
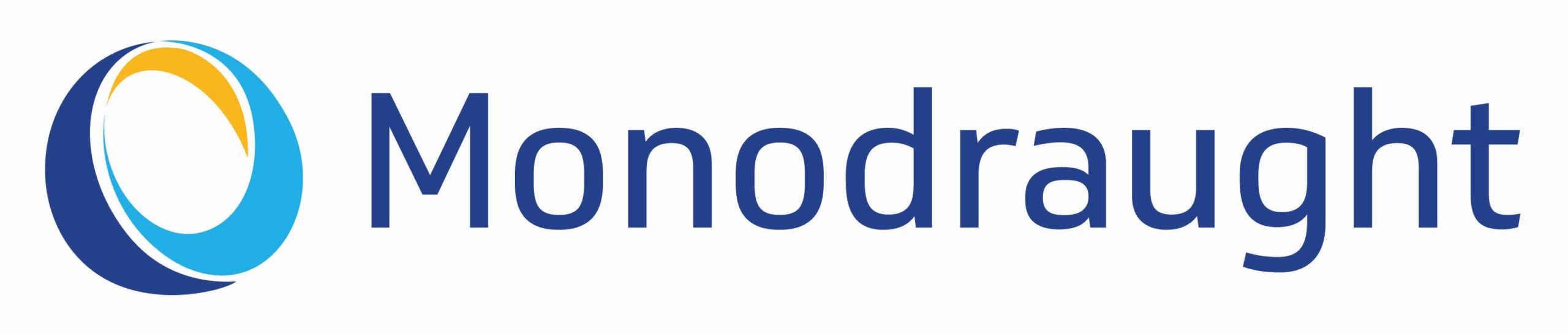
Reliable methods are essential to assess the realistic operational energy performance of new homes, particularly when they include innovative applications of building services systems. By drawing on a recently reported study, this CPD illustrates the benefits of a properly matched energy system and how the misinterpretation of output from current regulatory tools can dissuade building purchasers and users from moving towards systems that can otherwise help move towards net zero homes.
Beyond passive measures, such as improving the thermal performance of the building envelope, the England Building Regulations AD Part L 20211 enhanced the requirements for mechanical components that contribute significantly to primary energy use and CO2 emissions.
The demands of Part L 2021
Current England Building Regulations AD Part L1 requires that new homes must, at least, meet three target requirements that are determined using the SAP (as annual figures). These are the target emission rate (TER) (maximum CO2 emission per m2); the target primary energy rate (TPER) (maximum primary energy use, kWhPE.m-2); and the target fabric energy efficiency rate (TFEE) (minimum fabric energy efficiency, kWh.m-2). TFEE relates solely to fabric performance, whereas TER and TPER are additionally impacted by fuel choice.
It can therefore be challenging to satisfy the present regulation (as determined by the UK’s standard assessment procedure2 (SAP)) and achieve carbon reduction with the most advanced condensing conventional gas boilers. (The consultation has recently closed on the UK government’s draft home energy model (HEM), which will provide a more flexible steady-state calculation methodology designed to assess whether homes meet the Future Homes Standard; in 2025, it will replace the UK’s SAP.
A recent study3 by Monodraught employed dynamic simulation modelling (DSM) for two example new-build, high-specification, four-bedroom homes to assess the energy and CO2 performance for a novel ‘energy module’ package (using commercially available products) compared with a ‘conventional’ system. The conventional (baseline) system comprised a high-efficiency condensing gas boiler, hot-water cylinder and continuous operation extract fans.
The factory-tested packaged ‘energy module’ included an air source heat pump (ASHP), mechanical ventilation with heat recovery (MVHR), and a hot-water thermal battery, all as discussed in the panel ‘Packaged “energy module”’). The two services variants for each of the two homes – detached house type A (Figure 1) and semi-detached house type B (Figure 2) – were also evaluated using the UK government’s SAP calculations.
