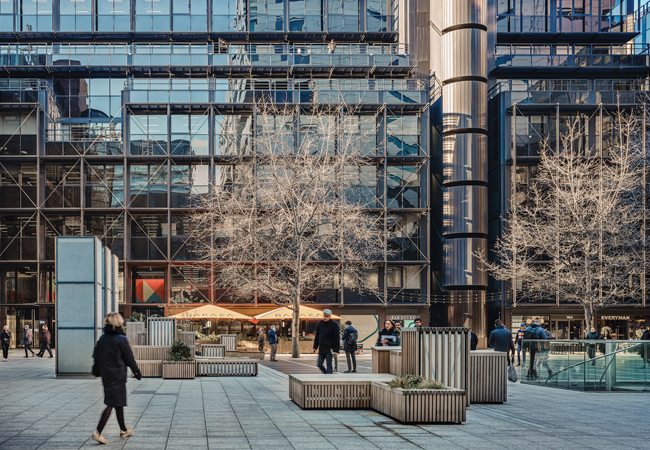
1 Finsbury Avenue is still a pioneering development
When it was built, 1 Finsbury Avenue was a pioneer of high-tech, high-end office buildings. Designed by Arup Associates and built in 1984, at the time of the stock market Big Bang, the eight-storey spec-office building was one of the first to be completed as part of London’s Broadgate development.
The office – with its deep floor plates illuminated by a central glazed atrium and distinctive, glazed, black steel façade, featuring its prominent diagonal bracing and brise soleil – was intended for a single finance tenant.
Almost 40 years on, and 1 Finsbury Avenue is still a pioneering development. It now has listed building status; its banking tenant has moved out; and it has undergone a major refurbishment designed by architect Allford Hall Monaghan Morris (AHMM) to make the building attractive to a new type of tenant – the silicon-tech crowd from nearby Old Street and Shoreditch.
Radically, rather than gut the building and rebuild it anew, the focus of its refurbishment has been to reuse as much of the original as practical to extend the life of this office.
Elements that would normally be replaced in an office refurbishment have been renovated and reused, including 90% of the central plant. ‘Reusing the plant was hard work for everyone, which couldn’t have been undertaken without a team effort,’ says Mike Beaven, director – and Fellow – of Arup, the project’s building services engineers.
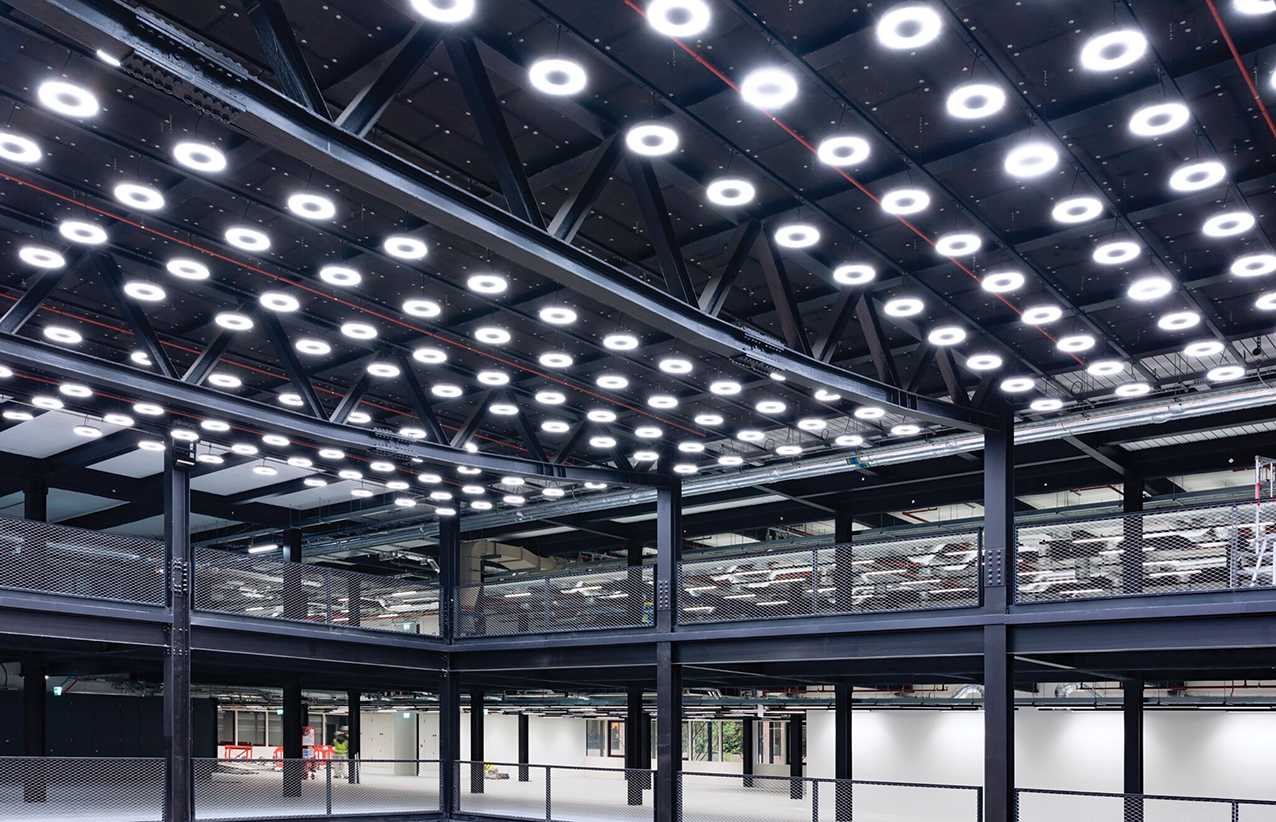
All the floor plates were gutted, including stripping out suspended ceilings
