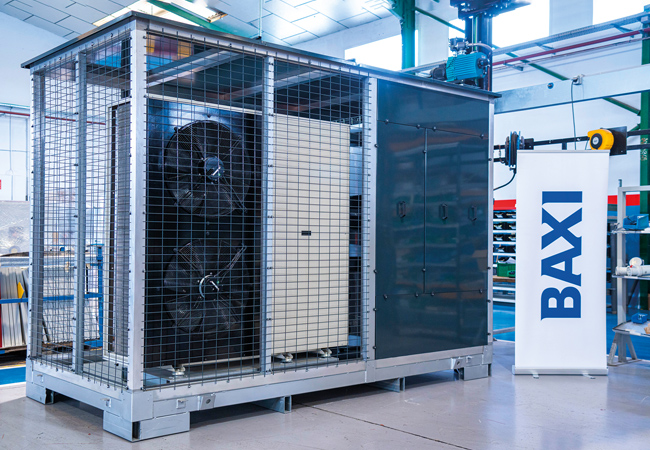
We all know the phrase ‘fabric first’. It means to design with good thermal efficiency in mind, to ease the burden of heating (and cooling) plant.
When we say ‘fabric first’ in the context of renewables, however, we are really asking what can be done to the building envelope to reduce heat loss. A reduction in heat loss means that a lower kilowatt (kW) capacity of heating plant is required, meaning lower capital and installation costs. It also means heat pumps can run more efficiently (see panel, ‘Why heat pumps suit fabric first’).
However, if heat losses are high because the fabric first approach cannot be taken, heat pumps will struggle to compete with the boilers they are replacing in terms of running costs. (Improving the fabric efficiency may not be possible if costs are prohibitively high or buildings cannot be altered for conservation reasons.)
So, what can be done if a building owner wants to decarbonise their heat and the existing building thermal envelope cannot be improved? One option, which is nearly always fast, affordable and efficient, is to design a hybrid system combining boilers and heat pumps – but this won’t do if the client brief is for full electrification of heat.
Many argue that high-temperature air source heat pumps (HT ASHPs) have been developed to solve this problem. However, the solution is not as simple as it is often made out to be. For anyone considering this route, it is essential to investigate the building and system to ensure an appropriate design and specification.
This article considers possible solutions for high-temperature heat pump retrofits and looks at the key areas to investigate before undertaking such a project.
Switching boilers for heat pumps
Discussions of high-temperature heat pumps allude to bringing the operation range into the familiar 82/71°C or, potentially, 80/60°C range. This, however, can be slightly optimistic, as an 80°C flow temperature for even the most modern of R290 (propane) ASHPs is at the very top end of the performance envelope.
BS EN 14825:2022, which recommends conditions for testing heat pumps, states that a high-temperature heat pump must deliver 65°C at -7°C/-8°C (dry-bulb/wet-bulb) ambient conditions, with medium and low classifications required to deliver 52°C and 35°C respectively at the same ambient conditions. Even when HT ASHPs are able to deliver 80°C, this falls slightly short of the 82°C flow required by 82/71°C circuits. Added to which, most heat pumps prefer to operate in the 5-10K ΔT range, making a straight swap on 80/60°C circuits not impossible, but challenging. From my experience, in 82/71°C circuits the boiler(s) will nearly always be set to ~85°C to mitigate hydronic inefficiencies, the most common of these being temperature dilution.
Pragmatically, the challenges involved in the detailed design of swapping out boilers for heat pumps are not to be trivialised. Before embarking on a project of this sort, we strongly recommend that a significant amount of investigative engineering is undertaken. Try to ascertain (but not be limited to) the following:
- What were the original design temperature and loads?
- Are there hydronic inefficiencies – such as exposed, poorly insulated pipework or temperature dilution – that can be addressed?
- Has the building been extended/reduced/zoned or had alternative heating systems installed in localised areas
- Can the true building load requirements in summer, winter and transient months be measured or calculated with a degree of accuracy?
- Are any bounding spatial constraints yielding enough to allow for new plant to be installed?
- Does budget allow for 100% of the required heating power to be via ASHPs?
- Are electrical capacities sufficient?
- Are there factors to offset the potential higher running costs, such as PV?
Design information for dated buildings is often limited to a hand-drawn schematic on the plantroom wall. To add to the confusion, many will have seen a dated building run, at some point, on one boiler out of three during winter, with no complaints.
Improving our understanding of the building profile can be done through installing items such as ultrasonic heat meters, undertaking a full heat-loss calculation (if budget and time allow) and using known data, such as gas-meter readings. Extrapolation of live data or interpolation of fragmented historic data help piece together the jigsaw, for a greater insight into the true thermal profile.
The goal here is to understand what might be changeable, what can’t change, and the risks. For example:
- Flow temperatures may be reduced by fixing hydronic inefficiencies.
