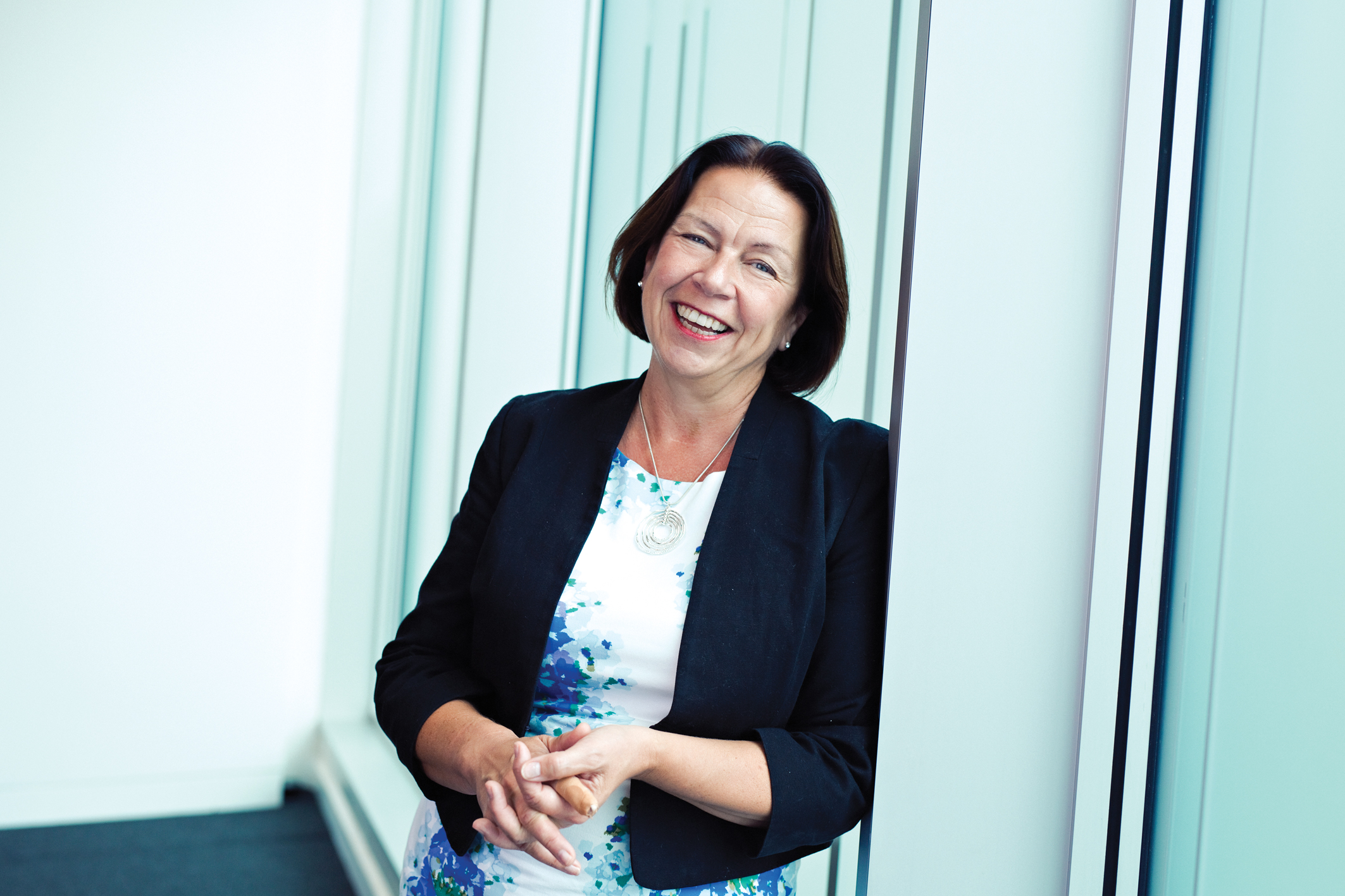
As head of sustainability at one of the UK’s biggest property companies, Debbie Hobbs has the opportunity to cut carbon emissions from a large chunk of the country’s commercial real estate. Legal & General Investment Management (LGIM) Real Assets manages £24.9bn of property on behalf of investors, and has 2,700 buildings, occupied by 5,000 tenants. If all of these buildings were run efficiently, a vast amount of savings could be made.