The refurbished building features a new pared-back aesthetic. Ceilings have been removed from the office floors; the basement car park has been replaced with cycle parking and showers; the basement squash courts are now a two-screen cinema; and the roof has been opened up to provide an eighth-floor outside terrace. Externally, the biggest change is that the ground floor has been opened up to make the building more permeable, with the addition of retail units, cafes and restaurants, which open onto the street and to the atrium.
Developing a building services solution that used much of the existing services was quite a challenge. The eight-storey building had been occupied from completion by investment bank UBS Warburg. During that time, the original building services systems had undergone multiple interventions to adapt them to the changing needs of its tenant, including conversion of the original overhead variable air volume (VAV) air conditioning system to an underfloor system.
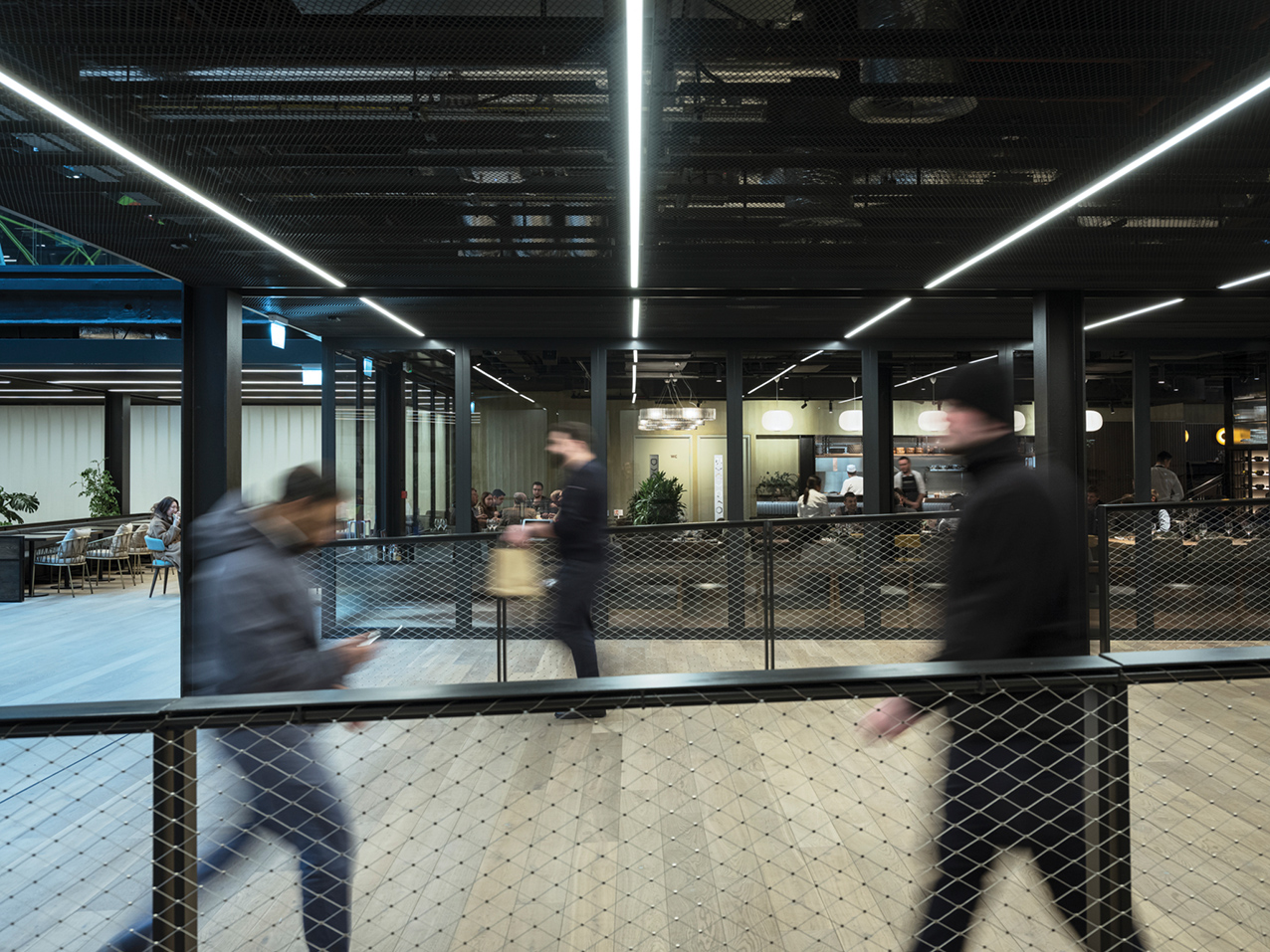
The design has created a raw aesthetic
More major interventions included flooring over the atrium at Level 3 to create a dealing floor supported by a data centre squeezed onto the floor below. Beaven describes it as ‘a banking factory with lots of cooling, chillers and power’. This banking factory was serviced by four giant, roof-mounted air handling units (AHUs), each supplying 20m3·s-1 of air to a VAV air conditioning system. The AHUs were located in pairs, two above the service riser in the north core and two above the south core riser.
Each core also incorporates a cooling tower connected to a large centrifugal chiller in the basement, as part of the landlord’s primary cooling system for the VAV AHUs. Additional air-cooled chillers had been squeezed into spaces around the roof to provide the cooling to the data hall.
