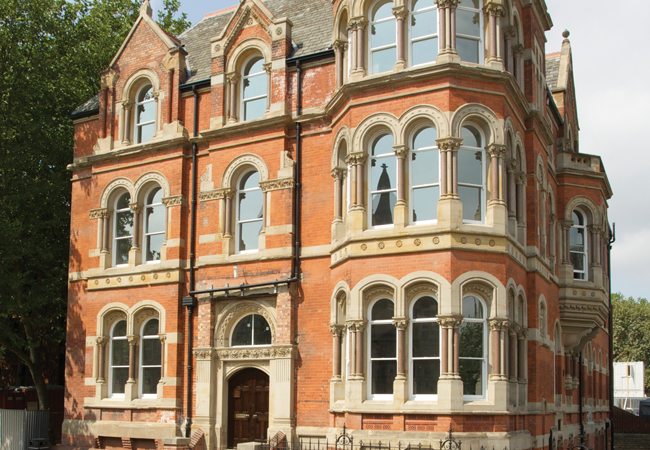
Grade II listed 50 Shakespeare Street, built in 1882
When Nottingham Trent University (NTU) acquired a listed building in the heart of Nottingham in 2012 as the future new home for its central administration team, the University’s in-house engineering department knew it had a difficult task ahead.
Built in 1887, 50 Shakespeare Street is a Grade II listed former council register office. Over its lifetime the building had suffered years of neglect, bomb damage and unsympathetic refurbishments – and, with an Energy Performance Certificate (EPC) rating ‘F’, it was obvious the building was also leaking energy.
Four years on and the building’s transformation has been nothing short of miraculous. Now fully refurbished and restored by the university, this Romanesque gem is an exemplar of energy efficiency; its EPC rating has improved significantly from an F to a B – a similar rating to an equivalent newly built scheme. Also, after a year’s occupation, the scheme delivered a B Display Energy Certificate (DEC) for operational energy, well below the energy use expected for a building of its type.
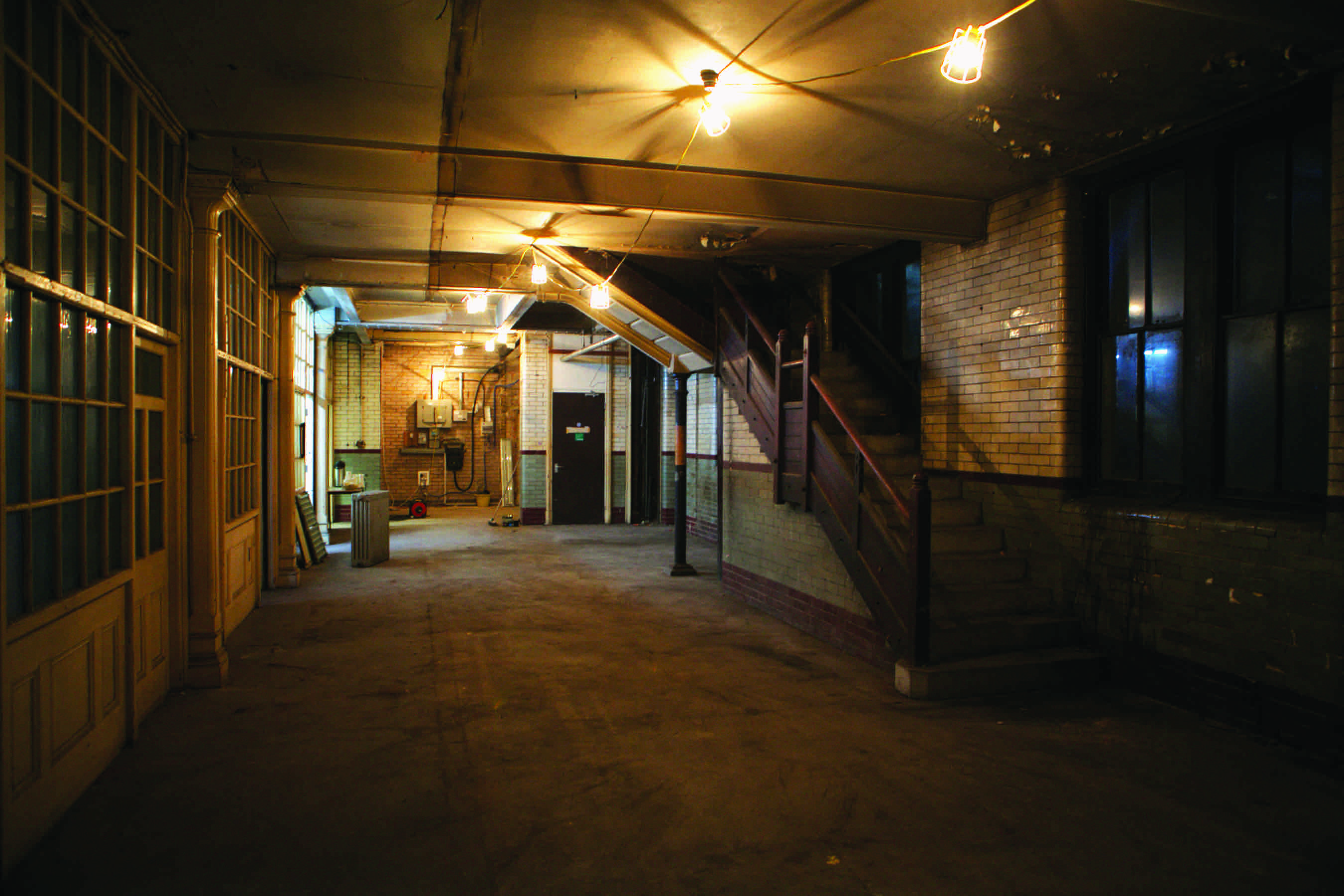
The low energy lighting scheme is based on LEDs and high frequency T5 fittings
The success of this challenging refurbishment was recognised by CIBSE in this year’s Building Performance Awards when the project won the Commercial/Industrial category. The Judges said the project had ‘a very good focus on energy efficient design’.
The low energy refurbishment came about because sustainability is a high priority for the operation of the NTU estate. The university has a goal to reduce overall carbon emissions by 48% from a 2006 baseline by 2020. So when, in 2012, the engineering department embarked on refurbishing 50 Shakespeare Street, it wanted to develop the most energy efficient solution that it could for the listed building.
‘We were looking to maximise the carbon savings where we could with this building,’ says Simon Smith, chief engineer at Nottingham Trent University.
To understand the scale of the task that lay ahead with the refurbishment, the team set out to estimate the existing building’s annual energy and carbon emissions. The building’s age and construction meant that it was not possible simply to use standard benchmark energy and carbon figures. As such, steady-state heat losses were calculated and normalised using degree day analysis. The calculated annual heating load was then substituted into the relevant benchmarks for the building within CIBSE Guide TM46 for type 18 University Buildings and the ECG 016 Guide: Energy Use in Offices. The results show that if the building were to remain unchanged, then energy usage was estimated at
354kWh·m-2·year-1 and CO2 emissions at 87.1kgCO2m-2·year-1.
