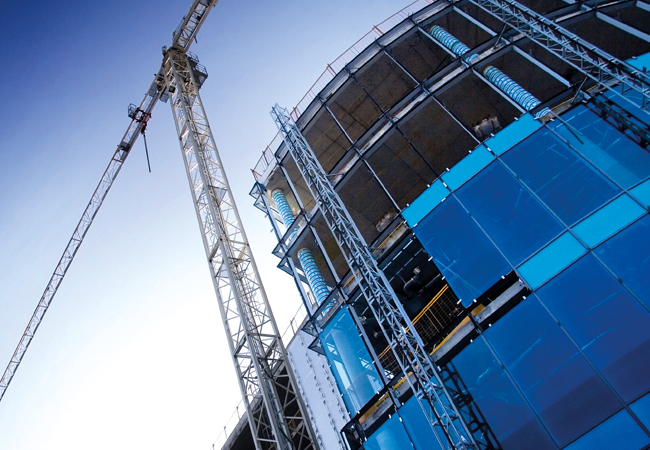
The recent updates to the Building Regulations for England, together with the associated Approved Documents (ADs), are referred to as ‘interim’, and intended to raise standards in the design and construction of buildings in preparation for the Future Buildings Standard and Future Homes Standard, which are due in 2025 and will set higher targets. As outlined in last month’s CPD, there is concurrent activity across the four nations of the UK to develop the Building Regulations (and supporting documentation), aiming towards a net zero future.
This CPD article will focus on some of the changes in the recently updated ADs that particularly affect the provision of heating, cooling, and ventilation for non-domestic buildings.
Overall, the intent in updating the Building Regulations is to drive the construction and property sectors towards delivering lower-carbon, energy-efficient buildings that employ ‘decarbonised’ energy sources. Applied since 15 June 2022, the amended ADs are AD L Conservation of energy and AD F Ventilation, which are both spilt into volume 1: Dwellings, and volume 2: Buildings other than dwellings. A new addition is AD O Overheating, which covers the overheating mitigation requirements in new residential buildings.
The previous ADs made use of complementary ‘compliance guides’ to provide detail of the provisions to meet requirements – the revised ADs include that level of detail without reference to a supplementary guide.
The new ADs also include a clearer indication of the specific regulation that is being addressed by the guidance, with bold notation providing the relevant regulation reference at the top of each page.
ADL2 Buildings other than dwellings sets out measures that will satisfy the energy performance as required by Part 6 of Building Regulations 2010. As with the previous edition, this is evidenced by meeting a target performance created from a notional building that is the same size and shape as the actual building, as specified by the UK’s National Calculation Method for Non Domestic Buildings.1 The energy performance of the notional building establishes two targets. To comply, a proposed building must meet both annual targets – the target emission rate (TER) in kg CO2.m-2 per annum that, overall, is 27% lower than the previous requirement, and the newly introduced target primary energy rate (TPER) in kWhPE.m-2 per annum (as discussed in last month’s CPD). ADL 2021 requires that buildings must be nearly zero-energy, which would be evidenced by the calculated building emission rate (BER) being no greater than the TER.
Software such as Simplified Building Energy Model2 (SBEM) is used to compare the performance of the actual building against the targets set by the notional building, with calculations undertaken for both the design and as-built stages.
The regulations include an uplift in requirements for fabric performance including lower U-values for fabric elements and reduced air permeability, both of which must be addressed at the design stage. Minimum performance standards for the main fabric elements – including walls, roof elements, floors and windows, as shown in Table 1 – have been reduced by around a quarter compared with the previous requirements. The targets set by the notional building for a project will depend on the size and use of the building, and the systems installed, which will combine to deliver the TER for a building that has improved energy performance.
The fabric minimum standards are intended as a ‘back stop’, and the TER and TPER will be met by a combination of:
- Fabric energy efficiency
- Efficient building services
- Low- and zero-carbon technologies.
Before construction commences on a new building, an analysis is required of the technical, environmental and economic feasibility of using ‘high-efficiency alternative systems’. Example systems are noted as:
- Decentralised energy supply systems based on energy from renewable sources
- Cogeneration
- District or block heating or cooling, particularly where it is based entirely or partially on energy from renewable sources
- Heat pumps.
