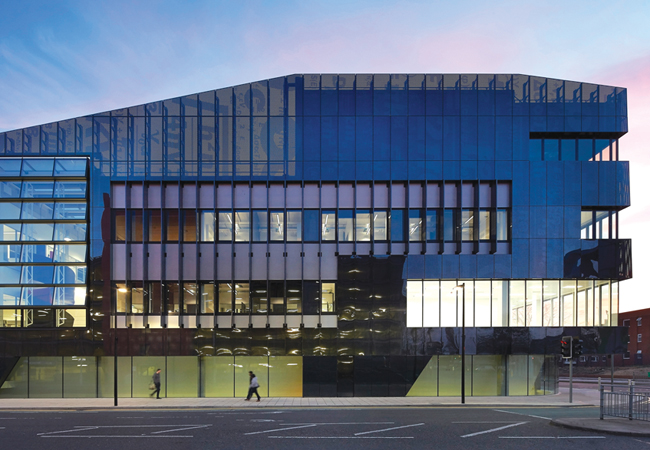
The National Graphene Institute
In 2004, two professors at the University of Manchester Andre Geim and Kostya Novoselov isolated graphene, and such is the fascination with the possibilities and properties of graphene, they were awarded the Nobel Prize for Physics in 2010.
Graphene is the world’s thinnest material and even though it’s only one-atom thick, it is 200 times stronger than steel and its superior strength, conductivity, stiffness and transparency mean its revolutionary properties have applications in electronics, energy and medicine.
To capitalise on the work done by Geim and Novoselov, the University of Mancheseter has built a £61m state-of-the-art laboratory dedicated to the research and commercial development of graphene.
The National Graphene Institute (NGI), designed by Jestico + Whiles is a five-storey glazed building containing 7,600m2 of research space.
Project team
Client: University Of Manchester
Technical architect and M&E consultant: CH2M HILL
Building architect: Jestico + Whiles
Main contractor: BAM Construct
Structural engineer: Ramboll
Project manager & QS: EC Harris
CDM cordinator: Keelagher Okey Klein
Approved building
inspector: HCD
Its aim is to bring academics and commercial partners under one roof to explore potential applications for graphene. The facilities will allow the development of prototypes that could potentially enter into full production. Commercial partners include BAE and Rolls Royce.
Funded by the UK government and the European Regional Development Fund, the NGI is one of the most advanced research laboratories targeting graphene and other two-dimensional materials (one-atom thick). The building is designed for use by 200 researchers and includes laser, optical, metrology and chemical laboratories. It has offices, seminar rooms and two cleanrooms (spaces with very low levels of contaminants), including one that takes up the whole lower ground floor.
Carrying out research at an atomic level requires highly controlled environments. As well as being clear of contaminants, temperatures must be stable and rooms free from vibration, magnetic and noise interference. The facility also has huge energy requirements – the heat gains from the vacuum pumps, fans and magnets, servicing the specialist equipment is 3-400W/m2.
The cost of the services accounts for 50% of the construction cost, which gives you an indication of the scale of the challenge faced by the MEP designer.
Laboratory design
The scale and sophistication of the building services and the required power and cooling capacities for research are similar to those found in industrial research and manufacturing facilities. Capabilities to achieve power distribution for research equipment alone in excess of 200W/m2 result in the potential for large cooling loads. The system is designed so that any space can have environmental cooling for occupants or process cooling for equipment, where it is currently built out as a lab or not.
