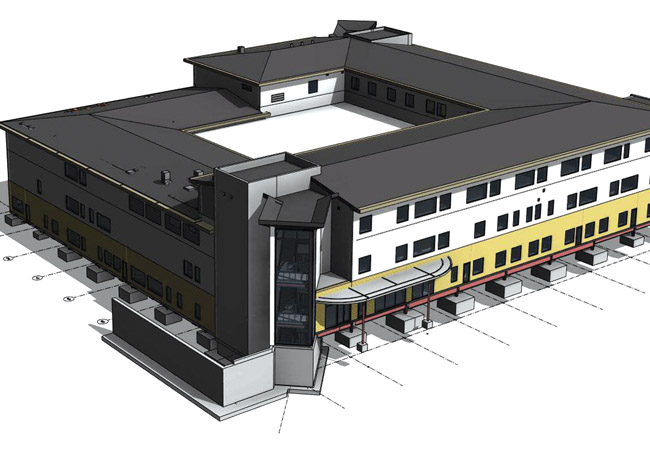
BAM started work on the new Wharfedale Hospital in 2002. The 9,500m2, 76-bed facility, which replaced an outdated Victorian hospital, comprises an endoscopy suite, minor injuries, outpatient, physiotherapy, pathology and radiotherapy departments, and two operating theatres.
Built around a quadrangle, the three/four storey hospital is designed as a patient-friendly building that is easy to navigate. The private finance initiative (PFI) project was delivered by BAM PPP which, in-conjunction with BAM Construction and BAM FM, built and now maintain the hospital.
At a glance: The approach at Wharfedale
The way maintenance is planned and undertaken at Wharfedale was transformed by:
- Creating a 3D model of the hospital containing 4,000 assets
- Digitising the condition survey process
- Using QR codes placed on assets to update information automatically within the model as checks are carried out
- Expanding our approach to cover building operations and provide tickets for PPM activities.
BAM developed its initial building information modelling (BIM) for the FM solution at UCL Academy in Camden, London, where we digitised operation and maintenance (O&M) information – such as manuals, drawings and plans – and linked it to the BIM model. This enabled the FM team to access the most current data via an iPad, and update it in real time as work was undertaken.
At Wharfedale, we saw an opportunity to develop our approach further and assist the hospital to address some of the operations-related challenges it faced.
Retro BIM modelling Wharfedale
Retrospective BIM was used to develop an operational 3D FM model of the hospital, containing more than 4,000 assets that require servicing and maintenance. During the development of the retro model, a major consideration was the building’s services and their related components and systems.
The BIM team was given a unique insight into the factors that were most important for the hospital’s operations through our discussions with BAM FM’s staff and, as a result, we identified three main focus areas:
- Prevention of scalding from hot water
- The need to locate all fire dampers and their access, which was hard to identify on the paper plans
- The ability to record planned preventative asset maintenance.
Our team modelled the associated ‘asset types’ for each issue; they were checked and verified using the existing 2D record drawings. Each major service asset was then classified using Uniclass 2, which meets the requirements for Level 2 BIM.
The data contained within the model is easily accessible using BIM360Field on an iPad, putting FM information at the users’ fingertips. This has improved the accuracy of data and cut the time for undertaking tasks.
“During the development of the retro model, a major consideration was the building’s services”
The success of this approach was seen very early on in the project when – during a fire inspection – we were able to use the model to quickly locate and provide information on all smoke and fire dampers in the hospital.
Recently, we have added additional data to the model to meet the needs of the NHS Trust. This included the creation of essential electrical distribution drawings, which highlight electrical cupboards and the areas they serve, making it easier to carry out electrical work.
Addressing Wharfedale’s operational challenges
Once the model was complete, we explored how we could use it – and other technologies – to address some of the issues raised during our initial discussions with the FM team.
Recording maintenance procedures
Planned and preventative maintenance tasks are traditionally time consuming to complete, but our approach – which uses a mobile device linked to the model – has changed this.
In previous years, the annual condition survey involved the manual completion of multiple excel sheets by facilities managers. However, the survey process is now on iPad and linked to the model. This allows users to complete checklists quickly and efficiently, view previous checklists and see what work has been carried out.
To make the process even faster, we have installed barcodes in each room, which, when scanned with the iPad, take the user straight to the relevant room’s condition survey and data. As a result, our FM team is now able to carry out 60 room surveys in two hours – 33% quicker than the manual way.
Preventing scalding
We have used the model to carry out regular checks to ensure that water is being supplied at below 40°C in all taps. Each valve is tagged with a QR code, and when this is scanned by a technician using a mobile device, they receive the latest information on that unit, including: the date of the last inspection, issues identified and when the next check is due. Once a new check is undertaken, data is updated automatically.
Plantroom at Wharfedale Hospital
More effective work planning
Building on the work to digitise the condition survey process, we have now visualised the survey results by creating hospital floor layouts that show the condition of each room. These allow the FM team and the NHS Trust to see at a glance what work needs to be undertaken over a five-year period, and to schedule these activities so that they cause minimum disruption to the hospital’s daily operations.
Currently, the layouts are paper based, but we are working to place this information within the BIM model so the client will have all the information they need at their fingertips, while being confident they are seeing the latest version.
BAM PPP is also using the layouts in its discussions with its funders, who need to see work plans before releasing funds. The diagrams provide the team with a visual tool that is quick to explain and easy to understand, helping them secure the money they need.
As a visual aid, the condition survey drawings linking back into the BIM model are far more valuable to clients and the banks, allowing them easily to see the high-priority areas and understand that our life-cycle replacement choices are based on sound evidence and a forward-looking plan of works.
Saving energy and money using latest technologies
The FM team is continually looking for ways to keep the building’s energy consumption at a minimum, while maintaining a safe and clean environment for patients and staff.
We have helped the hospital to cut electricity use in its operating theatres by 28% by shutting down the heating, ventilation and air conditioning systems when the theatres are not in use.
Sensors were fitted to reduce ventilation by 50% when the theatre was unoccupied for one hour, and shut down completely at night and over the weekends. A quick restart sequence was programmed into the building management system to switch on the ventilation in case of emergency.
These changes have resulted in annual electricity savings of more than 13,600kWh and more than six tonnes of CO2 emissions.
- Phil Palmer is virtual construction manager at BAM Construct UK