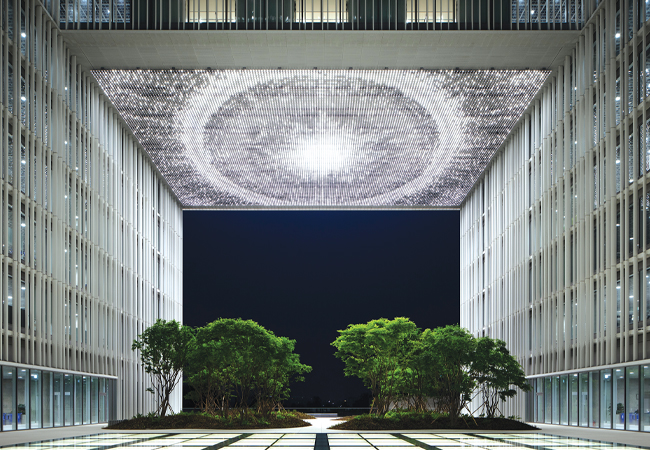
The courtyard incorporates a glazed floor to admit daylight into the atrium below
The brief was to create a landmark building with a distinct identity that was also an exemplar for low energy and sustainability, says Arup’s submission to the 2021 CIBSE Building Performance Awards, Project of the Year – Commercial/Industrical category.
The consultant’s entry is for the building services design of the Seoul headquarters of South Korea’s largest cosmetics company, Amorepacific. Arup worked on the scheme with David Chipperfield Architects Berlin. The design team has embraced the brief by making sustainability inherent to key design decisions, the most significant of which relate to the building’s form. In Seoul, the convention is for corporate headquarters to shout about their presence by building tall. However, Amorepacific’s HQ has been designed as a mid-rise, 29-storey, 110m-tall cube, to maximise the use of passive systems for daylighting, shading and natural ventilation, to reduce energy demand and enhance occupant comfort.
To avoid the creation of deep-plan office floor plates, the building’s core has been exposed by punching an opening through the roof and down through the cube’s centre, to allow natural light and air to enter the heart of the building.
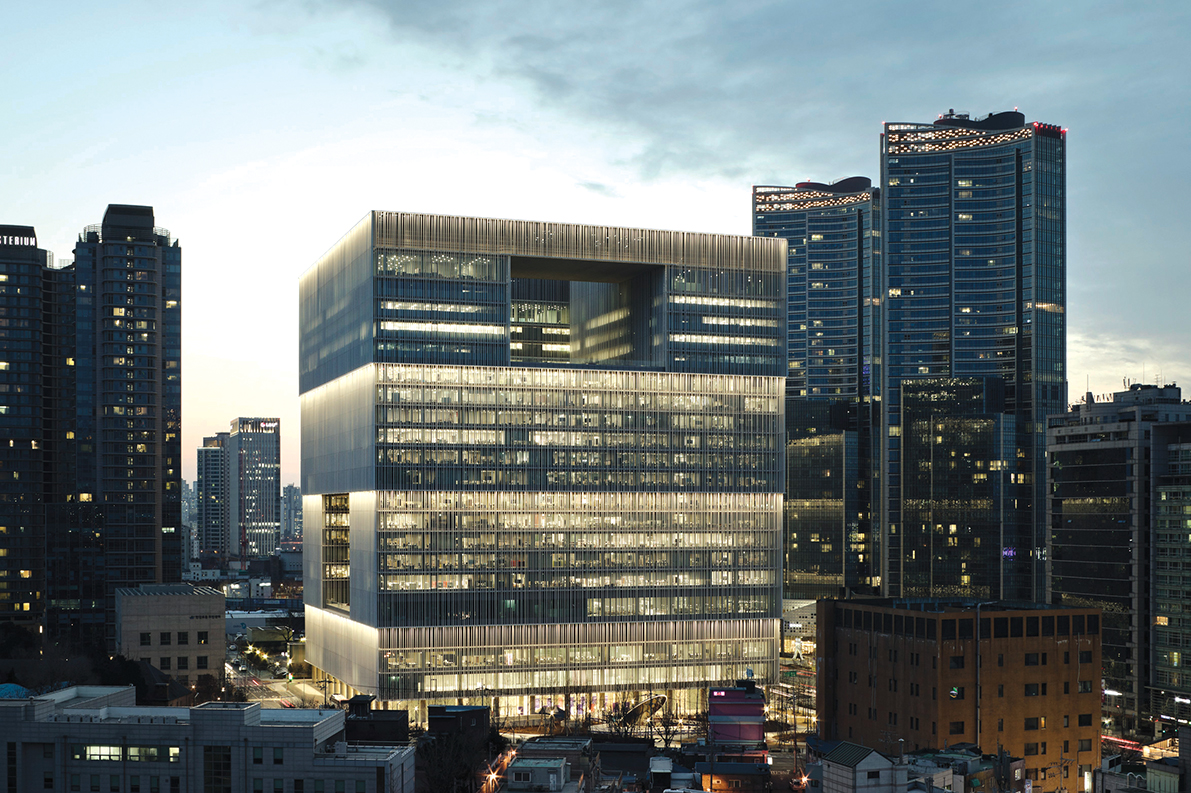
The glazed façades are partially concealed behind vertical brise soleil
‘The proportions of the building have been carefully designed around a central atrium to maximise the effectiveness of natural ventilation and daylight on all floors,’ says Ant Marsh, building performance and systems engineer at Arup.
Additional horizontal openings have been punched through the elevations to the core, on the fifth, 11th and 17th floors. These openings house landscaped gardens and terraces to provide recreational spaces for staff and visitors. Arup optimised the location of the openings to take into account the impact of the prevailing wind direction and minimise wind deflections from the façades down onto the entrances below.
The façade is formed from triple-glazed panels, with solar-reflective glass, to maximise daylight and views while retaining thermal resistance to heat gains
A courtyard has been created at the base of the building’s open core, on what is actually the roof of the building’s double-height atrium. This courtyard incorporates a glazed floor to admit daylight into the atrium below. The floor is partially covered by a 70mm-deep reflecting pool, which enhances the courtyard’s calming ambiance.
