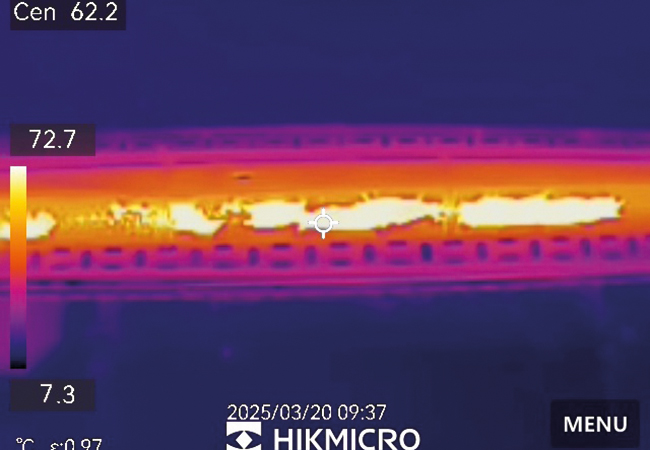
Non-UV-resistant elastomeric foam insulation will quickly degrade and lose thermal performance. The lack of thermal performance doesn’t seem to stop birds from taking an interest - as evidence of droppings around the refrigeration line suggests
Thermal insulation of pipework could and should be playing a key role in our national decarbonisation plans. However, thermal insulation is often no more than an afterthought. It should be considered at all stages of the project life-cycle, from design and specification to installation, inspection and aftercare.
Even if we can put in place good specification and installation practices, there is still a huge legacy of poorly insulated pipework.
The examples of poor insulation and specification in this article are taken from recent air conditioning inspections and are typical of issues that are having a profound impact on system efficiency.
The reward for addressing poor insulation is huge – improvement to insulation in the industrial sector alone can save 20,934MWh of energy, equivalent to the consumption of 863,000 households or 1.7 million cars1.
The problem is common to all sectors. Poorly insulated plantrooms and pipework systems are the forgotten energy thieves operating in plain sight in our schools, hospitals, offices, and pretty much every other building in which we live, work and play.
So when should pipework be insulated in the plantroom? The easy answer is when there is ‘any application where the heat transfer is not considered useful’. Heat transfer can only be considered useful in a small minority of applications.
An example of useful heat loss would be on pipework leading from the compressor to the condenser on direct expansion refrigeration lines, where lowering the temperature naturally increases the efficiency of the system.
We should also be asking ‘when should we protect the insulation?’ For refrigeration and domestic projects, upgrading a standard flexible foam insulant to a clearly identifiable UV-resistant one should be the minimum requirement for any externally located refrigerant pipework.
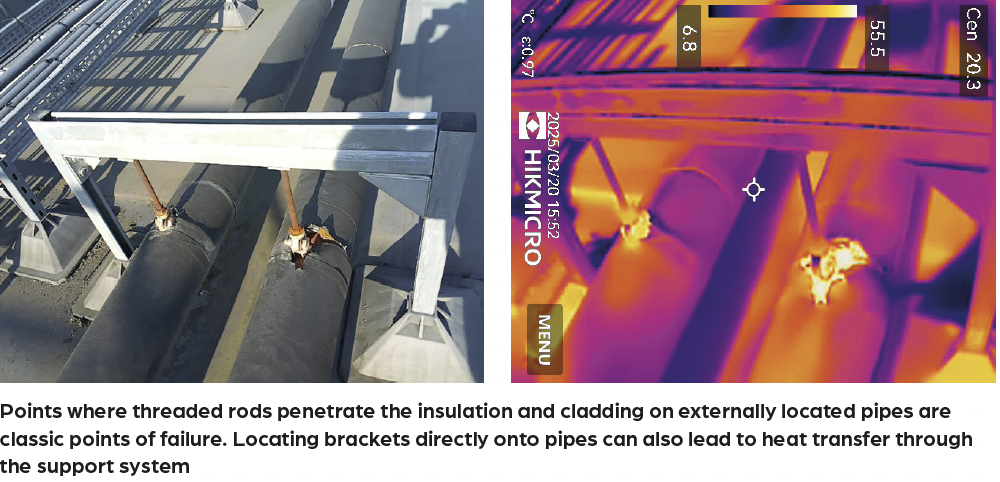
What are the relevant standards?
The key standard for the specification of thermal insulation is BS 5422:2023. This contains multiple tables for the minimum thickness of insulation required in a variety of applications.
It is important that the consultant specifies a particular table rather than a general ‘do it as per BS 5422’ approach. There are multiple tables for similar applications – some will give the client a better operational carbon-reduction result than others, but contractors will invariably assume ‘lowest-cost scenario’ unless instructed otherwise.
There is also a code of practice for the application of thermal insulation and cladding (BS 5970:2012). This standard is under review, with a new edition hopefully out for public consultation in early 2026.
Bearing in mind the huge legacy of poorly insulated pipework in the industrial sector, we should also welcome the new thermal insulation energy performance standard BS EN 17956:2024. This allows a client to stipulate a minimum energy rating for thermal insulation in the same way that we may stipulate an energy rating for buildings and consumer items.
It should be highlighted that heat network projects typically work to higher specification. With the Heat Network Technical Assurance Scheme due in 2025/26, we should expect thermal insulation of secondary/communal heating systems to be a key consideration for heat network efficiencies.