Heating and hot water load 38.43kWh.m-2 per year Total energy load (based on Part L energy modelling by Arup) Carbon emissions (all) 28.2kgCO2.m-2 (based on Part L energy modelling) Annual mains water consumption (BREEAM Wat 01 methodology) Airtightness at 50Pa 7.24m3.h-1.m-2 (sample of the existing façade on level 7) Overall thermal bridging heat transfer coefficient (Y-value) 0.38W.m-2K Embodied/whole-life carbon 11.55kgCO2eq.m-2 (value refers to structure manufacture + construction processes A1-A5. Estimated using Arup’s embodied carbon tool PECC. Assumes 0KgCO2eq.m-2 for retained curtain wall façade and mainly retained central plant).Building data
Under the refurbishment, all the floor plates were gutted, including stripping out the suspended ceilings and all the existing services. ‘We thought about reconfiguring the VAV [on the office floors], but the market place wanted water-cooled because it is more efficient and saves on carbon emissions,’ explains Beaven.
Two-pipe fan coil units (FCUs) now provide cooling to the refurbished office floors. Fresh air is ducted to the units at a rate of 16L·s-1 per person, based on an occupant density of one person per 8m2 of floor area. The FCUs, along with all of the other services installed under the Category A fit-out – including a new sprinkler system – have been left exposed to give the offices a more raw aesthetic.
A major challenge of fitting out this 40-year-old building to serve the current market is that its floor-to-soffit height is less than in today’s speculative offices. ‘The slab-to-slab height was comparatively low compared with today’s offices, so, by exposing the services, we were able to push them up between the beams to minimise their visual impact,’ says Dave Pearce, associate director at Arup.
