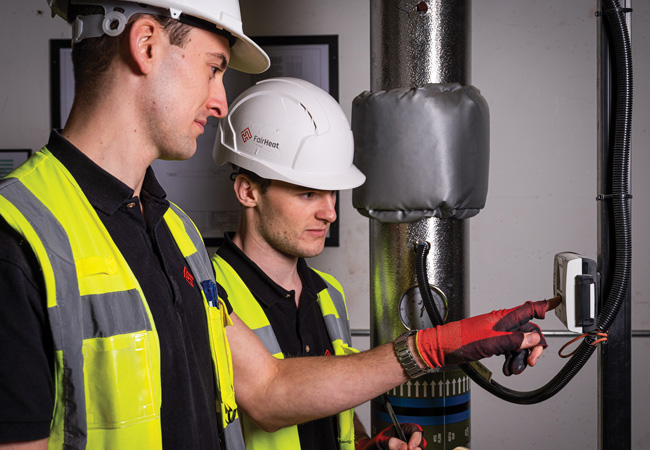
FairHeat Engineers checking the plantroom heat meters to inspect flow and return temperature performance from a central plant
Working in the construction sector as a heat-networks specialist, I have seen my fair share of policy changes and new technology trends. However, none has been as significant as the transition we are currently navigating: the heat pump has arrived, and it is here to stay. Heat-pump technology is our best bet to aggressively decarbonise the UK’s heat sector, as we move from fossil fuel-based systems and take advantage of the falling carbon intensity of the Grid.
Only 18 months ago, the projects I was supporting were gas-based combined heat and power (CHP), but this era feels well and truly behind us now. The new challenge is to integrate heat-pump technology into heating systems effectively, while still providing the resident with an affordable and reliable service.
It is now common for a development to supply both residential and commercial spaces with heating and hot water, and a communal system is often the most cost-effective way to achieve this, rather than commercial units having to install standalone systems.
This article is focused on optimising the design of low temperature heat networks (LTHN) to enable efficient integration of centralised heat-pump technology. The LTHN system in question can be considered to comprise of:
- A site-wide heat network that supplies heating and hot water to end users through heat interface units (HIUs) that separate the network from the resident’s dwelling-level heating and instantaneous hot-water systems
- A centralised energy centre containing the generation and distribution plant that serves the site-wide heat network
- Low flow temperatures of 55-60°C
- Low return temperatures of 25-30°C.
It’s all about the temperature
Even in CHP-led systems, FairHeat has been preparing developers of heat networks for low temperature design and operation. This is to combat the excessive heat losses and overheating risks that have plagued the industry from systems operating at, or above, 70°C. A heat network can supply heating and hot water to meet the demands of residents at flow temperatures of 55-60°C, but this requires joined-up thinking between the dwelling and heat-network design.
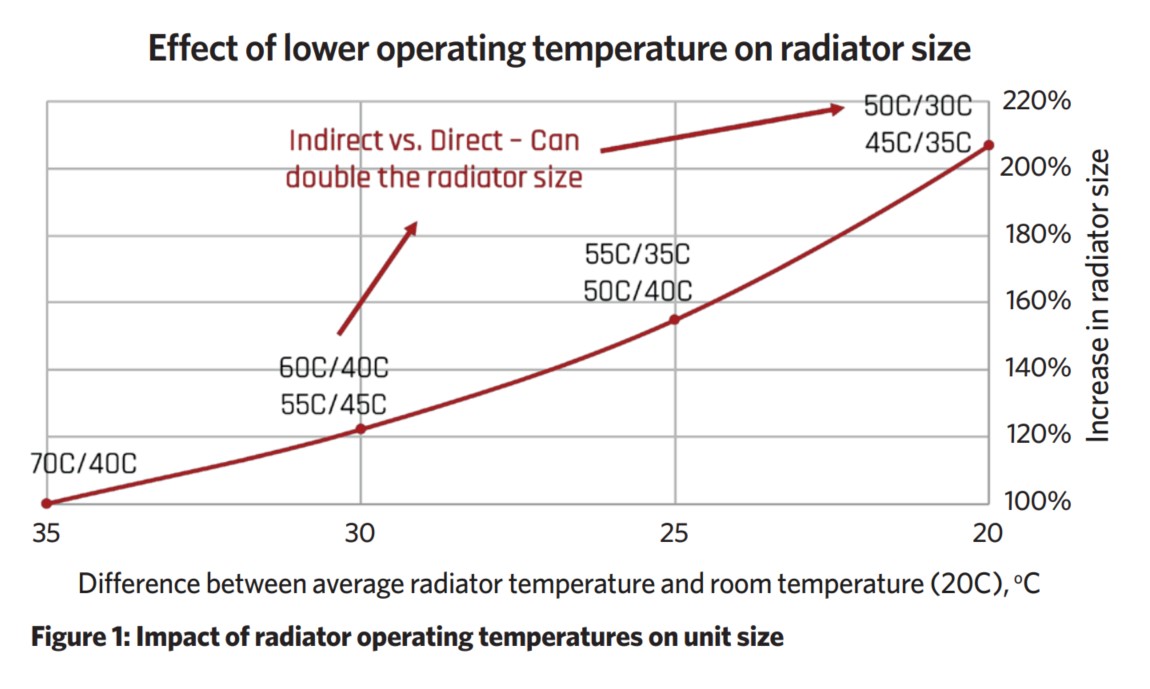
With the introduction of heat pumps, it is doubly important for the operating temperatures to be as low as possible. Heat pumps operate more efficiently at low output temperatures. Perhaps even more challenging, most models on the market have not been optimised for operating in heating mode, but are really chillers operated in reverse. For the few ‘high temperature’ heat pumps available, their coefficient of performance (COP) generally starts to be compromised at output temperatures above 60°C, which puts an upper limit on the operating temperature of heat networks.