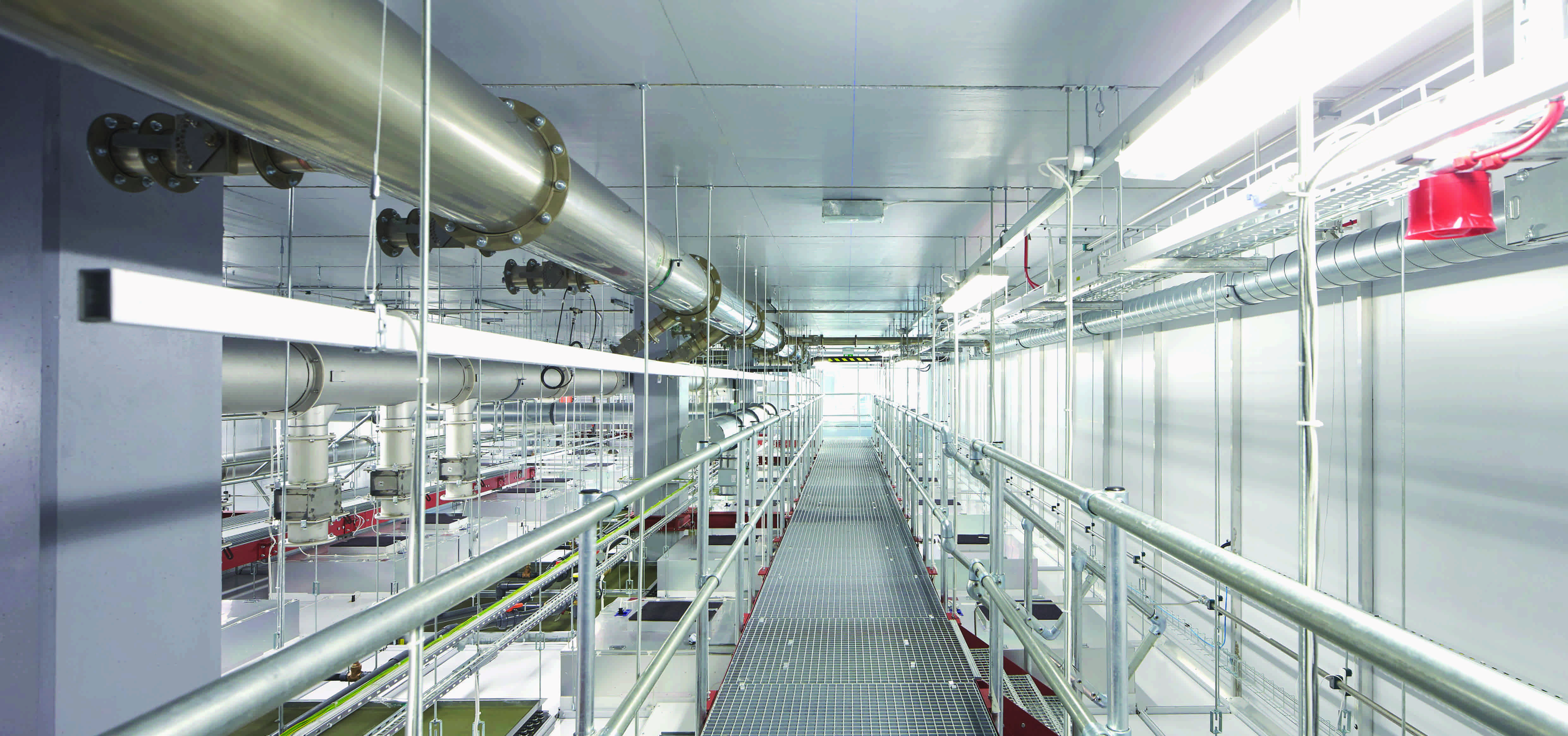
The client brief required the cleanroom and labs to accommodate interdisciplinary research, which meant designing flexible spaces that can meet future research needs.
The lab spaces are in a modularised structural grid, which allows the floor area to be reconfigured into specialised zones or open-plan research space. Process service distribution is through a fixed spine in each floor plate. Standard lab zones have two recirculation air-handling units capable of meeting the high room gains. Control can be done per lab module in parallel or master slave, or by grouped control if labs are opened up. Centralised make-up air is provided to compensate for the three segregated process extraction systems that remove solvents, gases and general fumes.
The exhaust from fume cabinets, wet decks and other ancillary exhausts are considerable, and the systems are designed to remove and treat up to 24m3/s of exhaust.
As such, the make-up air plants are extensive, with a cleanroom plant including pressurisation capacity of 27m3/s and a laboratory make-up air and supply system capable of supplying 11m3/s and recirculating up to 7m3/s. Heat recovery run-around coils were installed between the process exhaust streams and makeup air handling units. The centralised plants control relative humidity within the labs and cleanroom to 45%+/-5%.