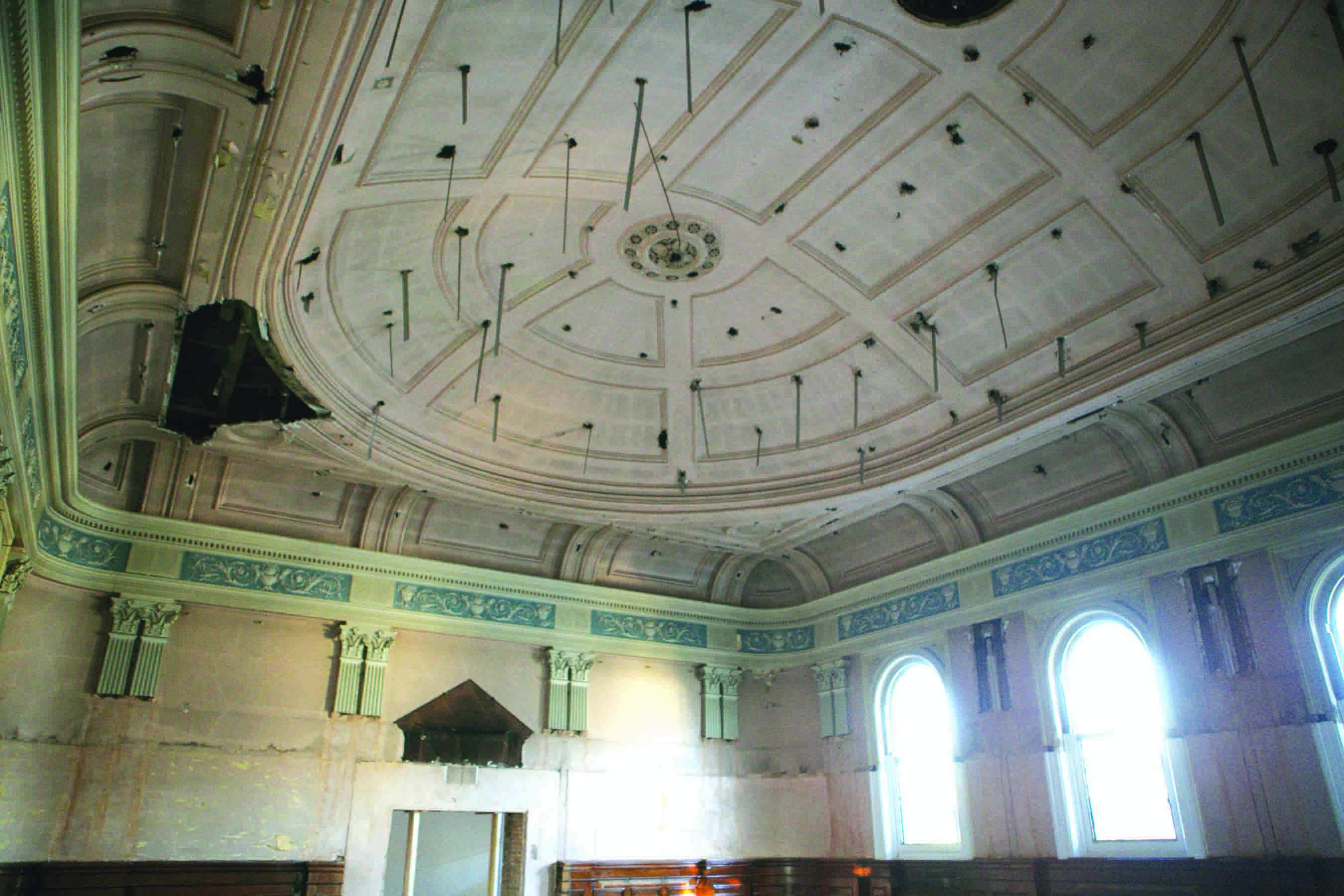
Tall windows provide significant daylight
The engineering department also carried out a full survey of the building and its existing services. This enabled the team to identify potential improvements in the building fabric, and to understand the constraints of the building on any future servicing solution.
The first step in reducing carbon emissions was to install high performance roof insulation and to refurbish 63 of the building’s 68 single-glazed sash windows, which included fitting ultra-thin, high performance double glazed units. The remaining five windows were beyond repair and had to have bespoke replacements fitted. Improvements to the fabric resulted in a 22% reduction in energy use and an 18% reduction in carbon emissions.
Lightening the load
When it was built, the openable sash windows provided daylight and natural ventilation to the 19th century building. The engineering team have stuck with this solution for the building’s 21st century makeover, which also eliminated the need for ventilation plant and its associated ductwork installation.