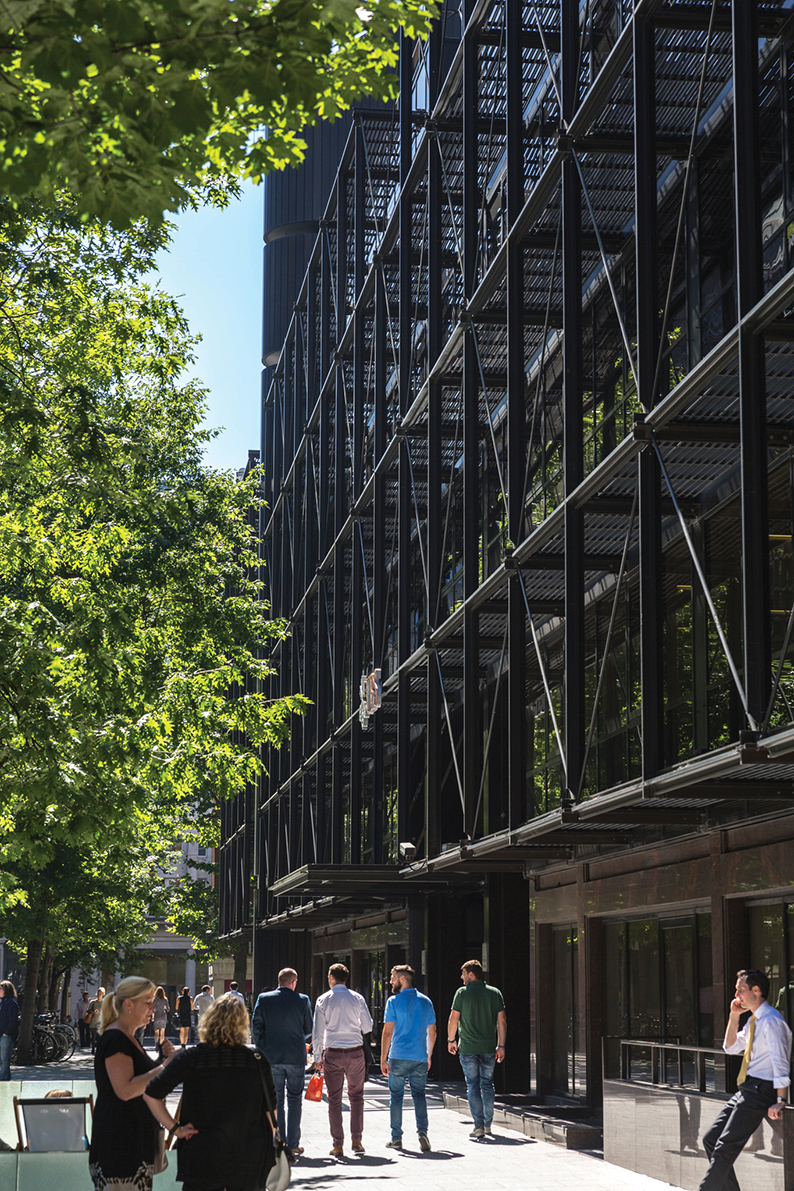
The building has retained its distinctive façade
Originally, British Land had intended to fit out one office floor to show potential tenants what could be achieved, but the landlord was so impressed with the solution it decided to adopt it across all floors.
Level 2 was the most challenging office floor to fit out. It had originally housed the bank’s data centre and, as such, contained some very large chilled water pipes and pumps that Arup wanted to retain to service the refurbished building. Its fit-out was further complicated by the need to accommodate existing ductwork fitted to extract smoke from high level in the floored-over lower section of the atrium to outside.
Fortunately, the building had been point-cloud surveyed at the outset, making it easier to accurately coordinate the new with the existing services and structure. ‘Having a point cloud scan was really important. It gave us a really good 3D model to work from to ensure we could maintain the clear height on the office floor,’ explains Beaven.
Smart controls
The services on the refurbished floors also include Internet of Things gateways on each system to provide smart control. Beaven says that, as far as Arup is aware, ‘it is the first existing building, as opposed to it being a new building built from scratch, that has been made smart’. He says the control is there for current and future tenants to manage lighting and comfort conditions, ‘if they want it’.