Hobbs says the difference between a typical, well-maintained property and a wasteful one is 40% fewer carbon emissions – but, she adds, there is a major issue for the property industry. ‘In the UK, we have lost the engineering skills to operate buildings. We design lovely new, shiny buildings, but we don’t maintain them properly.’
Hobbs believes the supply chain lacks the technical knowledge to operate HVAC effectively. ‘Ultimately, clients have driven the market through competitive tendering, and demanded lower and lower prices from managing agents, who have responded by having fewer skilled staff.’
The state of engineering in the real-estate industry has been in a downward spiral since 2008, claims Hobbs. ‘The strategy was fine for a year after the recession, when everyone wanted to minimise cost, but it doesn’t work if the long-term goal is to optimise buildings.’ This isn’t just bad for the environment, adds Hobbs – it also means tenants have higher bills, and property owners have more risk in their portfolios.
She believes the supply chain needs to upskill if it wants to deliver the buildings promised by architects and engineers.
At this year’s Ecobuild conference, Hobbs gave some stark examples of what happens when technical skills are lost. In one case, a newly purchased LGIM property was using eight times more gas than best practice; Hobbs discovered that, during a previous refurbishment, the building management system (BMS) had been programmed to night-purge all year round. ‘The poor building was being frozen each winter down to 5°C every night and then being heated up to 25°C,’ explains Hobbs, who believes a building team with technical skills would have identified the issue.
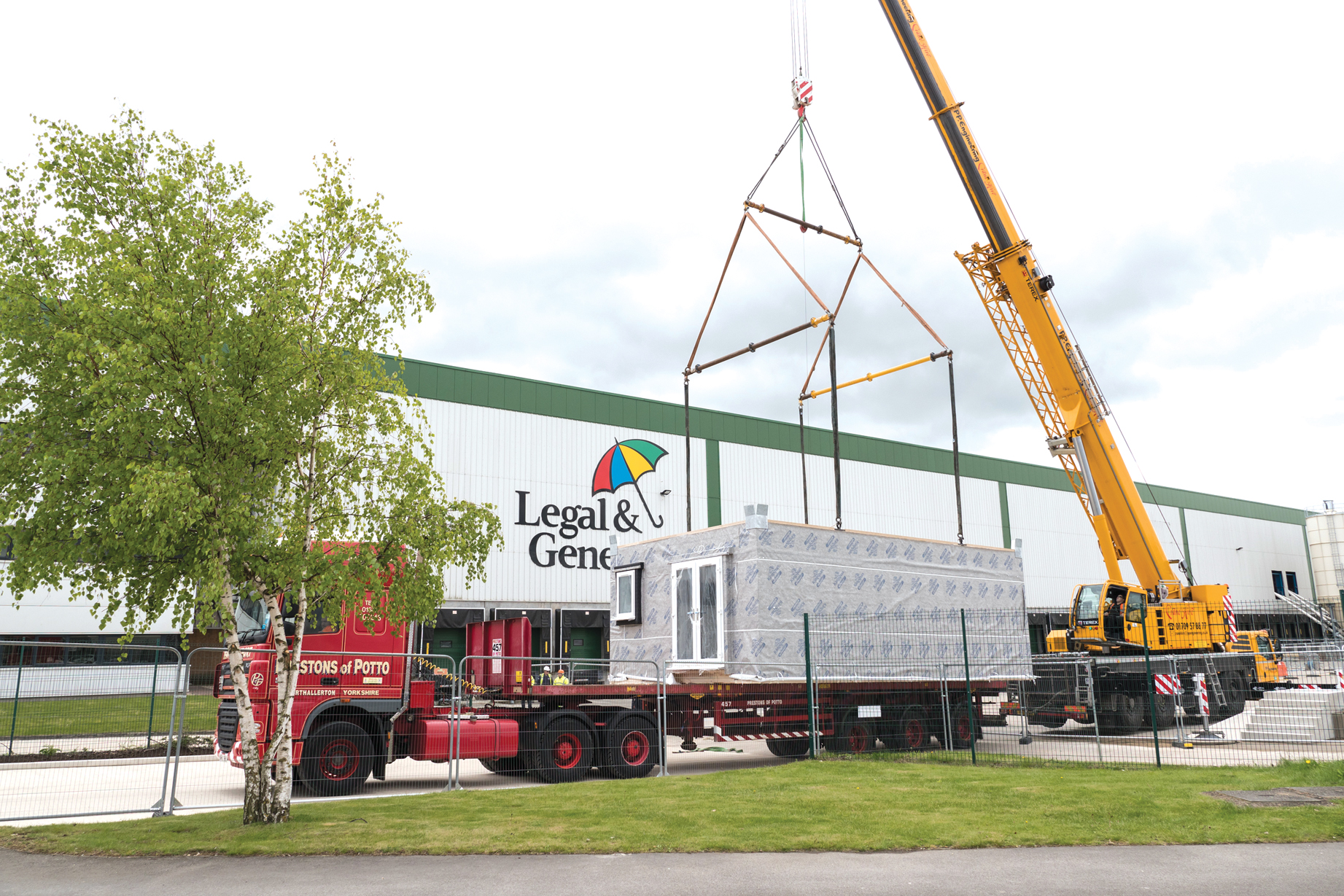
Before she joined Legal & General in 2012, Hobbs had a wide-ranging career in building services, and years spent in ‘every nook and crevice of the industry’ has given her the skill set to tackle performance issues. She first became interested in low-energy technologies in the final year of her physics degree and – because she didn’t ‘want to teach or go into the nuclear industry’ – she chose building services engineering. Her first job was as a renewable energy engineer at Wimpey Homes Technology Laboratory, after which Hobbs took on an energy-management role at West Sussex County Council, just as BMSs were coming to the fore. Two years later, she moved to controls specialist Trend, which gave her a ‘brilliant grounding’ in the technology.
‘These days, everyone’s frightened of BMSs – they don’t want to touch them because they don’t understand them,’ says Hobbs, who believes this lack of awareness is contributing to poorly performing buildings today.
She joined property company MEPC in 1992, as an environmental engineer, but when the firm was bought by Hermes – which started to outsource property management – she began her own sustainability company. This was later bought by Oscar Faber (now Aecom), because it wanted its own sustainability team. Hobbs then joined Environ, which carried out environmental audits for the likes of Disney, in the United States.
