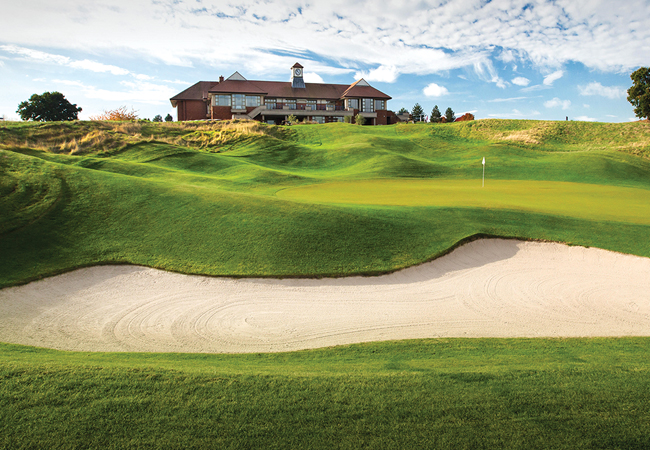
The Oxfordshire Golf, Hotel & Spa has attracted some of the biggest names in golf, with the likes of Nick Faldo, Seve Ballesteros and Laura Davies all testing themselves on its championship course, which features more than 130 bunkers and four artificial lakes.
The lakes are water hazards to golfers, but to Lolli Olafsson, CEO and founder of Geyser Thermal Energy, they offer the opportunity to tap into a reliable source of energy for the clubhouse and adjoining hotel and spa.
Geyser is currently installing a closed-loop water source heat pump system as part of a £700,000 energy retrofit for The Oxfordshire. The retrofit will see pipework take water from the lake to the heat pump in the main plantroom. The aim is ultimately to replace the resort’s oil-fired boilers and chiller with a low-energy heat pump system, linked to a 250kW solar array installed onsite.
Taking aim at energy savings
Geyser’s retrofit heat pump strategy, along with the solar array installation, offers a payback of five years for the resort owners Leaderboard Golf. For Ryan Bezuidenhout, the general manager at The Oxfordshire, the return on investment had to based on the most conservative estimates of potential system savings. ‘We have been very honest. I wanted the most pessimistic numbers possible,’ he says.
Bezuidenhout is banking on a reduction in energy costs to maintain the resort as a top-end destination and increase its profits by up to 30%, as well as reducing its environmental footprint, a key commitment backed by Leaderboard Golf owners, Paul, Jennifer and PJ Gibbons. ‘Energy is such a big cost to our business, and utility costs are only going to head north.’
The project, which is eligible for grants via the renewable heat incentive (RHI), centres on the installation of two modulating heat pumps in the main hotel plantroom. These will replace a R22 chiller and will partially replace the boilers – oil consumption is expected to be cut by two-thirds when the system is turned on, and by even more as the project progresses. Some split air conditioning systems will still be in operation, as they were added locally and are not connected to the plantroom.
The resort has three connected facilities: the golf clubhouse, built in 1994, and the hotel and spa added to the complex 10 years ago. Pipework has already been installed around the outside walls to connect the heat pumps with the spa and pool. Thermal storage has been increased to reduce the peak demand on the heat pumps, and the BMS has been upgraded so that the new plant can be closely monitored (see panel ‘The Oxfordshire’s £500,000 retrofit’).
The Oxfordshire's retrofit
- Replace chiller with two heat pumps totalling 350kW (50kW of which are high temperature for the hot water)
- Upgrade AHUs: replace belt-driven fans with direct-drive fans, fix broken doors and leaks
- Replacement of fan coils
- Increase thermal storage to prevent peak demand on heat pumps
- Installation of tamper-proof TRVs on radiators and limit to 20˚C
- Upgrade BMS to monitor and control system. Alerts added for when system operates outside set parameters
- Replace water softener with chemical-free alternative (Next Scale Stop)
- Add biological water treatment to waste in the kitchen to reduce fats, oils and grease in grease traps, and in sewer pipework and pumps
- Add variable speed drives to circulation pumps
- Add water treatment and sludge protection in heating system
Future phases
- Removal of oil boilers
- Upgrade of taps and shower mixers
- Reduction in use of DX air conditioning
Olafsson says energy retrofits should be approached in three stages: first, reduce consumption; then calculate future loads; and, finally, see what energy resources are available onsite.