The effectiveness of the courtyard façade shading reduces the office peak load by 50% at upper levels and 25% at lower levels, which reduces the required size of terminal units and chillers for climate control in offices.
The courtyard is intended to be the communal centre of the company workplace. Above it, the quadrangular office floor plates provide 80,000m2 of office space; below it, the ground-level atrium is open to visitors and the public on all sides. In addition to being the main arrival point, the atrium is an event space for art installations, concerts, lectures and other cultural activities, including a museum, restaurants, retail spaces, and 450-seat auditorium.
Controlling solar gains
While the atrium is open to the streets, above it the building’s glazed façades are partially concealed behind a diaphanous covering of vertical brise soleil. The fins are needed because the building’s orientation at an angle of 45° from north means that two elevations face in a northerly direction, while glare and solar gains have to be carefully controlled on the south-west and south-east elevations.
The distinctive metal curtain formed by the bespoke brise soleil solution has become a signature feature of the building. It comprises 1,150 aluminium fins in four sizes – 450mm, 350mm, 250mm and 200mm deep. Although these fins appear to be uniform, they are grouped in patterns that vary around the building in response to solar exposure. On the north-east and north-west elevations, where direct solar exposure is minimal during normal work hours, shallow fins are used to maximise the amount of natural light permeating the façade. Controlling solar gain and glare is more critical on the south-east and south-west façades, so deeper fins are used to give enhanced solar shading and reduce cooling loads.
South Korea is subject to typhoons, so the brise soleil are designed to resist high wind loads. To optimise the fin design, Arup conducted a series of tests to enable the behaviour of wind at the edges of the large façade openings, and the down-wash impact at entrances, to be predicted, while ensuring the structural robustness of the fins. As a result of the tests, the engineer introduced 3mm linear vertical protrusions to the fins to encourage vortex shedding. These linear strips help induce micro turbulence, which reduces deflection and vibration effects, while improving robustness.
