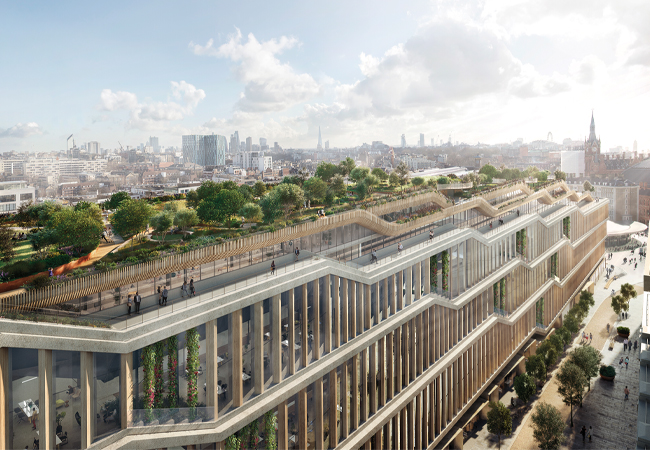
Google’s new London HQ – the multinational technology company’s first purpose-built office in Europe – takes a new approach to the traditional office. Designed by Heatherwick Studio and Bjarke Ingels Group, and currently being delivered by BDP, the team has taken a subtle and considered approach, with a low-rise scheme that sits proudly within the urban context of London’s King’s Cross.
Currently being built, the huge 60,000m2 wedge-shaped ‘landscraper’ known as ‘Platform G’ stretches 330m along the length of the pedestrianised boulevard connecting King’s Cross station with Granary Square, to the north. Among its standout features are extensive landscaped roof terraces, a running track, and a swimming pool.
Project team
Client: Google
Concept architects: Heatherwick Studio and Bjarke Ingles
Design delivery architect: BDP
Building services design, energy analysis and environmental design: Atelier Ten
Main contractor: Lendlease
Structural engineer: AKT II
Cost management: Gardiner & Theobald
Building information modelling (BIM) was a client requirement and essential to coordinate the services within the floor voids. It also enabled early involvement of specialist contractors, which gave the project team more scope for prefabrication and meant access for plant-maintenance needs could be baked into the model at an early stage.
The workers are housed across eight office floors at its 60m-wide northern end, tapering down to five floors at its narrower, southern elevation, where it faces the station.
To further minimise the building’s presence on the streetscape, the design lifts the mass of office floors two-storeys above the street, to enable the west façade to accommodate retail buildings beneath.
The approach is continued inside the building, where workspace flexibility and a loose-fit servicing strategy will enable the technology business to adapt and evolve the office spaces over time.
The structure is unusual in that every third floorplate stretches the full width of the building. These are constructed using reinforced concrete and are stepped along the length of the building, with the varying levels connected by a feature staircase.
The wedge-shaped ‘landscraper’ stretches the entire length of the pedestrianised boulevard connecting King’s Cross station with Granary Square
Between these wide concrete structures, additional floors of cross-laminated timber (CLT) have been inserted. These interstitial floors are set back from the glazed façades to create double- and triple-height workspaces, increasing flexibility while opening up the volume to allow daylight deep into the floor plates.
Atelier Ten, the project’s base-build MEP engineers, worked with the concept architects and delivery architect, BDP, to develop the façade design to complement the triple-height concept. Daylight analysis and extensive parametric modelling were used to establish thermal gains and losses. Sunlight and glare were also modelled; these are mitigated using a top-down/bottom-up blind system controlled by the occupants.
The offices also feature an energy efficient LED lighting scheme incorporating daylight dimming to prioritise natural daylight over artificial illumination.
The façade incorporates a saw-tooth detail, where giant timber mullions shade the angled, glazed elements. Glazing is high-performance, low solar-transmission and high visible light-transmittance, to further reduce the need for artificial lighting while minimising heating and cooling loads.
