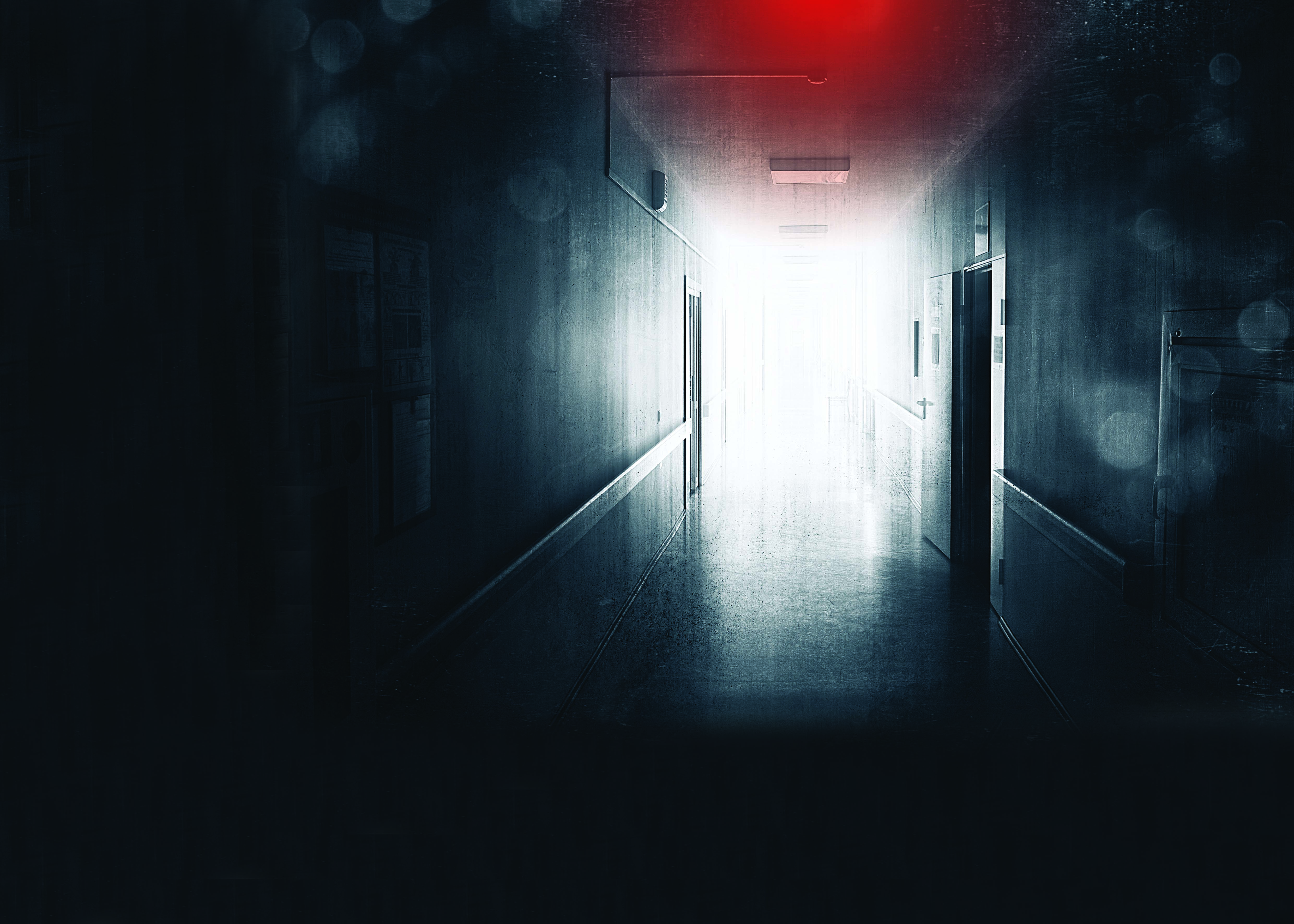
Credit AMVISIUM / SHUTTERSTOCK
Making a case
This article discusses current state-of-the-art ventilation solutions for overheated corridors. Such systems have a relatively low added installed cost, and the running cost is limited to the power for the fan.