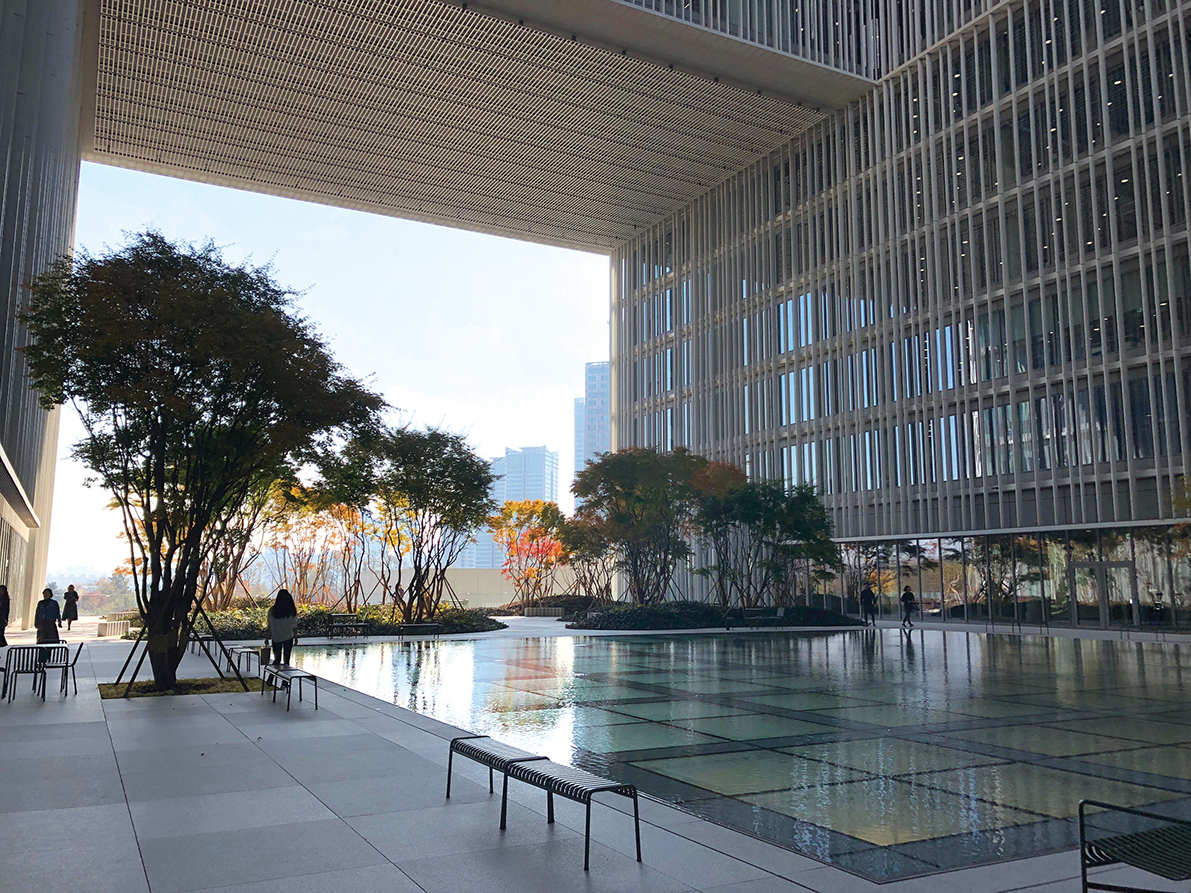
The courtyard floor is partially covered by a 70mm-deep reflecting pool
Behind the brise soleil, the façade is formed from triple-glazed panels, with solar-reflective glass, to maximise daylight and views while retaining good thermal resistance to both heat gains and losses.
The brise soleil are separated from the glazed façades by perforated metal walkways at each floor level. As well as supporting the fins, these provide horizontal shading and allow the outside of the windows to be cleaned. The walkways also provide access to the motorised ventilation louvres at the top and bottom of the windows that enable the office floor plates to be naturally ventilated.
Ventilation
The external design conditions for Seoul are: 31.2°C drybulb/25.5°C wetbulb summer, and -11.3°C in winter. The opportunity for natural ventilation on the office floors during the swing seasons has been maximised by locating workstations next to the façade, with meeting rooms and auxiliary areas concentrated in the interior zones of floor plates. Motorised ventilation louvres at high and low level ventilate the perimeter spaces in spring and autumn, to reduce power demand from the air conditioning.
