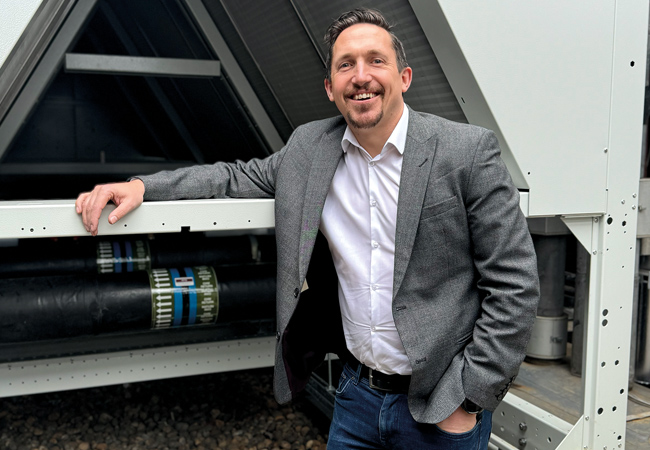
Draper impressed the CIBSE award judges with his obvious passion for the development and growth of engineering
CIBSE’s 2024 Engineer of the Year, Phil Draper, is well known at the Institution. Through his work for CIBSE, he has done much to disseminate practical knowledge around innovative systems, and has been forthright in his encouragement of apprenticeships.
Renowned for his work in retrofitting commercial heat pumps, Draper has made substantial reductions in carbon and costs in large commercial properties, using an innovative and lean engineering approach.
The award judges praised him for encouraging others to make the changes necessary for large buildings to decarbonise in a cost-effective way. ‘While we saw many great examples of leadership and development of teams, the winner stood out for his creativity and practical delivery of innovation,’ they said. ‘He clearly has a passion for the development and growth of engineering.’
British Land’s 350 Euston Road was the first large-scale heat pump retrofit in a commercial office building. The project was led by Draper who, in 2012, was working for British Land. ‘It was a really steep learning curve,’ he recalls.
British Land was on a mission to reduce its energy use by 40% by 2015. The seven-storey office building’s three gas-fired condensing boilers and two air cooled chillers were approaching the end of their life. Retrofitting heat pumps was the obvious solution, Draper says, because, like most commercial offices, this one required concurrent heating and cooling for a large part of the year.
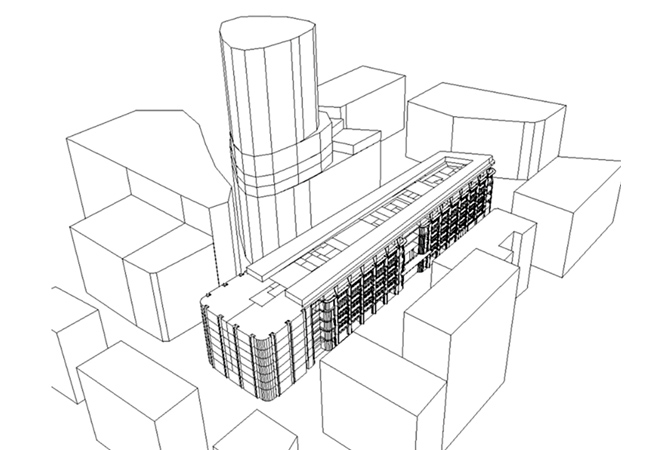
Model geometry for dynamic heat pump analysis with surrounding built environment
‘If you have a building that needs heating and cooling simultaneously, why would you run a separate heating and cooling plant when you could run a 4-pipe heat pump unit to help improve the building’s energy performance and reduce its carbon footprint,’ he says.
A major challenge in replacing the gas-fired boilers with an air source heat pump (ASHP) is the lower temperature of the heating supply. At Euston Road, the boilers supplied fan coil units (FCUs) on the office floors with water at 70oC. While heat pumps can now produce water at this temperature, at the time they did not. Instead, the heat pumps were designed to operate at a much more efficient system temperature of 45oC; with the FCUs supplied with heat at this lower temperature.
Heating demands in offices tend to be higher now than they would have been in a 1990s office, because heat outputs from computer monitors and lighting are less and office densities are generally lower – Phil Draper
The project uses a Climaveneta ASHP, which has three basic operating modes: chilled water only; hot water only; and simultaneous hot and chilled water production. ‘When simultaneous heating and cooling demand occurs, heat energy can be obtained almost for free,’ Draper says.
In 2014, ASHP technology was unable to deliver a sufficient quantity of high-grade heat to meet the heating demand when ambient temperatures were low. For the Euston Road project, when ambient drops below 5oC the building’s gas boilers kick in to meet the heat demand.
The solution worked. ‘The additional expenditure to retrofit the air source heat pump achieved payback within a year and now saves occupiers £60,000 every year,’ Draper says. In addition, the switch to using an electric heat pump as the primary heat source, as opposed to gas boilers, is helping to reduce carbon emissions by 470 tonnes a year and improve local air quality.
