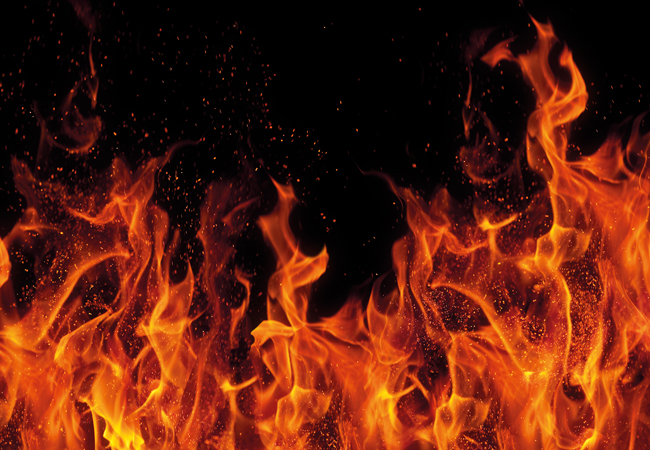
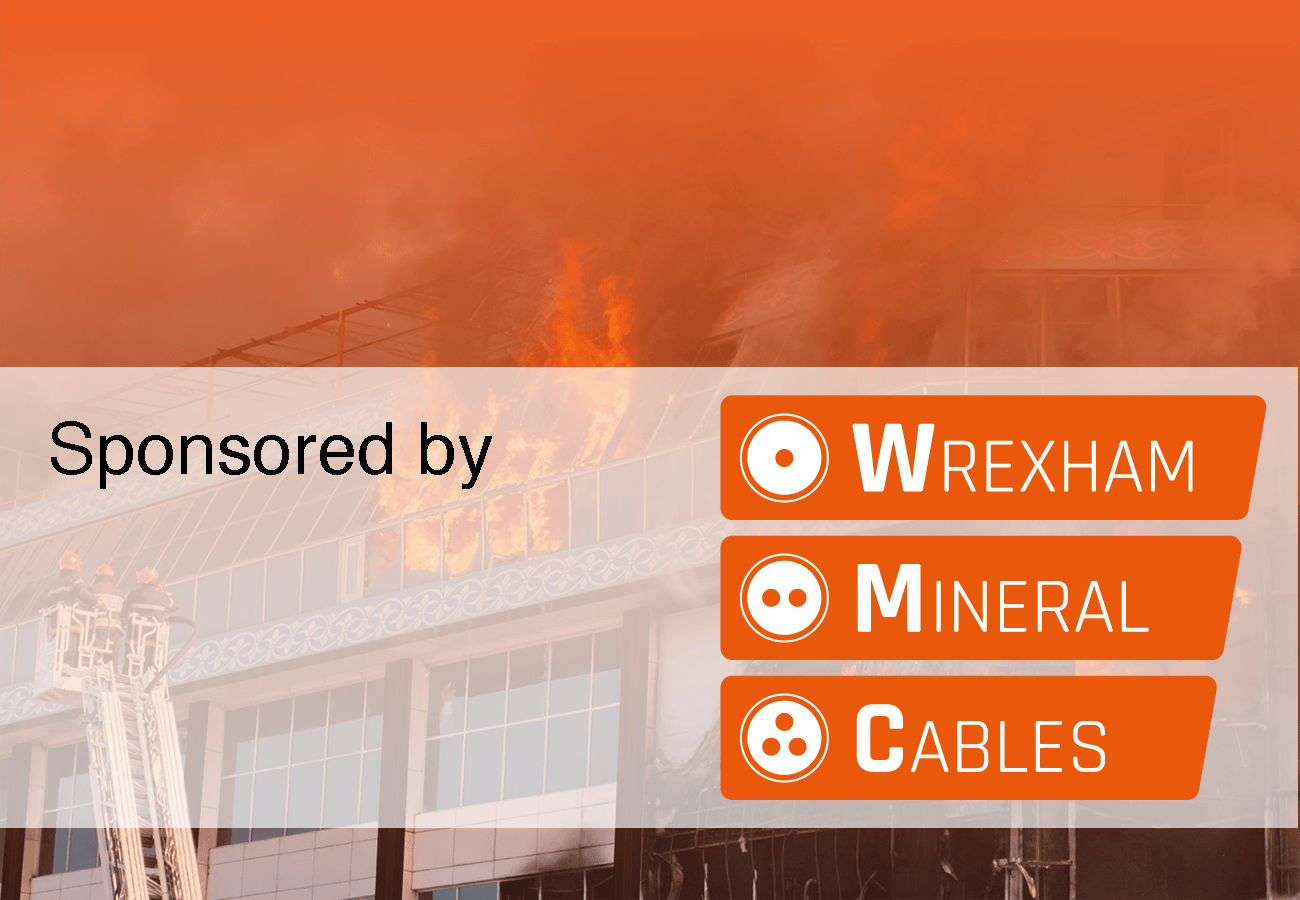
The network of power, control, and communication cables that pass through every part of a building provide amazing utility, but if not properly specified and procured, they could equally create a significant hazard and risk to safety in the event of a fire.