Underfloor mechanical displacement ventilation serves the central floor zone and provides mixed-mode ventilation to the perimeter. Displacement ventilation was chosen to provide flexibility in the layout for the floor plans and to facilitate a simple zoning control strategy between the perimeter zone (which can be isolated when the windows are open) and the central floor plate zone, which remains operational regardless of window position. ‘During spring and autumn, conditions at the perimeter of the building can be maintained by natural ventilation, as can those in the areas of building facing the courtyard,’ explains Marsh.
Twin elevators are a double win
The central courtyard arrangement means the lift and stair cores have had to be positioned in the four corners of the building. The cores comprise five passenger lift shafts, and one service and firefighting lift.
Unusually, the scheme features two independent lift cars in each shaft, one on top of the other. Both cabins use the same guide rails and landing doors. According to Arup, this twin-lift arrangement, with hall control, gives ‘an increase in conveyance capacity and a reduction in waiting time, as well as a reduction in energy consumption’ when compared with a conventional double-deck lift. At the time, it was the largest application of its kind in the region.
In line with LEED, office ventilation rates are 30% higher than ASHRAE 62.1 minimum requirements. The systems are designed to operate at full fresh air when external conditions allow. An interlock prevents operation of the mechanical ventilation system when the louvres are open.
Office temperatures are maintained by a combination of perimeter fan-coil units for the perimeter zones, and floor-standing air handling units for the central areas. Fresh air is delivered from central air handling units, located at roof level. Placing workstations next to windows also maximises the use of daylight and exploits views out; 98% of workspaces have a direct line of sight to the outside.
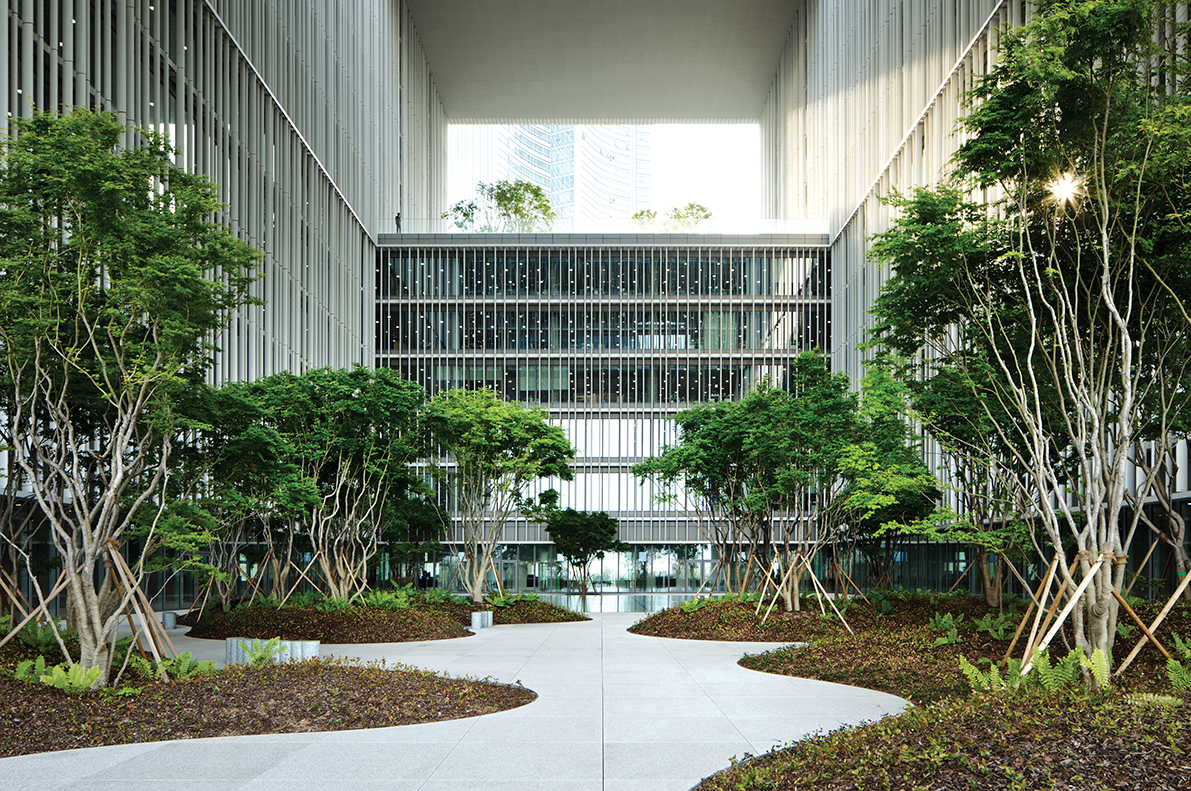
The courtyard is intended to be the communal centre of the workplace
A central chilled water system will provide cooling to meet the building requirements. Chilled water plant is installed in the basement, with water cooled chillers, primary and secondary pumps, and ancillary equipment located in a dedicated plant room. Cooling towers provide heat rejection for the chillers.
