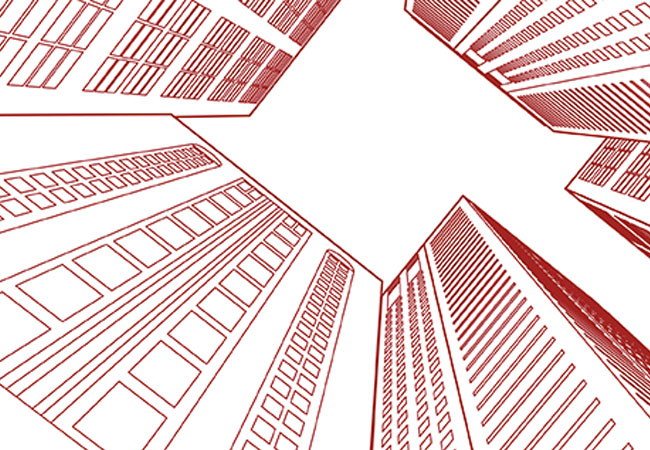
Credit: iStock.com M_pavlov
There have been various attempts within the UK building industry to address the issue of real energy performance. These include the Design for Performance1 framework – which is mainly based on the Australian Nabers2 – Leti self-declaration,3 and the new Breeam 2018 additional energy credits under Ene01.4
To understand how buildings are performing compared with the theoretical performance calculated during the design stage, building managers can use a measurement and verification protocol that has been established by the US Department of Energy. The International Performance Measurement and Verification Protocol (IPMVP),5 promoted by the Efficiency Valuation Organisation,6 assesses investment in energy and water efficiency, demand management and renewable energy projects. The Guide to Energy Performance Contracting Best Practice7 is closely related to the IPMVP, and can be used in conjunction with it.
Measurement and verification is more easily achieved for existing buildings when an energy efficiency strategy is being implemented to reduce energy consumption. This is because the building’s energy consumption before implementation of that strategy can be monitored and measured, and used as the baseline. When commissioning a major refurbishment or new development, however, the client could – and perhaps should – expect the same level of commitment to achieving the calculated energy performance rating during operation.
Sufficient sub-metering is invaluable to model calibration, allowing the model’s disaggregated energy output to be compared with the operational sub-meters
So how can delivered building performance be evaluated against the theoretical performance calculated at the design stage?
In a retrofit project, the baseline is clear – it is the monitored energy performance of the existing building. For new construction, such a baseline does not exist; instead, designers use various other measures – for example, compliance with Part L of Building Regulations – to establish a theoretical energy performance for the building. In the past decade in the UK, Energy Performance Certificates (EPCs) have also been used.
The problem is that, after completion and handover, actual operating conditions can differ significantly from those assumed at the design stage. Option D of the IPMVP, using a calibrated simulation, offers a solution to this.
How it works
Dynamic thermal modelling of the building is carried out during design and, for more accuracy, the HVAC schematic may be added to the model. For unknown operational items, such as occupant density or operational hours, assumptions will be used. This model is the ‘unadjusted design stage baseline’. Once the building is in operation, the model can be modified to match the actual operational conditions, including the small power density, occupancy, operational time and weather data.
All elements of the model – including the specifications, efficiencies and controls – are adjusted to represent the existing building. The modifications will be made so the results represent the operational energy performance. Sub-metering is invaluable in model calibration; sufficient sub-metering of the building systems will allow the model’s disaggregated energy output to be compared with the operational sub-meters.
Once the model is calibrated and the team is satisfied with its accuracy, the two models can be compared. The difference between the adjusted baseline and the calibrated operational energy consumption will represent any discrepancy between the energy performance targeted during design and that achieved in operation.
