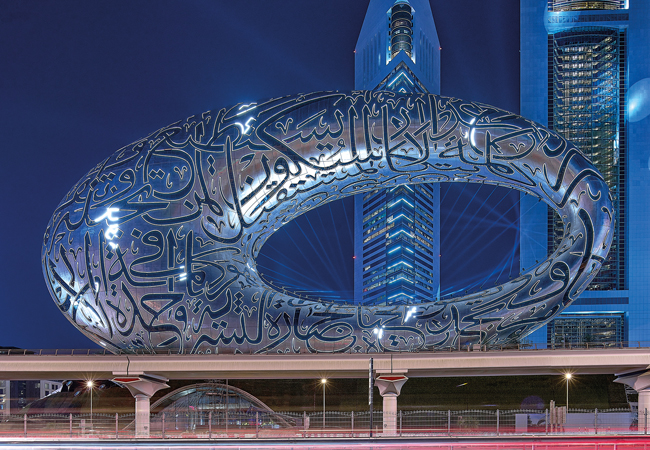
With its bold shape and façade of intricate Arabic calligraphy, the Museum of the Future is already one of the Emirate of Dubai’s most iconic buildings. Opened in February 2022, the museum comprises a torus-shaped structure surrounding an elliptical void, supported above the streetscape on a large verdant mound.
Designed by architect Killa Design and engineered by consultant Buro Happold for the Dubai Future Foundation, its construction pushes the limits of contemporary engineering. Fundamental to both its design and construction was building information modelling (BIM) and parametric modelling.
More than a million people have visited the museum in its first year and it has won 10 international awards, including International Project of the Year – New Build, at the Façade 2022 Design and Engineering Awards.
Without the use of BIM, the MEP systems design and installations would have been almost impossible to achieve in certain areas
In 2015, when the design was in development, working in a 3D BIM environment was still a relatively new concept in construction. Only through fully embracing digital design could the design team realise the abstract geometry of this unusual scheme while keeping museum visitors comfortable in the heat of the Arabian desert. ‘The building’s geometry meant we couldn’t have done it without the entire scheme being designed in a BIM environment, which was groundbreaking at that time,’ said Marko Ruljanovic, associate building services engineer at Buro Happold.
Described as ‘a gateway to a future world’, the cursive Arabic scripts in the building’s interior are glazed to allow daylight to illuminate the column-free interior with gallery spaces beneath. More than just a repository for historical artefacts, the building combines elements of exhibition, immersive theatre and themed attraction, with the ambition to explore the big challenges facing humanity and the creative solutions that people might deploy to overcome them.
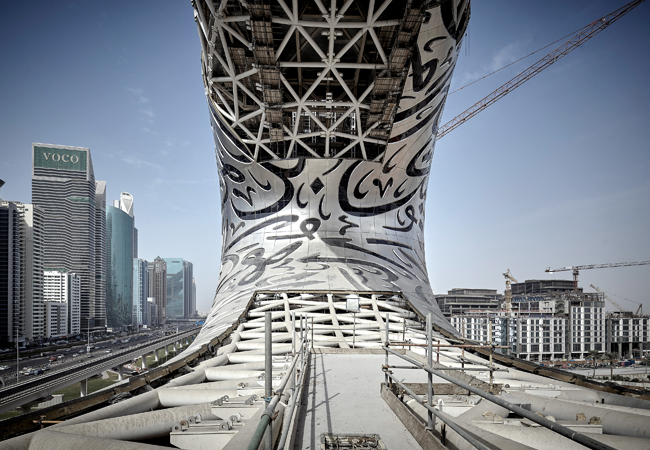
Steels are the same diameter thanks to parametric models
From the outset, Buro Happold’s structural team used parametric modelling to fine-tune the building’s form and structure to make it simpler to construct. A steel diagrid of intersecting tubular steelwork was selected as the most practical system from which to construct the building’s rigid structural exoskeleton and support the museum’s reinforced concrete floor plates. Parametric modelling allowed the designers to optimise the form of the diagrid and ensure that every steel member was the same diameter, to help rationalise its procurement, cost and construction.
A façade formed from more than 1,000 stainless steel-clad composite panels covers this optimised grid of steel tubes and nodes. These contain the windows, which are formed by calligraphy cutouts. The digital model was used to ensure that none of the grid structure was visible through the windows formed by the letters.
Designing the façade
Encasing the grid of steel tubes and nodes is a façade formed from 1,024 stainless steel-clad composite panels. These contain the building’s windows, which are formed in its shell by calligraphy cutouts.
The digital model was used to size and position the calligraphy around the façade to ensure the diagrid’s structural nodes were not visible through the glazed letters.
The script spells out three quotes from Sheikh Mohammed bin Rashid Al Maktoum, vice-president and Prime Minister of the United Arab Emirates (UAE): ‘We won’t live for hundreds of years, but we can create something that will last for hundreds of years’; ‘The future will be for those who will be able to imagine, design and build it, the future does not wait, the future can be designed and built today’; and ‘The secret of the renewal of life, the development of civilisation and the progress of humanity is in one word: innovation’.