In January, Bezuidenhout initiated stage one – an energy-saving strategy whereby heating and cooling of hotel rooms was controlled manually by guests rather than left on permanently. ‘Aircon used to be blasting 24/7, as were the towel rails. That’s bad practice and complacent,’ he says. ‘The argument is you’re providing a comfortable environment, but you don’t have to have air conditioning on 24-hours a day.’
Bezuidenhout says guests have not noticed the change because rooms only take 20 minutes to regulate and maintain a desirable temperature. He says hotel staff carrying out inspections of bedrooms after guests check out ensure everything is turned off (to prevent staff changing corridor temperatures, TVRs were installed on the radiators and set at 20°C). Since the initiative began, energy consumption has already fallen by 11%.
Calculating future energy loads and establishing a benchmark for energy use was not straightforward, says Olafsson. Energy use was not monitored for different buildings, but the resort did have occupancy reports and they knew how much oil was being used. Electricity use was fairly steady over the year.
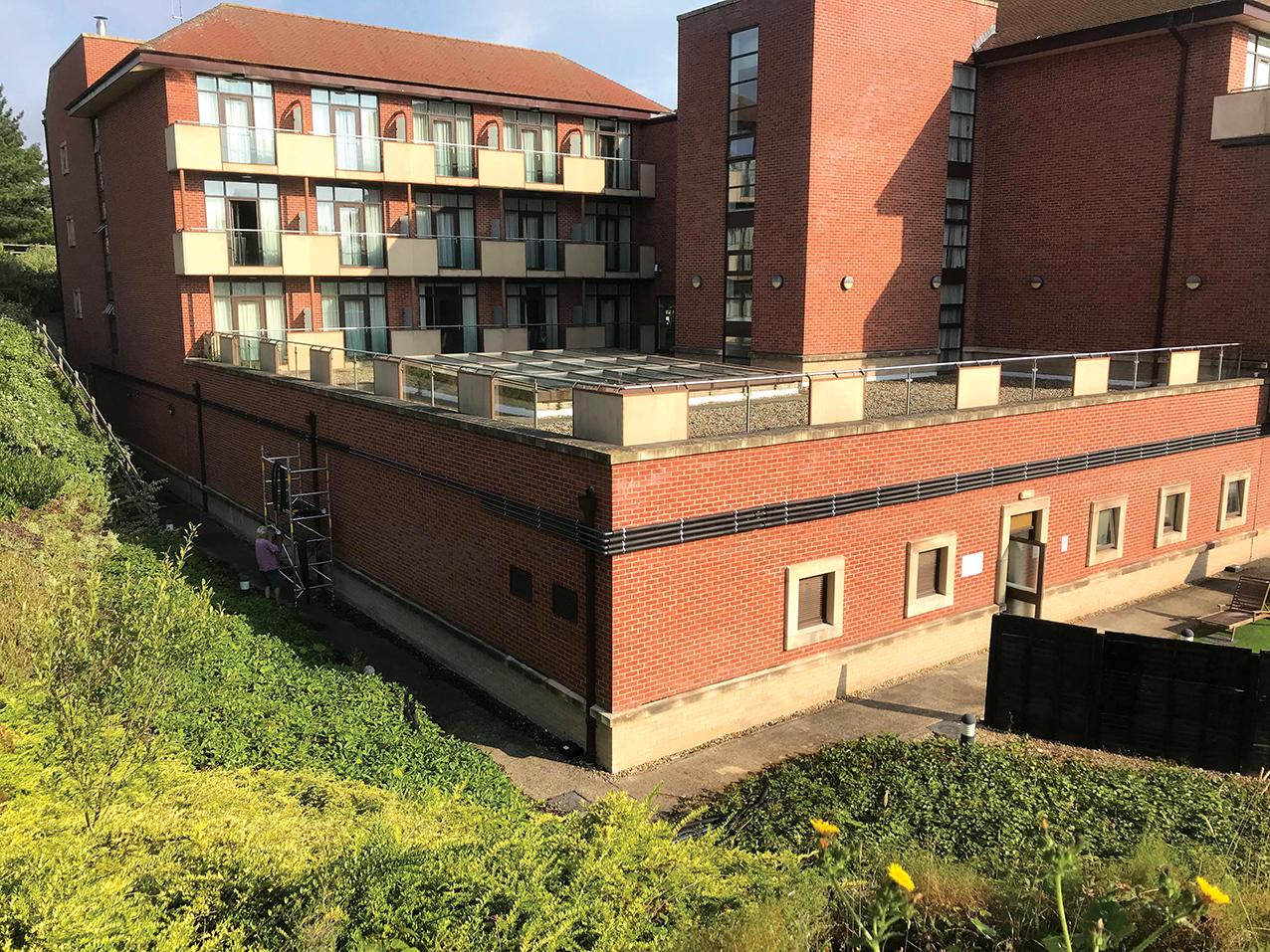
New pipework installed on external walls to connect the pool with heat pumps
The savings are based on oil consumption; reduction in other M&E plant, such as pumps and fans, has not been included. For example, the use of heat pumps rather than boilers means the air handling units (AHUs) have been changed to run on lower temperatures, saving energy (as running AHUs at higher temperatures would require high temperature heat pumps, which are more expensive and use more electricity). There is also a saving from belt-driven fans replacing direct fans.