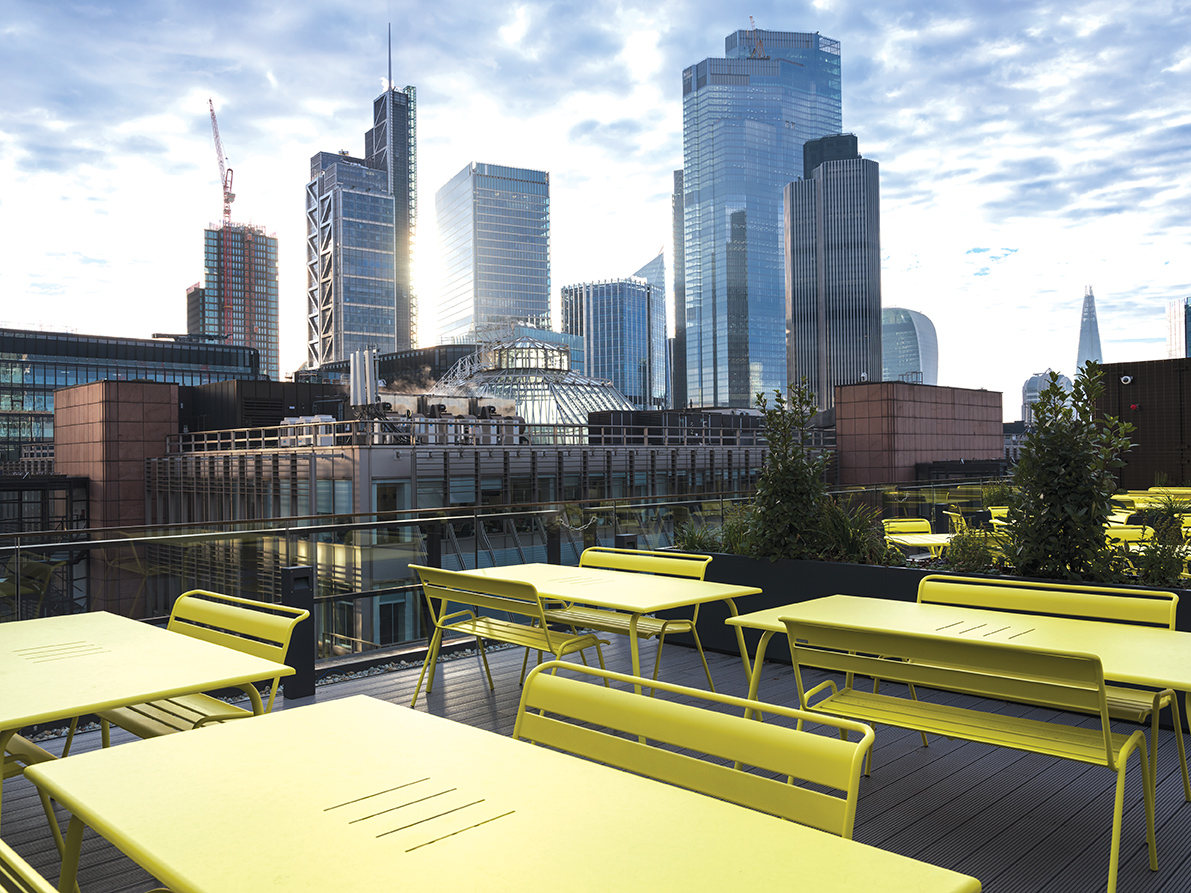
The new tenant roof terraces
Fresh air to the offices is supplied predominantly from the two existing roof-mounted VAV AHUs above the building’s south core. These have been refurbished and heat recovery systems added. The units now run at a reduced capacity. ‘The old VAV system [supplied fresh air and office cooling] on a recirculation basis, so it was pushing a lot of air around the space,’ says Pearce. ‘Switching to FCUs and a fresh air-only system enabled us to reduce the volume of supply air.’
