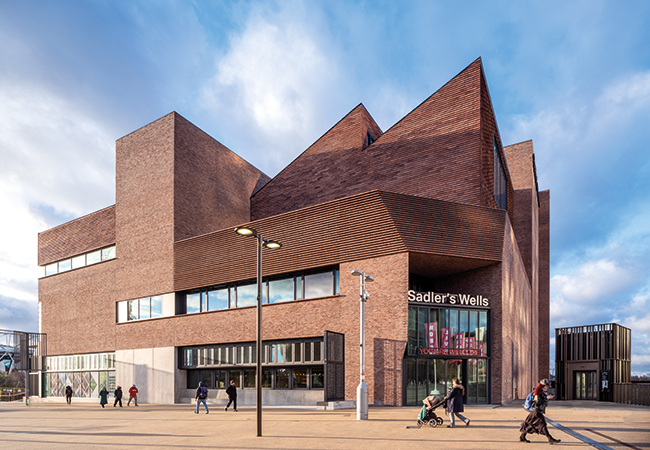
Sadler’s Wells East is the latest addition to the East Bank cultural development, which is transforming London’s Queen Elizabeth Olympic Park. It is a unique building: designed by architect O’Donnell + Tuomey, working with engineers Buro Happold and theatre consultants Charcoalblue, it is a purpose-built theatre for dance. Beneath its brick-clad exterior is a 550-seat auditorium, dance studios, a public foyer, cafe, bar, and community performance space.
Project team
Client: Sadler’s Wells
M&E, structural and lighting engineer: Buro Happold
Architect: O’Donnell + Tuomey
Specialist theatre consultancy: Charcoalblue
Project manager: Mace
Quantity surveyor: Gardiner & Theobald
Specialist contractor – concrete and steel: Kilnbridge
Acoustic isolation specialist: Mason UK
It’s location meant that Sadler’s Wells East had to connect to the Queen Elizabeth Olympic Park district energy network, which was built to supply heating and cooling to the area ahead of the 2012 London Olympics. All the AHU heating coils in the building are supplied with heat from the district heating system (see CIBSE Journal, August 2011). Connection to it was a requirement of the London Legacy Development Corporation, as was the building achieving Breeam Excellent.
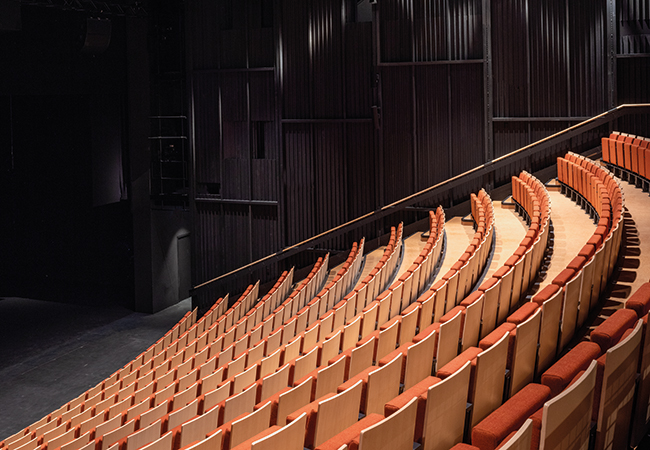
The raked seating in the main auditorium. Each seat has a small grille underneath it to allow air to enter the space
For an art form in which performers are essentially silent, it is striking that the building’s design is all about acoustics. This is perhaps less of a revelation when you consider that it will be home to groups of dancers jumping and moving in unison. This has the potential to excite structural resonances – and with six dance studios and an auditorium, dancers will inevitably be moving to different rhythms simultaneously. To ensure acoustic and vibration separation across all performance and rehearsal spaces in this compact building, Buro Happold has adopted an integrated building services and structural engineering approach.
‘Acoustics is the biggest challenge for a building dedicated to dance and performance,’ says Kenichi Hamada, associate director at Buro Happold and the project’s lead building services engineer.
Sound advice
Of all the spaces, the auditorium and Studio One have the most onerous acoustic requirements. Theatre consultant Charcoalblue specified a preferred noise criterion (PNC) of 20 for both.
PNC curves are a refined version of Noise Criterion (NC) curves, with lower allowable sound pressure levels across both low and high frequencies. This provides a more sensitive measurement system for ambient noise in indoor environments, particularly in spaces requiring critical acoustic performance.
To help minimise structure-borne sound transmission, the building is supported on a reinforced concrete frame, providing mass and stiffness.