Critically, the building’s tall windows and high ceilings also admit a significant amount of daylight. The use of glass partitions, rather than solid walls, ensures maximum daylight penetration on the office floors. A low energy lighting scheme based on LEDs and high frequency T5 fittings supplements the natural light. Previous experience with intelligent lighting systems meant that, on this project, lighting control is through local switching combined with absence detection. This allows the users full control of the lighting, while ensuring the lights do not remain on when the room is unoccupied. The only exception to this strategy is in the court room, a large function room on the top floor, where the LED lighting is controlled from a local lighting control system to allow an appropriate lighting scheme to be set for the various events taking place in the room.
To reduce the need for artificial lighting, the engineers also reinstated a large roof light at the top of the main circulation staircase, which had been removed and covered with bitumen felt at an earlier stage in the building’s life. At the same time, openable vents were added to the roof light to allow the light well to act as a ventilation chimney, to aid air movement in the building.
‘Because it was a listed building there was a limit on what fabric improvements we could undertake,’ says Smith.
In addition to the fabric improvements, the scheme also set out to reduce energy used in ventilation and lighting (see ‘Lightening the load’).
Improvements to the building’s fabric and lighting are calculated to reduce annual energy use by 28% and the associated carbon emissions by 30%.
Although these savings are significant, the team then set out to see what additional carbon savings could be achieved through the use of low and zero carbon technologies in the building. A number of options were considered, including gas-fired heating, connection to Nottingham’s district heating system, air source heat pumps, a biomass boiler and various combinations of these different technologies.