The building specification can change during construction, but the completed building must still meet the targets. When construction is complete, the calculations for primary energy and emission rate must include any changes made during construction, as well as using the measured building air permeability.
ADL2 requires that controls for comfort cooling and air conditioning systems should meet BS EN 152323 Energy performance of buildings – impact of building automation, controls and building management class C or above. Class C is a ‘standard building automation and control system (BACS)’ and is essentially environmental zone control for temperature and ventilation. For space heating or air conditioning systems with an effective rated output greater than 180kW, the control system is required to:
- Fully comply with BS EN ISO 164844 Building automation and control systems
- Continuously monitor, log, analyse and allow for adjusting energy use
- Benchmark the building’s energy efficiency and inform the person responsible for the facilities or building management about opportunities for energy-efficiency improvement
- Allow communication with connected fixed building services and other appliances in the building, and be ‘interoperable with fixed building services across different types of proprietary technologies, devices and manufacturers’.
ADL2 notes that a BS EN 15232 Class A-rated-type system would meet these requirements.
For existing buildings, ‘consequential improvements’ are required, in a similar way to earlier regulations, for buildings with a floor area greater than 1,000m2 when a space is extended or a new/extended building service system is installed. This would require coincident energy efficiency improvements to the building where they are technically, functionally and economically feasible. ADL2 section 12 on consequential improvements is rather easier to follow than the appendix in the previous ADL2B. ADL2 Table D1 highlights the acceptable energy-efficiency measures that should ‘usually’ be installed when consequential improvements are required. This includes broadly similar requirements to the previous AD, including upgrading heating systems, cooling systems or air handling systems that are more than 15 years old, by providing new plant or improved controls.
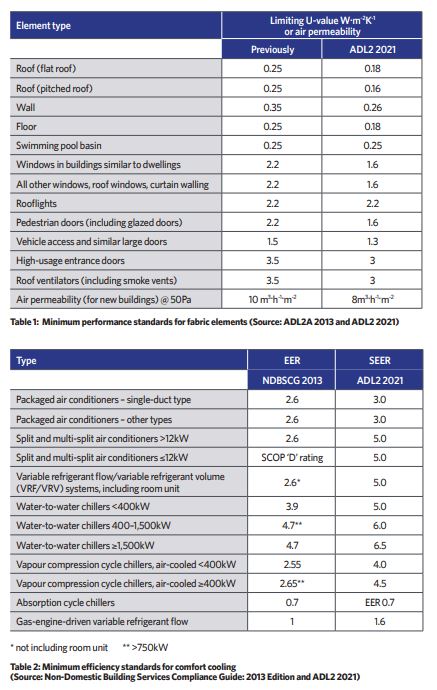
ADL2 also includes some important changes to requirements for building services equipment – specifically, how energy efficiencies are measured and demonstrated. The requirements for comfort cooling equipment must now explicitly meet minimum seasonal energy efficiency ratio (SEER) requirements – the previous requirement was in terms of the minimum full-load energy-efficiency ratio (EER), as shown in Table 2. The SEER was previously only employed in the determination of the building emission rate (in SBEM or similar).
BS EN 148255 is the referenced testing standard for determining SEER and SCOP (seasonal coefficient of performance). However, the requirements of ADL2 for variable refrigerant volume/variable refrigerant flow (VRF/VRV) systems require that the SEER should include the full system, which includes indoor units. Such calculations must include indoor and outdoor conditions, the power for controls, and the power used by the indoor units – this is not covered explicitly by BS EN 14825. This requirement produces a value that is akin to the SSEER (seasonal system energy-efficiency ratio) as employed by the National Calculation Method.1 A potential value of a SEER to check compliance with ADL2 for such systems could be evaluated by employing detailed manufacturer’s data – including appropriate power consumption for internal components – in the SEER equation from ADL2
SEER = a(EER100%) + b(EER75%) + c(EER50%) + d(EER25%)
Where EERX is the EER measured at the load conditions of 100%, 75%, 50% and 25% at the operating conditions detailed for that particular part-load energy-efficiency ratio, and a, b, c and d are cooling load factors (as provided in ADL2 for office accommodation). (The notional building in the NCM applies a cooling SSEER of 4.4.)