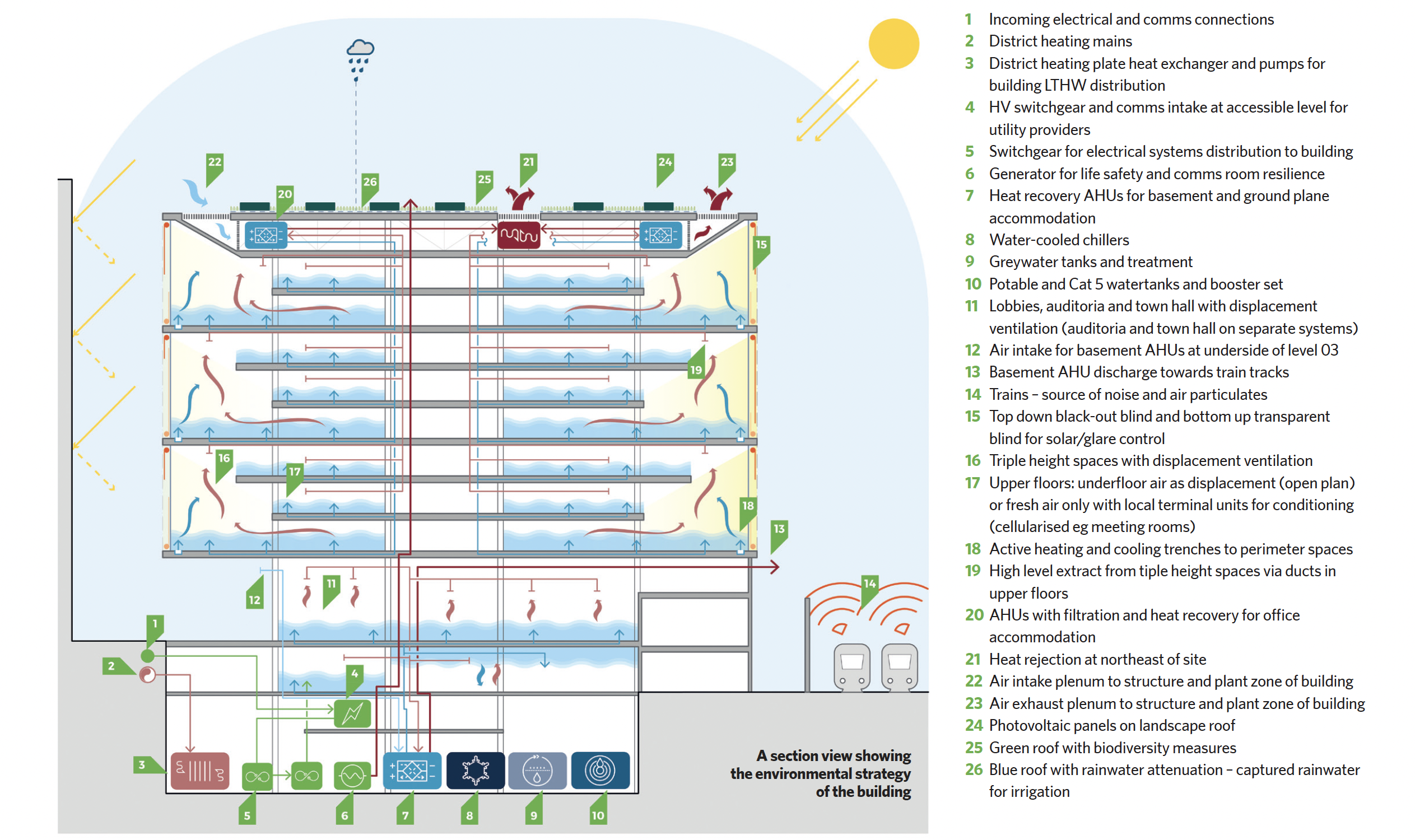
Electrifying experience
The building’s incoming, high-voltage 11kV power supply comes from a dual ring-circuit to provide 8.5MVA capacity in a resilient N+1 arrangement. Two standby 1MVA generator sets, located in the basement, provide a secondary supply to support life-safety and firefighting systems. Extensive sub-metering is provided to monitor energy use on a zone-by-zone basis.
In addition, the building is fitted with a roof-level photovoltaic array with the potential to generate up to 19,800kWh of electrical power annually.
‘We analysed several different iterations of the saw-tooth design to develop the orientation of the fins on the east- and west-facing façades, to ensure there is no direct solar gain on the office floors, while allowing daylight in,’ says Gita Maruthayanar, associate director at Atelier Ten.
To deal with façade-generated heating and cooling loads at source, the floor plates incorporate perimeter four-pipe trench units to provide additional heating or cooling.
Atelier Ten refined the design of the internal office spaces using a mix of computational fluid dynamics (CFD) models to analyse internal air distribution and stratification, along with multi-zone thermal dynamic simulation to ensure occupant comfort. The engineer also undertook CIBSE TM54 modelling to assess the building’s operational energy performance.