The limitation of such systems is that they cannot cool the incoming air, so corridor temperatures will fluctuate with outside ambient temperature. Running the systems at night can pre-cool the corridor structure, limiting day time peaks, but corridor temperatures will still generally match or slightly exceed outside temperatures.
In expensive, high-quality developments this may be considered unacceptable, and then designers have no choice but to air condition the corridors – a solution which provides much better control of conditions in the corridors, but at a significant ongoing cost in terms of maintenance and energy use.
Intermediate solutions such as Colt’s Coolshaft enhances ventilation system performance by pre-cooling the incoming air but without the high running costs of full air conditioning. The system runs much of the year in normal free cooling ventilation mode, with adiabatic cooling brought on line when internal temperatures exceed a set point. This cannot match the close temperature control of air conditioning but, for all but the most exclusive developments, is one solution.
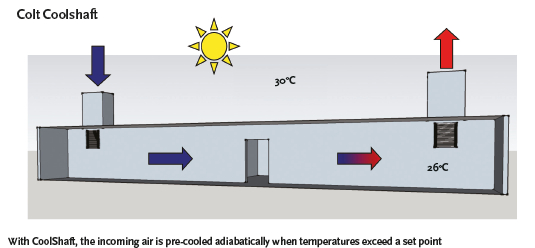
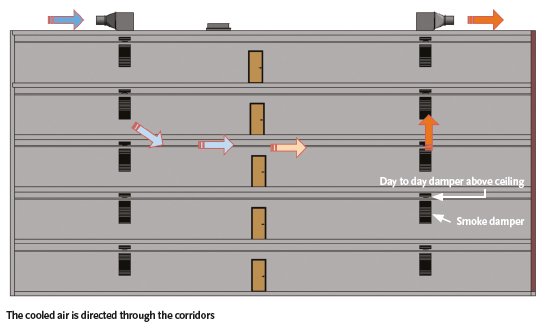
Good ideas can have unwanted consequences.
There has been a continuing push for improved energy efficiency in buildings, driven largely by government targets for reductions in CO2 emissions. Approved Document L to the Building Regulations has been regularly tightening energy use targets, resulting in buildings that are better insulated, better sealed and have more efficient services. All this is very laudable but it can have unintended consequences.
ASHRAE has taken up concerns that the drive for energy efficiency has reduced the focus on IAQ in buildings, and that building users may be suffering as a result. After all, buildings are primarily there to provide a comfortable and healthy environment for their occupiers1.
One particular example of this problem is conditions in apartment block corridors.
If we look back 10, 15 or 20 years, U values were high, air leakage was high and corridors generally extended to outside walls and had windows, so if there were any environmental concerns they were largely that the corridors might be too cold in winter. Nowadays we have well-sealed, well-insulated corridors and architectural trends have changed so that corridors are often landlocked. The concern over cold winter conditions has largely evaporated.
But there has also been another change. Apartments, which were generally heated using individual electrical appliances, now often benefit from a centralised source of heat, engineered to provide much greater energy efficiency. This heat source circulates hot water around the building, using the ceiling voids above corridors as the main horizontal distribution route. Of course the pipework is well insulated, but the heat leaking from these pipes 24/7 leads to overheating of such well-insulated and sealed corridors.
This problem was first recognised around five years ago and it is now receiving more attention as designers search for effective solutions with low energy and low maintenance requirements. Occupants who have paid large sums of money for rental or purchase expect reasonably comfortable conditions in corridors, despite them only being transit spaces, but will not want to pay high service charges for the privilege.
Fortunately in the UK we have regulations requiring ventilation of stairs and some lobbies and corridors, albeit for smoke control rather than day-to-day comfort ventilation, and it is not a huge step to adapt these systems to solve the overheating problem.
