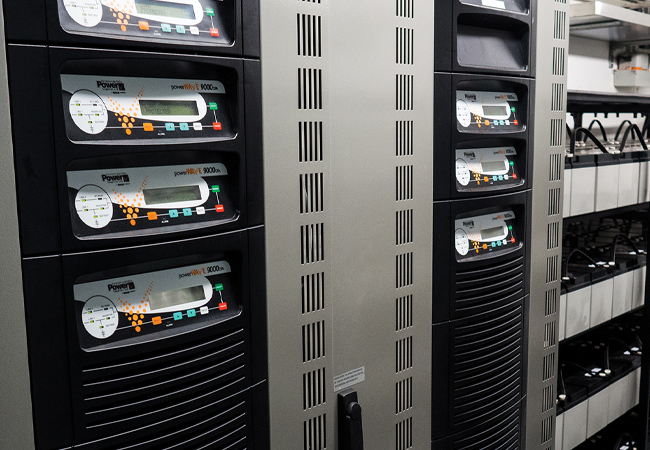
For uninterruptible power supply (UPS) system builders and users today, two battery chemistries predominate: lead-acid – typically valve-regulated lead-acid (VRLA) – and lithium-ion (Li-ion).
While Li-ion has limited presence in the UPS market, it has been growing in popularity in other areas as a result of advances in technology and power output, plus a reduction in cost. Li-ion is finding large-scale use within motive power and electricity grid storage applications and, with its rapid response, is often found in wind and solar renewable energy systems.
Li-ion batteries have a better power-to-weight ratio than similarly rated VRLA types (see Table 1). They also discharge more efficiently than VRLA at high discharge rates, although this advantage becomes less important at lower rates (see Figure 1).
Charging rates from a fully discharged state are also higher, as long as the charger can deliver the required power. Full recharging can be completed in three hours, compared with a typical 80% charge in six hours for VRLA.
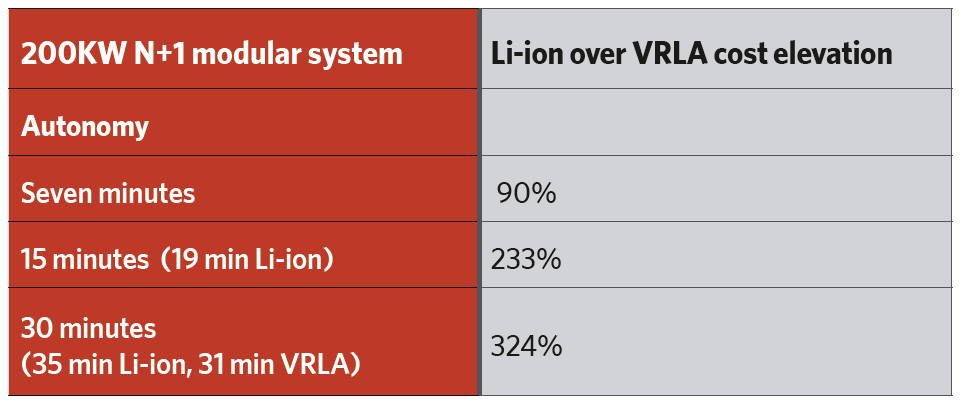
Table 1: Comparison of Li-ion and VRLA battery dimensions and weights *‘N’ is the number of UPS units required to meet the design load demand, ‘1’ indicates that a single UPS unit failure will not adversely affect meeting the load
Another advantage is a very wide usable temperature range, although discharge rates and longevity can normally be optimised by operating at 23°C ± 5K. Li-ion batteries have improved resilience to temperatures outside this range, with much better low-temperature discharge capabilities, than VRLA. This makes Li-ion much better suited to uncontrolled temperature environments where free cooling can be employed using the lower-temperature outside air.
NB: VRLA systems include battery management system Table 2: Percentage cost elevation of Li-ion over VRLA for various autonomies
However, like VRLA, operating at excessively high temperatures significantly reduces Li-ion batteries’ useful life. Figure 2 gives more detail on the two chemistries’ relative temperature/lifetime profiles.