The maximum cooling load for the site is about 10MW. Local codes limit the cooling that can be directly generated using dedicated chillers to 40% of the total building load. The chiller room will house four water-cooled centrifugal chillers. Two chillers provide chilled water directly to the primary chilled water system, while two chillers are linked to a bank of individual ice storage tanks located in the basement.
During the night, the ice storage chillers will operate to generate ice in the storage tanks. During the day, the peak cooling load will then be met by a combination of the direct chillers (40%) with the ice storage chillers providing cooling directly to the building (30%) and the release of cooling energy that has been stored in the ice banks overnight (30%). Each of the three chilled water generation elements will be fed into a single primary header from which connections will be made to each core for distribution throughout the building.
Placing workstations next to windows maximises the use of daylight and exploits views out
The primary source of heat for the building will be steam. Steam will be generated by four steam boilers. Steam will be used directly for heating coils and humidification within air handling units, and for domestic water heating. Steam will be used to generate low temperature hot water, which will be distributed within each core to provide heating as required at each level of the building.
The building was awarded LEED Gold certification. This included a ‘LEED innovation in design’ credit for the use of an ice-storage system. The system was introduced to increase the efficiency of the cooling system by producing and storing extra coolth at night. This is used to offset the cooling requirement the following day, to help to minimise the building’s peak electrical loads – which also helps to reduce capacity requirement on the local electricity grid.
In addition, to reduce demand for potable water and minimise wastewater generation, the building incorporates rainwater harvesting, greywater treatment and low-flow water fixtures.
On the electrical systems, sub-metering is included on all electrical distribution points in the building. Dali lighting control, including daylight linking and occupancy sensing, were also used to reduce energy consumption, and the scheme has roof-mounted PV panels.
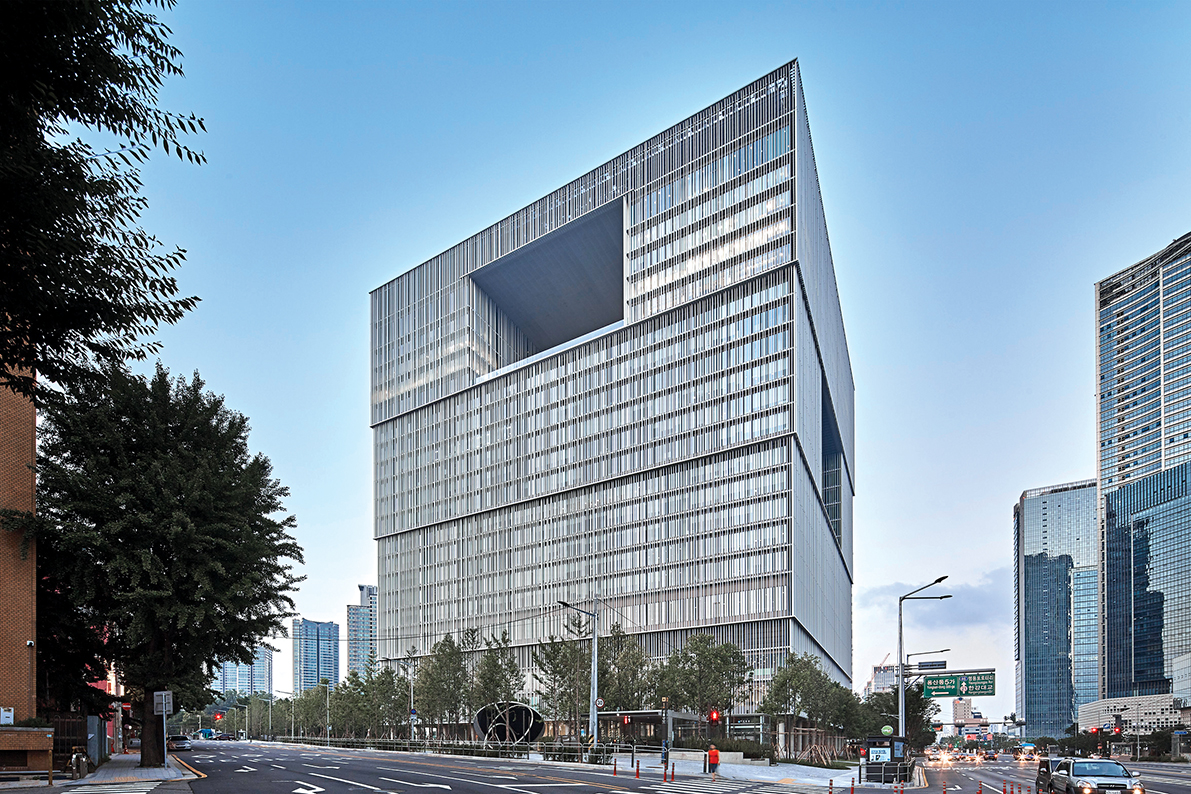
Performance data
In 2018, Amorepacific moved into its new headquarters. It undertook an occupant survey, focusing on the impact of the new facility on staff satisfaction and wellbeing. Impressively, the survey found that, after relocating to the new headquarters, 70% of employees felt the workplace environment had improved.