Early attempts at dual-purpose systems could be crude and experimental, with no-one able to quantify the problem confidently and hence no real design specification available but, as experience has developed, so suppliers have been able to refine their systems.
These systems tend to split into two broad categories, namely single shaft systems used where lobbies and/or corridors are short, and twin shaft systems used where the smoke control system has been designed as compensation for extended escape travel distances. A hybrid is also possible, where there are two stairs with separate single shaft systems for smoke control that can be used together for day-to-day ventilation by holding separating fire doors open with maglocks to allow through-flow.
With single shaft systems, the two initial decisions that drive system efficiency are the source of replacement air and the shaft location. The source of inlet air is easy – the stair always has a high level ventilator, so this (if suitably weathered) can allow air in and a small fire-rated motorised damper can be used to transfer the air into each lobby. The shaft location needs a little more thought. For smoke control purposes, regulations allow the shaft to be located anywhere. However, for day-to-day ventilation, it really needs to be located as far as possible from the air inlet for maximum effectiveness.
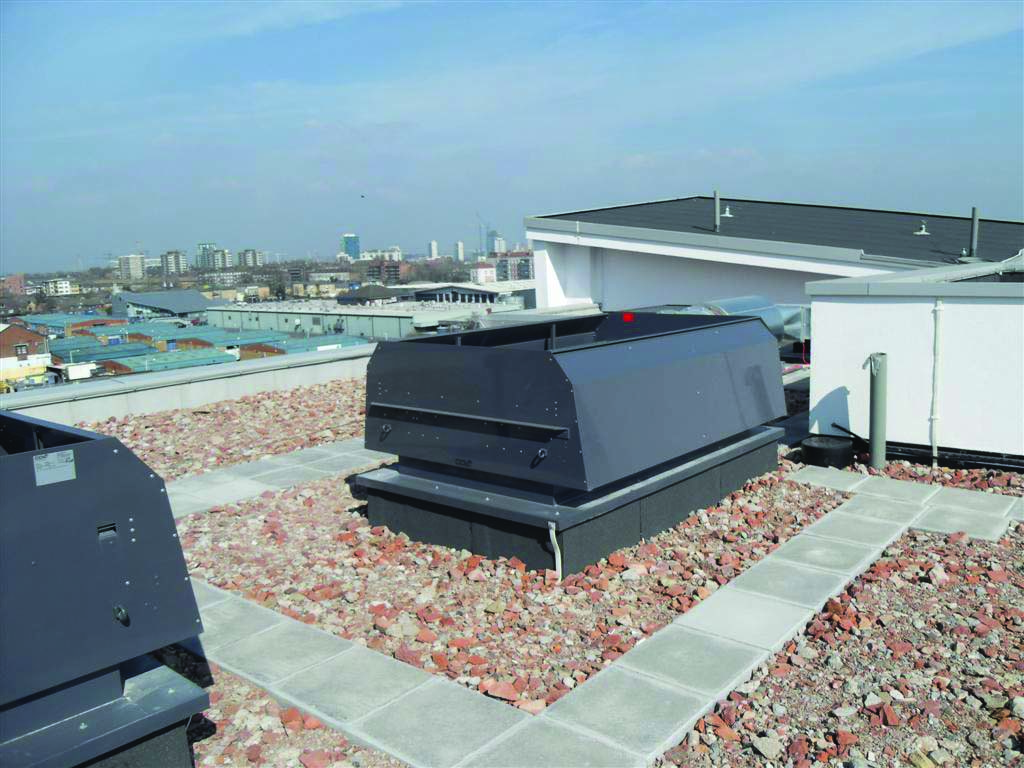
Automatic opening ventilation for supply air at the head of the staircase
With twin shaft systems, the shafts are normally as far apart as possible for smoke control purposes, so no special thought has to be given to their location.