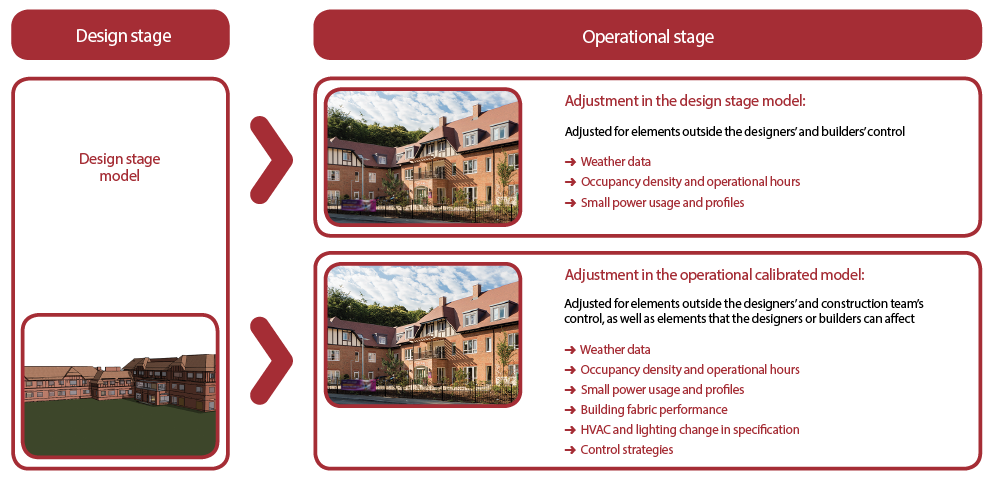
Diagram for measurement: once the building is in operation, the model can be modified to match the actual operational conditions
Validated energy-performance ratings
While, arguably, the overall impact of EPCs has been positive in making UK buildings more energy efficient, the consensus in the industry is that a lot more should be done to improve operational energy performance. A method to validate the energy-performance rating issued for a building at design stage according to the actual energy performance would be a significant step forward.
A model calibrated with operational performance data can be used to produce a validated, as-built EPC rating for the building.8 Once the model is calibrated, it can be used in accredited software to create an EPC rating by reverting to National Calculation Methodology (NCM) operating conditions.
This rating is comparable with the theoretical rating created by the design team. It enables the client to assess the design and – more importantly – the construction quality of their building, to determine whether the targeted energy-performance rating was achieved.
While the method is straightforward, it can be made more effective if the building services are also modelled, rather than relying on the NCM standard lists and benchmarks. This may require enhanced modelling skills, plus additional time and resources for building simulation, to cover completing the calibrated model during operation based on monitored energy consumption.
The success of this method will depend, partially, on good sub-metering data in the completed building, plus post-occupancy evaluation and monitoring. But it allows the current regulatory structure to be used to assess the design and construction teams’ success in achieving the targeted energy-performance rating of a building.
Following this process and reporting on the lessons learned will also identify opportunities for improving energy performance at the building and stock level. So, as building services engineers, we will be able to give robust advice to our clients and be confident in the design decisions we make.
■ Nazli Dabidian is head of energy and sustainability at consulting engineers Mecserve. She is a certified measurement and verification professional and CIBSE low carbon energy assessor
References:
1 Design for Performance, Better Building Partnership – accessed 26 August 2018, bit.ly/2UADU8z
2 Nabers – accessed 26 August 2018, www.nabers.gov.au
3 London Energy Transformation Initiative – accessed 26 August 2018, www.leti.london
4 Ene 01 Reduction of energy use and carbon emissions, Breeam – accessed 26 August 2018,
bit.ly/2CipvGK
5 International Performance Measurement and Verification Protocol (IPMVP), Efficiency Valuation Organisation – accessed 26 August 2018, bit.ly/2XXVhSI
6 Energy Valuation Organisation (EVO) – accessed 26 August 2018, evo-world.org
7 Department of Energy and Climate Change, 2015, Guide to Energy Performance Contracting Best Practices.
8 Burman E, 2014, Towards measurement and verification of energy performance under the framework of the European directive for energy performance of buildings, Energy 77 (2014) 153-163.