As a carbon assessor, Hobbs recalls writing lots of reports for companies about embedding sustainability into their working practice – but she wondered how much of it was ever acted upon. ‘We would use a spreadsheet to add up energy use but – often – nothing was done, either in terms of reducing energy use or even measuring it against benchmarks,’ she says.
Hobbs decided to look for a role where she could influence change, and joined LGIM Real Assets. She says it was looking to transform its culture to take advantage of the increasing demand for environmental funds by investors. (See panel ‘Impact investment’.)
Hobbs was impressed by the commitment to sustainability of Bill Hughes, head of LGIM Real Assets and a trustee of the UK Green Building Council. Hughes insisted everyone in the company complete a 60-hour sustainability diploma course, because – if LGIM was going to offer low-carbon investments – it had to upskill its staff to understand what was being offered.
‘Sustainability is embedded in what we do. We have to do it ourselves and not outsource it to a specialist,’ says Hobbs. ‘We have to live and breathe it – which is a great philosophy.’
Taking back control
There is a growing trend for impact investment, which includes funds that offer environmental and social value, as well as an economic return. L&G has created a future-world fund with HSBC, which tracks the FTSE 100, but also takes into account the carbon intensity of companies, and looks at the amount they are investing in renewables and fossil fuels. ‘It has attracted a lot of interest from investors who want to signal to the market their environmental credentials,’ says Hobbs.
For these funds to work, there must be a robust methodology to measure environmental impact. ‘You can’t put a green-mulch PR spin on this,’ adds Hobbs. ‘It’s difficult.’ The global real estate sustainability benchmark (GRESB) is one measure available to investors. Companies supply data on the environmental, social and governance performance of their assets and portfolios, and this is benchmarked against other firms.
One driver for sustainable investment is the Principles of Responsible Investment (PRI), to which L&G is a signatory. This not-for-profit group encourages investors to use responsible investment to enhance returns and better manage risks. L&G’s modular housing factory in Leeds also fits with the PRI, says Hobbs. ‘The use of cross-laminated timber ensures the home will have impeccable sustainability credentials,’ says Hobbs. The products and materials selected are also aimed at giving the end-user a home with lower running and maintenance costs.
LGIM Real Asset is attracting capital from sustainable funds such as Dutch pension fund PGGM. It has also set up a build-to-rent fund to develop low-energy buildings that offer social benefits for the occupants, such as shared gyms and dining facilities.
When Hobbs started at LGIM Real Assets, she audited every property, and gave managing agents a top 10 list of things to do to improve performance. Subsequently, she noticed anomalies in the BMS – such as the wrong temperature settings and the occupancy times not being corrected.
