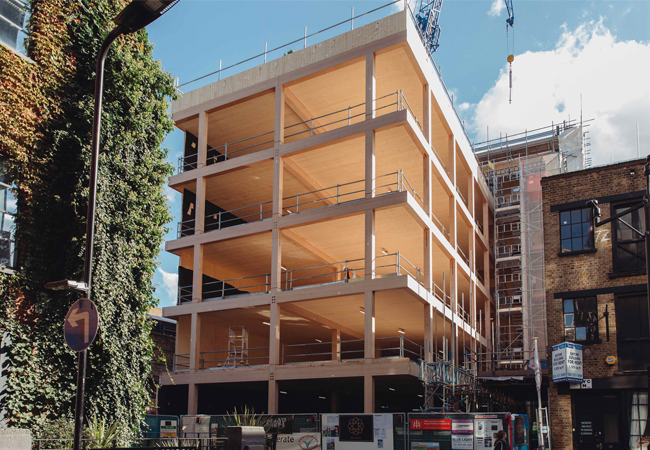
The floor slabs and staircases are all built from CLT
The Office Group’s brief for the Black and White Building, a six-storey commercial office development in London’s Shoreditch, was for it to be an exemplar of timber construction. It does not disappoint.
Designed by Waugh Thistleton Architects working with structural and façade engineer Eckersley O’Callaghan (EOC), the 17.8m-high building features a hybrid beech laminated veneer lumber structural frame, with a core, the floorslabs and staircases all built entirely from cross-laminated timber (CLT).
More impressive still is the façade. Designed by EOC, this is also constructed from timber. It features floor-to-ceiling glazing supported by a glulam composite timber/aluminium curtain wall, complete with external timber louvres to provide solar shading.
The façade’s size and innovative use of timber makes it unique in the London office market, an achievement recognised by the judges of this year’s Façade 2023 Design and Engineering Awards, run by the Society of Façade Engineering (SFE), at which the scheme won the UK Innovation category.
‘Despite initially considering an aluminium façade, in line with typical office buildings in London, we carried out a comparative analysis of embodied carbon and façade-profile depths structurally required to achieve the spans for both timber and aluminium options,’ says Ben Buckley, senior engineer at Eckersley O’Callaghan. ‘Ultimately, timber proved to have significantly lower embodied carbon content than aluminium, while maintaining a comparable profile depth, which maintained the net internal floor areas.’
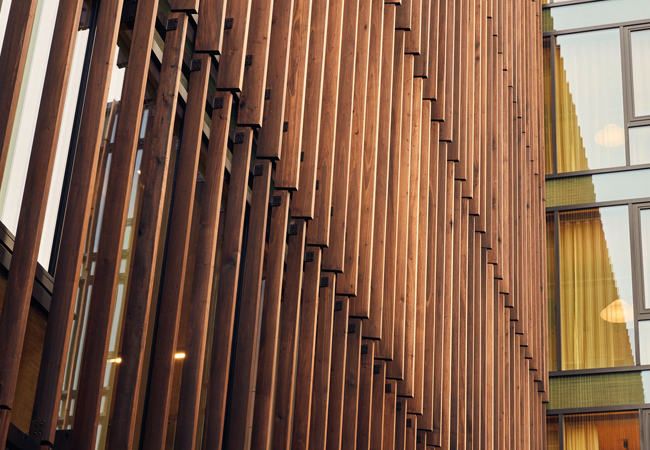
The louvres increase in depth as they ascend the building
One of the biggest challenges in attaching a timber façade to a timber building is the need to accommodate movement from the timber swelling and shrinking in response to changes in moisture. With the superstructure constructed from timber, it is lighter, and prone to greater movement from wind loads and occupancy, than if it had been built with a concrete frame.
Fortunately, EOC was also the project’s structural engineer, so façade engineers were able to work with their structural engineering colleagues to predict structural movement during construction and when occupied, to ensure these could be accommodated. ‘Early coordination enabled stringent deflection criteria to be specified and designed to minimise the risk of design changes once contractors were appointed,’ explains Buckley.
Embodied carbon
The fully engineered timber superstructure makes a powerful sustainability statement, with claims that it contains one-third less embodied carbon than a comparable six-storey structure. Only the basement box and integral ground-floor slab are constructed in concrete.