Cost is another critical factor. Prices have fallen significantly – up to 85% – over the past decade, and these reductions naturally increase Li-ion’s appeal. Nonetheless, as Table 2 shows, Li-ion pricing is still a barrier.
However, we are definitely in the early stages of adoption. While prices aren’t decreasing as fast as previously, they are still tracking down, creating a significant upturn in adoption.
In Europe and the Middle East, there are lags in Li-ion adoption, but there is increasing deployment in North America and Asia. Figure 3 shows historical and projected future trends for battery pack manufacturing costs.
Design life is another factor, for which manufacturers are quoting up to 15 years. Operational life is probably nearer 10-12 years, but is not yet proven. This compares with a real-life norm of 7-8 years for VRLA.
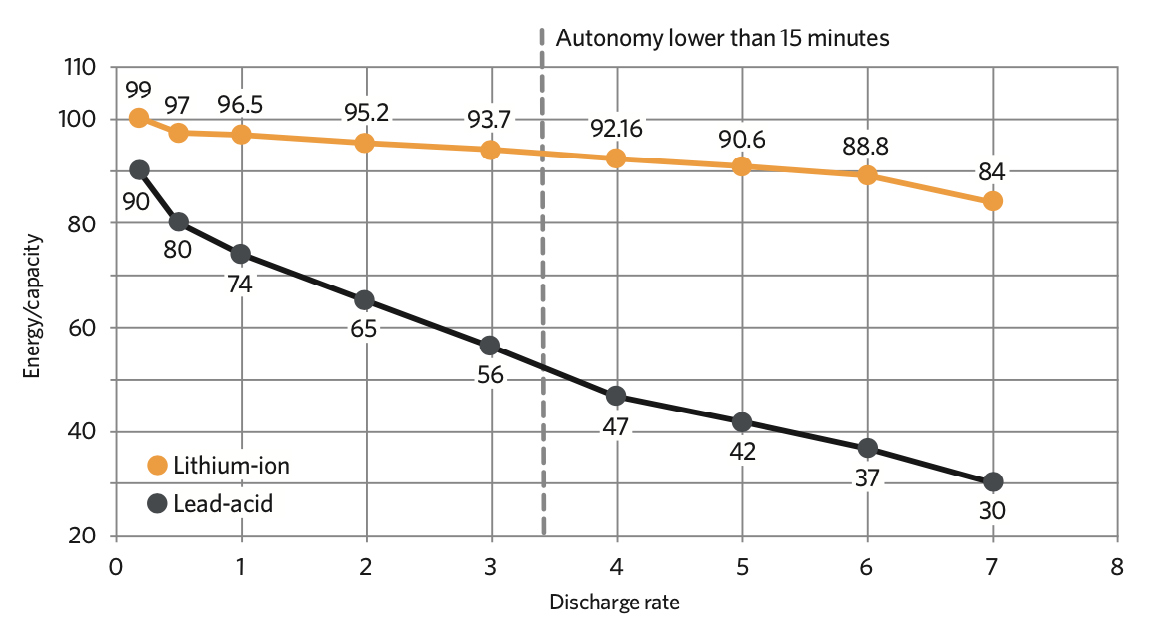
Figure 1: VRLA versus Li-ion discharge efficiency. The discharge rate (known as C) relates to the current drawn from the battery over a period of time. 1C is the current to discharge the battery in one hour. A two-hour discharge is described as 0.5C and faster discharges, for example 30 minutes, are described as 2C.
Why not Li-ion?
Li-ion enthusiasts point to the batteries’ longevity as an advantage offsetting its higher capital cost. However, Kohler Uninterruptible Power’s experience shows that UPSs – correctly installed in a suitable environment and properly maintained and supported – are typically reliable for 15 years. This neatly matches two consecutive 7-8-year VRLA lifetimes, but raises replacement coordination issues with 12-year Li-ion batteries.
Li-ion is also disadvantaged by the true costs of achieving suitable autonomy, which is traditionally 10-15 minutes for UPSs. However, in reality, most blackouts last three minutes or less, or for closer to three hours.