Cleanrooms
The centrepieces of the facility are the 1,500m2 cleanrooms at basement and first floor level. These are configured as a bay and chase layout on a raised floor construction.
In this arrangement, the clean bay area contains the process tools and equipment, and clean air is supplied downward from the ceiling mounted FFU (fan filter unit). The air passes into the room through the raised floor and then recirculates up through the adjacent clean bay chase (see Figure 1).
The cleanrooms consist of three main areas: the 1 metre deep raised floor, the 3 metre high cleanroom and finally the plenum space which is 4 metres at its highest point. The plenum height is required to contain the numerous service and ducts. Air inside the plenum is pushed down into the cleanroom. (See the section views in Figure 2.)
Facilities are interconnected by dedicated clean stairs and clean lifts. The lift is fitted out to cleanroom material standards – the lift shaft is epoxy coated, the car has fan filter units in the roof and the shaft is at a negative pressure with respect to doors, landing and adjacent areas.
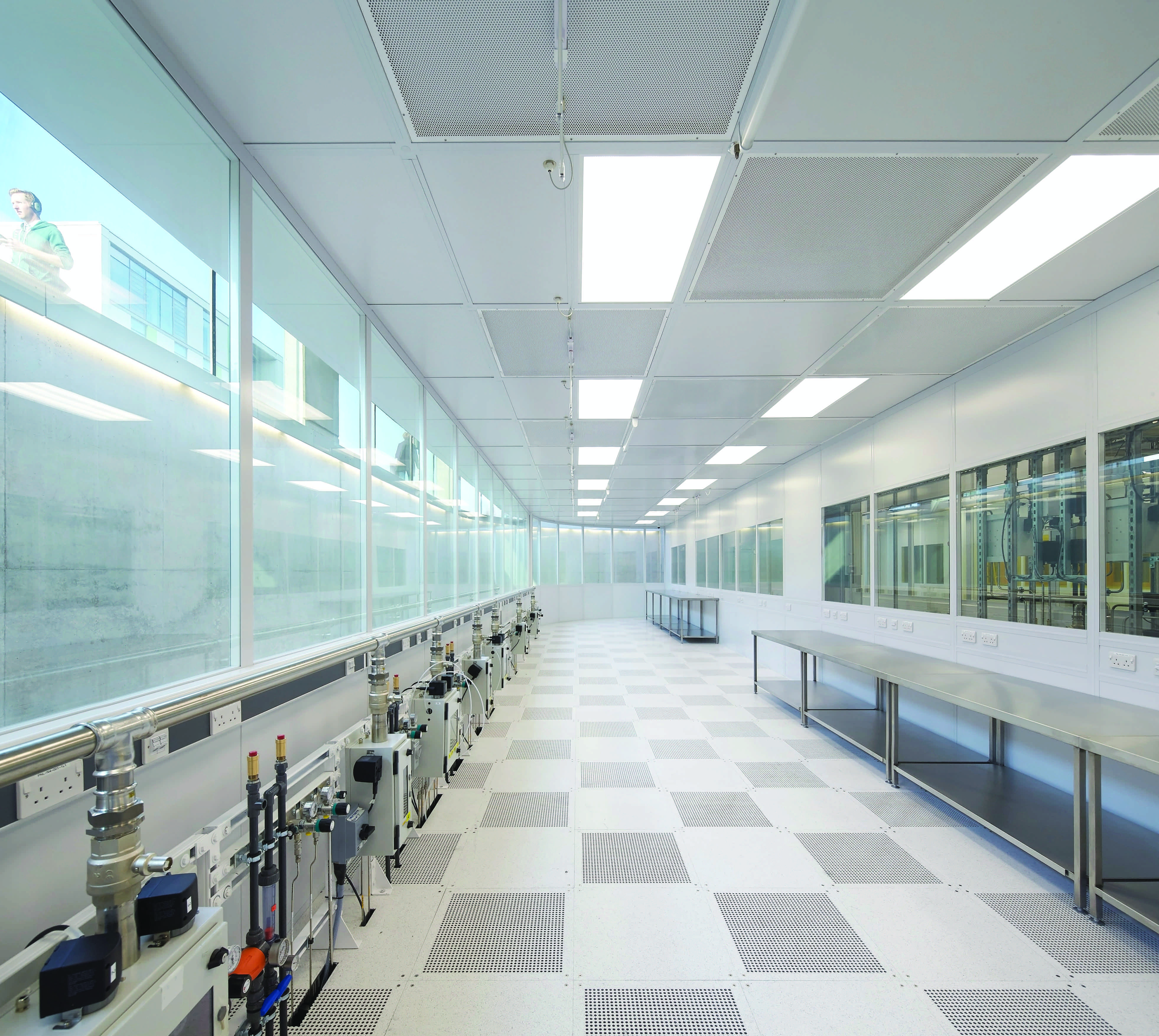
Bays are linked by a work-in-process corridor allowing easy inter-disciplinary movement between shared facilities.