The transfer of structure-borne sound between the two venues is minimised by insulating the studio from the auditorium below with what is, effectively, an empty floor. The studio is placed on 100mm-thick natural rubber bearings mounted on giant trusses, which span the 5m-high void.
Hamada says meeting PNC20 criteria for ambient noise with HVAC systems ‘takes a big effort and a lot of technical thinking’.
The foyer, cafe and entrance to the main auditorium are on Level 0. Directly above the auditorium is the largest of the studio spaces, Studio One, which can double as an event space. To the side of the auditorium is the cafe, above which are stacked five smaller studios.
The auditorium comprises a stage with a fly-tower above. Facing this is the audience on a single rake of seating. The dimensions of the stage are identical to that of the Sadler’s Wells theatre in Islington, to enable productions to transfer seamlessly from one venue to another. The space is also flexible: by removing and retracting the audience seating, the stage area can be expanded to allow artists to create work for a variety of configurations.
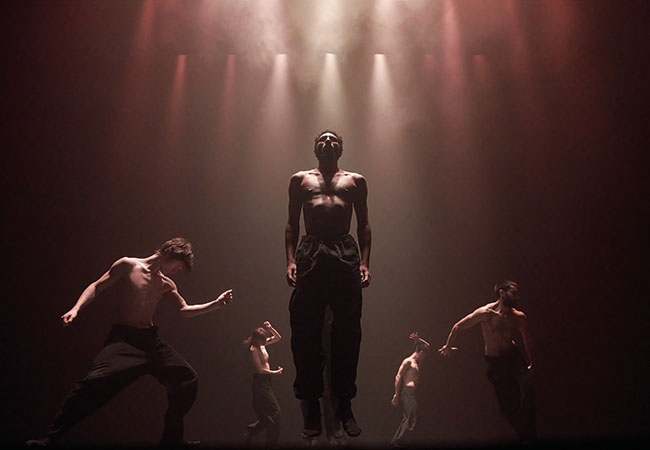
Tempered fresh air from the main auditorium can be diverted to supply additional fresh air to the foyer (right) during intervals, when 300 people could be in the space
HVAC services for the auditorium are driven by the need to provide fresh air and heating and cooling, to maintain the space at a comfortable 22°C ±1K, in line with CIBSE guidance.
‘HVAC for this space was always going to be an air-driven solution to meet acoustic criteria,’ says Hamada. As such, two AHUs provide fresh air: one serves the auditorium and the other the stage; both are capable of operating as full recirculation and full fresh air, and both incorporate mixing/recirculation dampers and thermal wheel to recover energy from exhaust air.
The stage AHU is the smaller of the two. It is designed to keep dancers comfortable during rehearsals without the need to run the main auditorium AHU. ‘A lot of rehearsals will take place on stage without the audience present, so we decided to split the fresh air supply between stage and auditorium,’ says Hamada.
‘HVAC for this space was always going to be an air-driven solution to meet acoustic criteria’ – Kenichi Hamada
Fresh air to the auditorium is from a single, large AHU. Air is delivered through wall displacement diffusers at the rear of the auditorium and two displacement ventilation plenum boxes, one either side of the seating at the back of the auditorium. These are dressed in fabric to complement the adjacent acoustic panels.
With the seating extended, the plenum boxes are covered by the bleachers, so that fresh air fills the plenum beneath. A small grille under each seat enables air to enter the auditorium. This is partially covered to help distribute air evenly. ‘We are predominantly cooling, so front seats would get most of the cooled air as they are the lowest. The grilles were restricted to enable cool air to get to higher seats,’ says Hamada.
With the seating retracted, the plenum boxes are exposed. ‘We designed the supply so there is minimum reaction to seating location,’ says Hamada. ‘Even when the seats are retracted, there are still a lot of gaps, so we can still get the air out onto the floor.’
Fresh air supply rates are controlled by temperature and CO2 sensors. ‘We upped the fresh air rate for the dancers,’ Hamada adds, which means the stage AHU supplies fresh air at 16L.s-1 per person while the auditorium supplies fresh air at 10L.s-1 per person.