Air displacement ventilation
To keep workspaces comfortable, while ensuring future workspace change can be accommodated, Atelier Ten developed a full fresh-air displacement ventilation system concealed in the floor void. ‘This solution provides additional benefits, including improved air quality and increased comfort levels within the occupied space, while also reducing energy use because of free cooling opportunities,’ says Maruthayanar.
Airflow rates are modulated locally using variable air volume (VAV) boxes in response to carbon dioxide levels in the offices. Lengths of flexible ductwork connect each VAV to floor diffusers. ‘The use of floor-based air supplies provides a denser distribution of outlets, which can go a long way to improving flexibility and simplifying workspace reconfiguration,’ Maruthayanar says.
A plantroom has been formed in the void created by the giant steel roof trusses that span east-west above the office floors”
Indoor air quality was an essential element of Google’s brief. It specified a fresh-air supply rate of 16L·s-1 per person, an impressively high volume given the brief was established pre-Covid. According to Maruthayanar, the air-supply rate is equivalent to providing 4.6L·s-1 of outside air per m2 of floor area, which, she adds, is well above the British Council for Offices standard. ‘The brief challenges industry norms in terms of provision of fresh air in contributing to the health and wellness of staff, which should lead to better productivity,’ she says.
In an attempt to minimise duct sizes within the floor void, Atelier Ten initially proposed combining the fresh-air ventilation system with either ceiling-mounted passive chilled beams or cooling pipework embedded within the soffits. However, the decision was made not to have water-based systems on office floors. ‘That meant we had to push up the ventilation rate to deliver sufficient cooling through the underfloor ventilation system, which is why we have bigger ducts and a larger floor void,’ Maruthayanar says.
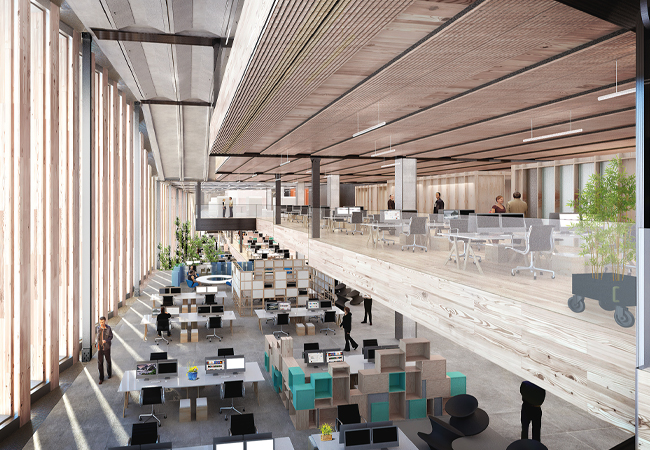
Interstitial floors are set back from the glazed façades to create double- and triple-height workspaces
To minimise the length of ductwork concealed beneath the floors, the engineer investigated pressurising the floor voids. However, Maruthayanar says, there were concerns about potentially high levels of air leakage on the interstitial CLT floors, which could have compromised the volume of conditioned air delivered to workspaces on these floors. ‘If you pressurise the plenums, you would have had air leakage on the CLT floors because their design means they are not fully sealed,’ she explains.
55 air handling units (AHUs), located in what Maruthayanar calls the ‘roof-truss plantroom’, provide conditioned air to the office floors. This plantroom has been formed in the void created by the giant steel roof trusses that span east-west above the office floors. The trusses carry the weight of the landscaped roof garden above and the weight of the floor plates below on the western elevation, which are suspended from them.
Material evidence
While the architectural design pushes boundaries with the building’s form, it is also striving to push boundaries with its approach to sustainability and occupant wellbeing. Construction materials for the project were chosen based on Google’s healthy materials programme. This evaluates building products and materials based on established industry standards that value transparency and occupant health.
‘We looked at moving away from steel ducts to using cardboard ducts, but – because of the challenge of dealing with the extensive amount of ductwork – we decided not to push forward with this option,’ Maruthayanar says. ‘We did look at other materials for ducts and pipework, but the building is quite large, so to move away from conventional materials would have been quite difficult.’
‘To incorporate the rooftop garden, it was necessary to concentrate the majority of engineering services equipment within basement plantrooms or in air handling rooms directly below the garden,’ says Maruthayanar.