The building’s embodied carbon is calculated to be 410kgCO2e·m2 (modules A1-A5, excluding sequestration), compared with that of a conventional building of around 670kgCO2e·m-2.
Impressively, the timber structure is bolted together to enable it to be dismantled easily and reused at the end of its life. If its timber is reused, then the sequestered carbon for as long as it is in (re)use lowers the building’s embodied carbon figure still further, to just 180kgCO2e·m2, below the LETI 2030 target for office buildings
For the façade alone, the use of an aluminium/timber hybrid was calculated as having 40% less embodied carbon than the equivalent aluminium system if sequestered carbon is included.
The curtain wall spans CLT floor slab to CLT floor slab, with differential movement accommodated through the connecting brackets. ‘To accommodate the larger, long-term deflections of the timber structure compared with a concrete structure, we also designed a thicker horizontal transom to accommodate the movements,’ says Buckley.
The floor-to-ceiling glazed panels that enclose the floor plates are punctuated with inward-opening casement windows to enable the workspaces to be naturally ventilated as part of a mixed-mode ventilation strategy.
EOC’s façade engineers engaged with the building’s MEP engineers, EEP, to refine the shading solution of timber louvres. Parametric modelling was used to determine the layout and form of the louvres to enable solar control and to maximise daylight on the floor plates, to minimise the need for artificial light. It was also used to meet the daylight levels required for Well and Breeam certification.
The project demonstrated impressive architecture and innovative design while ensuring sustainability was at the centre of every decision
The resulting timber louvres run from street level to the roof; they are positioned horizontally on the southern façade, and vertically on the east and west façades. Spaced at 375mm centres, the louvres increase in depth as they ascend the building. A secondary structure supports the timber fins to transfer loads to the 1,200mm-spaced mullions.
Tulipwood, a readily available hardwood from the USA, has been used to craft the louvres. For this project, it has been kiln heat-treated to enhance its stability and durability, thereby extending its service life. As the building has been designed to be demountable, the louvres can also be removed and repurposed at the end of the scheme’s life.
It is one of the first times wood from this tree species has been used in the UK, so EOC had to work with the American Hardwood Export Council to obtain the appropriate testing, strength and durability information.
The louvres’ fire performance was also enhanced. The European standard EN 13501 defines the reaction-to-fire performance of construction products. To enable the louvres to meet the Class B reaction-to-fire performance, the timber fins are impregnated with a fire-retardant resin to ensure they only make a ‘limited contribution to fire’. As there was no UK fire test data available for tulipwood, EOC had to organise for a fire-testing body to undertake testing before the fins were procured.
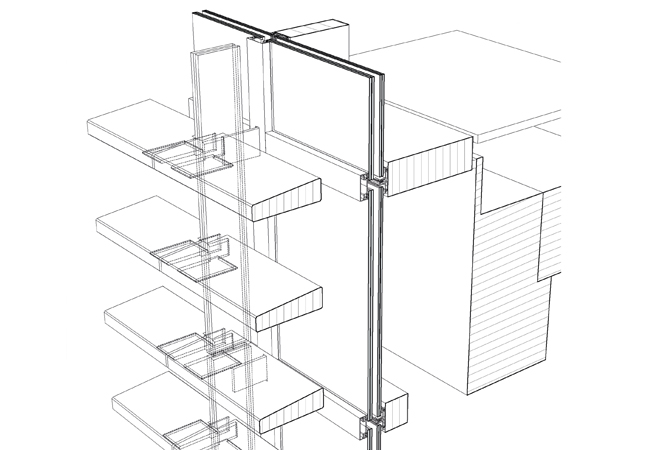
View of the curtain wall with horizontal fins
For this pioneering building to comply with the fire regulations, and to respond to insurance company concerns post-Grenfell, detailing on this project was developed with the client, fire engineer, building control body, and product suppliers and contractors to alleviate all potential risks. Fire performance is further enhanced by having sprinklers throughout the building.
As the awards judges recognised, the engineering of the Black and White Building is highly innovative and proof that carbon-minimal construction can be achieved through clever design. It is the tallest mass-timber office building in central London, and its innovative façade sets a new precedent for contemporary low carbon architecture.
- For more information on the Façade 20023 Design and Engineering Awards, and the full list of the winners visit: SFE Façade 2023 Design and Engineering Awards.