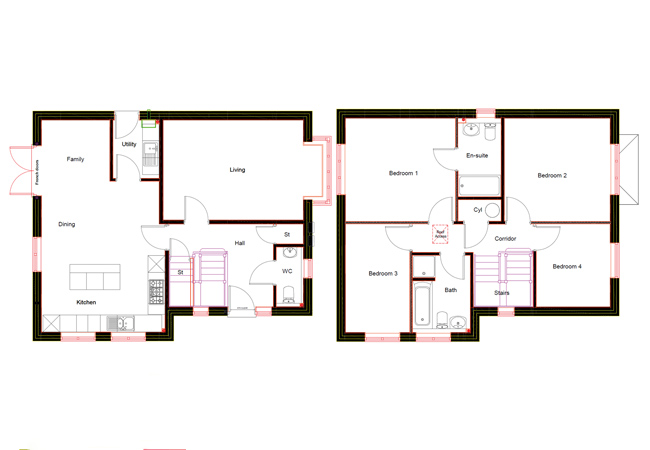
Figure 1: Detached house type A floor plans (ground floor, first floor) – image courtesy of Woodall Homes
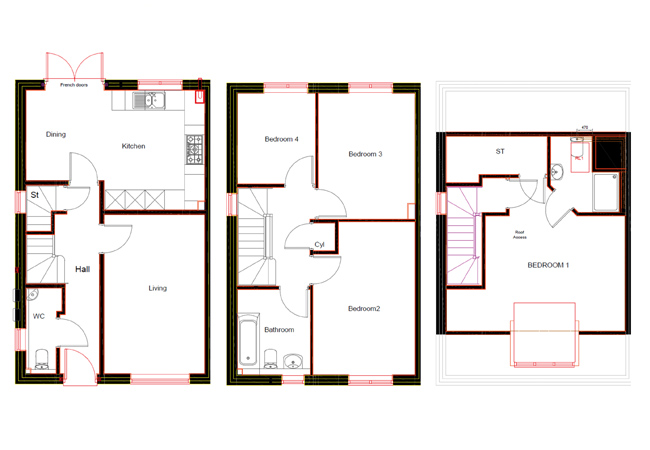
Figure 2: Semi-detached house type B floor plans (ground floor, first floor, mansard) – image courtesy of Woodall Homes
The fabric U values in the homes were at least as good as – and most improved upon – Part L limit values.
In the baseline case, outdoor ventilation air is drawn through ventilation slots incorporated in the windows of bedrooms and living rooms. The bathrooms, the utility room and kitchen are fitted with decentralised mechanical extract ventilation (dMEV) fans with two-speed control that meet the AD F boost ventilation requirements. The specific fan power (SFP) of extract fans was taken as 0.3 for kitchens and 0.25 for other wet areas. With the ‘energy module’ MVHR, air is supplied to each bedroom and living room, and extracted at bathroom, toilet, utility room and kitchen areas.
Using the guidelines in England Building Regulations AD Part F,4 the required supply and extract ventilation rates were calculated for each space. For house type A, the total ‘high rate’ for extract ventilation exceeds the required minimal supply, so background ventilation was set to 37L.s-1 and the boost rate of 43L.s-1 during the active occupied hours in the kitchen and bathrooms. House type B can always operate with 37L.s-1, which meets both the minimum total ventilation rate for the dwelling and the boost extract rates of the wet areas.
The houses have an airtightness of4.0m3.h-1.m-2@ 50Pa that translates to a total of 10.5L.s-1 and 6.7L.s-1 for house type A and house type B respectively. Although the minimum ventilation is provided by mechanical means, temperatures may be controlled by opening the windows.
Packaged “energy module"
The offsite manufactured and factory-tested ‘energy module’ incorporates an air source heat pump (ASHP) for space heating and DHW production linked with whole-house mechanical ventilation with heat recovery (MVHR).
The ASHP may originate from one of several market-leading manufacturers – the modelling considered a commercially available product with a SCOP of 4.58. The extract air from the MVHR is used to maintain high working efficiency of the heat pump, even during cold weather conditions.
The DHW is provided through a hot water thermal battery using phase change materials (PCM) to achieve a compact module equivalent to 185L water volume at 40°C and 28W standing loss. The hot-water module could potentially be charged by any renewable source, but this study used the ASHP as the main heat source.
The whole-house ventilation is provided by a commercially available MVHR unit with a working SFP of 0.88 (supply and extract) and heat recovery efficiency of 90%.
The modelling of natural ventilation was set so windows were activated whenever room temperatures exceeded 23°C, to avoid overheating, although CIBSE TM595 (assessing overheating risk) and England Building Regulations AD Part O6 (mitigation of overheating) were not part of this study.
Occupancy and equipment gains were distributed over 24 hours according to profiles detailed in CIBSE TM59.5 Internal lighting efficiency was set to 80Lm.W-1 in accordance with AD Part L1 2021,1 and standard lighting levels were applied according to occupancy type. Lighting was simulated to operate based on photosensors whenever the natural light decreased below the desired level within each occupied room, except bathrooms where the lighting is controlled according to a fixed occupancy schedule at the start and end of the day.