- Bracketing of the heating system may reduce the requirement to run all circuits at 80°C or 82°C all year, improving running costs (see below, ‘Bracketing’).
- Spatial challenges can be solved by sizing real requirements through measuring and calculation.
This may take months to complete, and can be further complicated by seasonal conditions. Ideally, this would involve at least a year’s worth of data, with any subsequent installation planned for warmer months.
Bracketing
Bracketing involves consolidating the heating system into frames of known and weighted data. For example, if the survey data shows a sizable constant temperature (CT) circuit serving an air handling plant exclusively, the decision may be taken to ‘bracket’ this out of the overall heating system.
By bracketing this circuit and serving it directly from its own heat pump plant, we are now able to change the tempering or reheat coils to suit a 55°C flow temperature (or lower). This decision alone could increase the heat pump efficiency by up to 150% from a design temperature of around 80°C.
The same principle can be applied to variable temperature (VT) circuits when the CT circuit is unable to deviate from the current design flow temperature.
VT circuit bracketing can yield massive efficiency rewards, as the weather compensation can be undertaken at the plant without the use of mixing valves.
With direct weather compensation on HT ASHPs, the flow temperature could range from 35°C-80°C. If heat losses mitigations have been carried out then, potentially, emitters may be changed when and if possible, to allow a more aggressive reduction in flow temperature.
Why heat pumps suit fabric first
The main reason heat pumps are tied so intrinsically with fabric first is related to flow temperatures.
ASHPs are more efficient when the ambient temperature is higher and/or the sink temperature is lower. Ambient temperature is highly variable in the UK and not within our control. The sink temperature, or flow temperature, is within our power to reduce, when and if we can.
Lower flow temperatures reduce emitter outputs if they were originally designed for higher mean water temperatures, but if less heat is required because of fabric upgrades, the equation should balance itself out.
