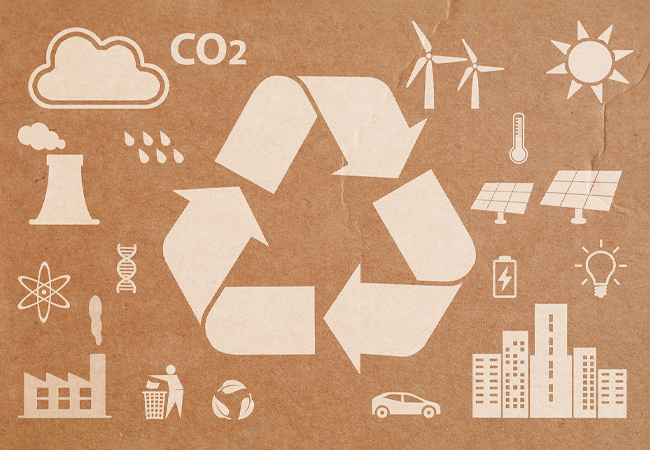
Credit: iStock – lukbar
A circular economy presents engineers with an opportunity to improve system performance, decrease whole-life cost and reduce the environmental impact of their buildings.
Following the recent recommendations by the Committee on Climate Change for net zero greenhouse gas emission for the UK by 2050, CIBSE has set out its own climate action plan, detailing activities that work collectively towards reducing carbon emissions and preparing for the future impacts of climate change. See CIBSE Climate Action Plan
What is a circular economy?
The traditional resource consumption model is linear, where resources are extracted from natural systems to make products. These are often thrown away once they have served their purpose, without the full value of their component materials being realised.
A circular economy aims to move away from this, by designing out waste, maximising value, improving maintenance and returning materials into the cycle at the end of their lives. A transition to a circular economy aims to decouple business growth from resource consumption, providing the coherent strategy cities, organisations and projects need to achieve both economic and environmental goals (Figure 1).
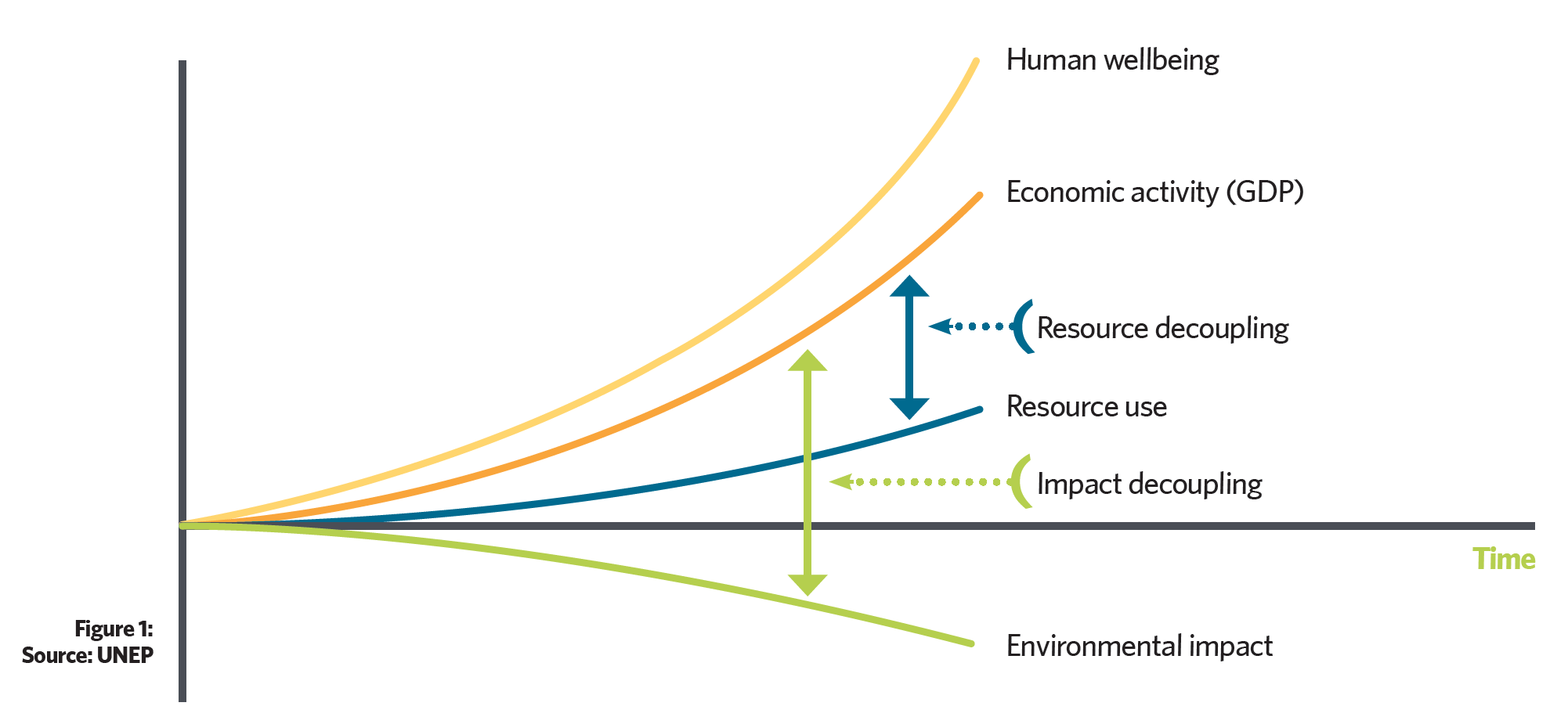
It should be noted, therefore, that ‘circular economy ‘is not simply a way of rephrasing ‘sustainable development’. It is a shift in the way we do business, which can offer direct value to adopters through improved system operation and maintenance, novel financial opportunities and performance-driven contracts.