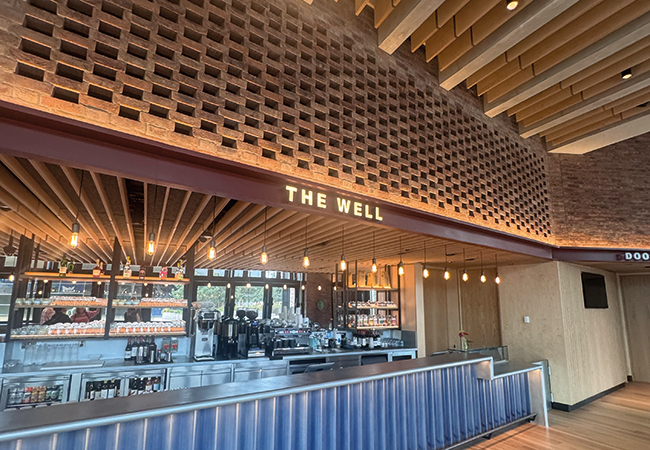
The main auditorium AHU also incorporates a mixing box to preheat/precool the performance space.
Air is extracted from the auditorium at high level at the rear of the raked seating, where it is most effective to remove heat from the occupied space. ‘We found the best location for the extract using CFD [computational fluid dynamics] modelling,’ says Hamada.
There is a supplementary extract at high level in the fly-tower serving the stage AHU. ‘We did not want the entire auditorium extract to be from the fly-tower, because smoke is used for some performances, which would have been affected by the high airflow,’ explains Hamada. The auditorium fire alarm also has a ‘smoke inhibit’ mode to allow smoke effects to be used without triggering the alarm.
To achieve preferred noise criterion 20 (PNC20 – see panel, ‘Sound advice’), duct air velocities have been kept low, at between 3m.s-1 to 4m.s-1, reducing to 1.5m.s-1 at the point where ducts enter the auditorium. ‘Ductwork is really large and duct runs are long to keep the air entry into the auditorium far away from the AHU fan,’ explains Hamada.
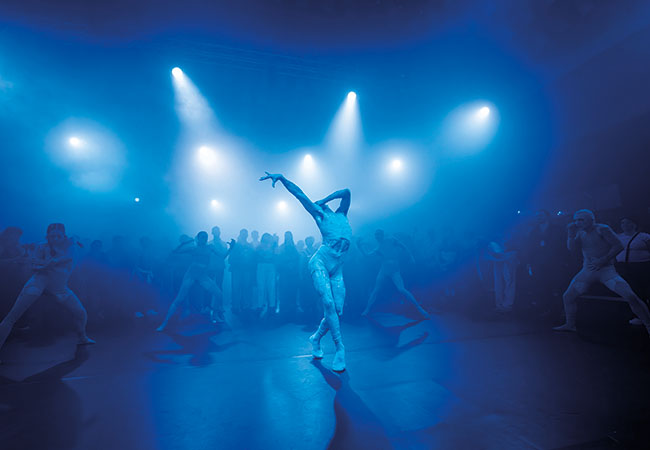
Duct-noise control is further enhanced by three attenuators: one at the point the duct leaves the AHU, a second where the duct enters the building from the rooftop plant gantry, and a third just before it enters the auditorium. In addition, the ductwork has been configured to be symmetrical in layout, so it is effectively self-balancing to minimise the use of noise-inducing volume-control dampers. ‘The benefit of having such large ducts is that the fan power is very low,’ says Hamada.
The two auditorium AHUs, along with the building’s 10 other AHUs, are located outside, in a three-storey rooftop plant gantry. AHU cooling coils are supplied with chilled water from two roof-mounted air cooled chillers. ‘All the vibrating equipment sits on top of the building and had very strict vibration isolation criteria,’ says Hamada.
Performance data
Total energy use (kWh per year): 976,000
Floor area m2 NIA: 8,954
Upfront carbon kgCO2e.m-2 : NA
Peak electricity demand kW.m-2: 96
PV peak capacity: 25.7
Water use: m3 per year: NA
Refrigerant data
Refrigerant: R1234ze for chillers
GWP: 7
Base charge kg: 89
Actual leakage rate: NA
The rooftop plant gantry has been designed to be spacious and accessible by crane, to enable plant to be uprated to deal with higher cooling loads from the changing climate. ‘You might have to go for bigger chillers when the plant is replaced in 20 to 30 years’ time, so we’ve built in extra space and risers to allow the diameter of the chilled water pipework to be increased in the next iteration of the building,’ Hamada says.
The studios incorporate windows to allow in natural light and provide views out towards the former Olympic Stadium. Most also have access to terrace spaces. In some studios, natural light is further enhanced by north lights formed by the saw-tooth roof. ‘We did the modelling to find the optimum balance between natural light levels and solar gains,’ says Hamada.