With heat pumps, it is doubly important for the operating temperatures to be as low as possible
To make a 60°C network flow temperature work for accommodation, a forward approach temperature (the difference between the incoming and outgoing hot water) across the HIU will be required to transfer heat from the network to the dwelling. If this temperature difference is too low, the plate heat exchangers become too big, and the control stability can be compromised.
For domestic hot-water (DHW) generation, we recommend that a forward approach temperature of 5°C is used. For space heating, this will probably need to be between 7°C and 10°C depending on the HIU selected.
The HIU will need to deliver DHW at sufficient temperatures to meet the HSG 274 requirements for legionella control. Historically, there has been confusion in the industry about how this is applied to HIUs supplying instantaneous hot water, as opposed to hot-water cylinders, for which the risk is much greater because of the presence of stored water.
This has been clarified through the work of the CIBSE DHW Working Group, with the Health and Safety Executive confirming that HIUs delivering instantaneous hot water are to be considered ‘low risk’ systems, required to deliver a minimum temperature of 50°C at the outlet or immediately upstream of any TMV. This is now reflected in the updated ADE CIBSE Heat Networks Code of Practice, CP1 (2020), which permits network flow temperatures as low as 55°C.
Lastly, the HIU will need to deliver sufficient space-heating temperatures to the dwelling-level heat emitters to achieve their design outputs. Underfloor heating (UFH) systems, because of the large surface area of loops, operate at very low temperatures of 40-45°C. This makes them ideal technologies for LTHNs, as they no longer influence the minimum operating temperature of the main network, which is, instead, determined by the DHW set point. This allows LTHNs supplying UFH to operate at network flow temperatures as low as 55°C, as dictated by the DHW requirements.
Heat pumps are an expensive technology; an AHSP is likely to cost £500-800/kW of capacity
For radiator systems, the solution has become a trade-off between low temperatures and increased radiator sizes. Traditional radiators have operated with flow temperatures of 60-70°C, whereas this will need to drop to nearer 50°C for LTHNs. The increase in radiator size this necessitates can be problematic for the dwelling design, leading to aesthetically unpleasing wide or deep radiators.
As can be seen, the dwelling design is intrinsically linked to the viability of a heat pump-led heat network. This requires early consideration in the design process and alignment between the responsible design parties. We have seen a significant shift to UFH systems by developers in recent years because of the benefits they provide to LTHN operating temperatures, and the simplicity of commissioning compared to radiators.
Thermal storage: heat pumps’ best friend
Heating and hot-water demands have a frustrating characteristic for heat-network designers: the peak demand that the system must be capable of providing occurs infrequently and for short durations. Most of the time, the load is significantly lower than its absolute peak. This is illustrated by Figure 2, which shows the hourly load profile for an example, high-density, 500-unit residential scheme; 50% of the annual heat demand is occurring below 20% of peak demand.
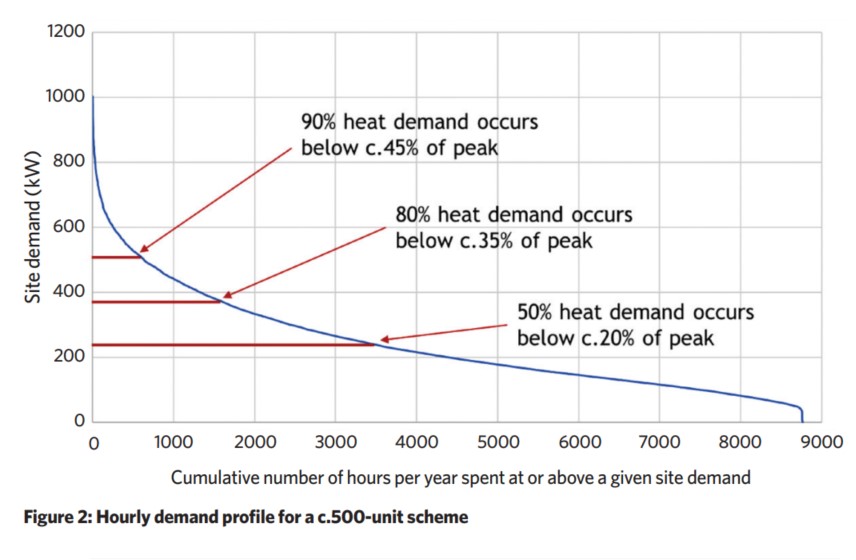
Heat pumps are an expensive technology; an air source heat pump (ASHP) is likely to cost £500-800 per kW of capacity. As a result, shifting a network’s peak demand entirely on to heat pumps will result in significantly more expensive systems. For a 1MW system, this is a £500k-800k expenditure on the heat pumps alone.