This CPD will consider how significant UK fire events have heightened concerns in building safety, discuss some of the principal UK standards that are defining fire performance in cables, and identify some of the potential gaps that might well be filled in the revitalised, responsible culture ushered in by the recently introduced Building Safety Act1 in England.
As reported in CIBSE Journal June 2018, the inquiry in the aftermath of the Grenfell Tower fire that occurred in London on 14 June 2017 determined that all lobbies from level 4 to level 23 became smoke-logged and, repeatedly in the testimonies of the Grenfell survivors, black smoke (Figure 1) had impeded safe escape. The 2009 fire in Lakanal House, Southwark, was reported to the Grenfell enquiry, as there were thought to be similarities in the response to the fire and the rapid spread of the fire to other floors, as well as the devastating impact from smoke.
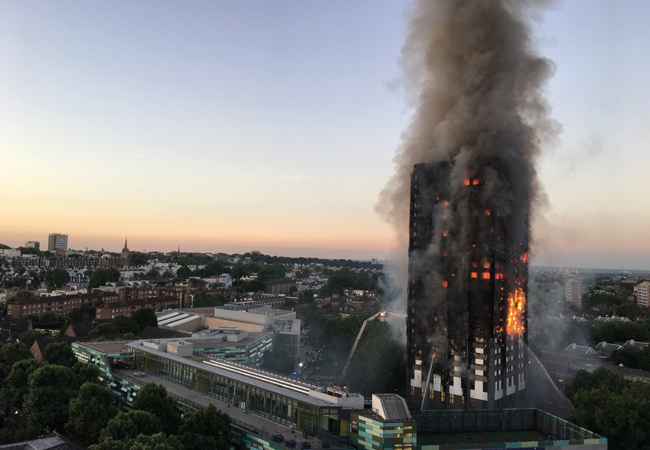
Figure 1: Grenfell Tower at 4.45am on 14 June 2017 (Source: Nathalie Oxford – bit.ly/CJJan24CPD5)
Within 30 minutes of the fire starting, smoke had spread to involve floors 6 to 12 (of the 14 storeys) and smoke-logging affected large parts of the building, including the communal staircase, corridors and many of the flats. However, some 22 years prior to that, the King’s Cross Underground station fire in London (Figure 2) had already heightened concerns around fire safety procedures and protocols, and the devastating impact of smoke on safe egress from a fire. In addition to loss of life, the fire destroyed much of the station equipment and fixtures, including the cabling systems.
However, the predominant cause of death resulted from the dense black smoke.2 Witness statements in the subsequent public inquiry2 noted that as survivors ‘reached the steps up to St Pancras Station, the smoke quickly turned from brown to dense black, which smelt to them like a burning plastic cable’. The coroner reported that it was impossible to ascertain the source of toxic fire fumes, and so it was not possible to determine the source of toxic materials found in the bodies of those who had died.2
In these tragic fires, electrical wiring was not directly implicated in the cause of the fire, or in specifically creating the smoke that prevented the safe escape of many occupants. At King’s Cross, for instance, a fire-damaged cable had disrupted the automatic operation of the Victoria line, but this was not explicitly associated with the main incident.