The proportion of the year when the HT ASHPs must remain at 80°C flow may be offset, in terms of net efficiency, by the period of time that flow temperatures are not required at 80°C via direct weather compensation.
The weighted aspect of bracketing involves understanding the split in capacity required for each circuit. If VT equates to 80% of the overall load requirement, then addressing that in isolation, with CT remaining on 80°C flow, may impact the overall efficiency of the building sufficiently, without the need to replace air handling unit (AHU) coils.
Figure 1 shows a two-boiler reverse return header setup, with CT and VT circuits, that is typical of many 82/71°C legacy designs. Using data from the current VT setup (if available), the VT minimum temperature can be reduced below current settings to assess whether the target space temperatures may still be maintained. Even a modest reduction in flow temperature will ensure higher efficiencies.
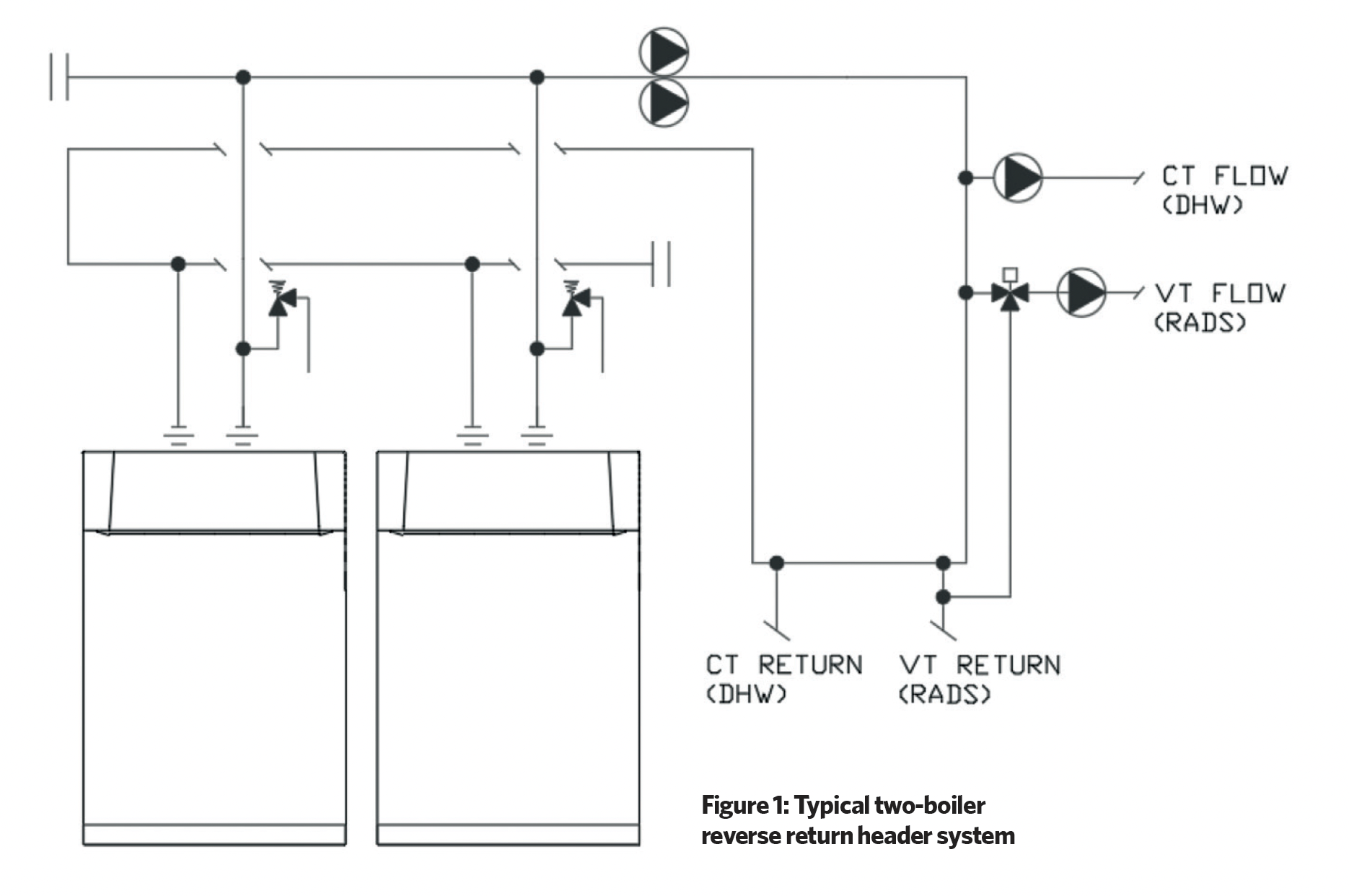
Most HT ASHPs would deliver a coefficient of performance (COP) of approximately 2.2 at 65°C flow and -2°C ambient conditions.
If we were able to drop the weather compensation to below 60°C, output from medium-temperature (MT) and HT ASHPs may be blended, potentially reducing any siting or budget complexities of a full HT.
In the blended MT/HT example solution shown in Figure 2, the heat pumps are cascaded, with a three-port diverting valve being used to deliver heat to the calorifier. Typically, the MT ASHP(s) would act as lead for the directly weather-compensated circuit, supported by the HT ASHP(s) during peak demands. When higher temperatures are required for more challenging design conditions, the HT ASHP can increase the thermal store temperature up to 80°C.
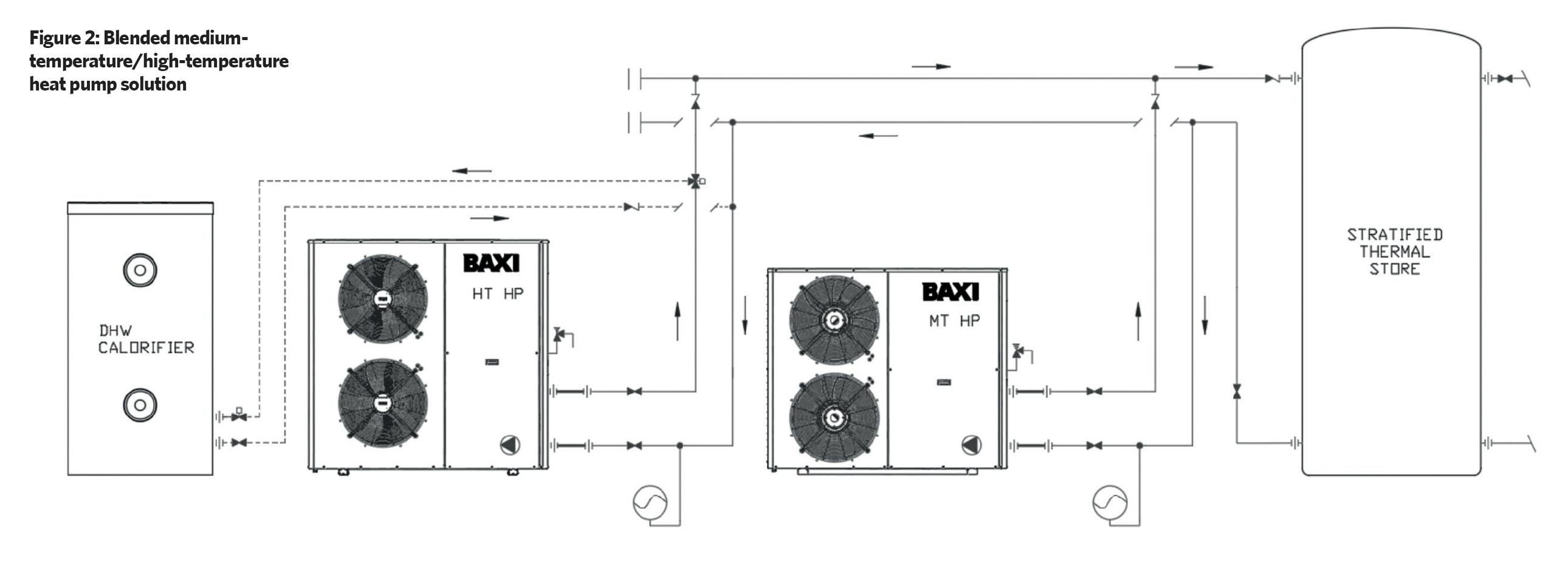
If Figure 1 (the reverse return arrangement) had been designed on a ΔT of 20K, one solution is the alternate cascading method shown in Figure 3. This uses the thermal store lower and upper stratified sections to provide a cascaded temperature rather than the load. This is an identical philosophy to that used with most hybrid solutions. Temperatures are still key, and with good weather compensation a blend of MT and HT ASHPs can still work. However, this solution is more suited to HT ASHPs as, at a higher design temperature of 80/60°C, MT ASHPs are unable to delivery any useful heat.