An alternative approach is to combine large thermal stores and ‘peak top-up’ boilers to limit the required heat-pump capacity. Large thermal stores are essential for extracting the maximum kWh contribution for each kW of heat-pump capacity. Because of this impact, they are a key driver for reducing the total system cost, so should be considered as early as possible in the design to ensure sufficient space is provided for their installation.
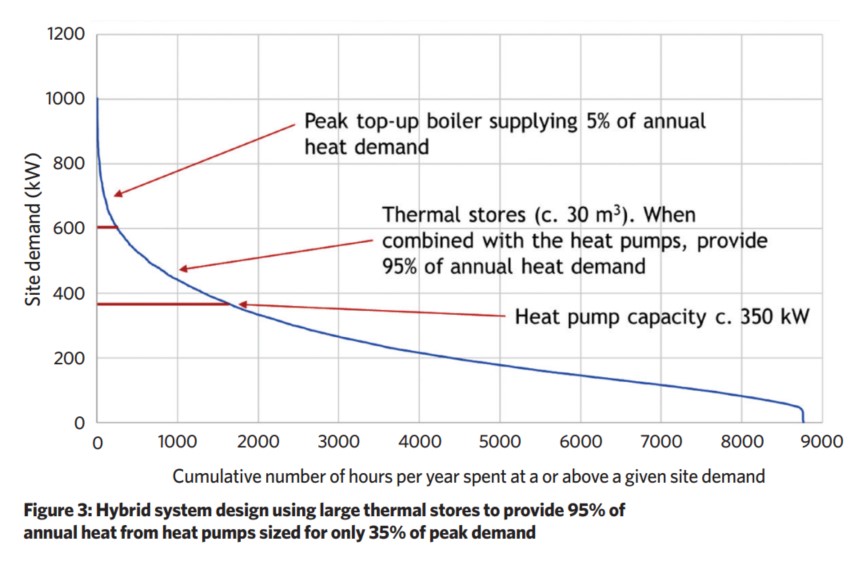
Figure 3 shows how, for the same 500-unit scheme, a 350kW heat pump, combined with a 30m3 thermal store, can provide 95% of the annual heat demand. The remaining 5% is provided by boilers, which can be gas or electric depending on the requirements of the site.
From a decarbonisation perspective, the result is comparable to an all-heat-pump system, but with several advantages. The system has a capital cost about 50% less than an all-heat-pump solution. Further, it is future-proofed, as the carbon intensity of the heat will decarbonise with the Grid and, when appropriate, the boilers can be replaced with lower-carbon technology. The system could also connect to a nearby heat network and deploy a controls strategy that determines whether to run the onsite heat pumps or use the heat-network supply, based on carbon, cost or combination of the two.
An exciting time to be in heat networks
Decarbonising heat is a massive challenge, and heat networks will play an important role in this journey. Engineering optimal solutions that are cost-effective for all stakeholders in the life-cycle is critical to their success.
Their unique position as a technology agnostic infrastructure for decarbonising heat at scale, and over a long period, is, arguably, unrivalled, and is proven to work. Scandinavia shows us that this challenge, while daunting, does not require us to reinvent the wheel.
Heat pumps are a new engineering problem to solve. To navigate this successfully will require pragmatism, consideration for the end user, and a risk-based approach, to arrive at designs that deliver for all stakeholders.
About the author
Michael Ridge is a principal engineer at FairHeat
Optioneering requires an open mind
Optioneering is a critical part of the energy strategy process, particularly with the introduction of new technologies in an uncertain policy and regulatory environment. During the optioneering stage of an energy strategy, there are two fundamental questions developers are faced with for LTHNs with heat pumps:
- What type of heat pumps should be selected?
- Where will the heat pumps be located?
On the first, it is easy to discount ground source heat pumps (GSHP) based on cost, complexity and risk. There is no doubt that due to the infrastructure requirements of the closed- or open-loop bore holes, GSHP systems will cost more £/kW than an ASHP system. However, if rooftop space either holds particularly high value that could be used for alternative means, or the scheme is large and multi-phased, locating all the heat pump on the roof may not be desirable.
Despite common misconception, closed-loop borehole GSHP systems do not require any permits from the Environmental Agency, this is specific to open-loop systems. It is also possible to drill and install as far as 240 m deep, meaning even highly dense urban developments will often provide sufficient footprint for a baseload heat pump. The key is undertaking the technical due diligence and not discounting the technology prematurely or based on mis-information.
When it comes to location, hastily disregarding alternative options can lead to ripping up designs 12-months later and starting again with a strategy that was discounted in week one. For ASHP systems, with plant already on the roof, it may be optimal to locate the entire plant on the roof. This can free up ground level space and simplify overall coordination. Weatherproofing will be required but this is not insurmountable.