In addition to the two existing AHUs, fresh air is supplied from a new 19m3·s-1 AHU located above the north core. This unit replaces the two giant VAV AHUs that have had to be removed to create access to the new tenant roof terraces.
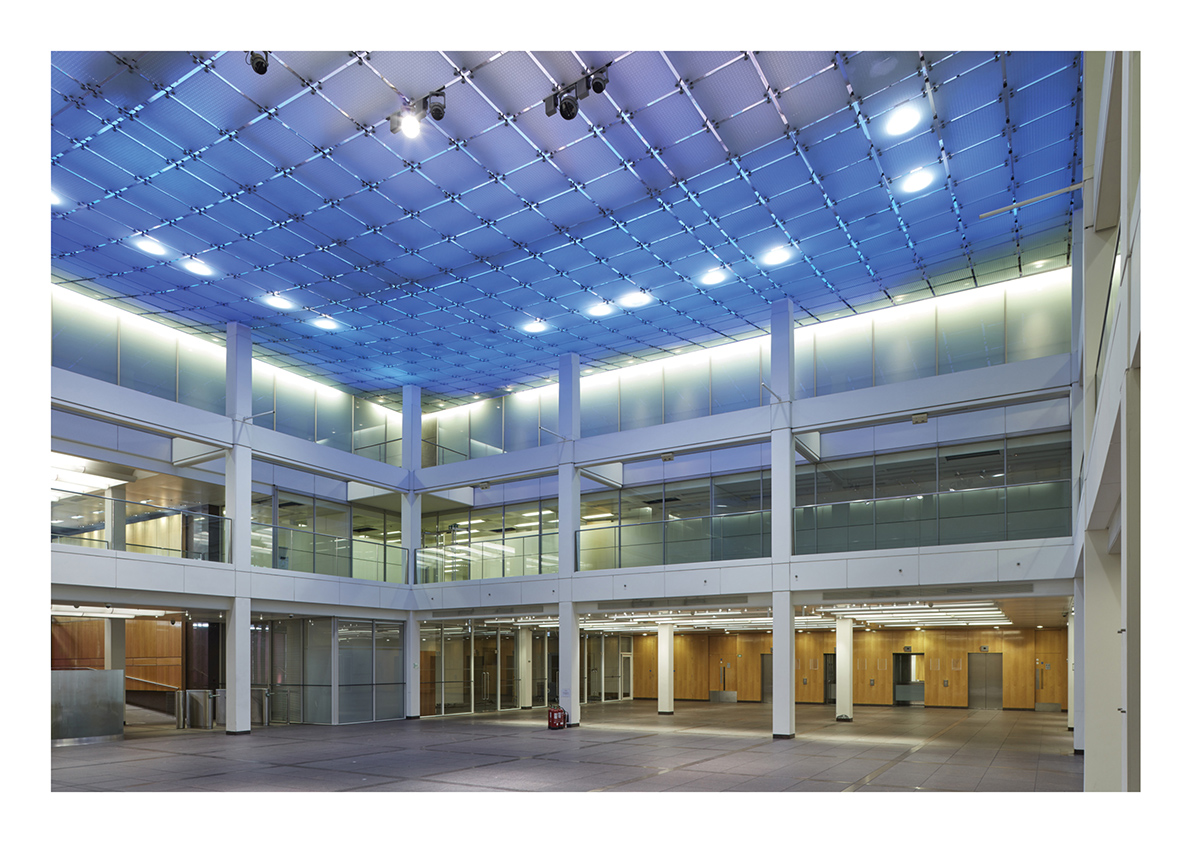
Before
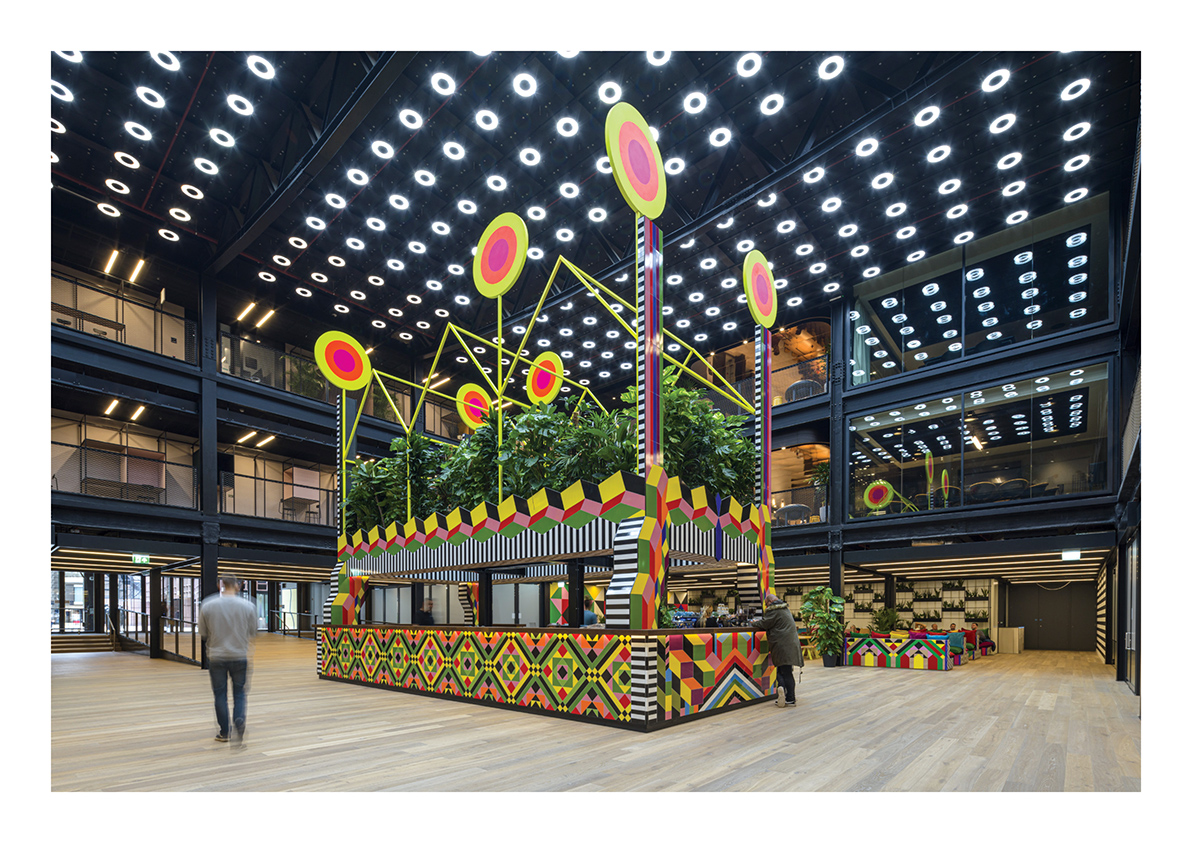
After
‘Moving to a FCU enabled the architects to provide lifts and stair access to the roof level for the two roof terraces,’ says Pearce. It was not easy: ‘We spent an awful lot of blood, sweat and tears routing pipework to create the roof terraces, because there were an awful lot of services running between the two services cores,’ Beaven adds.