The baseline configuration of the houses includes gas-fired condensing boilers with a seasonal coefficient of performance (SCOP) of 93%, or seasonal efficiency of domestic boilers in the UK (SEDBUK) rating of 89.4% for heating and domestic hot water (DHW) employing a 180L hot-water cylinder with a standing loss of 67W at 60°C.
Based on CIBSE Guide G,7 the daily hot-water demand was calculated as 115L per person at 65°C for six occupants, which equates to a modelled 31.15L.h-1 hot-water consumption at 60°C. The baseline DHW power demand was 1.81kW. Adding the standing loss and a 0.93 boiler efficiency, 2.02kW will be needed for hot-water production – an annual demand of 17.67MWh.
The standardised test offered by SAP 10.2 (the current version of the UK government’s standard assessment procedure) provides a relative benchmark for testing compliance with Building Regulations. It considers annual space and water heating costs for a standardised heating regime when assessing the energy performance of dwellings. SAP’s promised successor for 2025, the home energy model (HEM), aims to improve the modelling process in an open software environment, employing ‘wrappers’ (or, in software parlance, ‘objects’) making it adaptable to many more scenarios. A significant change will be the adoption of 30-minute intervals compared with SAP’s monthly analysis, and the flexibility to model individual energy systems under various conditions. The increased granularity promised in HEM will allow more incisive steady-state assessments of energy consumption patterns, to promote more effective energy-saving strategies. However, SAP, and in the promise of its new form, HEM, are not primarily designed to provide a forecast of a home’s energy performance – this requires a more detailed assessment of the thermal performance of the home, systems, and occupation.SAP and HEM
The phase change material (PCM) battery delivers DHW at 40°C without water storage and no risk of legionella to the consumer, and is targeted at an end use of 40°C. The hot-water flowrate was increased to 46.72L.h-1 @ 40°C, which is equivalent to 31.15L.h-1 @ 60 °C. The energy necessary to heat up 46.72L.h-1 mains water from 10°C to 40°C is 1.628kW, slightly lower than the baseline system.
Taking account of storage losses, 0.22kW of power can be potentially saved with the PCM battery, which means a 1.58MWh annual saving in hot-water production with the new technology.
CO2 emission and primary energy factors for electricity were based on the latest figures of the National Calculation Methodology (NCM) guideline , which varies slightly in each month. For natural gas, typical figures were employed of
0.21kgCO2.kWh-1 and 1.126kWhPEPE.kWh-1.
The annual primary energy figures for the studied scenarios are summarised in Figure 3. The DHW energy is the driving factor in the annual energy consumption, comprising 90% of the whole system energy compared with only 4% energy spent for space heating and 6% for fan/pump energy. The heating energy and all other energy categories are relatively small compared with the DHW consumption.

The envelope heat losses are small for homes designed for net zero so, in energy simulation, heat generated by equipment offsets much of the fabric and infiltration heat loss. When swapping the gas boiler with an ASHP the heating energy at house type A and house type B decreased by 91% and 64% respectively.
Changing the location of the homes to Southampton (which has milder weather) did not significantly impact the overall system energy. Although the space-heating demand dropped by 36%, there was just a 1.4% drop in the overall energy consumption in the ‘energy module’ applications, as 91% of energy was attributed to DHW.
The heating and ventilating energy reduction in both house types resulting from applying the ‘energy module’ was 80-82% lower than the baseline case. When including the unchanged equipment and lighting energy requirement, the overall energy saving came to 74% in both house types. In terms of carbon savings calculated for systems and lighting, both house types emitted 82% lower CO2 for the ‘energy module’ system compared with baseline.