A calculation of associated energy use, carbon emissions and costs showed that a new biomass boiler, supported by a connection to Nottingham District Heat Network, was the most suitable option to maximise both energy and carbon savings. The biomass boiler, which includes a thermal store to ensure it runs efficiently, supplies approximately 75% of the heat. The remaining heat energy is provided by a 220kW connection to the Nottingham District Heating Scheme.
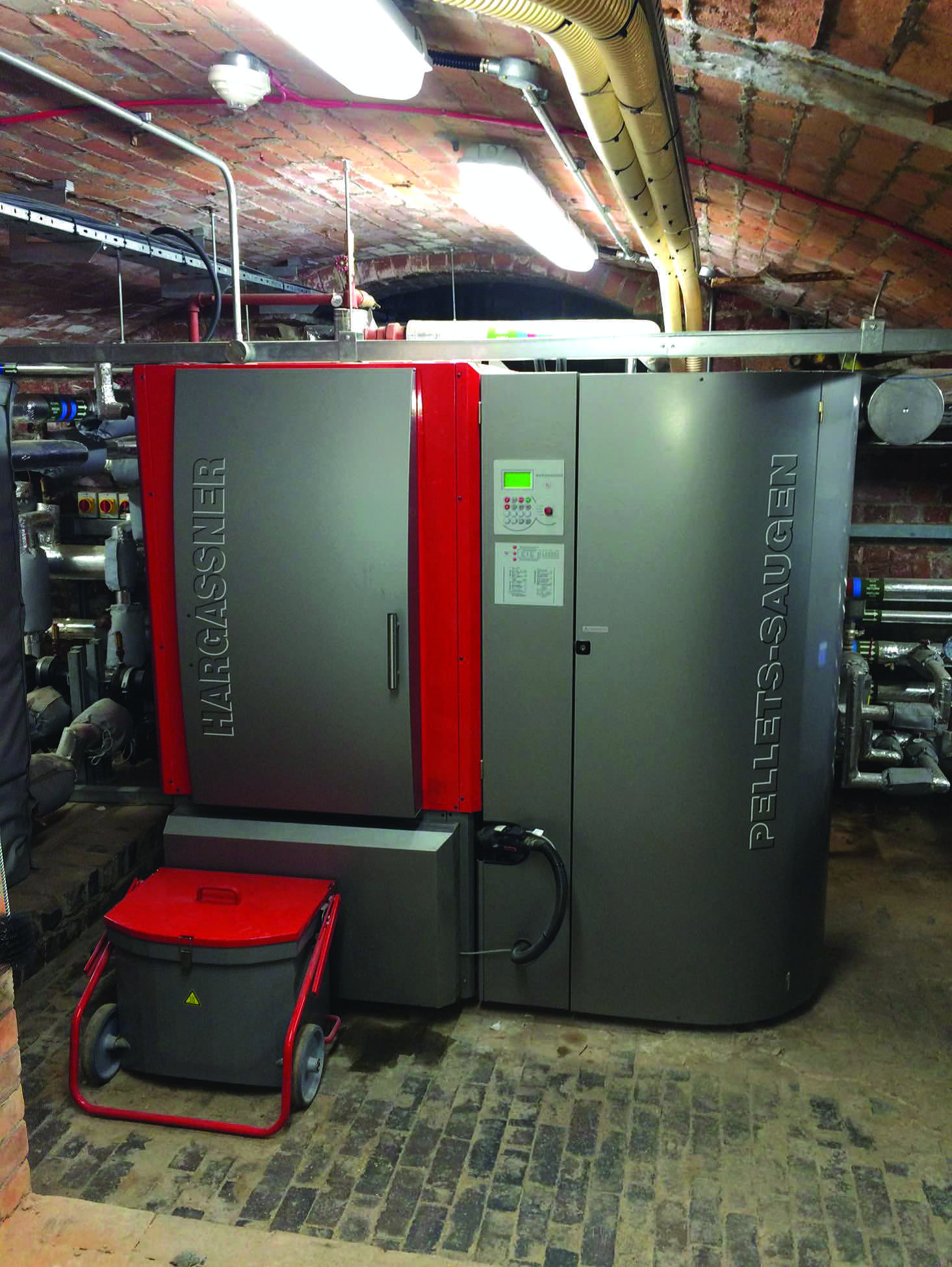
The Hargassner biomass pellet boiler sits in the building’s sub-basement, which acts as the main plantroom

Baseline energy usage and CO2 emissions from the biomass boiler and back up district heating would be 259.46kWh·m-2·year-1 and 14.38kgCO₂m-2·year-1 respectively. When this option is coupled with improvements to the building fabric and lighting, annual energy use is calculated to reduce by 27% and carbon emissions by more than 83%, when compared to the existing building.
Radiators are used to heat the building. The LPHW system is zoned floor-by-floor and is controlled through the university’s centralised Trend building management system with local control provided by thermostatic radiator valves. NTU carried out a series of thermal and CFD modelling exercises to ensure the design would perform as intended, including an assessment of the effectiveness of the natural ventilation and the potential for the building to overheat, in addition to checks on how the proposed radiator locations would distribute heat.
This modelling highlighted the potential overheating risk of installing full-height partitions in the basement offices, which would have prevented effective cross ventilation, for example.
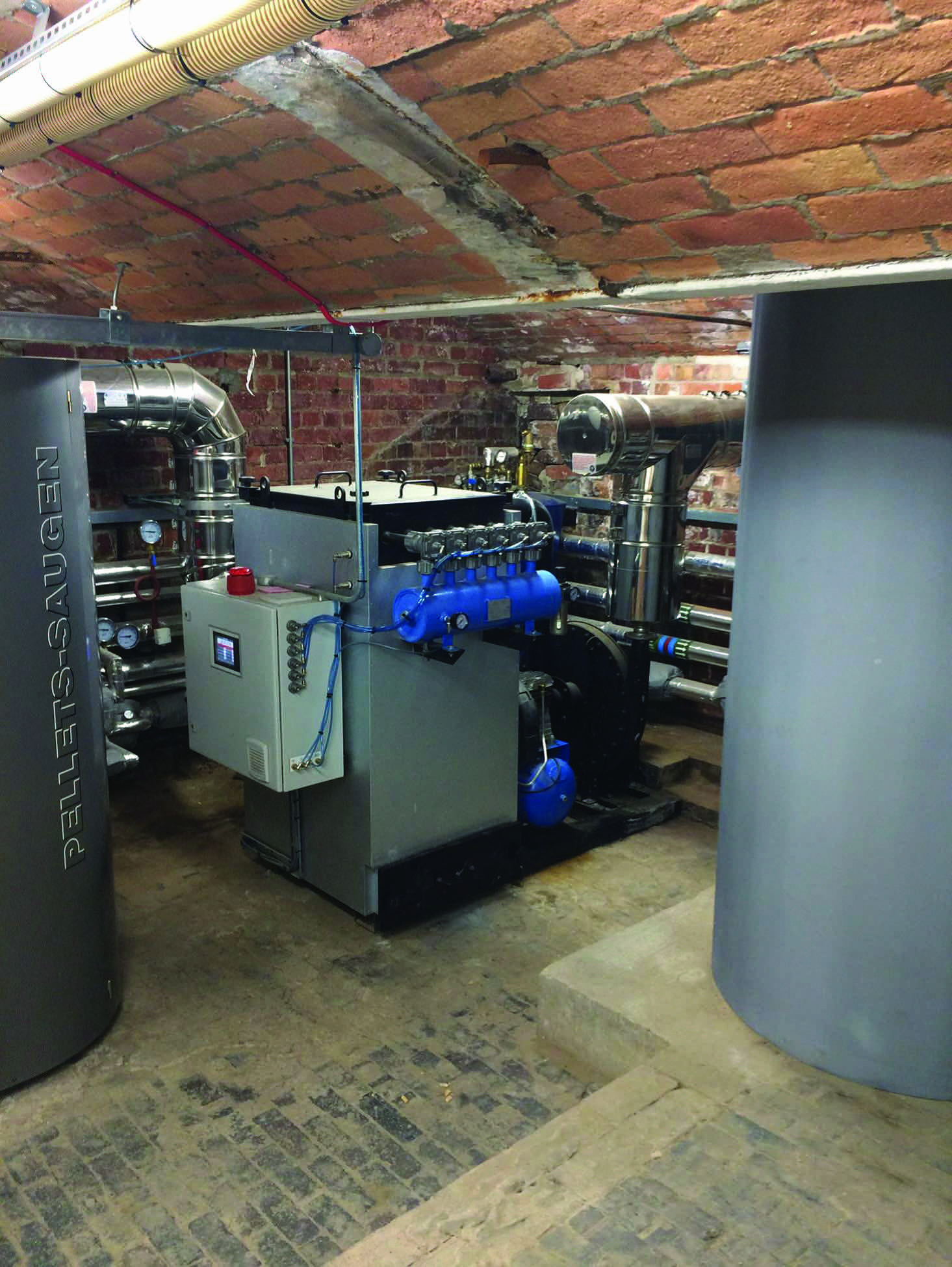