Chilled water to the AHUs is supplied from the existing cooling towers and basement chillers. The cooling towers had new impellers, belts and bearings fitted. ‘They were stainless steel, built to the original, exceptional Arup specification, so they were relatively simple to refurbish,’ laughs Beaven. The chillers originally installed by the bank to cool the data hall have also been reused to provide chilled water to the FCU system. ‘We capacity tested them using a heat bank and they delivered almost 100%, even after running for 20 years at 24 hours a day,’ says Beaven. ‘So they are still really good chillers, in good nick, which meant we were able to retain them.’
The load profile works well; in the morning everyone cycles in and uses showers, then, for rest of the day, most hot-water use is retail
Beaven says a process of ‘test, appraise, use or abandon’ was applied rigorously to all existing plant, to ensure it was capable of functioning for the 15-year tenant lease period to meet the team’s ambition for reuse. This included getting the original equipment manufacturers on site to survey the plant and provide a report and recommendations on the work needed to extend its life.
‘It was an exhaustive process of testing, getting results back, seeing what interventions or improvements were needed, and then applying them before the plant could be offered as a going concern,’ Beaven adds. The team was helped in this process, he says, by the bank having maintained the plant properly; Beaven describes it as ‘like having a car with a full service history’.
Pearce says reusing the plant and distribution pipework was key to enabling the landlord to get the building back onto the market as soon as possible. ‘If we’d stripped out all the major plant, especially the distribution pipework in the risers, it would have had major programme implications, which would have added months to the completion date.’
RETAINING THE HEATED FAÇADE
The façade is a proprietary system manufactured by façade specialist Gartner. It is heated by circulating hot water through the transoms and mullions, which help offset perimeter heat losses from the office floors. The hot water is supplied at a temperature of around 40°C on a bay-by-bay basis from a perimeter heating flow-and-return loop at a high level on each floor plate. A thermal break separates the heated internal skin from the external skin. ‘We had an option to put in radiators, but the façade was mentioned in the building’s listing, so we decided as a team that it was a good idea to retain it,’ says Beavan.
As a part of the reuse strategy, thermal imaging was used to prove the façade was still performing as intended. It was also tested for airtightness, to see how it compared with current Building Regulations requirements for air leakage: ‘It was pretty close – just a sniff off,’ says Beavan. Concerns about the condition of the mullions and transoms internally were allayed when a link bridge was removed, which provided the opportunity to access the façade panels. ‘We were able to cut sections to ensure it was still in good condition,’ Beavan adds.
The reuse strategy was applied pragmatically on the building services plant. For example, Beaven says the boilers were ‘pretty good’, but it was ‘much cheaper to replace these than to refurbish them in situ’.
One element of the building that had to be retained was its distinctive heated, black-steel and glazed façade system, which was fundamental to keeping the perimeter of the refurbished office floor plates comfortable in winter (see panel, ‘Retaining the heated façade’).
Reusing the façade had major implications when it came to converting the ground-floor offices into shops and restaurants. ‘Normally with retail, we’d put a big louvre at top of the façade. This was not possible because the façade was listed.’ Instead, new louvres have had to be installed in the reveals formed in the recesses created by the building’s four perimeter stair towers; these cannot be seen when the building is viewed in elevation. The louvres ensure tenants can duct fresh air in and exhaust air out of their demise.
In addition, the landlord supplies chilled water, hot water, domestic hot water, cold water and power to each retail unit. Because of the amount of retail on the ground floor, new calorifiers had to be installed to serve the shops and restaurants and the new cyclists’ showers in the basement.
‘The load profile works well; in the morning, everyone cycles in and uses showers, then, for rest of the day, most hot-water use is retail,’ Beaven says.