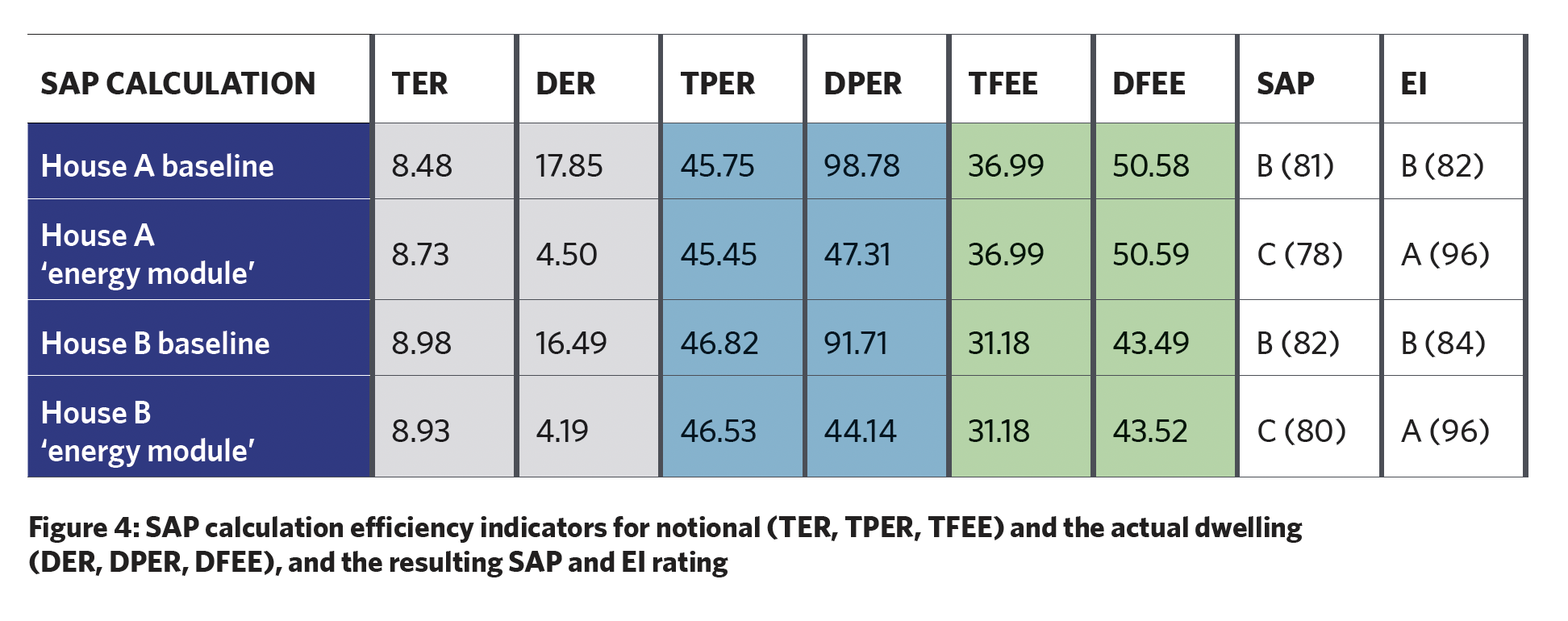
The main indicators of the SAP calculations in Figure 4 show the CO2 emissions and primary energy for the actual dwellings (dwelling emission rate (DER) and dwelling primary energy rate (DPER)) were significantly reduced in case of the ‘energy module’, while the dwelling fabric energy efficiency rate (DFEE) remains the same.
The DPER reduced by 52% and DER CO2 emissions by 75% when applying the ‘energy module’. The SAP environmental impact (EI) rating went from Category B to Category A when the buildings were served by the ‘energy module’.
Despite the significant energy and CO2 performance improvements of the homes that employed an ‘energy module’, it did not improve the SAP rating, as that is contingent on the notional running costs of a home. The dynamic model showed that the system energy for the ‘energy module’ is a third of the baseline case.
However, the SAP fixed cost for electricity is 4.53 times higher than gas, so an ASHP system is unable to demonstrate an improved SAP rating. (The current UK residential price cap sets electricity at 3.85-times the cost of gas.) As the SAP rating is a key indicator for property purchasers and landlords, it will remain challenging to encourage the investment needed in ‘alternative’ technologies if future homes decisions are made on a regulation compliance rating dominated by nominal energy prices, rather than primary energy and the increasingly pressing considerations of the environment.
References:
- England Building Regulations Conservation of fuel and power Approved Document Part L Volume 1: Dwellings, 2021 edition incorporating 2023 amendments, bit.ly/CJMay24CPD1 – accessed 2 April 2024.
- bit.ly/CJMay24CPD2 – accessed 2 April 2024.
- Bakó-Biró, Z and Hopper, N, HomeZero performance in DSM and SAP modelling for domestic properties,
- Monodraught 2024.
- England Building Regulations Ventilation Approved Document F Volume 1 applies to dwellings, 2021, bit.ly/CJMay24CPD1 – accessed 2 April 2024.
- CIBSE TM59 Design methodology for the assessment of overheating risk in homes, CIBSE 2017.
- England Building Regulations Overheating Approved Document O, 2022, bit.ly/CJMay24CPD1 – accessed 2 April 2024.
- CIBSE Guide G Public health and plumbing engineering, CIBSE 2014. bit.ly/CJMay24CPD3 – accessed 2 April 2024.