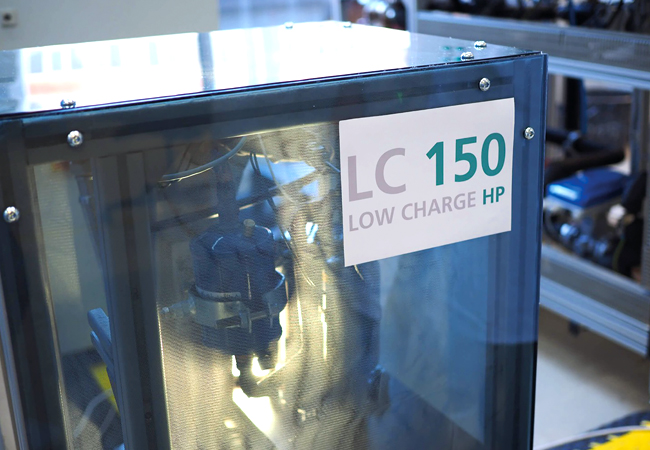
The LC150 heat pump, developed at Fraunhofer ISE, is based on the climate-friendly refrigerant propane
The reduction in fluorinated greenhouse gases (F-gases) used in refrigeration is seen as essential if Europe is to meet its carbon-reduction targets.
In a recent assessment report on the progress of the F-gas Regulation in Britain1, it was concluded that there had been success in achieving the objective to reduce emissions, as well as significant financial benefits.
As explored in this month’s CPD article, this success is mainly the result of the hydrochlorofluorocarbon (HFC) phasedown and the transition from high global warming potential (GWP) HFCs to lower-GWP blends of HFCs and hydrofluoroolefins (HFOs), and non-F-Gas alternatives, such as propane.
CIBSE Journal CPD Module 99, from 2016, noted that propane’s operating pressures and temperatures are well suited to use in air conditioning equipment, including chillers, and the natural refrigerant has a GWP of just 3.
What is global warming potential?
GWP is a measure of how much heat an F-Gas traps in the atmosphere. It compares the amount of heat trapped by a certain mass of refrigerant to the amount of heat trapped by a similar mass of carbon dioxide over a 100-year period.
The latent heat of vaporisation of propane (HC-290) is almost twice that of most common HFC refrigerants, which means a higher cooling/heating effect for the same refrigerant mass flow2 that requires reduced compressor power and, so, higher operational efficiency.
The hydrocarbon propane has good compatibility with materials commonly used in the construction of refrigeration and air conditioning equipment, is commercially available, and relatively inexpensive (at less than 20% of the cost of HFOs2). It can be stored and transported in steel cylinders in the same way as other common refrigerants. However, being flammable – and so classified as an A3 class refrigerant – there are specific rules to observe. Depending on room volume and application type, there are also limits to the mass of propane that may be used.
In a swiftly changing legislative landscape, the limits vary across the world – although, historically, an indoor limit of 150g was, and remains, a common benchmark for a propane charge in single appliances.
The goal of reducing the amount of refrigerant to 15-30g /kW has been exceeded
BS IEC 60335-2-40:2022 ED73 is pending an agreed update, which includes changes that allow higher charge limits for propane of up to 988g in a standard system (with added safety measures) – this is likely to eventually shift the global acceptance of higher propane charges.
Since the CPD article of 2016, there has been a flurry of activity from national and multinational manufacturers to develop propane-based heat pumps for commercial and domestic applications.
The Fraunhofer Institute for Solar Energy Systems (ISE), in Germany, and a consortium of heat pump manufacturers are developing a standardised and refrigerant-reduced propane refrigeration circuit under the ‘low charge 150g’ LC150 project, as a pathway to developing safe and efficient domestic and small commercial propane-charged heat pumps.
Since October 2021, the Fraunhofer ISE project team has been building prototypes for brine heat pumps (systems specifically designed to transfer heat from the ground or surface water to a water-based heating system), and assembling the individual components (evaporator, compressor, condenser, heat exchanger and expansion valve) in a variety of different configurations.
These modules are measured on test rigs 24 hours a day, for two weeks at a time. Each prototype is run at between 30 and 150 operating points, and the measured values are recorded by 26 sensors. In the search for the ideal heat pump, 26 prototypes have been built.
As reported by Fraunhofer in October 2022, the system with the best component configuration achieved a maximum heating capacity of 12.8kW and an efficiency of 4.7 (ratio of heat generated to electricity used) with only 124g of propane.
That means the amount of refrigerant required per kilowatt of heating capacity was only 9.7g of propane. The project’s goal of reducing the amount of refrigerant to 15-30g/kW has been exceeded. Commercially available heat pumps use about 60g of propane per kW.
The record-breaking refrigeration circuit4 is not yet ready for market, as it employs a semi-hermetic automotive compressor. This requires less refrigerant at a higher capacity thanks to its high rotational speed and low oil volume.
So far, automotive compressors have not been designed for the high operating hours of a heat pump that is meant to last 20 years. ‘However, the manufacturer is already working on fully hermetic compressors with a longer service life,’ says Clemens Dankwerth, of Fraunhofer ISE.
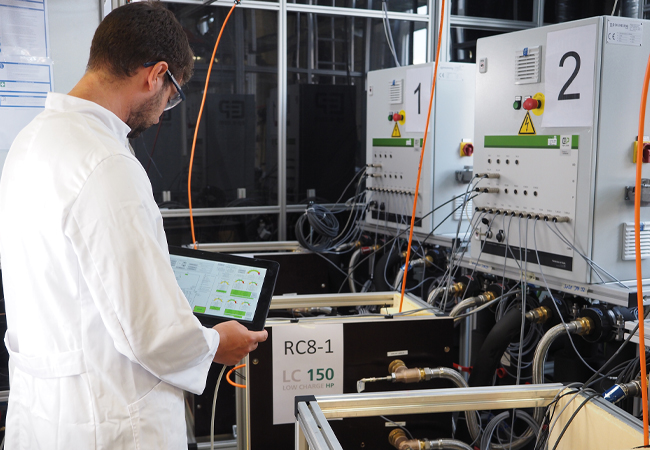
Heat pump test rigs running 24 hours a day
The final version of the refrigeration circuit would be implemented with slightly more refrigerant and a larger heat exchanger, to achieve a more balanced system. The team is confident that the goals of the project – a refrigeration circuit with an output of 8-10kW and maximum charge of 150g – can be achieved under real operating conditions.
The second-best refrigeration circuit in the test programme so far also met the project’s targets, with a charge of 164g of propane at an efficiency of 4.8% and a heating capacity of 8.1kW. A conventional fully hermetic compressor was used here.
In addition to the compressor, the research team adjusted other factors to reduce the amount of refrigerant. For example, the internal volume of the heat exchangers and the amount of oil required have been reduced. Additional components, such as sensors, have also been kept to a minimum, and the piping was kept as short as possible to reduce the internal volumes.
The LC150 project is funded by the German Federal Ministry for Economic Affairs and Climate Action and runs until March 2023
References
- Intergovernmental Panel on Climate Change (IPCC), Climate change 2021: The physical science basis
- Defra, F-Gas Regulation in Great Britain Assessment , December 2022, bit.ly/CJFeb23R2901, accessed 24 January 2023
- BS IEC 60335-2-40:2022 ED7 ‘Household and similar electrical appliances. Safety. Part 2-40: Particular requirements for electrical heat pumps, air conditioners and dehumidifiers’ (pending approval)
- Fraunhofer ISE, Propane-based refrigeration circuit for heat pumps achieves new efficiency record, bit.ly/CJFeb23R2902, accessed 24 January 2023