Amorepacific also uses an online platform to solicit ongoing feedback from staff on the building’s internal environment. These comments are used to make adjustments and give feedback on user preference. After an initial period of operation, the company provided 12 months of detailed energy performance data, which formed the basis of an energy-performance review after the building’s first full year in operation.
Based on the review, Arup made a number of suggestions to optimise the building’s performance, including:
- Examine the operation of the natural ventilation system and whether greater energy savings could be realised
- Examine the operation of the floors with the lowest energy consumption to determine whether there are lessons that can be applied to floors with a higher consumption
- Check the lighting loads on the floors to see whether more savings can be made by adjusting the automated lighting-control system
- Consider whether additional sub-metering of the main supply would allow a better understanding of the contribution of individual sub-systems to overall energy consumption
- Examine the sub-metering of the renewable and low carbon systems (for example, PV and ice storage) to ascertain whether they are delivering peak operational benefit
- Examine the sub-metering of water to determine more detail on consumption patterns, and compare with Korean benchmark data to see where improvements can be made.
Utility consumption
The overall utility use for the building was calculated and converted into industry-standard energy use intensity (EUI) figures, so that the building could be compared against other office buildings.
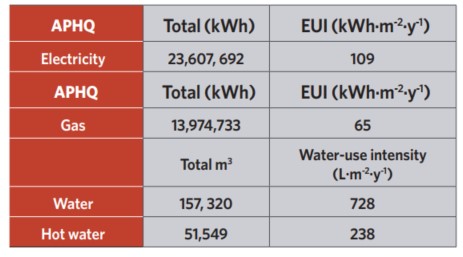
The building performance data compared well with benchmarks for South Korean commercial buildings taken from a peer-reviewed academic study published in 2017. This study takes data from South Korean government statistics and derives a set of internationally comparable benchmark values for a range of building types.
One of the key findings from the Arup study was that the building’s operational energy performance is, overall, 50% below South Korean benchmarks for commercial buildings. The study also showed that the headquarters performs significantly better than the South Korean benchmarks across all categories of end-use energy consumption, with reductions of 62% for mains power, 38% for lighting, 42% for small power and 52% for gas (for heating).
When the Amorepacific HQ building won Project of the Year – Commercial/Industrial category in this year’s CIBSE Building Performance Awards, the judges commended the scheme for ‘its contribution to the quality of life for the building’s occupants and visitors’. A worthy winner.