In all three fires, multiple factors coincided to produce the catastrophic outcomes. Many of these shortcomings were undoubtedly identified in the respective inquiries, and there has been significant work undertaken in the intervening years by London Underground/Transport for London, the London Fire Brigade, and, most recently, through the designation of responsibility and competence (and the aspiration of ‘cultural change’) in the Fire Safety Bill 20213 and the Building Safety Act 2022.
A key objective of the acts is to remedy the systemic issues identified by the Independent Review of Building Regulations and Fire Safety4 by strengthening the whole regulatory system for building safety. Many of the new requirements apply not just to ‘high-risk buildings’ but to all non-domestic premises, such as where people work, visit or stay, including workplaces, and the non-domestic parts of multi-occupied residential buildings (for example, communal corridors, stairways and plantrooms). The requirements do not apply within individual domestic premises.
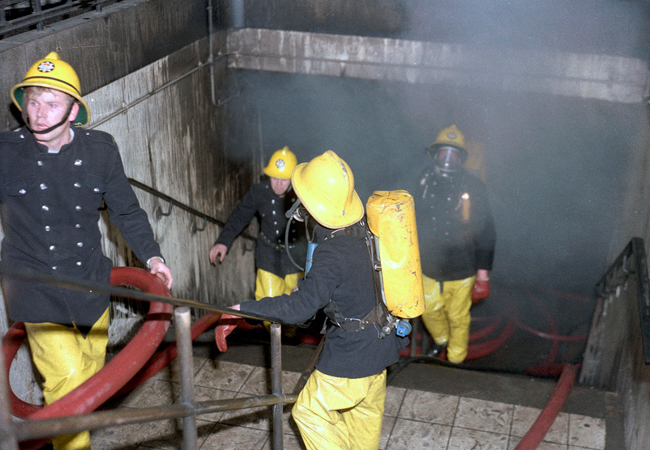
Figure 2: Firefi ghters emerge through the smoke as it billows from the fire at King’s Cross Underground station (Source: London Fire Brigade – bit.ly/CJJan24CPD4)
As seen in the fires discussed above, large, complex, and high-rise built environments that are more likely to be densely populated will have extended evacuation times. Smoke from inappropriately specified or inadequately manufactured cables will reduce the opportunities for successful escape from a fire. Circuits of safety-critical services need to function for extended periods, and fire plans are likely to rely on critical circuits continuing to perform to prevent potentially disastrous events, such as: fire alarm cable failure; sprinkler system not activating; smoke extract fans and smoke louvre power supply failure; and emergency lighting and signage failing to remain illuminated.
Fire-resistant cables provide extended periods of circuit integrity where uninterrupted functionality is crucial during a fire. They are designed to maintain their functionality and structural integrity for a specified period of time during a fire, and are constructed using materials that can withstand high temperatures when exposed to tested levels of flame, water and shock. They remain intact in harsh conditions, although they are not necessarily fireproof.
The insulation and sheathing are made from materials that do not propagate flames or produce excessive smoke, and so are able to provide protection against fire. Performance will vary depending on the specific type and design of the cable. The two principal types of fire-resistant cables are polymeric cables and mineral insulated copper cables (MICC).
Polymeric cables use synthetic materials such as polyethylene (PE), polyvinyl chloride (PVC), cross-linked polyethylene (XLPE), mica tapes and other polymers for insulation and sheathing, such as in the simplified sketch in Figure 3.
The flexibility of these cables makes them relatively easier to handle and install. Polymeric cables can be designed with various material layers to ensure that they maintain circuit integrity for a specified duration during a fire under defined conditions. The temperature rating of polymeric cables varies based on the specific polymers used.