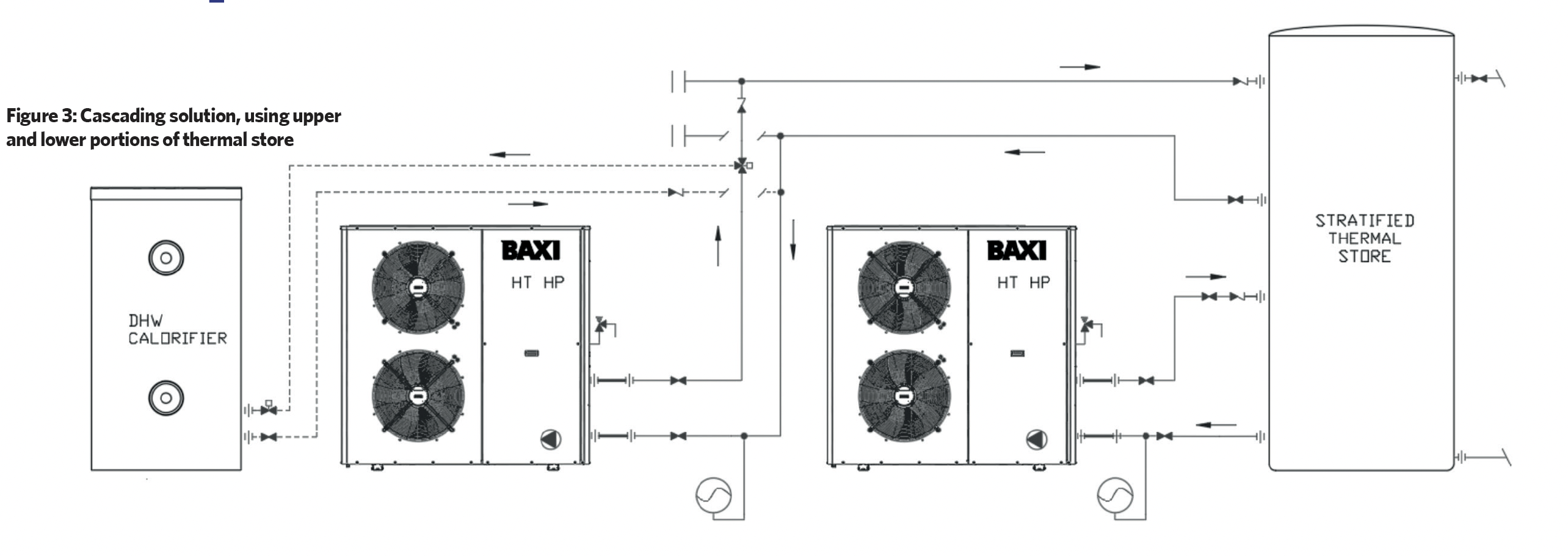
Managing expectations
As clients start to review boiler-replacement projects and the achievable options to decarbonise asset heat, we must still ensure fabric options are considered first.
Emitter replacement to suit low-temperature heating will tend to yield a higher efficiency overall than a high-temperature heat pump system. Heat pumps should not be over-specified in terms of capacity, for economic and spatial reasons.
Ultimately, perfect is the enemy of the good when it comes to decarbonising buildings unable to offer a significant improvement from fabric upgrades.
However, a well-considered assessment of the building thermal profile delivers essential intelligence for a clearer understanding of the impact of the potential system solutions, to ensure true life-cycle benefit.
About the author
Ryan Kirkwood is engineering solutions manager at Baxi