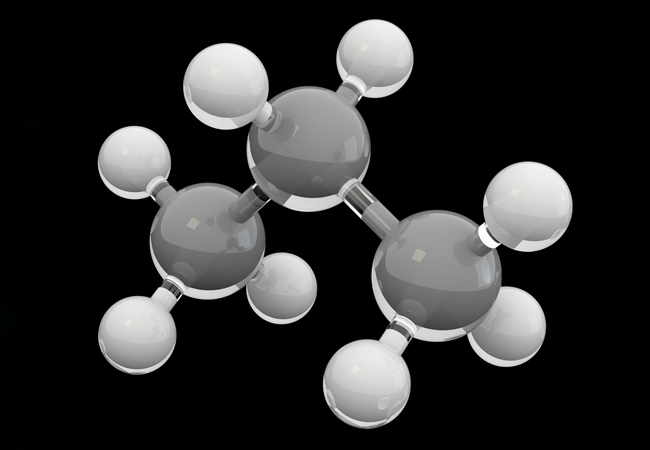
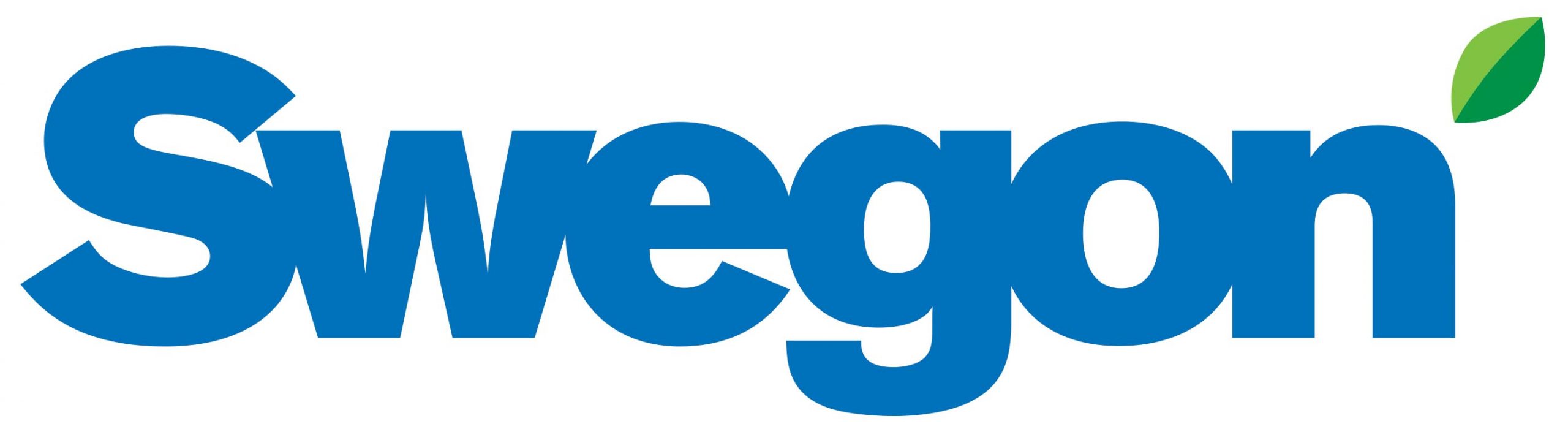
It is seven years since CIBSE Journal produced a CPD article specifically on the application of refrigerant R290 – propane – that, at the time, was likely seen by many as an outlier in the refrigerant marketplace. Over the intervening years, the relative benefits, challenges and opportunities of using such refrigerants – one of the ‘natural’ refrigerants – have moved on significantly. This CPD will highlight the continuing challenges, and consider the changes that appear to be ushering in the new era of propane-charged heat pumps and chillers.
The quest for more environmentally benign refrigerants gained international prominence when it was discovered that the synthetic refrigerants chlorofluorocarbons (CFCs) and hydrochlorofluorocarbons (HCFCs) were adversely impacting the global ozone layer. Under the 1987 Montreal Protocol,1 many countries agreed to phase out CFCs and HCFCs. This accelerated the application of hydrofluorocarbons (HFCs) that – although exhibiting zero ozone depletion potential (ODP) as they have no chlorine content – were subsequently associated with global warming.
The 2016 Kigali Amendment set a schedule for countries to gradually reduce HFC consumption, initially with developed nations taking the lead, and now recognised by 155 countries.2 The global initiatives to reduce the use of high-global warming potential (GWP) refrigerants have a significant focus on the reduction in the use of fluorinated HFCs and hydrofluoroolefins (HFOs). In Europe the F-gas regulation,3 initiated in 2016, set the pace, and this has provided the basis of the subsequent UK F-gas regulation.
Recently, in October 2023, revisions to the EU F-gas regulation were provisionally agreed4 to accelerate the implementation of measures towards the phasing out of HFC consumption by 2050, with the production of HFCs phased down to a minimum (15%) from 2036. A full ban was provisionally agreed, commencing in 2027, for specific chillers, small (<=12kW) monobloc heat pumps, and air conditioning with F-gases with a GWP >= 150, with complete F-gas phase out in 2032.
For split air conditioning and heat pumps that contain F-gases, the agreement was for a full ban starting in 2035, with earlier deadlines for systems with higher-GWP refrigerants. There was some wriggle-room included to support the aspirations of the EU to significantly increase the adoption of heat pumps – most of which currently use HFCs.
