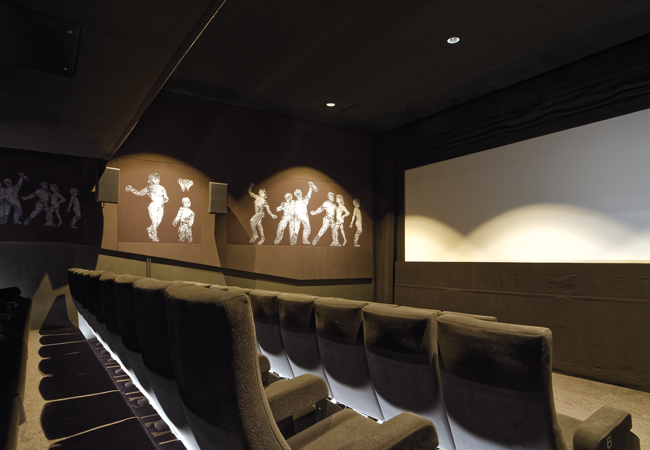
Lighting the exterior of a building in an area classed as intrinsically dark could be the definition of ‘a challenge’ – but it was just one of the issues the design team faced when creating a new community hub in East Sussex.
Depot, in Lewes, is a three-screen, independent cinema – with capacity for 306 people – that includes a restaurant, as well as seating in the foyer and externally.
The building was originally a General Post Office (GPO) depot, and then a store for a brewery before this was closed down. With local people having to travel nine miles to Brighton to see the latest movies, however, the client – Lewes Community Screen – saw an opportunity to create a neighbourhood facility with sustainability at its heart. Photovoltaic (PV) panels, a green roof and a simultaneous heating and cooling heat pump were incorporated into the design.
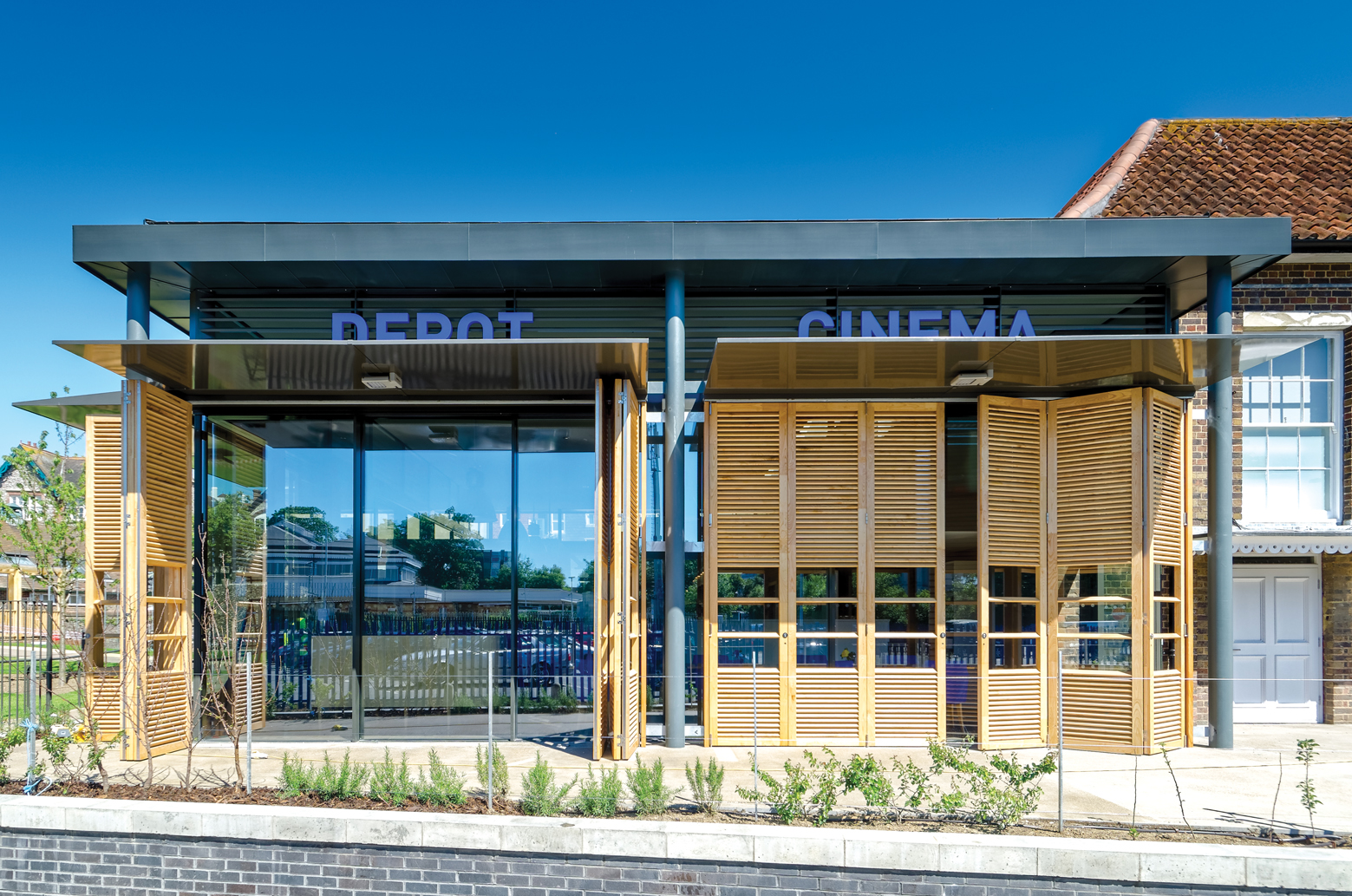
Horizontal brise soleil ensure the correct amount of shading
The town, though, is situated within the South Downs National Park – an E1 environmental zone. This means it is an area with intrinsically dark landscapes, so the amount of artificial light that can pollute the surrounding sky, or impact on neighbours and wildlife, is strictly regulated.
Early and close collaboration between all members of the project team was to prove vital and invaluable, as new life was breathed into a much-loved old building to deliver a positive, welcoming facility for the people of Lewes.
Passive measures
As an existing building, the orientation of the Depot’s foyers – predominantly south- and west-facing – was fixed. To reduce unwanted solar gain behind the new curtain walling during summer, modelling was done at an early stage to optimise the overhangs. This also ensured solar gain into the space in winter was achievable.
Close collaboration with the architects was important to ensure the correct selection of glazing units. The project’s mechanical and electrical (M&E) consultants, SGA Consulting, wanted a good solar performance and the architects desired clear glass, for an unobstructed view of the new soft landscaping that was to replace the tarmacked car park.
Working together ensured that the curtain-wall glazing was the first defence against overheating in the summer, while also being aesthetically pleasing to the planners and architects. A compromise was found by installing a product that gave a good reduction in solar gain while maintaining an almost clear tint for the aesthetics. (see below ‘Data from the specified curtain walling’).