The AHUs are sized to slot between the trusses. They incorporate cooling and heating coils to temper the supply air and a heat recovery unit to reclaim energy from the exhaust air.
Chiller approach
Cooling is provided by high-efficiency Turbocor water-cooled chillers. These are located beneath the building in a two-level basement plantroom; this space also accommodates the ventilation plant for the basement and ground-floor operations. The chillers are served by cooling towers discreetly located at the perimeter or the wider, northern end of the roof.
Maruthayanar says that Atelier Ten did look at alternative cooling technologies, including air source heat pumps, but ‘based on the loads, we calculated that the Turbocor chillers were the most cost- and energy-efficient option, particularly as their efficiency at part load is quite high.’
The chilled water system is described by Maruthayanar as variable speed. ‘From the chillers, we have a pump set circulating chilled water around the AHU circuit; a pump set that supplies the perimeter trench units on the office floors; and a pump set serving the ground-level spaces.’ Dividing the system into three allows the pumps to turn off if there is no load on a particular circuit.
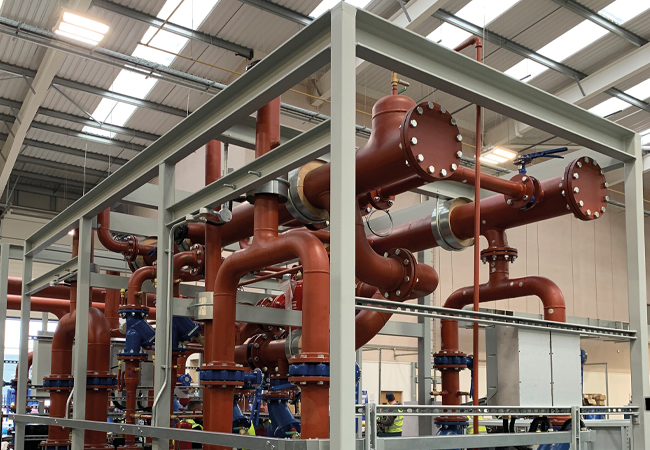
Prefabrication halved the construction time of plantrooms
Heat for the AHU coils (and domestic hot water) is supplied from the combined heat and power (CHP) and boiler plant forming the King’s Cross district energy centre. ‘Although King’s Cross Energy Centre generates heating and cooling, it could only supply heat to this building, which is why we have the chillers,’ Maruthayanar says.
The AHUs are fitted with carbon filters and F9 filters to maximise indoor air quality. ‘This is an enhancement on what is the norm for London office buildings,’ Maruthayanar says. The filtered, tempered fresh air is ducted to the floor plates via risers formed in the building’s five concrete cores.
The benefits of BIM
BIM was a project requirement. Modelling was key to coordinating the mass of services within the floor voids, a task made more challenging because the voids incorporate a structural grid of castellated up-stand beams, on the concrete and CLT floors, through which many of the services had to pass.
‘The best way we could see to coordinate everything was to use the BIM model to position the openings in every up-stand beam, to ensure the services could pass through the castellations,’ Maruthayanar says. There are more than 10,000 such openings. ‘It was quite an intense information process,’ she recalls.