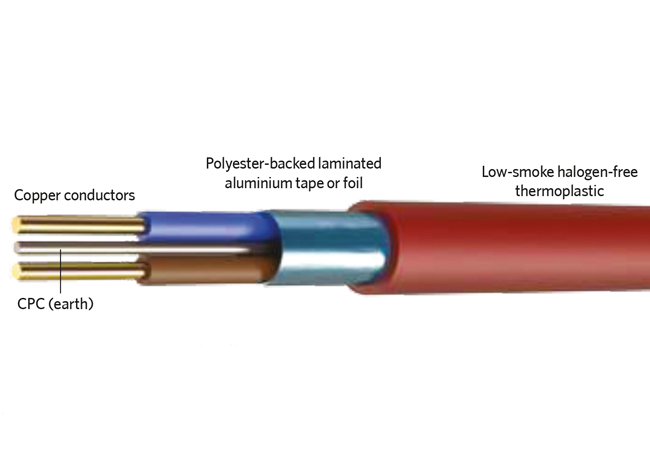
Figure 3: A simplified sketch of an example fire-resistant polymeric cable. There are many variants of such cables that are designed to meet specific fire-resistance requirements
The Institution of Engineering and Technology (IET) notes5 that there are many acronyms employed to represent the emissions performance of polymeric cable, and it is important not to confuse ‘low smoke halogen free’ (LSHF) and ‘low smoke and fume’ (LSF). PVC compounds are used during the manufacture of LSF cables, and while additional additives reduce the smoke emissions, they are not eliminated. There are no standards governing LSF cables, unlike LSHF, which are manufactured and tested to BS EN 61034,6 which considers the measurement of smoke density from burning cables, and BS EN 60754,7 which provides guidance on corrosive and acid gas emissions.
In MICC, the conductors are surrounded by mineral insulation, commonly magnesium oxide (MgO), and the principal outer sheath is typically made of metal, such as copper (Cu) or an alloy, as illustrated in Figure 4 and Figure 5. They are rigid and less flexible compared with polymeric cables; however, the rigid construction, resulting from the highly compressed powdered mineral insulation, provides excellent mechanical strength.
MICC are inherently fire-resistant because of the mineral insulation, and can withstand high temperatures and maintain circuit integrity during intense fires. This type of cable can typically safely carry an electrical load at temperatures in excess of 1,000°C.
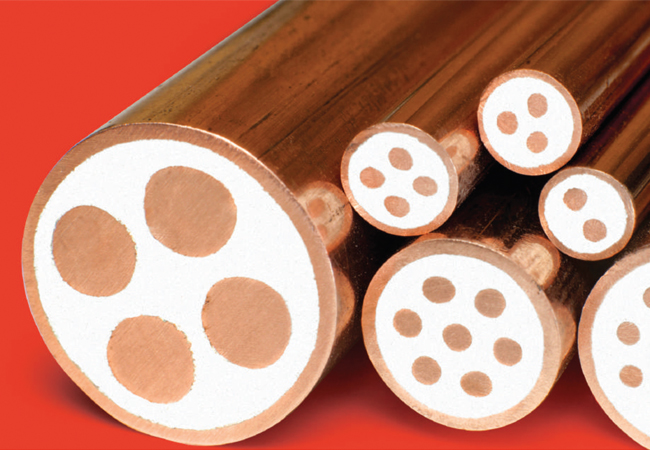
Figure 4: Examples of MICC (Source: Wrexham Mineral Cables)
Most cables installed as part of a permanent installation within domestic, residential and commercial buildings are subject to the Construction Products Regulation8 (CPR) that requires relevant cables to be CE-marked. Cable conformance includes reaction to fire and release of dangerous substances in normal operation, dismantling and recycling. All UK countries will accept9 the EU’s CE mark as appropriate for cables until at least 2025.
The supporting standard BS EN 5057510 covers the reaction to fire of cables in construction works on a scale of Aca (non-combustible, such as bare MICC) to Fca (no performance determined and likely to burn uncontrollably in a fire). In addition, there are classifications for smoke (s), flaming droplets (d), and acidity (a) as described in BS EN 13501-6,11 with each classification graded from 0 or 1 to 3. The BCA provides guidance12 on appropriate CPR ratings – for example, a cable designated as Cca – s1, d2, a1 is likely to be suitable for installations where ‘improved’ (as opposed to ‘low-risk’) fire performance of cable is required.