The basement area cleanrooms are currently fitted out with a combination of ISO 5/6 (Class 1,00/1000), which means air must contain no more than 100 particles (0.5 microns or larger) per cubic foot of air for ISO 5 and 1,000 particles for ISO 6.
By comparison, air in a typical office contains between 500,000 to 1,000,000 particles (0.5 microns or larger) per cubic foot of air, so the least contaminated NGI spaces are 10,000 times cleaner. The 400m2 first-floor cleanroom provides an ISO 6 (Class 1000) space which can be adapted to improve cleanliness if required.
The clean air management system has programmable variable speed control, allowing individual spaces to be tailored to the research demands and night time set-back of air flows while still maintaining cleanliness levels. This ensures energy use and room cooling is minimised throughout its lifecycle.
Additionally, the cleanrooms have to comply with stringent vibration criteria of VC-D at the basement level and VC-B on the first-floor area. Rigorous vibration control is essential for research at an atomic level.
Avoiding magnetic interference
The equipment necessary for research into atom particles, such as electron beam machinery, is very sensitive to magnetic interference. Some of the equipment is so sensitive to magnetic fields that the turning of a metal handle can skew results.
To prevent/minimise interference of sensitive electromagnetic equipment, their metals have to be designed out within a 5m radius. This means that re-bars in some areas are made from stainless steel rather than ferrous steel.
If rooms are small, faraday shields have to be built into adjoining spaces to ensure the magnetic field is not disturbed.
The control gear required for LEDs has to be moved out of plenum spaces because of their high magnetic fields.
Extensive design effort was made to isolate the main mechanical, process services and electrical plant from the sensitive laboratory spaces in a structurally independent central utility block (CUB).
Not one, but two frames were acoustically and structurally isolated from the main building via a 50mm isolation joint. The smaller frame contains plant equipment while the second houses the principal laboratory, cleanroom and office accommodation.
Specialist and electrical services
Contained within the main clean space is a suite of microscopy rooms, each with individual air temperature controls capable of maintaining +/- 0.1K over periods of 12 minutes. Increased acoustic attenuation is provided to mitigate potential noise contamination of the scientific measurements which are completed in this suite.
Facilities such as NGI cannot exist without special services that integrate with scientific equipment. Providing for these services, emergency power, early smoke detection and security systems means there are more than 75 different HVAC, electrical and process flow systems and streams covering 3,000m2 of laboratories, cleanrooms and support space.
The electrical services follow some of the traditional laboratory and cleanroom approaches by dedicating and separating power by research lab or cell.
This also requires specialist earthing systems for each laboratory. A total diversified power load of over 3MW is required to serve the research demands as well as the cooling and HVAC plant power requirements.
All systems are backed up by a standby generator.
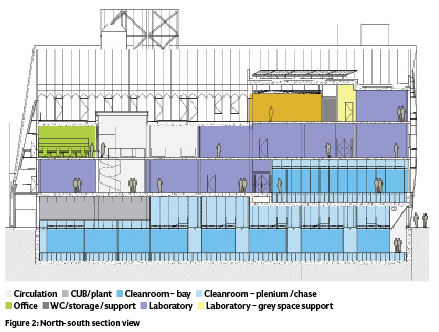
Figure 2: North-south section view
The benefits of BIM
The complexity of the services required for cleanrooms, labs and support spaces within a restricted building footprint made BIM invaluable on the project, and a fully federated model was prepared to ensure the usable research space was maximised.