Good installation practice
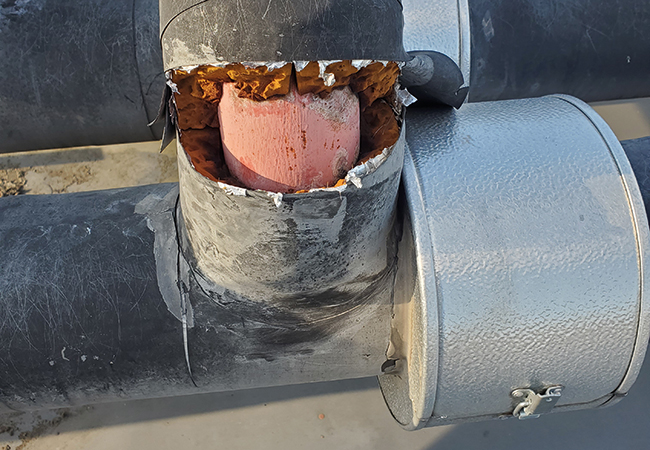
Failed phenolic insulation with a probable PIR outer wrap. Part of a rooftop low-temperature hot water system serving multiple air handling units at a leisure centre that was completed in 2014
The application of ‘flexible pipe lagging’ on small-bore pipework is not regarded as a skilled trade and is generally considered to be part of the domestic plumbing or commercial refrigeration package. However, the application of thermal insulation and cladding in all other scenarios is a skilled trade with a clearly defined route to competence. All thermal insulators should be able to evidence individual competence with a TICA CSCS Thermal Insulator Skill Card.
Thermal insulation contractors should be able to evidence their organisational capability to carry out this specialist trade. TICA membership is often specified as a minimum criterion for thermal insulation organisational capability, but in many cases it is not. Specifiers have a role to play in ensuring the competence of specialist trade associations on their projects and should not be afraid to challenge organisations to evidence their capabilities.
Pipe insulation is part of a system
Thermal insulation sections are just part of the system. Pipe equipment, such as valves and flanges, should also be insulated. One part of the system that often gets overlooked is the pipe-support bracket. Wherever possible, an insulated pipe-support insert should be used. This has a dual purpose; to continue the integrity of the insulation and to maintain the load-bearing integrity of the fixing point.
Where cladding is required, care should be taken to ensure the cladding runs straight through the pipe-support bracket. Points where threaded rods penetrate the insulation and cladding on externally located pipes are classic points of failure. Getting these details right matters, but it does involve early engagement between the mechanical and thermal insulation contractors.
As the name suggests, UV-resistant thermal insulation offers greater resistance to UV damage – but this does not make the insulation UV-proof. Inspection cycles will still need to be in place, even if the risk of degradation is far lower.
The standard of insulation is reported with the CIBSE TM44 inspection every five years. However, it is only reported as ‘good or bad’ and there is no further guidance. Where it is suspected that non-UV-resistant flexible foams have been used, an immediate intermediate inspection should be carried out on the externally located insulation.
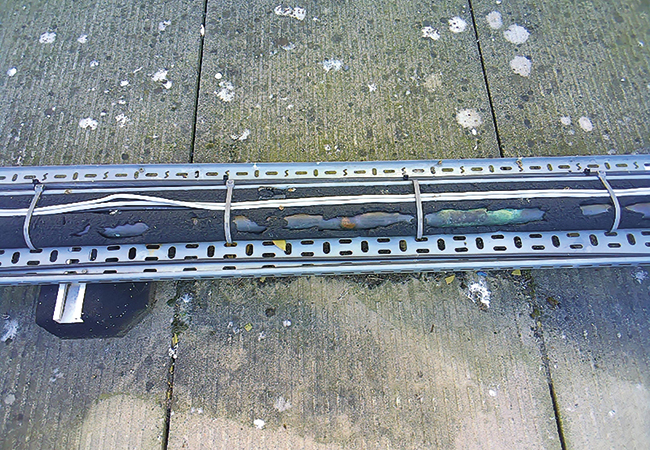
Non-UV-resistant elastomeric foam insulation will quickly degrade and lose thermal performance. The lack of thermal performance doesn’t seem to stop birds from taking an interest - as evidence of droppings around the refrigeration line suggests
The five-year cycle leaves ample opportunity for non-UV-resistant insulation to break down and start losing heat from the pipe. Humid air can then reach the surface of the pipe and condensate, leading to corrosion, ceiling damage and mould growth.
Even insulation protected with a professionally installed external cladding system can be susceptible to damage. Any weak point in the system could lead to water ingress and the potential for corrosion under insulation, so there is always a need for ongoing inspection.
There’s also a lot going on inside a building. Every uninsulated valve or flange is adding to the system heat loss. A general rule of thumb is that the heat loss associated with one valve is broadly equivalent to one metre of uninsulated pipe. Yet valve jackets are often not specified – and when they are, they are often not reapplied after being taken off.
For large manufacturing plants and energy facilities, a full audit of the process pipework system should be carried out with a programme such as the European Industrial Insulation Foundation’s (EiiF’s) Tipcheck. This will highlight the return on investment based on a prescribed thermal insulation energy rating; payback for the necessary work is often weeks or months, rather than years.
The issue of poorly insulated pipework needs to be resolved if we are serious about our national net zero ambitions. A focus on strong specifications, good installation practice and ongoing care will make a huge difference over time to saving energy and money. For existing systems, we will have to get onto our roof spaces and plantrooms and tackle the situation head on. 1
The authors will shortly publish a white paper, How can government incentivise adoption of thermal insulation of pipework as a key carbon-reduction enabler?
A recent CIBSE webinar can be viewed at cibse.org/GrowYourKnowledge
About the authors
- Lawrence Leask is managing director at Kaizen Energy Consultancy and is a CIBSE Low Carbon Energy Assessor – Air Conditioning Inspector with 20 years’ experience surveying HVAC equipment
- Chris Ridge is technical director at the Thermal Insulation Contractors Association
References:
1 Industrial insulation factsheet 2021, European Industrial Insulation Foundation (EiiF)