Each element of the cursive script is formed from a series of flat glazed panels recessed within the depth of the composite panel façade. There are 10,000 pieces of glass, each cut to shape using water jets controlled using dimensional data extracted from the model. Dimensional accuracy was key to ensuring the script flowed seamlessly from panel to panel around the entire building. The panels also include the LED lighting (14km in total), which outlines the script at night.
The building’s geometry and the calligraphy cutouts mean that each façade panel is unique. UAE-based façade manufacturer Affan Innovative Structures used three-dimensional data from the digital model to control its CNC machines used to mill the mould for each composite panel. The moulded panels were then 3D-scanned to ensure the actual panel matched its digital twin before its stainless-steel finish was added.
Needless to say, Buro Happold’s MEP team also fully embraced BIM. As its design was developed, the digital diagrid model evolved into a full BIM model of the building, which included the glazed calligraphy façade. As a result, the MEP team was able to take the model and use it to develop the environmental systems based on daylight and solar modelling.
External design conditions in the Emirate are 46°C dry bulb, 30°C wet bulb. ‘We modelled everything in 3D; we took the model and put it into IES software and then ran the energy modelling to determine the peak load conditions for the various spaces, to enable us to design the HVAC systems,’ explains Ruljanovic.
Inside the torus, a regular horizontal grid, consisting of six exhibition floors and a floor of admin offices, has been inserted around the elliptical void. The building’s form means that the top floor is by far the largest in area, as it spans the width of the building above the void. This floor has its own dedicated plant space in the curved void between the floor plate and the roof of the elliptical void.
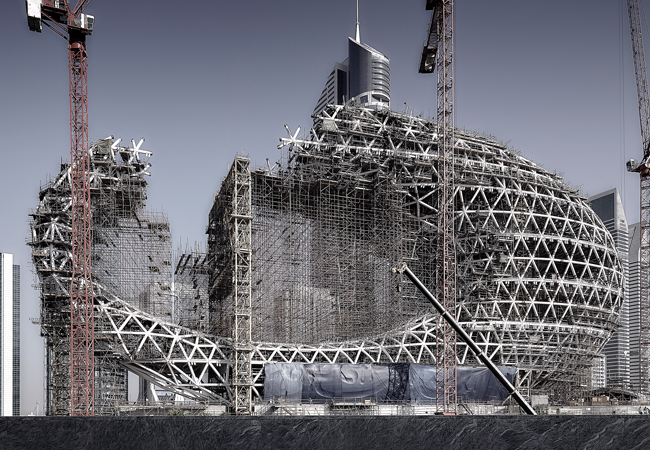
Beneath the torus, the three-storey podium incorporates plant spaces, a 400-seat lecture theatre, and reception lobby.
‘In the underbelly of the top floor there was an unused space above the void,’ says Ruljanovic. ‘So we worked with the structural team and architect to ensure we could get as much of that space allocated for plant as possible, to ensure we did not overburden the plantrooms in the mound.’
Cooling strategy
According to Ruljanovic, fitting the MEP within the building, while leaving clean open spaces and beautiful architecture, was a challenge. A giant lift shaft, staircase and adjacent full-height atrium, located on the opposite side of the building to the void, connect the podium – visually and physically – to the exhibition floors. Vertical services risers concealed within he core connect the basement plant to the exhibition floors.
Exhibition floors are kept at a temperature of 24°C, 50% relative humidity (RH) using a chilled air system. Cooling is provided by dedicated in-room mini air handling units (AHUs), concealed within the 2m ceiling void formed above the 7m-high exhibition spaces. Ruljanovic describes these units as being ‘somewhere in size between a conventional fan coil unit and a full-size air handling unit’.
The mini AHUs are fully recirculating; they incorporate a cooling coil and a connection to the fresh air supply. Variable air volume (VAV) boxes deliver fresh air to the units on demand, based on CO2 levels within the space. To help save energy, the building management system (BMS) is programmed to reduce the unit’s fan speed when conditions allow. Ruljanovic says Buro Happold has tried to make the exhibition systems ‘as flexible as possible’ to give the client a range of options on how they configure the exhibition spaces in the future.
Dedicated AHUs in the podium-level basement and sixth-floor plantroom supply fresh air to the spaces. These incorporate cooling coils, energy recovery units, and variable frequency drive fan motors.
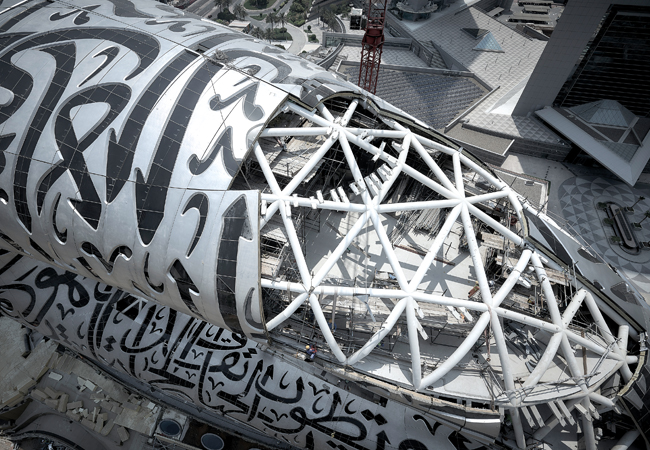
Chilled water from the nearby district cooling network is supplied to the units via heat exchangers located in the basement plantroom. Again, to save energy, the system incorporates a variable speed pump and pressure independent control valves (PICVs) to ensure flow is maintained to the cooling coils, regardless of the system pressure.