For Olafsson, using lake water as a source for the low-temperature heat network was a no-brainer. ‘The beauty of water is that it is a fast-replenishing energy source, as water absorbs heat much more quickly than earth,’ he says. ‘There is plenty of capacity in the lake, and we can add more if we have to in the future.’ The lakes were built originally to function effectively as a rainwater harvesting system.
One of the alternatives was a ground source heat pump, but the ground loops would have taken up space where the PV array is set to be installed, says Olafsson.
The lakes are used as a source of irrigation for the greens, which creates movement in the water, reducing the risk of freezing. ‘We don’t have to worry about the cold,’ says Olafsson. ‘The temperature of the lake in winter can go down to 7-8°C, and we could potentially take heat out with the temperature down to 3°C.’
Six 90mm pipes at 600mm depth will run from the hotel to the lake between golfing holes, so the trench work will not disturb the golfers on the course.
It is a low temperature system – the flow temperatures for the heating are 50°C/45˚C and 60˚C/55˚C for the hot water – which means heat losses through the pipework are minimised and that cheaper plastic pipes can be used rather than steel, says Olafsson.
A closed rather than open water loop was selected in part because of the low maintenance required, says Olafsson. ‘An open system can have issues with filtration. A closed loop is more reliable as long as the water is well maintained. The circulation pumps are the only moving parts,’ he says.
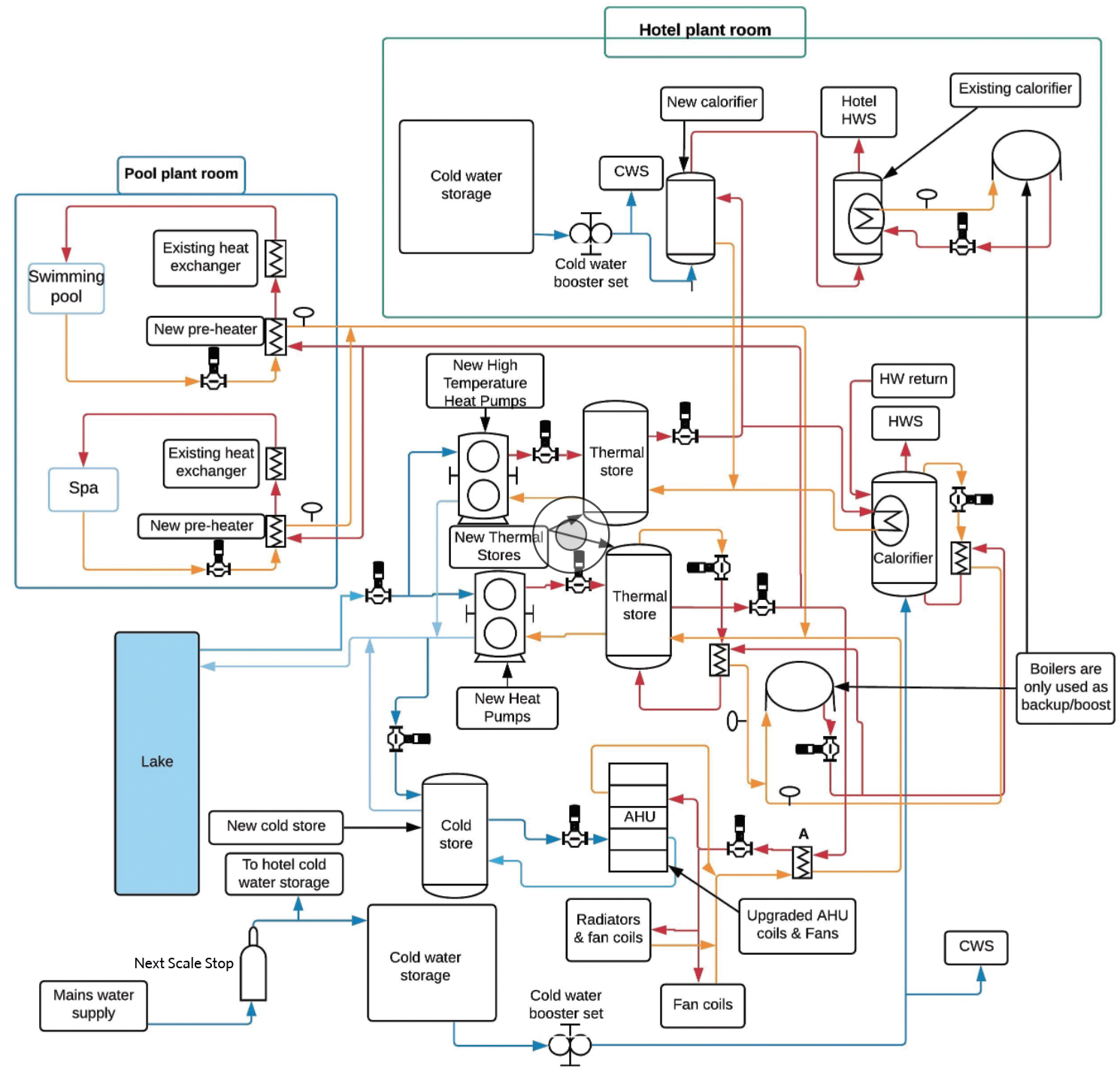
Schematic of the new services layout in the plantrooms
Buffer tanks for both hot and cold water will reduce peak loads and enable the hotel to take advantage of cheaper off-peak electricity, says Olafsson.