The circular economy has been gaining momentum across the built environment, a sector responsible for huge amounts of waste: physical waste through construction and demolition, energy waste through system operation, and space waste through inefficient use (Figure 2).
In addition to the contribution of buildings to climate change through carbon emissions, CIBSE TM56 describes how the production of building services components also results in the direct destruction of ecosystems, the release of toxic by-products, and increasing water stress through process demands.
Arup has been working with colleagues around the world, exploring the ideas of a circular economy for more than five years. These efforts have intensified since 2016, when Arup became the global knowledge partner for the built environment of the Ellen MacArthur Foundation, a leading proponent of circular economy thinking.
Through the partnership, Arup and the foundation have been considering how circular economy principles might operate in the particular circumstances of the built environment.
Circular design principles
More recently, Arup has been working with UCL Estates and the Bartlett School of Planning to create circular design principles for MEP systems, specifically those of Marshgate 1, UCL’s new 35,000m2 building in Stratford, East London.
Supported by Schneider Electric, and with input from Aecom lifecycle cost consultants, the work sought to use circular principles to address the key challenges faced by UCL relating to its MEP systems.
These challenges included the need to avoid the early obsolescence of installations, by future-proofing designs, addressing the performance gap that often arises between design and installation, and overcoming the barrier of upfront cost being a greater driver for design decisions than the total cost of a system over its life.
Another aspiration of UCL was to incorporate sustainability measures that would go ‘beyond Breeam’, while addressing the key operational challenges. The project hoped to indicate the cost and whole-life carbon benefits of applying circular principles.
Technology now enables key circular economy principles, such as the sharing of information, tracking material flows, real-time usage data and straightforward collaboration. In short, digital technology has unlocked the potential of the circular economy in the built environment.
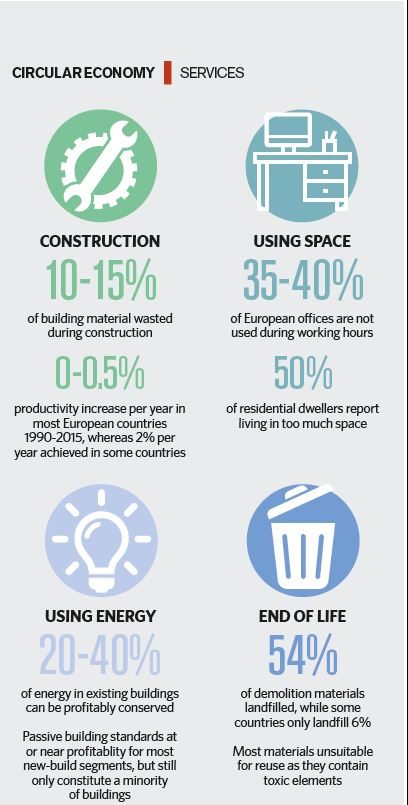
The circular economy building blocks and levers defined by the Ellen MacArthur Foundation were used to create five scenarios, each focusing on a different aspect, tailored to achieve the aims set out by UCL (see panel, ‘Circular framework’).
There are several key considerations to be made for each scenario, along with opportunities and current barriers to implementation. In the case of the UCL Marshgate building, there were reductions in whole-life cost and carbon across the board, demonstrating the business case for a building services circular economy.
Each project is unique and shall lend itself to a different combination of approaches. Appropriate consideration of the maintenance strategy must be included during the design stages to support whichever approach is taken.
Application of these principles shows that design and operations engineers should look together at the circular economy from beyond a component recycling and reuse level. It is equally vital to design out waste to ensure the value of materials are maximised throughout their lives.
The application of these scenarios enables the sector to systematically offer more value to building operators by reducing costs and improving system performance, while improving environmental outcomes.
The outcomes of this research form the basis of a CIBSE technical guidance document, set for publication at the end of the summer, setting out each scenario, key considerations, opportunities, barriers and key enablers.
Circular Framework
These five approaches provide a framework that can be applied to any construction, refurbishment or strategic maintenance project to incorporate circular economy principles.
The universal scenario is a response to architect Stewart Brand’s theory that simple, flexible buildings get better with time, while complicated, inflexible buildings get worse. A universal building can accommodate several functions, allowing the building to be upgraded or change function in response to changing owner and occupant demands. Flexible buildings maintain their value for longer, or depreciate slower, than inflexible buildings, keeping the materials in the building at their highest possible value for as long as possible.
The joint venture approach aims to align the drivers of each stakeholder within a project by placing them under a single financial umbrella, where payment is dependent on system performance. The result is that designers become more invested in the building’s operation, while greater input is taken from facilities managers and potential occupants during design, reducing the risk of a performance gap.
The concept of passive buildings has been around for a long time. This approach minimises the use of active systems, replacing them with passive processes, such as natural ventilation and daylighting. Resource consumption is therefore designed out.
The aim of the recover scenario is to minimise the reliance of the building on external resource flows, particularly water and energy. Capturing the value of waste flows, such as low-grade heat and wastewater, are also prioritised. The consumption of virgin resources is thus minimised.
The pre-loved scenario is about how to incorporate secondhand equipment into buildings to create a market demand model for pre-used equipment, adding value to what is currently a waste flow.