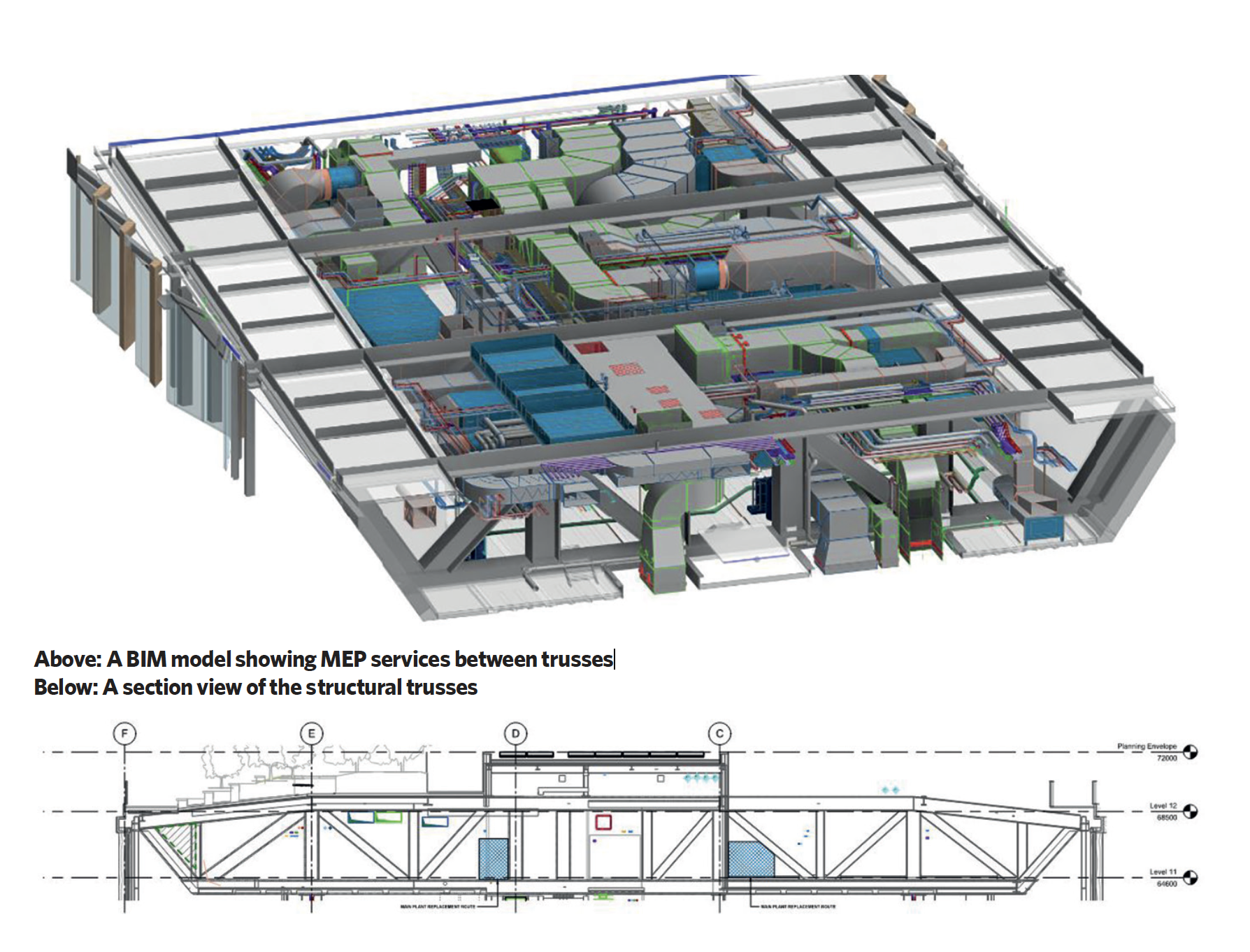
BIM also enabled early specialist contractor involvement, which was helpful in finalising the MEP base-build design. ‘The trade contractors took our RIBA 4A level design and evolved it to a RIBA 4B design with greater specificity over fabrication and installation, which we then adopted back into our BIM model,’ Maruthayanar explains.
Early involvement of the specialist contractors ensured appropriate access for plant maintenance was incorporated into the model at an early stage, along with MEP secondary steelwork and support systems. Maruthayanar says: ‘Involvement of the trade contractors enabled us to provide detailed RIBA Stage 4B drawings, which were a step beyond the standard for MEP projects. This helped reduce the construction programme and smooth the installation process on site.’
Early involvement of specialist contractors ensured access for plant maintenance was incorporated into the model at an early stage
BIM also enabled extensive use of MEP prefabrication in the basement plantrooms and risers. ‘We had allowed zones for the installation of prefabricated service modules within the risers, but we had not developed the structural support system for the modules,’ say Maruthayanar. ‘When the 4B process occurred, the trade contractor responsible for the multi-service modules was able to add all the supporting steelwork, gantries and walkways to the model.’
As well as being able to spatially coordinate the secondary steelwork, its addition to the BIM model enabled the weight of the prefabricated modules to be established, which was useful in helping finalise the structural model. ‘Prefabrication was beneficial, as it meant the modules were worked on off site by various trades simultaneously, which helped speed construction on site,’ says Maruthayanar.
Needless to say, the building will be smart. Maruthayanar says Google ‘will be developing its own network infrastructure to integrate the engineering systems and give users with tools to improve productivity and create a platform of accessible information, to make the building more flexible’.
The giant building is aiming for Breeam Outstanding and Leed Gold certification. According to Maruthayanar, the impact of Atelier Ten’s passive, active and renewable measures is calculated to achieve an overall reduction in CO2 emissions of 22% against Part L 2013 target emissions.