One of the most challenging aspects of the project was installation of the new 150kW Hargassner biomass pellet boiler, its fuel store and associated buffer vessel in the confines of the building’s sub-basement, which was to become the main plant room for the building. The room was far from ideal; it had limited space, a low soffit and access was via an existing staircase, down which everything had to be manhandled.
Along with the boiler, the room also accommodates the 200kW plate heat exchanger for connection to the district heating, electrical control panels and a touch-screen building management system – which features programmable time clocks to all mechanical plant to ensure systems only operate when needed, saving both energy and money.
All utilities are metered with radio equipment fixed to each meter to allow consumption to be closely monitored through the BMS remotely.
In addition to the wet heating system, the servicing solution includes two reverse cycle heat pumps serving the court room and boardroom. These rooms are used for formal functions and events, which means that on occasions occupancy levels will be high and that they have the potential to overheat, even with the windows open. To ensure conditions remain comfortable, the heat pumps supply both cooling and heating.
Total cost of the mechanical and electrical works was £900,000 but, in addition to the energy cost savings of £10,000 a year, the university also gains £15,000–£20,000 a year income from the government’s Renewable Heat Incentive.
Despite the building being listed and on a city-centre site, the NTU team has managed to deliver a building that exceeded the challenging targets the team set. In the first year, its DEC energy use figure of 178kWh·m-2·year-1 was 30% lower than the figure the university’s engineering department calculated at the design stage. No wonder the CIBSE judges were impressed.