CPR covers both reaction to fire and resistance to fire, but only the harmonised standard BS EN 50575, which considers reaction to fire, is currently available. Therefore, fire-resistant cables cannot be certified under the CPR, so it is not possible to CE-mark and issue a declaration of performance (DoP) for them.
In the various UK Building Regulations, to be classed as fire-resistant cable, a cable’s construction must meet the British Standard appropriate to the cable type and application. There are many cable fire-performance standards – code of practice BS 851913 provides a useful table that lists the appropriate cable categories and standards for specific applications.
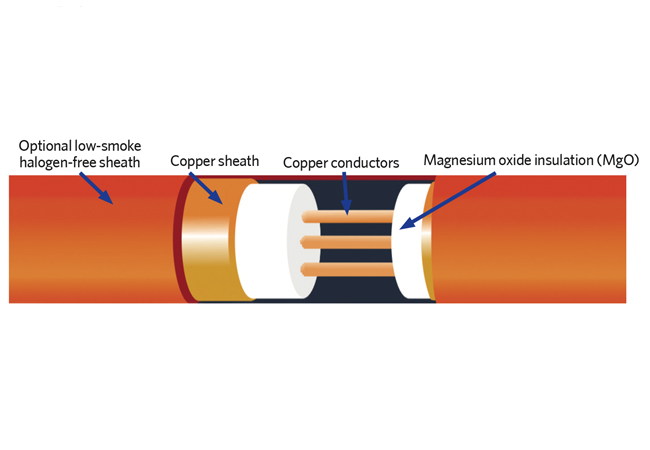
Figure 5: The components of a typical MICC
Each standard has a variant of time and flame temperature, with some incorporating physical shock and water spray, in order to test cables under simulated fire conditions – these can provide a bewildering array of ‘standardisation’. These can range from a 15- to 120-minute rated cable tested at 842°C – designated as PH 15 to PH 120 cable under BS 5020014 (which considers unprotected cables less than 20mm diameter for use in emergency circuits) – to a three-hour fire-rated cable tested at 950°C to BS 638715 (designated ‘category C’).
Code of practice BS 5839-1,16 which considers fire detection and fire alarm systems for buildings, makes recommendations for two levels of fire resistance – ‘standard’ (PH 30 with water spray) and ‘enhanced’ (PH 120, also meeting BS 8434-217) for unprotected cable. BS 8434-2 is a 120-minute test that includes direct flame, mechanical shock and a water spray, all conducted on the same cable sample in the same period at a temperature of 930°C. Cables with standard fire resistance are deemed suitable for the majority of applications.
However, cables of enhanced fire resistance are recommended where prolonged circuit integrity is necessary, such as in un-sprinklered high-rise buildings with phased evacuation arrangements, and premises that are likely to be part-occupied for a prolonged duration during a fire that might damage cables serving parts of the fire alarm system in occupied areas. Monitoring of circuits and protection of cables against damage are complementary requirement precautions, rather than alternatives.
Similarly, code of practice BS 5266-118 recommends (for unprotected cable) ‘standard’ (PH 60 plus 30-minute water spray) cables for normal use in emergency lighting systems and ‘enhanced’ (PH 120, also meeting BS 8434-2) cables for use in certain large and complex buildings where circuits are required to operate for longer periods to aid evacuation.
The well-established BS 638715 Test method for resistance to fire of cables required to maintain circuit integrity under fire conditions is widely applied internationally. The method is broken down into three separate tests – referred to as C, W, and Z – that are undertaken on a sample of cable.
