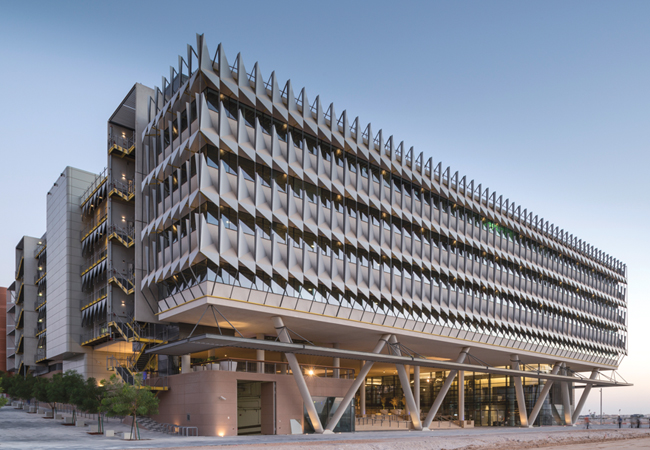
The Siemens’ HQ plot is unusual in that it overlooks an open square. Credit: Paul McMullin
The brief from Siemens was that it wanted a building with a great LEED rating,’ says Robert Murphy, associate director at engineer Aecom. He’s talking about the engineering and technology company’s new Middle Eastern headquarters in Masdar City, a giant demonstration project slowly being developed in Abu Dhabi to show how clean technologies can work in practice. Siemens wanted to use its new building to help promote the organisation’s low-energy values and philosophy to the region.
Aecom and its partner Sheppard Robson won the competition to design the low-energy HQ. The organisations had been working together to use parametric modelling to integrate low-energy features effectively into building design. So – after winning the competition – the obvious starting point was to focus on what might be possible with this building, using parametric modelling.
The site for the new office building was defined by the Masdar masterplan. This was based on emulating an old Arab city, with buildings clustered closely together to provide shade from the relentless Middle Eastern sun. The Siemens building plot was unusual in the scheme, in that it overlooked an open square – a feature the design team were keen to exploit.
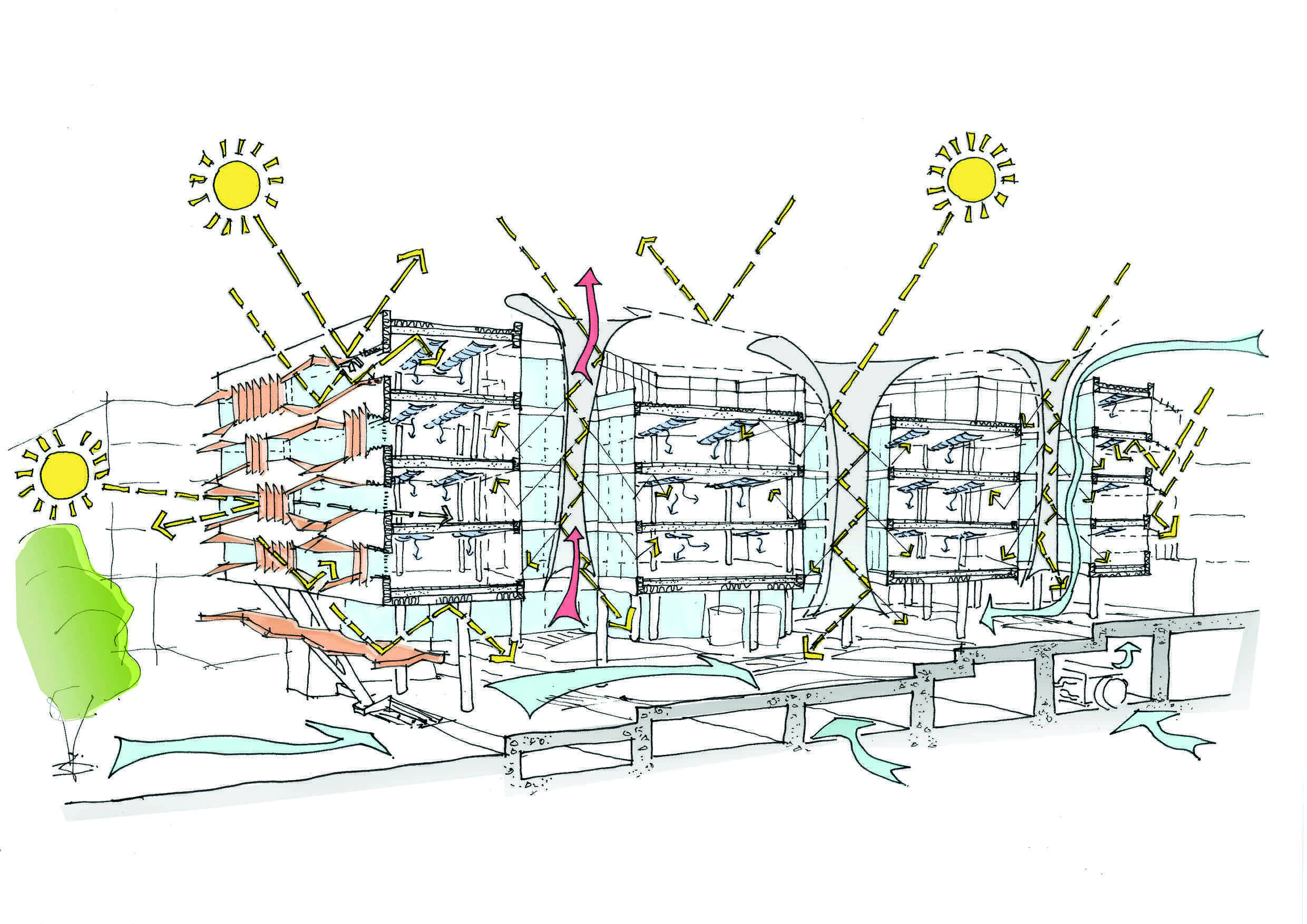
Diagram showing air flow through building and hot air being exhausted through roof openings
Their solution was to raise the four-storey building above a new public plaza, which was conceived as an extension to the existing public realm. Each of the building’s 4,500m2 floorplates is pierced by nine square atria; these act as ventilation chimneys to draw air across the plaza to keep it cool, while allowing daylight to enter – and the occupants to see out from – the giant floorplates.