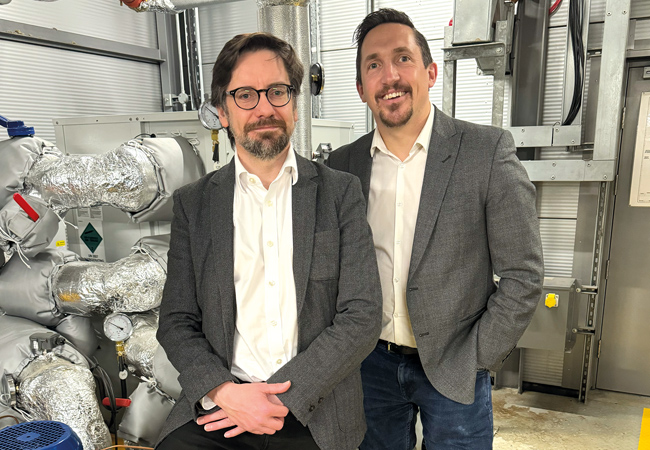
Draper frequently works with Darren Coppins, of Built Physics
Ten years on and the installation is still delivering. ‘What this first project demonstrated quite successfully is the use of a heat pump as a means of recovering heat,’ Draper explains.
Having proven the methodology, Draper has continued to build on this experience and the lessons learned from that initial project, both as an employee of British Land and, subsequently, as managing director of his own consultancy, Twenty One Engineering. He says retrofitting heat pumps is more demanding than installing them in new-build projects. ‘With new-build applications, there is generally more space and it is much easier to design systems from the outset to operate at a lower system temperature of 45oC/50oC to maximise heat pump efficiency,’ Draper explains.
He says the challenges for heat pump retrofits include ‘restrictions on plant space using existing plantrooms, limitations on the electrical power available, and the need to provide sufficient heat to existing equipment sized to operate at a higher supply temperature’. In addition, heating demands in offices tend to be higher now than they would have been in a 1990s office, because heat outputs from computer monitors and lighting are less, and office densities are generally lower. On the plus side, with a retrofit you will have the benefit of detailed metering information from the building, ‘so there will be far fewer unknowns’, he says.
My journey from apprentice to CIBSE Engineer of the Year
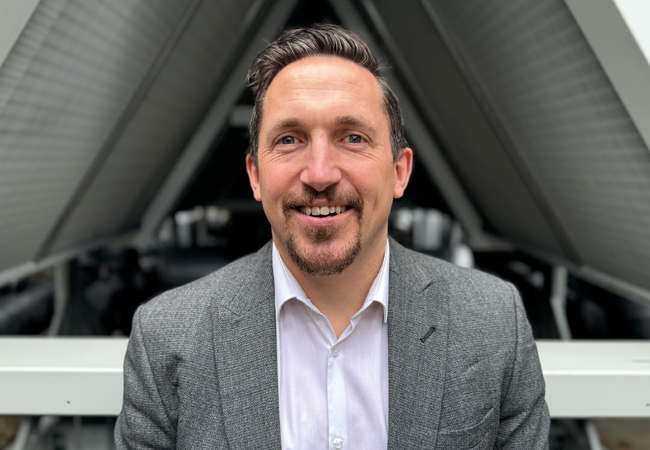
Draper has gone from ‘worst apprentice’ to ‘true leader’
I started out on an engineering apprenticeship, as a tool maker for e2v. Unfortunately, I cannot stand still, so, at the age of 18, I was told I was the worst apprentice they’d ever had and I was moved to facilities, where I undertook an electrical apprenticeship.
The e2v factory manufactures semiconductors and specialised components for medical, space and industrial applications. It has Class 10 and Class 10,000 clean rooms, and 11 substations – all high-end stuff. Learning about building services on a complex scale changed my mindset and I progressed to factory service engineer.
I left e2v to work for metering company EP&T, as technical lead. Our first big win was for British Land, where I designed and installed the metering system for nine of its buildings. I subsequently drove the energy management process for each, based on the operating data.
In 2011, British Land asked me to join them as senior engineering manager of its Regent’s Place complex. With experience of operating a Class 10 cleanroom, it is easy to transfer these skills to operating commercial office buildings. For the next three years, I drove operations at Regent’s Place to make the multi-let campus one of the most efficient.
In 2012, I started work on retrofitting a heat pump to 350 Euston Road – the first large-scale heat pump retrofit in a commercial building. By 2014, I was in a more central role, advising on how more of British Land’s buildings could target net zero. I started to engage with CIBSE and the Better Building Performance Group.
I left British Land to work, briefly, for a company called Cavendish, before setting up my own company, Twenty One Engineering, to use my skills and experience to deliver turnkey solutions for clients. These included British Land, where I continue to be involved in heat pump retrofits.
I’m a big advocate for apprenticeships, because that’s the route I’ve taken. Until now, no winner of CIBSE Engineer of the Year had done a hands-on apprenticeship – I should not be the only one.
The CIBSE BPA Judges said: ‘While we saw many great examples of leadership and development of teams, the winner stood out for his creativity and practical delivery of innovation. He clearly has a passion for the development and growth of engineering. A true leader by example and a genuine practitioner of engineering leadership.’