‘If you base your heating system on peak loads for an hour a day, you might have a system that’s 50% larger than if you had a buffer tank,’ he says.
The BMS has been upgraded to help the team understand how the system works and what the loads are in the pool, spa and air conditioning. ‘The unknown is what the total load will be. There will be continual improvement,’ says Olafsson. ‘We are pre-heating the pool and spa, and the idea is to eventually increase the capacity of the system to do all spa and pool heating.’
The system’s existing water softener is being removed and replaced by a non-chemical treatment called Next Scale Stop. Olafsson says this uses a process known as template assisted crystallisation to convert the minerals in hard water to harmless, minuscule crystals. He says the system requires no electricity, saves water and prevents excessive brine water from contaminating waterways. Olafsson estimates that adopting this method of scale prevention will save the hotel and spa 1.5-2 million litres of water a year.
The pipework, solar array and plantroom will be installed this autumn, and the heat pumps turned on, initially working alongside the oil-fired boilers that act as a backup. ‘The fun part will be switching it on and seeing what the performance is,’ says Olafsson, who is keen to continuously assess system loads and performance so the heat pumps can provide all the heating demand onsite – including the spa and swimming pool – and all oil boilers can be removed.
Needless to say, a proper maintenance regime will be in place. ‘If they are not maintained, the efficiency can be eroded and we’re back to where we came from,’ says Bezuidenhout, who is bullish about how the retrofit will affect The Oxfordshire’s bottom line: ‘The potential energy savings, RHI and solar installation gives us a fighting chance of making a huge impact,’ he says.