C considers fire at 950°C; W, at 650°C, additionally includes a water spray with 15 minutes fire and 15 minutes sprinkler; and Z is carried out with the cable sample ‘rigidly’ mounted for 15 minutes at 950°C with a metal bar hitting the metal mounting frame every 30 seconds. Successfully passing the C, W, and Z tests outlined in BS 638715 suggests to specifiers and contractors that a cable is capable of surviving all three scenarios of fire, water and shock.
However, there are features of the three tests that have been highlighted by manufacturers as potentially not being sufficiently stringent. These include the fact that the three tests do not have to be carried out on the same cable sample; the volume flow of water in test W is a minimum of 0.3 litres of water per minute – which compares with a real-life scenario fire hose discharge in excess of 500 litres per minute; and in test Z there is no direct impact on the cable sample – in a fire, debris is likely to impinge directly on cables.
In his recent review,19 cable fire safety expert Richard Hosier emphasises the global prevalence of the BS cable flame test methods for certifying fire-resistant electrical cables. He highlights the standard 500mm-long gas ribbon burner test rig, expressing concerns that the set flame temperature in ‘open air’ tests may not consistently match the full cable temperature. Hosier compares UK standards with international practices, noting that furnace testing – exposing the full cable specimen to furnace temperatures – is adopted in other ‘developed’ countries, aligning with fire-resistance testing requirements for various building elements.
The Building Safety Act is establishing a fresh regulatory framework, placing accountability on those involved in procuring, designing, creating and maintaining buildings to ensure safety for occupants. Moreover, it grants consumers the authority to pursue legal action against manufacturers and suppliers for breaching the CPR or providing misleading information during product marketing or supply.
Building Regulations requirements should be considered as a minimum standard. The selection of an appropriately tested and independently certified cable requires that the manufacturer, supplier, designer, and installer have a robust understanding not only of the application, but also the practical fire performance that might be expected from the cable based on the necessary limitations of the standardised testing procedures.
References:
- Building Safety Act 2022.
- Fennel, D, Investigation into the King’s Cross Underground Fire, UK Department of Transport, 21 October 1988.
- Fire Safety Bill 2021.
- Independent Review of Building Regulations and Fire Safety.
- bit.ly/CJJan24CPD1 – accessed 26 November 2023.
- BS EN 61034-2:2005+A2:2020 Measurement of smoke density of cables burning under defined conditions – Test procedure and requirements, BSI 2020.
- BS EN 60754-1:2014+A1:2020 Test on gases evolved during combustion of materials from cables – Determination of the halogen acid gas content, BSI 2020.
- Regulation (EU) No 305/2011 of the European Parliament and of the Council of
9 March 2011 laying down harmonised conditions for the marketing of construction products and repealing Council Directive 89/106/EEC. - bit.ly/CJJan24CPD2 – accessed 26 November 2023.
- BS EN 50575:2014+A1:2016 Power, control and communication cables. Cables for general applications in construction works subject to reaction to fire requirements, BSI 2016.
- BS EN 13501‑6:2018+A1:2022 Fire classification of construction products and building elements Part 6: Classification using data from reaction to fire tests on power, control and communication cables, BSI 2022.
- Recommendations for the Selection of Cables under the Construction Products Regulation (CPR), British Cables Association 2019.
- BS 8519:2010 Code of practice for the selection and installation of fire-resistant power and control cable systems for life safety and fire-fighting applications, BSI 2010.
- BS EN 50200:2015 Method of test for resistance to fire of unprotected small cables for use in emergency circuits, BSI 2015.
- BS 6387:2013 Test method for resistance to fire of cables required to maintain circuit integrity under fire conditions, BSI 2013.
- BS 5839-1:2017 Fire detection and fire alarm systems for buildings Part 1: Code of practice for design, installation, commissioning and maintenance of systems in non-domestic premises, BSI 2018.
- BS 8434-2:2003+A2:2009 Methods of test for assessment of the fire integrity of electric cables – Test for unprotected small cables for use in emergency circuits. BS EN 50200 with a 930° flame and with water spray, BSI 2009.
- BS 5266-1:2016 Emergency lighting – Code of practice for the emergency lighting of premises, BSI 2016.
- bit.ly/CJJan24CPD3.