Minimising heat gains from exposed façade was critical in ensuring the building achieved its low-energy aspirations. ‘Resolving the shading to the office façade overlooking the square was the first crucial element in developing a low energy solution,’ says Sasha Krstanovic, director at Aecom. The challenge for the designers was to establish what form this shading should take. ‘We didn’t know what shape to make the shading,’ Murphy explains, ‘so we developed a parametric model based on defining: the amount of area occupants could look out of; the amount of indirect daylight that could penetrate the floors; and the amount of sun blocked out as it moves across the sky. Then we pressed go.’
Krstanovic describes the resulting solution – a series of distinctive, folded, angular aluminium fins – as ‘looking like origami’. The form of the shading varies in response to the orientation of the façade on which it is mounted.
The outcome of modelling scores of potential design solutions is a technological response to the challenging brief, which ultimately informed the building’s aesthetic. ‘We extracted all the design ideas found by the computer, put them into words and gave them to the architect, who developed them into a design that met the functional requirement for shading, but was beautiful at the same time,’ says Murphy.
In addition to providing an architectural statement, the external aluminium shading is also very practical. ‘The clever thing about the solution developed by the modelling is that it does not have to move to track the sun, which means it does not have a mechanism that will get clogged with sand – which is important for a building in the desert,’ explains Krstanovic.
To further minimise solar gains, the aluminium fins have been given a reflective coating, while the building’s façades behind the shading are also highly insulated and airtight, to further minimise heat gains inside the offices.
In addition to parametric modelling, Aecom used thermal modelling to develop the design. ‘By looking closely at where energy is needed in the building, we were able to maximise the benefits of fairly conventional technologies,’ says Krstanovic. The resulting building services solution is as simple and robust as that of the fixed-shading solution. The design includes using demand-led, variable speed fan coil units (FCUs) to cool the offices and desiccant thermal wheels in the air handling units ‘to squeeze the moisture out of the fresh air supply’, says Murphy.
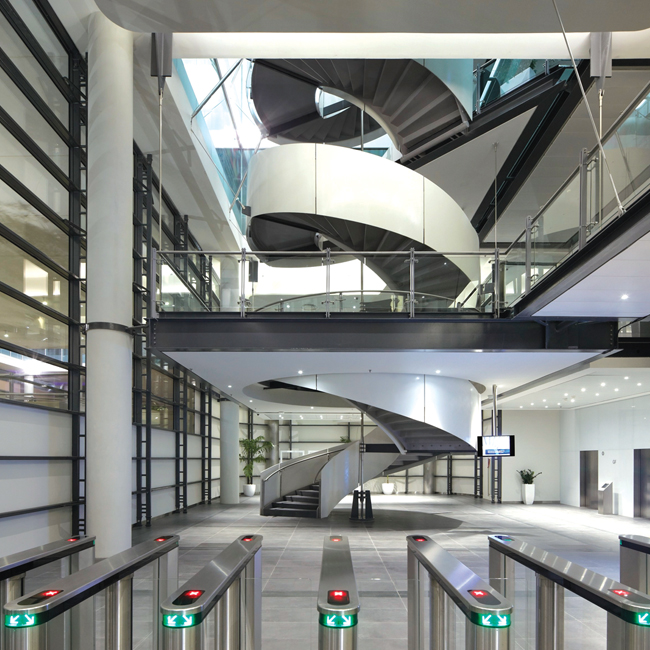
Siemens expects power and water savings of 50% when the HQ is fully occupied
Again, the engineering has been kept deliberately simple by using the building’s exhaust air to recharge the desiccant. ‘If we hadn’t modelled the building in quite so much detail, we wouldn’t have realised how important the desiccant wheel was in maintaining comfort,’ he explains.
Needless to say, the building uses Siemens controls for the building services and to optimise energy use – and, again, simplicity is the rule. The building management system senses which rooms are occupied and adjusts lighting and temperature levels accordingly; taps in the toilets are fitted with sensors to minimise water usage; the FCUs turn on and off when needed; and fresh air is only delivered where needed.