Data from the specified curtain walling
Light transmission = 61%
Direct solar heat transmission = 31%
G-value (solar factor) = 40%
Total shading coefficient = 0.46
Short wave shading coefficient = 0.36
Long wave shading coefficient = 0.1
Centre pane U-value = 0.4 W·m-2K-1
Simple SketchUp models of the building were created initially, to show all design team members where and when solar gains would peak within the foyers, and to ensure they focused on these areas. These models suggested optimal overhangs of 5.2 metres for shading on the west façade in the afternoon in summer, but – from an aesthetic and planning point of view – this was not possible. As a compromise, horizontal brise soleil was introduced to supply the correct amount of shading, while maintaining the look of the building.
Simple models were used to refine the brise soleil’s attributes and to demonstrate performance to the architects for the optimal layout of fins within the frame.
Once the simple model had provided all the information it could, it was imported into IES to verify the initial hand calculations.
All external luminaires at Depot have an upward light ratio of 0
The thermal mass of the existing façade was enclosed behind the curtain walling within the new foyers. This was an opportunity to add thermal mass to the space to deliver passive cooling during the day, with a night-cooling scheme – controlled via the building management system (BMS) – made possible through the addition of roof lights. Sensors ensure these close when it rains, to prevent water from entering the building.
Underfloor heating was also installed in the foyers, as the heating temperature flow and return worked well with the heat pump. The timber and polished concrete finish in the foyers also contributed to the thermal mass.
Solenoid valves – linked to the local lighting PIR sensors – were placed in the toilets to limit water use if these rooms are not in use. After 15 minutes, the valves close to ensure that water is not wasted if there is a leak. The sanitaryware chosen by the architect was coordinated with SGA Consulting, so low water-use fittings were specified to reduce hot and cold water storage within the plantrooms.