Condensate from the AHU cooling coils is recovered and stored in an insulated tank, where it is used to pre-cool the domestic cold-water supply, which can reach temperatures of 30°C in the summer. The condensate is at a temperature of between 12°C and 19°C, similar to that of the AHU off-coil air temperature. When depleted of coolth, the condensate is used for irrigation.
BIM was key to enabling the MEP design team to thread the services through the building. Equally importantly, it enabled the detection of clashes early in the design process, which ensured problems could be resolved in the model, long before work moved to site.
We were dealing with a shape that curves in multiple directions; we had to coordinate the services with the façade and the inner lining of the room, and we had to ensure the building services did not cross the calligraphy windows – Marko Ruljanovic
‘We were dealing with a shape that curves in multiple directions; we had to coordinate the services with the façade and the inner lining of the room, and we had to ensure the building services did not cross the calligraphy windows,’ Ruljanovic explained. ‘Without the use of BIM, I think the MEP systems design and installations would have been almost impossible to achieve in certain areas’.
The building is aiming for Leed Platinum certification. As such, it incorporates a variety of energy and water-saving solutions, including a greywater system that filters and cleans wastewater from the wash hand basins and washroom floor gullies, for use in irrigating planting on the mound using what Ruljanovic terms ‘a drip irrigation system controlled by moisture sensors’. In addition, up to 30% of the building’s power demand is met from a remotely located solar farm.
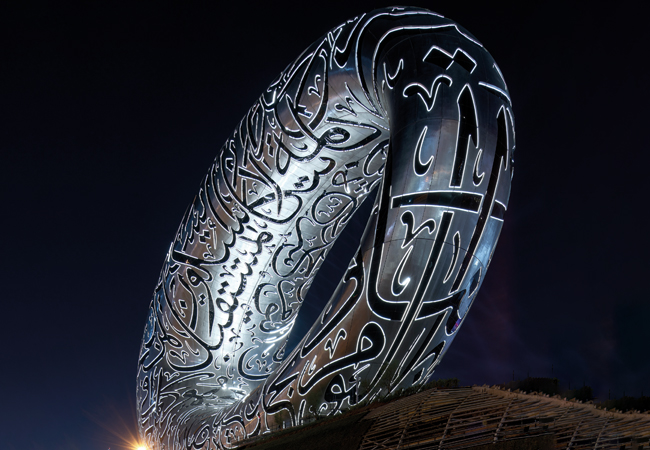
The BIM model was also used to analyse how people would move around the building, to identify circulation pinch points and, critically, to simulate evacuation strategies in the case of a fire.
BIM was also embraced by the project’s main contractor, BAM International. It developed the model further to enable its use in programming and sequencing the building’s construction. Alongside sequencing, the model was also key to ensuring this unique building could be built safely, by digitally defining work fronts and individual installation activities, and assessing the working-at-height activities and complicated crane lifts.
With the scheme completed and the museum open, the BIM model is now being used to support the facilities management team running the building to optimise its operation. In the future, the model will also be used to re-evaluate the movement of people around the spaces as the exhibits and exhibitions change and evolve over time, which is in keeping with the building’s ambition to be a gateway to the future.
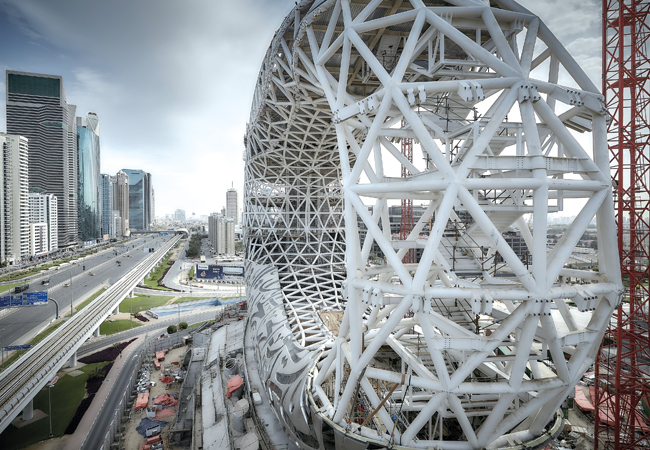
The exoskeleton is a diagrid of tubular steelwork
- The Museum of the Future won the International Project of the Year – New Build, at the Façade 2022 Design and Engineering Awards. The Façade 2023 Design and Engineering Awards are now open for entries. For full details and to enter visit www.cibse.org/facadeawards