Perhaps the most surprising aspect of the building’s low-energy design is that the only renewable technology included in the scheme is a roof-mounted solar thermal system, which generates hot water for the occupants. The design team would have liked to have incorporated more renewables, but were prevented from doing so by a lack of funds. ‘While the building works incredibly well, it would work even better with the addition of renewables,’ explains Krstanovic. ‘For example, if we’d had a big enough budget, we would have put PVs on the roof to drive down the building’s energy consumption still further.’
Even without the additional renewables, the scheme achieved LEED Platinum in accordance with the client’s brief, making it one of the most sustainable office buildings in the Middle East, at a cost per square metre similar to that of more conventional head office buildings in the United Arab Emirates.
Equally impressive, the robust solution appears to be performing in line with expectations. In its first year of operation – between February 2014 and January 2015, although the building was only partly occupied – it used 63% less electricity and 52% less water than a typical Abu Dhabi office building. Even when it is fully occupied, Siemens expects power and water savings to be closer to the designers’ estimate of 50%.
‘Because we all worked together from the outset, we were able to develop an optimised design that responded to the brief,’ says Krstanovic.
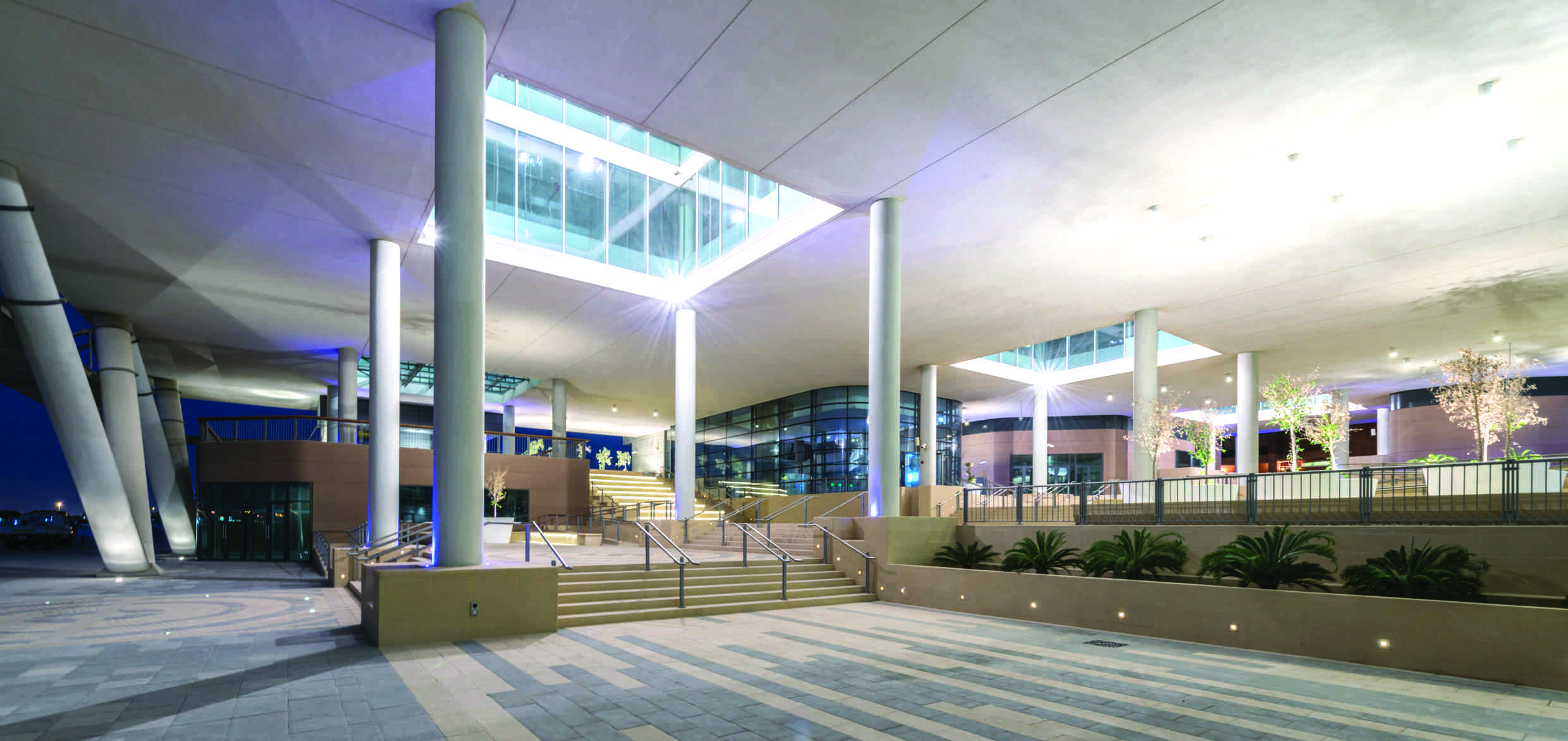
The square atria allow light to flood in. Credit: Paul McMullin