Constraints of a refurbished building
Two plantrooms were needed because of the layout of the existing building. The main ground-floor plantroom houses the ground source heat pump (GSHP), backup boilers and pumps, while a loft plantroom was created to house the new air handling unit (AHU) serving the cinemas.
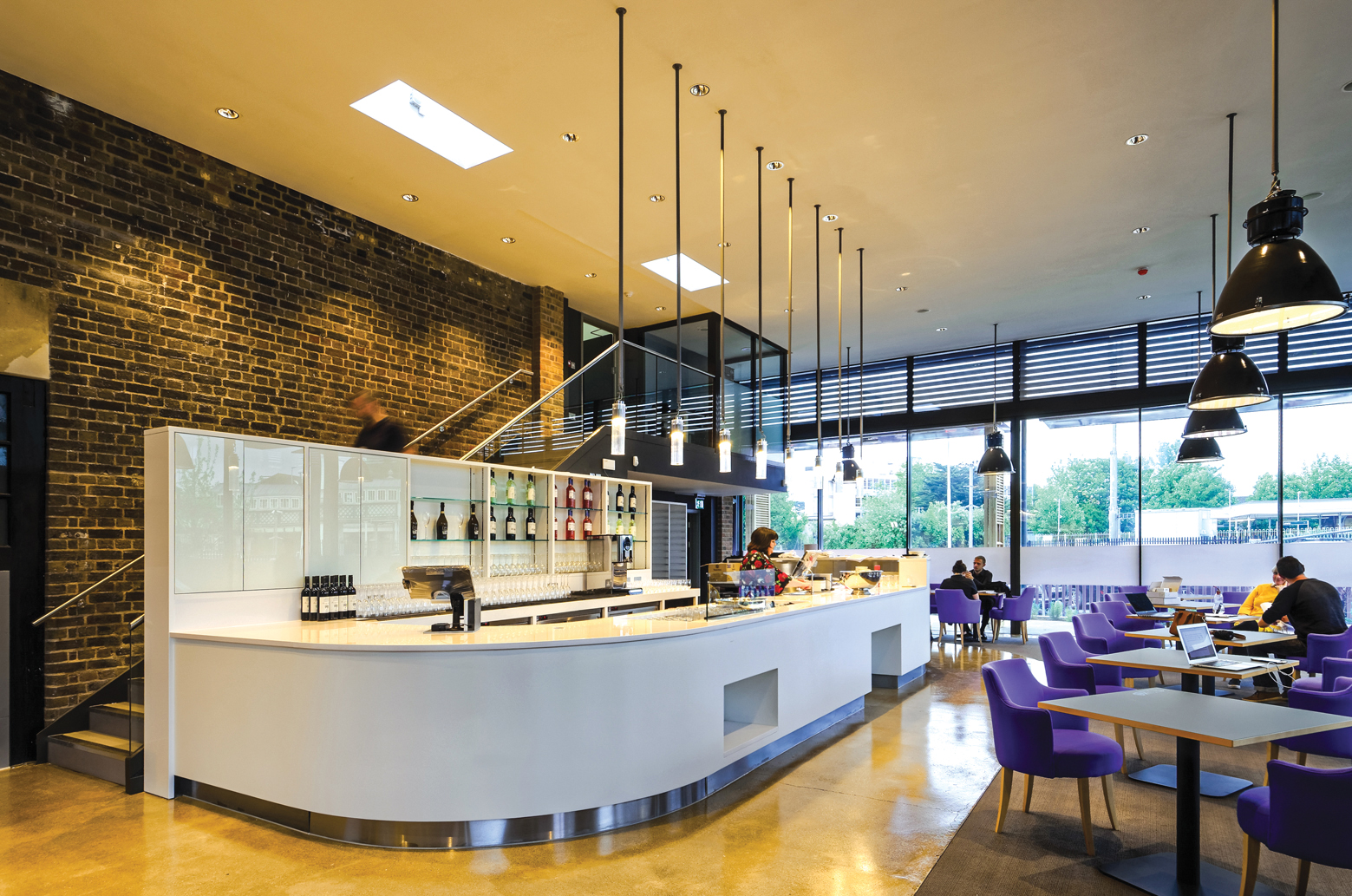
The former GPO and brewery depot is now a community facility
SGA Consulting had to work closely with the architects to ensure the loft was sized correctly to house the AHU and new ductwork. Collaboration with the structural engineers was also required to remove some of the existing timbers within the roof to open up duct and pipework runs.