For new buildings with a floor area over 1,000m2, there is now a requirement that the building owner should be handed a forecast of the actual energy use of the building that includes all metered energy uses (integrating unregulated loads such as appliances), in kWh per year, broken down by fuel type. ADL2 suggests several methods that may be used to produce these forecasts, including the recently published CIBSE TM54 Evaluating operational energy use at the design stage. In a useful reminder, it is noted that the output of SBEM and other compliance tools is not suitable for direct use to provide energy forecasting estimates. For new buildings with a BACS, information about the energy performance of the building automation and control systems should be included in the handover manual.
In existing buildings, when a new or replacement system is installed – such as a heating system, including heating appliance, pipework and emitters – or work on an system fundamentally alters the energy performance or system CO2 emissions, the energy performance of the resulting system should be assessed and, together with appropriate guidance, the assessment output should be handed to the owner.
The emphasis in the updated ADF Ventilation is to deliver high standards for indoor air quality to support occupant health and wellbeing. There has been a complete overhaul of the tables, which provide a useful quick reference to relevant regulations and guidance that will assist in the determination of appropriate methods of ventilation. The guidance in ADF2 mainly concentrates on offices, where the general outdoor air supply rate remains at 10L.s-1 per person or 1L.s-1 per m2 floor area – whichever is higher. The focus on air quality has meant that the section on minimising ingress of external pollution has moved from an appendix in the previous ADF to a whole section in the new ADF2 2021. This includes a new table of external pollutant limit values, including carbon monoxide (CO1), sulphur dioxide (SO2), nitrogen dioxide (NO2), benzene (C6H6), lead (Pb) and particulate matter (PM), that, if any are exceeded, indicates that there may be a need for the ventilation system to be specifically designed so as to minimise the intake of external air pollutants.
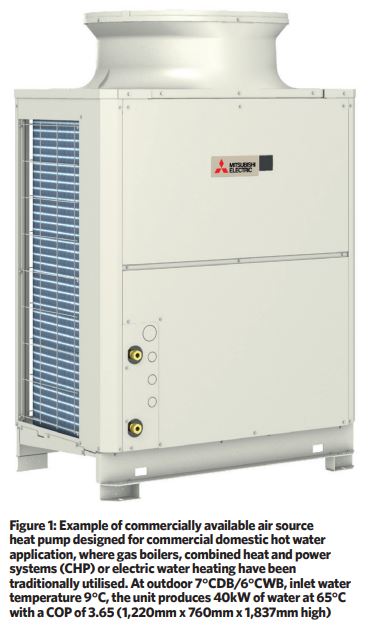
Indoor air quality (IAQ) monitoring is required by ADF2, by measuring the CO2 level as a proxy for the IAQ, which is informed by a new appendix that provides basic information on CO2 monitoring. This advises against ‘snapshot’ readings, as these can be misleading, and advises that continuous monitoring be used. It is suggested that to determine if a space is poorly ventilated, records should be maintained of CO2 levels, number of occupants, and type of ventilation in use at the time and the date of the reading. ADF2 notes that an average CO2 concentration of 1,500ppm over the occupied period is an indicator of poor ventilation, and action should be taken to improve the situation if readings are consistently high.
ADF2 notes that ventilation intakes should always be away from direct impact of the sources of location, and that where buildings are next to busy roads ‘mechanical ventilation may be the most practical way of achieving this requirement’.
In existing buildings, any work carried out must not result in any degradation of the ventilation standards in the building. However, when that building work includes the ventilation system, it must meet the relevant parts of ADF2. It is noted that if work is carried out that increases the energy efficiency of a building, airtightness may be increased and so any useful ventilation that was lost should be replaced in order to maintain a healthy indoor environment.
Decarbonising the built environment will lead to major changes in the choice of equipment for all buildings. Heat pump technology has advanced significantly in the past five years, resulting in systems that are able to meet the heating, cooling and hot water demands of non-dwellings, as in the example shown in Figure 1. Heat pump technology is also being applied within or alongside other building services systems to enhance energy efficiency. For example, heat pump VRF/VRV systems can provide energy-efficient cooling and heating for commercial buildings that use renewable sources, and district energy networks that, increasingly, employ ambient loops operating at low temperatures. Many of the new requirements can be met with technology available today. However, such applications require holistic thinking about design and operation, not only from designers, but also from building managers and the building occupants. This provides an opportunity to adapt to new and better ways of heating, cooling and managing buildings to prepare for a net zero future.
© Tim Dwyer, 2022.