While VRLA costs can be decreased by designing for this lower autonomy, the same isn’t true for Li-ion. Such short autonomies can only be achieved from more expensive higher discharge-rate cells. Accurately and cost-effectively sizing for different loads is also difficult with Li-ion’s – currently very limited – choice of capacities.
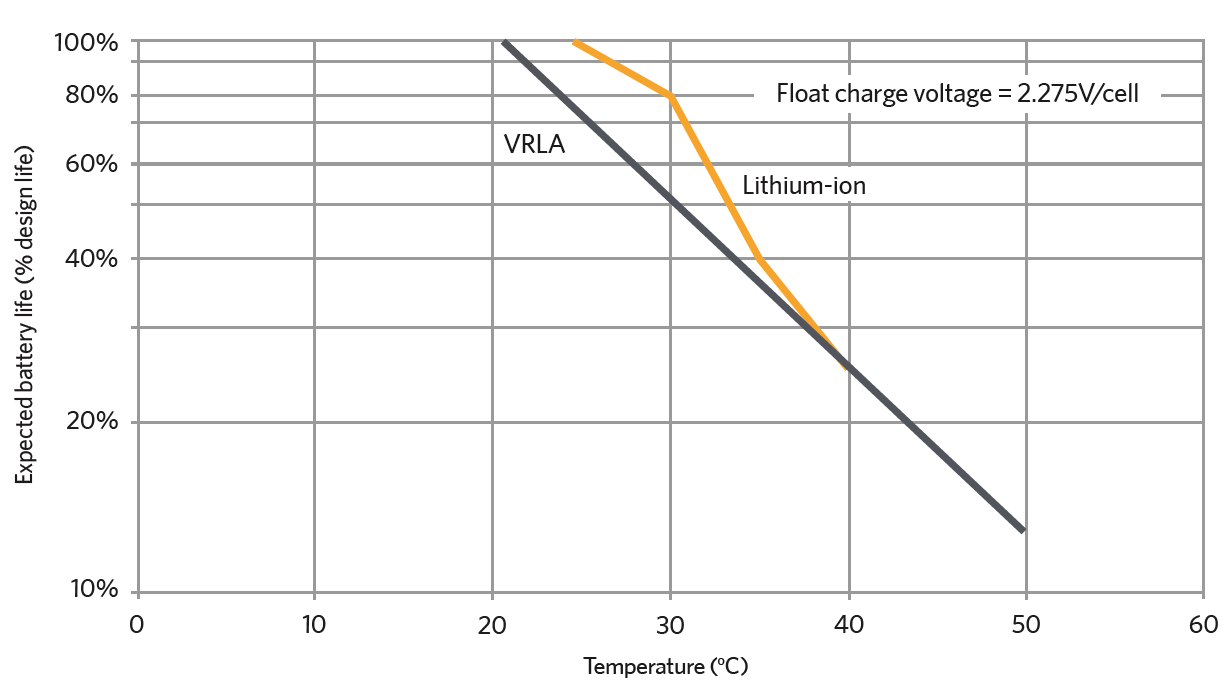
Figure 2: Expected battery life versus temperature for VRLA and Li-ion. This shows that, between 20°C and 30°C, Li-ion degrades much less than VRLA; however, at higher temperatures, degradation is similar
There is also an element of mistrust. Manufacturers have progressed considerably in addressing safety fears, through highly segregated cell designs, and mandatory advanced monitoring and management systems; however, Li-ion is still sometimes seen as unproven, and a safety risk.
End-of-life creates further problems; an exhausted Li-ion battery primarily comprises hazardous waste that’s difficult to recycle, and which is subject to high costs and restrictions during transportation.
Li-ion enthusiasts point to the batteries’ longevity as an advantage, offsetting its higher capital cost
By contrast, VRLA is up to 98% recyclable. However, as the volume of exhausted Li-ion batteries starts to grow, so will pressure to find sustainable recycling solutions. This is reflected, for example, in the US Energy Department’s launch in January of a Li-ion battery recycling research centre. The department is investing US$15m in the project, and hopes to boost the collection and recycling rate to 90% of all lithium-based technologies, up from the current rate of just 5%.
