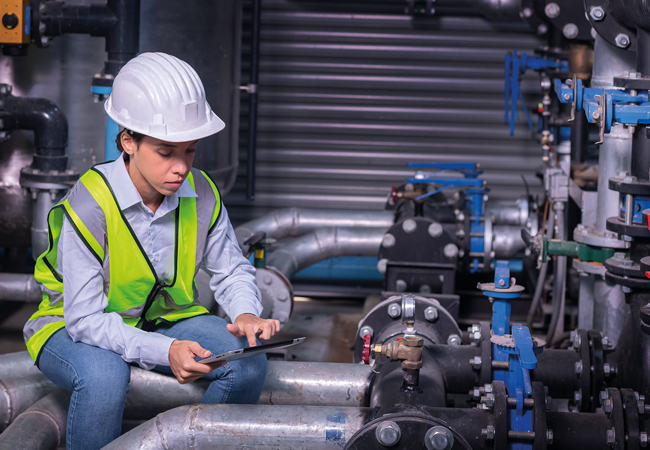
Guide M was last updated in 2014
CIBSE Guide M: Maintenance engineering and management is considered the ‘go to’ guide for the facilities management (FM) industry. Everything you need to know about operating buildings services is introduced and explained in this guide, and references to more in-depth resources are also provided.
The guide is based on UK best practice, updated for this third edition by volunteers, who each led on a chapter, or two, where they have knowledge of the subject and industry experience. There was an open call for contributors to volunteer their expertise.
Health, wellbeing and safety
Topical subjects are covered, including wellbeing, which has come into sharp focus since Covid. Lessons learned from the pandemic include the change in how people use buildings, and how management and maintenance that focuses on occupants can help organisations bring staff back into facilities.
Lessons learned from the Grenfell tragedy in the UK – and the resulting change in legislation and how this affects facility operators in terms of fire safety – have been provided, along with an update of all the legislation guidance. The need for the industry to take competence more seriously is another lesson learned from Grenfell, and the subject is covered in more detail than in the 2014 version.Energy and carbon are subjects that have undergone a lot of change since the previous edition. The content has been updated to cover the need for an energy management policy and capturing and using the energy-use data, and it explains what is required from an energy management system. Advice on low carbon and renewable systems has also been introduced.
Technology and controls
Controls can support the management of facilities more than at any time in the past. Advances in technology have required the subject to be almost completely rewritten in the guide, sharing current best practice from the Building Controls Industry Association. This includes the importance of the description of operation, how systems integrate, and a reminder to maintain the basics, but Guide M also offers insight into using controls for maintenance.
There is advice on upgrading control systems, as well as the importance of cybersecurity, commissioning and training.
Contracts and costs
The sections on contracts and costs of operation and maintenance now include guidance on the procurement process. Readers are reminded that awarding contracts based on lowest price alone often does not provide value for money and the guidance is to award based on a combination of price and quality.
Quality submissions should consist of questions designed to test the bidder’s understanding of the client’s requirements. It is an opportunity for the bidder to set out their approach to service delivery, their understanding of the services needed and of the client organisation, the benefits of the systems the company will deploy, and to indicate any innovative practices they may wish to introduce during the contract.
Guidance on mobilisation of contracts has been updated to provide a list of items that need to be discussed and agreed, such as: site familiarisation; access procedures/codes; helpdesk processes and contacts; emergency call-out contacts; details of emergency isolation points; and implementation and use of contract technology systems, such as computer-aided FM and computerised maintenance management systems.
Budgetary control, and the cost categories that can enable measurement of financial performance, is presented with maintenance cost consisting of labour, consumables, spares, specialist services, and other asset and equipment costs (such as capital allowances, grants, and so on). The section reminds readers that adjustment factors – such as access arrangements and any hours of working constraints – should be taken into account when calculating maintenance costs. Many criteria need to be included when building up maintenance cost plans and budgets, including an understanding of organisational need and business priorities.
The need for the industry to take competence more seriously is another lesson learned from Grenfell, and the subject is covered in more detail than in the 2014 version
As workplace strategies evolve, it is increasingly important to offer evidence of how costs are generated and used, to demonstrate that effective maintenance cost management can positively impact the workplace user experience.
The guide is still the only source in the industry with a comprehensive list of indicative economic life for engineering assets used in facilities. Life-cycle decision-making for asset renewal involves understanding that asset degradation is a trade-off between capital costs and operating and maintenance costs, while understanding the risks and probability of failure.
The application of asset-specific renewal interventions and threshold triggers for partial repairs (including mid-life overhauls), part or whole replacements during the expected life period, and end-of-life considerations are explained. Reference service life and replacement cycles will need to be adjusted account for a variety of factors. There is an updated explanation of these factors and examples to show how their use.
Economic life expectancy and factors are often used to determine when existing assets or components should be replaced, but this should always include reference to: records of the asset’s performance in use; where significant change in the operating and maintenance costs occur; legislation and environmental impacts, where applicable; and the risks and consequences of failure.
It is often assumed that once an asset reaches the age indicated by the economic life expectancy it should be a candidate for replacement. This is not necessarily the case, however, and may lead to premature – and sometimes inappropriate – interventions.
An updated Excel version of the life tables will be released as the CIBSE Indicative Economic Life Expectancy Tool, available at bit.ly/ToolBox23. It will be aligned with RICS NRM3 New rules of measurement, the BESA SFG20 Services and Facilities Group guide to maintenance tasks, and the NBS unified construction classification Uniclass. This ensures the construction and maintenance industry has a shared language to communicate effectively on asset life expectancy and maintenance engineering and management.
Guide M Parts
- M1 Guidance for building services designers
- M2 Strategy and techniques
- M3 Contracts
- M4 Energy and carbon
- M5 Controls
- M6 Commissioning and testing
- M7 Handover procedures
- M8 Documentation
- M9 Risk assessment and risk management
- M10 Costs
- M11 Economic life factors
- M12 Audits
- M13 Condition surveys
- M14 Legislation
- M15 Wellbeing
- M16 Training and competency
Jo Harris is the UK&I hard FM ambassador at Sodexo and lead author of Guide M: Maintenance engineering and management (2023). She was also lead author for the 2014 version.