Clash detection meetings and reviews between consultants and subcontractors occurred every two weeks when the team identified and resolved the main clash points.
The facility was designed to be able to adapt to new 2D material research as well as research on graphene. The building is highly modularised to allow spaces to change and reflect new areas of research. The process and HVAC services are universally distributed from the CUB to meet the primary demands of each space. The spaces are built at a scale that allows secondary systems, such as recirculation cooling, to be added or modified in each laboratory. Plant areas share access to the 3,000kg goods lift, which was sized and planned for delivery of scientific equipment, and there is plant maintenance access at 3.0 x 4.0m with a 2.7m door opening height. The through-and-through lift opens on each floor to the individual plant spaces as well as the access corridors serving the labs and cleanrooms. Although the NGI was an exceptionally tight build, which used 100% of the site curtilage, main distribution headers and cable trays have been installed with some flexibility to allow for higher capacity. Gas and process pipe racks were spaced and coordinated to allow capacity for additional future services. Consideration was also given to the potential future addition of a helium bulk storage tank and basement helium recovery plant to meet the cryogenic research demands of graphene. Built-in resilience
Resilience was a key requirement in terms of future proofing the building and ensuring research is never lost. All major plant has redundancy built in with spare air-handling units, chiller, transformer, pumps and fans. More specialised systems include leak detection, gas detection and monitoring, aspirated smoke detection (necessary due to high air change rates), and extensive telecom/data systems including more than 100km of Cat 6a cabling.
An example of the benefits of this ongoing dialogue was a problem relating to the footing of a 12-tonne roof mounted extraction unit that was overlapping the movement joint and had the potential to cause vibrations throughout the building. Had BIM not highlighted this, the contractor estimated it would have cost in excess of £30,000 to rectify the issue.
Research facilities such as NGI are high-energy users, and it is a big challenge to minimise unregulated and regulated carbon. This starts with passive elements such as the form and façade, which reduce heat gains in research spaces using lots of power.
The demands of low/zero carbon technology and Part L compliance has meant that sustainable engineered solutions are a cornerstone of the project. High efficiency plants, equipment and motors, low energy filters and variable volume flow systems were specified and there is extensive monitoring and automatic controls.
Specialist services
Scientific specifications required by NGI
- Compressed air quality complying with standard ISO 8573-1:2010 [1:1:1]
- High purity 99.999% pure bulk nitrogen gas
- Process vacuum for handling systems
- American Society for Testing and Materials (ASTM) D5127 Class E-1 standard for ultra-pure water
- Waste water drainage and collection system
- Twenty-three separate high-purity process gases (pyrophoric, flammable, toxic and inert).
Although the plant was designed with a standalone capability, the long-term intention is to integrate the primary energy supply onto the University of Manchester’s steam distribution infrastructure fuelled by waste heat from proposed CHP developments. With a view to this, the high-efficiency air-cooled central chiller plant has been designed with a lead absorption chiller utilising this waste heat to provide up to 900kW of base load cooling requirements for the facility.
Much of this cooling can be used at night and weekends as the facility requires continual operation of the cleanroom and process cooling water plant for research equipment. There is also a 17kW array of photovoltaic cells, which helped the building to achieve a BREEAM rating of very good, along with the wild meadow garden terrace and selection of sustainable building materials and methods.
The university believes graphene’s potential will best be developed by creating a second dedicated building, and CH2M is designing the MEP services for the £60m Graphene Engineering Innovation Centre (GEIC), which is designed to progress the research of NGI from technology readiness (TR) level 2 to TR levels 3-6 in the GEIC.
Due to open in 2017, the 8,400m2 facility will be used to develop industry-led applications into prototype and early production. It will also help to consolidate Manchester’s global position in graphene research, and help the university live up to its claim of being the home of graphene.
Ian MacAskill ACIBSE is UK design manager at CH2M Hill