Ideally, three AHUs would have been specified to serve each of the screens and ensure independent, close control of the internal environments. But the constraints of the loft space meant only one could be selected – so three branches were required on the supply and extract ductwork.
Again, liaison with the structural engineers was needed, as the ductwork runs parallel with the main steel zone supporting the roof above and the new cinema construction below. It then drops through the acoustic ceilings to serve each cinema within a purpose-made bulkhead.
Ductwork runs parallel with the main steel zone supporting the roof
To minimise energy consumption – and to allow independent control within each of the screens – a variable air volume (VAV) approach was adopted. The BMS monitors two parameters in the extract duct legs from each cinema: carbon dioxide (CO2) and temperature. If either of these are outside of the design conditions, the BMS adjusts the air volume into the space. This allows the optimum amount of air to be delivered.
The cinemas are ‘box in box’ constructions, which mean they have independent frames to ensure vibration from the main building does not pass into the screening areas. It is the same with the services; all services had to be hung from spring hangers, and flexible joints in ductwork were installed before they passed into the cinemas.
The Depot is in an area prone to flooding, so planning stipulated that the ground floor had to be raised. This offered designers an opportunity to use this zone for pipework, to allow distribution from one side of the building to the other. Pre-insulated HDPE pipework was specified, to ensure the run below the slab would be jointless, with joints made in accessible zones above the slab or within the main plantroom.
To reduce unwanted solar gain during the summer months behind the new curtain walling, modelling of the building to optimise the overhangs was undertaken at an early stage
New riser locations for pipework were mainly positioned in back-of-house areas, where they could be incorporated into purpose-built cupboards that not only gave ease of access, but also suppressed noise.
The impact of noise on the Depot’s neighbours was a particular focus for the design team. An air source chiller and acoustic enclosure – located on the new flat roof – were discussed at the conceptual stage, but the size of the enclosure was a deterrent for the architects and the client. It would have been prominent from the front of the building and would have reduced the space available for the PVs.
A solution offered to the client was the simultaneous heating and cooling GSHP. This allowed the equipment to be installed internally, reducing noise break out to neighbouring properties and offering a low-carbon solution for the heating and cooling needs of the building. Initial calculations showed that – while the main public areas require heating in mid seasons – the screens still need cooling when occupied.
The old car park was replaced with a new soft-landscaping scheme, which meant the boreholes could be located within this area. Given the local geology, these were drilled to a depth of approximately 120 metres, and eight were needed, based on the heating and cooling loads calculated.
To help reduce the amount of pipework in the plantroom serving the GSHP, a manifold system was installed within the soft-landscaping area. This required a flow and return to the plantroom, and each borehole’s flow and return was connected to the manifold.
Lighting in a dark-skies policy
Lewes is in the South Downs National Park, which has an environmental zone classification of E1, as defined in Guidance Notes for the Reduction of Obtrusive Light GN01:2011. This restricts the amount of artificial light that can pollute the surrounding sky, or impact on neighbours and wildlife. As a result, selection of the internal and external luminaires for the Depot had to take into account their impact on local fauna and limit their brightening of the night sky – also known as ‘sky glow’.
Careful consideration was also given to their mounting positions, with various options sent to the client and architects for approval. An analysis of the external lighting was completed using DIALux software, to optimise the number of fittings and assess their impact on the environment.
Project team
Client: Lewes Community Screen
Architect: BFF
M+E: SGA Consulting
Structures: Price & Myers
Acoustics: Arup
Main contractor: Durtnell
Mechanical subcontractor: SMS (Southern)
Electrical subcontractor: Lindfield Electrical Services
All luminaires chosen for the building’s external lighting had an upward light ratio of 0; this is the amount of spill light that shines above the fitting. Bollards mounted to one side of the path were selected for general footway lighting, while the luminaires on the patio were installed on the underside of the overhangs above the curtain-wall glazing.
SGA Consulting held talks with a ranger from the South Downs National Park Authority to ensure the colour temperature of this external lighting was fauna friendly; the ranger recommended it be less than 3,100K. For minimal impact on the local wildlife, The Depot’s external CCTV cameras use UV light at night.
Conclusion
The challenge with the Depot was to re-use an existing building to deliver something positive and welcoming for the community. Through great team collaboration and hard work, this has been achieved – and it has been recognised with two civic trust awards from the Sussex Heritage Trust.
- Daniel Howes, MCIBSE, associate SGA Consulting