Recycling of Li-ion batteries from electric vehicles (EVs) is limited in the UK; direct recovery of precious metals from these batteries– such as cobalt, nickel and lithium – is undertaken by specialist facilities abroad, mainly in Asia, although Europe is now starting to build processing capacity.
Currently, the barriers that Li-ion faces mean its uptake is mostly limited to fast-discharge or limited-space applications that particularly need its benefits. However, UPS Li-ion battery solutions are still in their infancy, with potential for further advances.
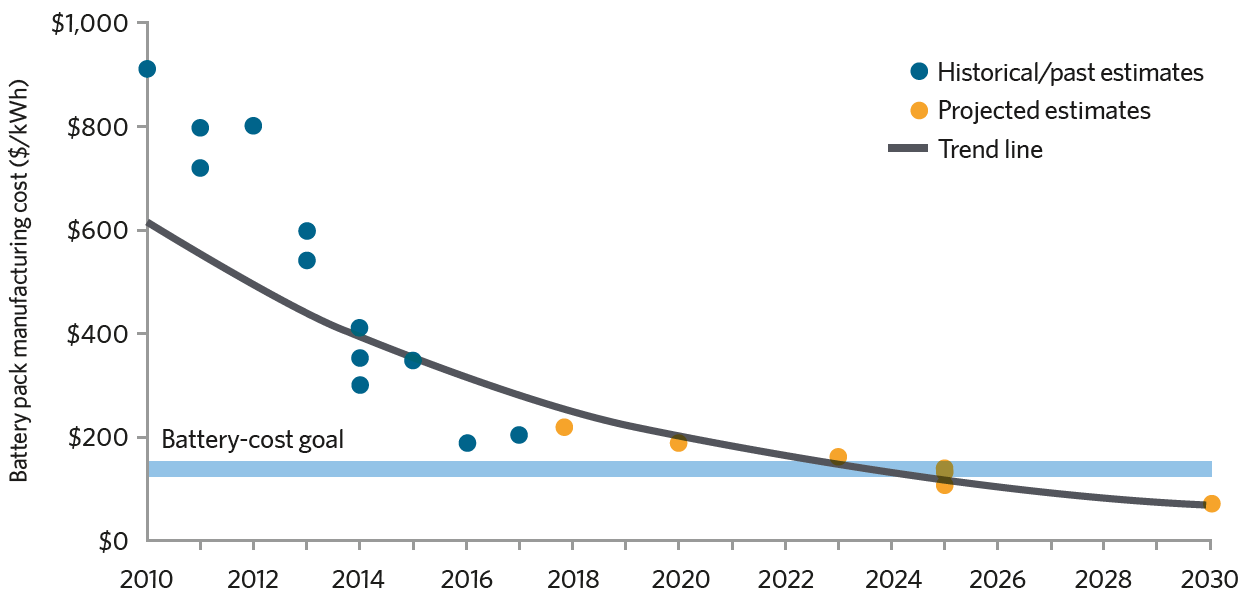
Figure 3: EV battery manufacturing cost trends. Manufacturing costs are falling and this is expected to continue.
Prices are expected to continue falling, albeit more slowly, driven primarily by growth in the EV and motive-power industries. As this happens, and Li-ion becomes more accepted by UPS owners and operators, the technology’s penetration of the data centre battery market can be expected to increase.
This growth will be accelerated when viable recycling strategies become available. In any case, the data-centre industry is motivated to replace VRLA because of perceived reliability problems and environmental restrictions.
Bloomberg New Energy Finance (BNEF) forecasts a market share increase from 15% in 2016 to 35% in 2025. According to BNEF, this is against an expected data-centre battery backup market growth from 3.5GWh to 14GWh over the same period.
However, VRLA will also continue developing. While not mandatory for VRLA, increasing use is being made of battery monitoring and management systems. These can increase VRLA battery lifetimes, potentially by up to 30%. This can, for example, increase battery life by monitoring and warning of when attention is required, and by management of the equalisation process, which corrects the charging voltage operating range.
About the author
Alex Emms is operations director at Kohler Uninterruptible Power