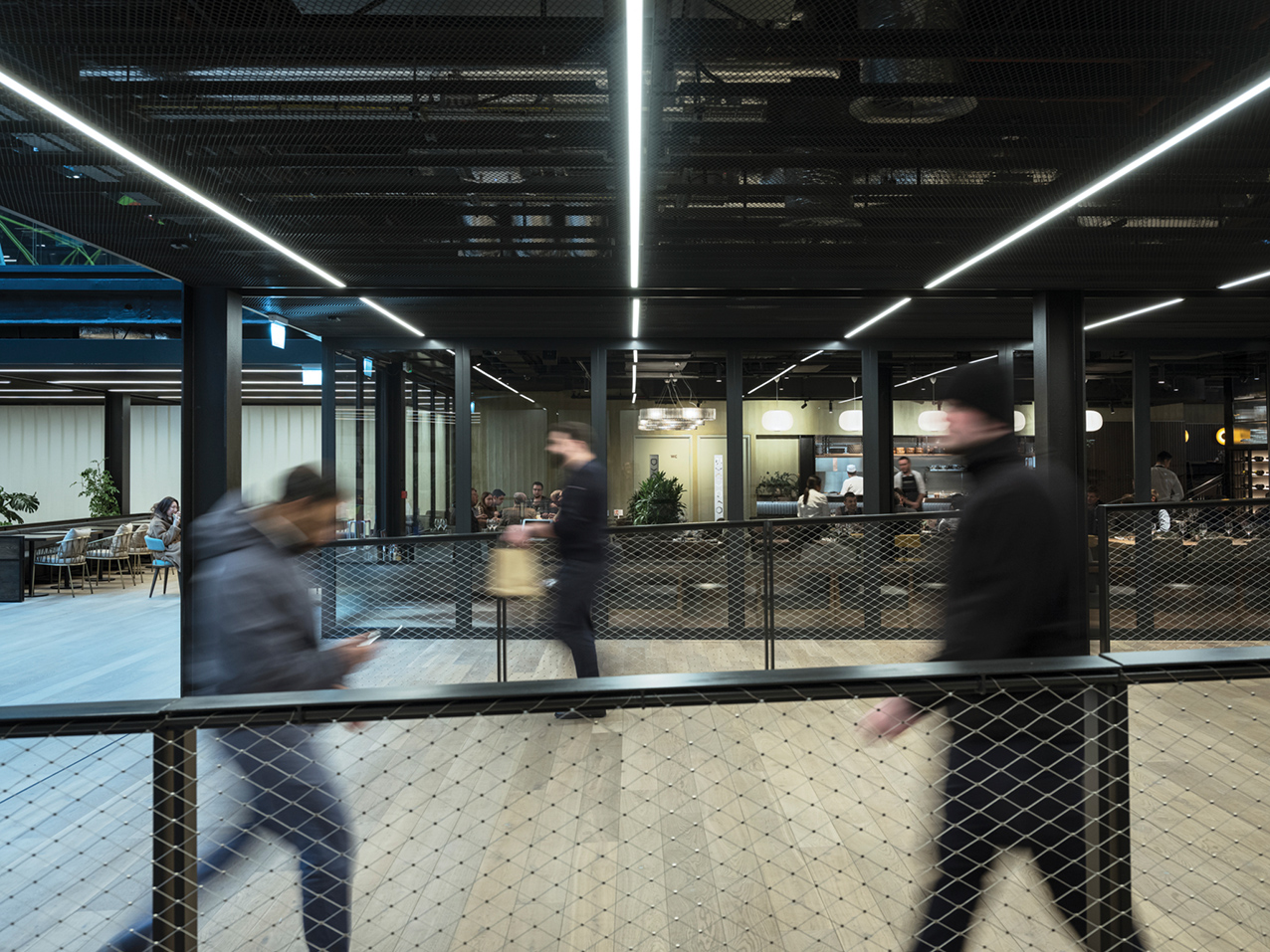
The refurbishment has changed the nature of the working space
Once the project was finished, the team were able to take a step back to assess the impact of reusing plant and systems. While plant reuse requires additional input from the consultants, ultimately, it is the landlord who carries the risk for service provision to the tenant. In this instance, Beaven says the risk was something British Land was prepared to take on because of the benefits to be had from retaining the systems. The building is managed and operated for British Land by Broadgate Estates. ‘Because it’s not brand new, we expect it will require more maintenance on a day-to-day basis,’ says Beaven.
Although reusing the plant means the consultants have to do much more work than they would if they simply specified a chiller from new, Beaven expects plant reuse to be something Arup will get more involved with in the future: ‘It’s not easy, but until the circular economy is running and we have a market to provide refurbished bits of kit, we have to make the best use of what we have.’
Project team
Client: Joint venture between British Land and GIC
MEP consultant: Arup
Acoustic and fire, façade and sustainability consultant: Arup
Architect: Allford Hall Monaghan Morris
Structural engineer: Arup
Quantity surveyor: Equals