To assess the viability of a heat pump retrofit, Draper often works with Darren Coppins, of Built Physics, to model the building and its systems. The model references the metered operational data to confirm its accuracy. When the metered energy data does not match that predicted by the model, the team must assess whether the problem is with the building or the model, says Coppins. He adds that it might be down to problems with the existing controls or excessive infiltration, or parts of the building may not be working as they were intended.
‘We can drill into that data to see if it is something that needs to be addressed with building maintenance or whether the model needs to be tweaked to factor in something I’ve not allowed for,’ Coppins says.
When all parties are happy with the accuracy of the model, it is used to assess the operation of the proposed heat pump retrofit.
For an effective heat pump installation, Draper believes designers have to start to think differently about a project. ‘The historical approach to heating and cooling design was focused on meeting peak loads, but the average temperature in the UK probably sits between 8oC and 15oC,’ he says.
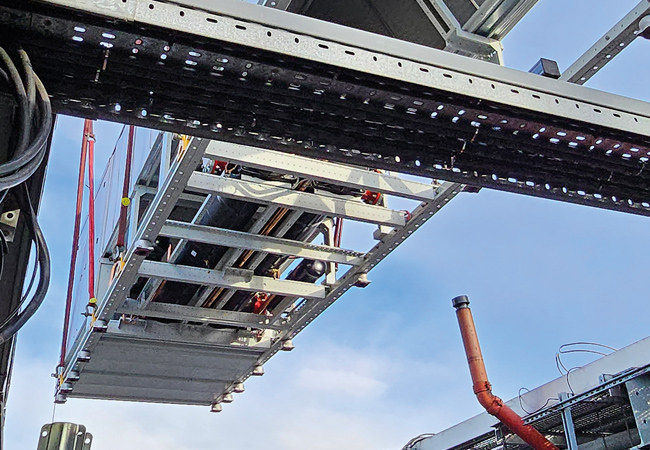
A heat pump being craned into position
It’s a point on which Coppins picks up. ‘We’ve got very used to using gas, which can be turned on and off very easily, but a heat pump does not work like that,’ he says. ‘With heat pumps, if we size them for peak capacity their lowest turndown won’t be low enough for them to operate efficiently or, potentially, reliably.’
For this reason, Coppins says it is important to optimise the heat pump for how it will run for the majority of the time: ‘We can predict that through building physics; rather than saying this building has a peak load of 3MW, for most of the time its load might actually only be half of that peak.’ He says a smaller-sized 4-pipe heat pump – ‘with a bit of top-up’ from an additional reversible heat pump – can be used to boost the heating and cooling outputs as required, and can provide a more reliable installation.
The downside of this type of solution is that the plant has to be hydraulically separated. For his latest project, however, Draper worked with Coppins to develop a conceptual retrofit design without the need for additional kit. ‘The system has been designed to work efficiently at 50oC, but – to meet peak demand – we’re planning to boost the heat pump system temperature from 50oC to 70oC,’ he says.
Innovative solutions such as this are feasible because Draper is keen to involve manufacturers. ‘Before we finalise our design, we will get the manufacturers in to have a conversation, because not every heat pump is the same and not every application is the same,’ he explains.
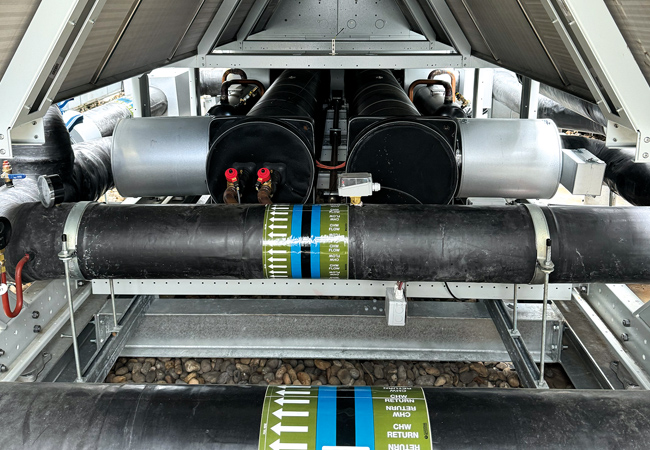
Inside a 4-pipe simultaneous heat pump
Another reason the team at Twenty One Engineering is able to develop innovative solutions, Draper believes, is ‘the open relationship we have with British Land as the customer and with Built Physics’.
In the 10 years since Draper became involved in retrofit heat pump installations, he says the biggest technological advance has been with refrigerant gases, because these allow higher circuit temperatures.
‘At Euston Road, we could achieve a circuit temperature of 50oC at an outside air temperature of 5oC. When the outside temperature dropped to 0oC, the system only achieved a temperature in the low-40s – while, at -5oC, you would struggle to get up to 40oC,’ he says.
‘Now, with different refrigerant gases, heat pumps can give us a system temperature of 55oC at -5oC ambient.’