As in the main auditorium, the studio AHUs supply fresh air, and supply rates are controlled by temperature and CO2 sensors to optimise energy usage. The use of dedicated units prevents noise transfer from ductwork serving multiple studios, and enables units to be turned off when studios are not in use.
With the exception of Studio One, which has a PNC of 20, the studios have a slightly more relaxed PNC of 25. ‘We’re still using big ductwork and low-velocity air supplies,’ says Hamada.
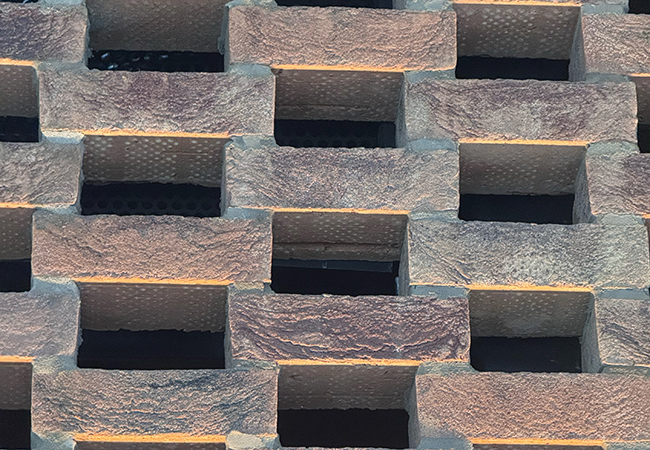
Ductwork in the studios is exposed at high level – grilles had to be at least 4.5m above the floor. Because of the continuous movement of dancers, air distribution is generally not a primary concern for thermal comfort in these spaces, says Hamada. What was a challenge, however, was getting the warmed supply air down to low level in winter using the same grilles that supply cooled air in summer. ‘We did eventually find a product that worked,’ says Hamada. Like the main auditorium AHUs, the studio units are fitted with heating and cooling coils and thermal wheel heat recovery.
In studios two to six, heating is supplemented by low-temperature hot water heating panels. These are under local control to give dancers the option to top up heating. In Studio One heating is supplemented by trench heating beneath its glazed outside wall.
Trench heating is also used beneath the windows in the L-shaped ground-floor foyer and cafe space, which includes The Dance Floor – a public performance stage for community groups. Acoustics here are less critical, and the aim is to strike a balance between a relaxed and lively ambience.
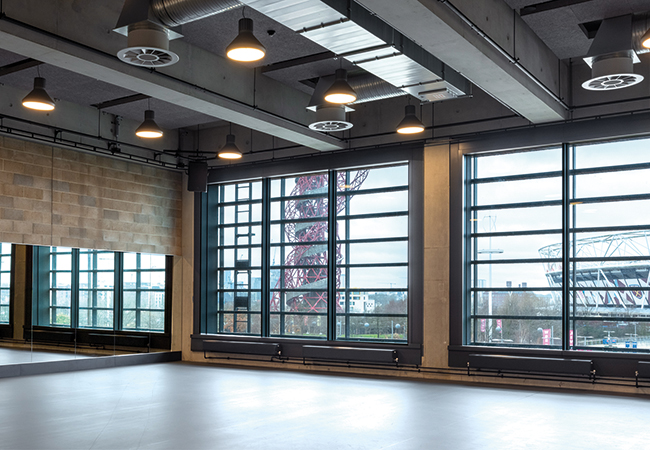
Windows in the studio spaces provide a view out over the former Olympic Stadium
This space has a mixed-mode ventilation strategy. Actuators open windows when outside air is cooler than inside, but only if the outside air temperature is above 16°C. The thermal mass of the brick and concrete walls provides some temperature stability.
An AHU beneath the public performance stage provides heating and cooling. This operates like a fan coil unit on full recirculation. Air from the unit is ducted to the perimeter, where trench heating is located. Cooling is only intended at times of ‘high occupancy’.
The foyer also serves as an interval bar for the auditorium, when up to 300 more occupants will occupy the space. At such times, the tempered fresh air supply to the main auditorium can be diverted to supply additional fresh air.
‘There is a mode where windows close so we can divert the auditorium supply air into the foyer,’ says Hamada. ‘This will drift into the double-height space of the foyer, from where it is extracted back to the auditorium AHU.’
Sadler’s Wells East opened in February and the FM team is optimising the HVAC systems’ operation in response to the dance activities.
‘Do it big, do it right, and do it with style,’ would be Fred Astaire’s advice to them.