‘I’d ask them to do something, however, often they didn’t have the technical skills to make the necessary changes,’ says Hobbs. ‘That’s when it dawned on me that we – as clients – had badly de-skilled the industry by demanding lower and lower costs.’
The managing agent is responsible for building operation and liaising with the tenant. Work is outsourced to a maintenance contractor, who subcontracts controls to the BMS specialist. They know how to change the temperature controls, says Hobbs, but the property manager probably hasn’t understood what they have to ask for and the instruction is lost.
Buildings also have in-house facilities managers (FMs), but they are involved in so many areas – such as security, maintenance, catering and IT – that the building controls don’t get the attention they need. The FM alone cannot serve the building, says Hobbs, and there needs to be a new technical services position, looking after such things as sub-meters, plant, controls and fire alarms; these could be in-house roles or outsourced. ‘I’m not saying FMs can’t do their jobs, but there’s a knowledge gap because we’ve squeezed out the engineering,’ she says.
A technical services engineer would save on maintenance costs, she adds, because they would be pro-actively resolving services issues. This reduces the chance of costly plant failure and replacement, and increases plant efficiency. ‘Your reactive, energy and whole-life costs become a lot lower,’ says Hobbs. ‘If you have buildings you know that you are going to keep for more than five years, you don’t want to carry out minimum maintenance, otherwise you’ll have to replace the plant and equipment in that period.’
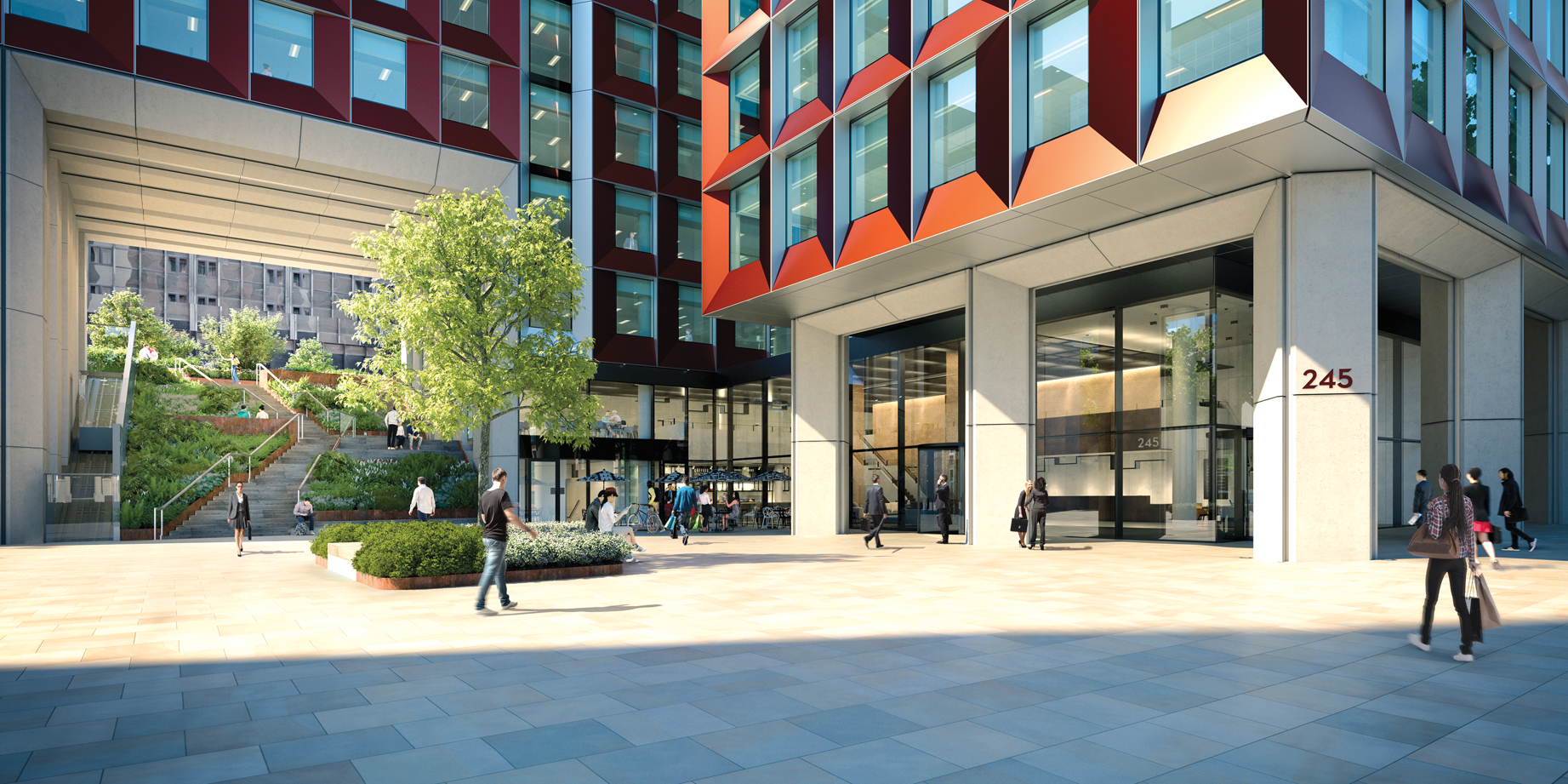
Hobbs says that the cost of upskilling would be paid for by a higher service charge: ‘If the investment will pay back in a year, it will be beneficial for tenants.’ If engineering results in lower bills, then it will also benefit the landlord, she adds, because this will help them attract future tenants.