The other important consideration relating to the shafts themselves is how to transfer air to or from them in day-to-day mode. Various vent types are used for air and smoke transfer in smoke control mode: motorised fire doors, flap ventilators or dampers and grilles. All of these are large and not really suitable for balancing the much smaller air flows needed at each floor for day-to-day ventilation.
In addition some can present other risks – such as finger trapping – when regularly opened. Various solutions are available, depending on the budget and the required sophistication of control.
Moving up to the roof, whether the shafts provide natural or mechanical ventilation in smoke control mode, a fan will be needed for day-to-day ventilation. This may be a separate, low power, low noise fan, or an adaptation of the main fans with inverter control and attenuation, as appropriate. If a separate fan is used, there needs to be suitable control to avoid bypassing between fans.
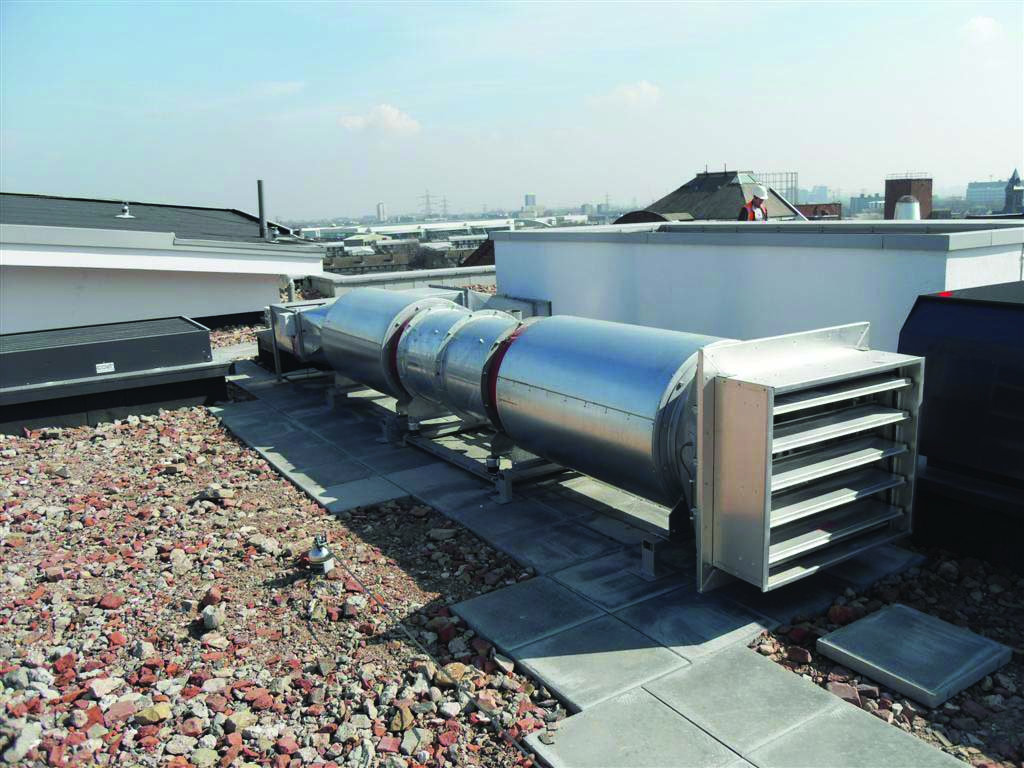
Attenuated extract fans
For all these issues, the system supplier should be able to provide advice, guidance and proven standard solutions. One thing the supplier can’t provide, though, is the design heat load, which the system needs to deal with. In principle this should be relatively easy to estimate, based upon flow and return water temperatures, pipe sizes and insulation, plus – of course – an allowance for lighting and any other heat sources within the corridor, but it’s amazing how rarely this is stated by the designer.
Overheating in corridors is an unwanted consequence of tougher regulations, but at least it is an issue that is now understood and has a practical solution.
Paul Compton CENG MCIBSE is technical director at Colt International
References
1 Indoor Air Quality Guide: Best Practices for Design, Construction and Commissioning, ASHRAE