Part of the problem has been the way in which money has been used. ‘We spend it all on the design of a building and very little on operation – yet this will span 30 years,’ says Hobbs, who believes it doesn’t have to be complicated. She cites a LGIM property that was improved significantly over five years simply by improving the controls when it had to install replacement chillers and boilers. The energy use went from 180kWh·m-2 to 40kWh·m-2, which is below the best-practice benchmark.
‘We have halved the energy use by paying attention to controls every time we do a tenant refurbishment,’ says Hobbs, who believes it’s the little things – such as the correct position of sensors – that make all the difference.
Deemed unsightly by architects, sensors are often hidden in the ceiling, where the temperature is higher, which means the controls aren’t able to provide comfort to the space occupied by people. ‘I’ve gone backwards from sustainability to basic maintenance,’ says Hobbs, who claims the health and wellbeing agenda will mean those operating buildings will have to pay much more attention to occupant comfort and the environmental control of spaces – and they will no longer be able to get away with haphazard placement of sensors.
“I’m not saying facilities managers can’t do their jobs, but there’s a knowledge gap because we’ve squeezed out the engineering”
”
Hobbs says property companies have a new weapon in their fight against poor performance – data analysis. Firms such as Demand Logic and Carbon Credentials are monitoring energy use closely, to look for anomalies that might signify problems with controls and plant that are resulting in poor performance.
‘You need this new breed of big-data experts to sit alongside the maintenance teams and identify issues. Data can then be checked afterwards to ensure the maintenance contractor has completed the necessary changes,’ says Hobbs, who wants the industry to be honest about the mistakes it has made. ‘Nobody wants to rock the boat. If we’re open about what we’re doing wrong, we’ll find a way of putting it right.’
There are encouraging signs that the supply chain is responding to the demand for more sustainable buildings by bringing back engineering skills. Clients are starting to use mechanical and electrical (M&E) consultants, says Hobbs, while some agents are bringing engineers back in house to offer the necessary technical services. ‘The industry is beginning to understand that it’s gone too far in reducing costs and management fees, and that it’s simply not giving us an optimum service.’
Don't miss Build2Perform Live
Debbie Hobbs will talk about the benefits of metering and analysing data at the CIBSE Build2Perform Live event on 21 and 22 November at London’s Olympia. Her session is one of 20 half-day streams being organised by CIBSE Divisions and Special Interest Groups, which will focus on wellbeing, digital engineering and energy.
Programme highlights include best-practice case studies from Cundall and Arup on how to design lighting for user wellbeing. There will also be a look at proven strategies for maintaining air quality in buildings, and an overview of forthcoming updates to CIBSE guidance in TM40 on health and wellbeing and CIBSE Guide L: Sustainability.
In addition, there will be sessions on how digital practices have improved building services construction, commissioning and facilities management, as well as on building simulation, procurement, metering, and the important role that facilities managers play post-occupancy.
Playing a key role in Build2Perform Live is CIBSE’s Young Engineers Network. Its stream, ‘How to engage better with clients’, challenges participants to work together to generate ideas for moving building performance higher up developers’ priority lists.
Build2Perform Live is free to attend – to register, visit www.cibse.org/b2plive