However, the suggested revisions will have a very significant impact on the selection of refrigerants and systems. Notably, the revisions also introduce certification schemes covering the safe handling of natural refrigerants. Simultaneously, the US Environmental Protection Agency5 announced enhanced provisions for the reduction and reuse of HFCs that will apply to products both produced in the US and imported. This will undoubtedly influence the global marketplace.
Separately, a recently completed consultation6 by the European Chemicals Agency considered proposals to restrict the use of per- and polyfluoroalkyl substances (PFAS) across the EU. The inclusion in the potential banned list of single component gases R125, R134a, R143a and the HFOs R1234yf and R1234ze(E) affects virtually all new and current lower-GWP HFC/HFO refrigerant blends.7 This has excited a huge response, including from trade organisations representing the refrigeration and air conditioning sector, who claim that the timeline of proposed reductions is practically impossible to meet.
As reported8 recently by the UK Committee on Climate Change (CCC), following the UK’s commitment to the 2008 Climate Change Act9 and the 2015 Paris Agreement,10 the UK government aims to reduce F-gas emissions to less than 3.4MtCO2e by 2035, from 11Mt in 2021, with most of the planned reduction coming from the UK F-gas regulation.
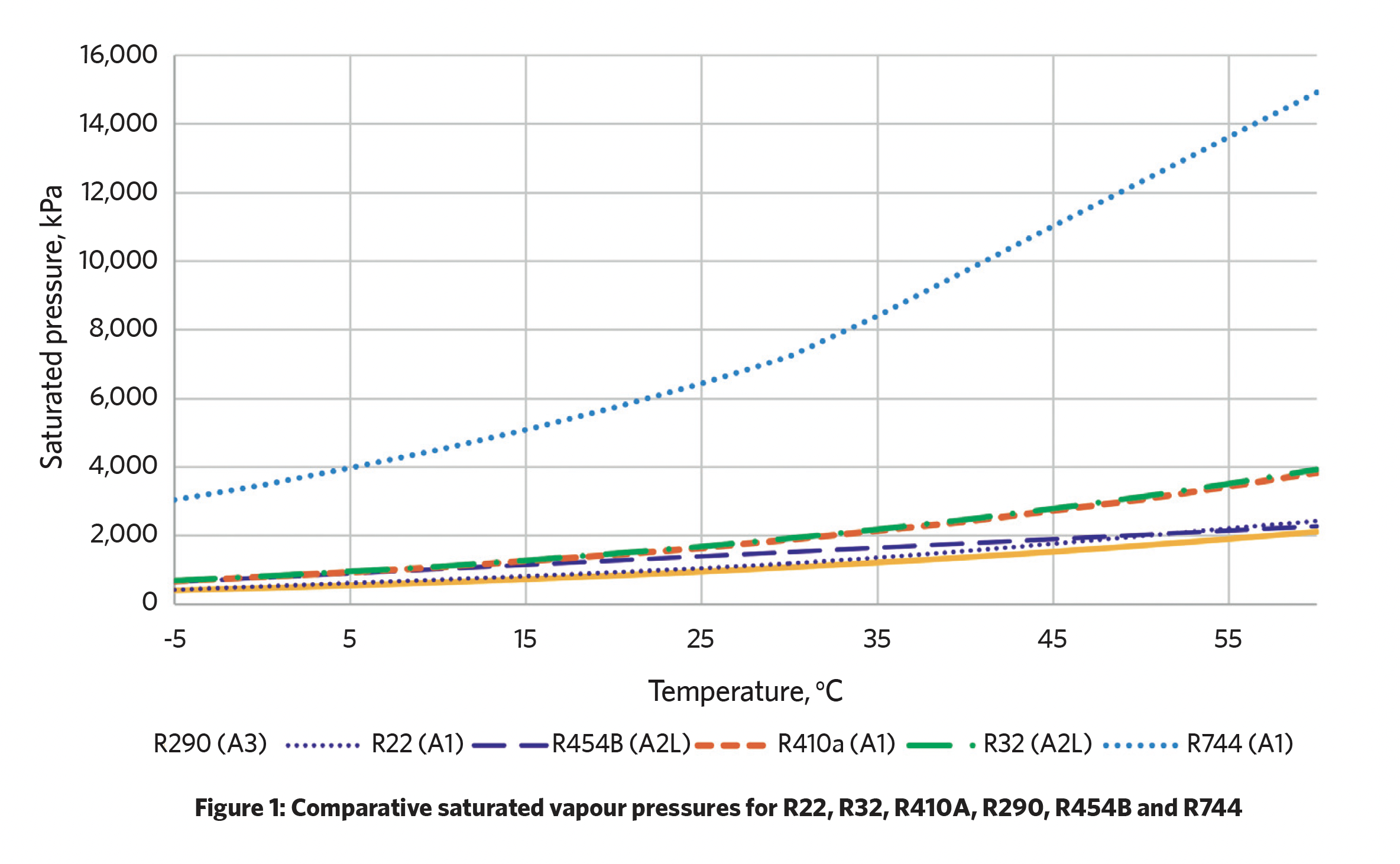
UK F-gas emissions have fallen over the past few years, decreasing by 6% in 2021; however, emissions remain higher today than in the early 2000s, and only 26% lower than 1990 levels. The CCC has determined that the consumption of HFCs must decrease to 15% of 2015 levels by 2035 to meet the UK government’s target. The UK F-gas regulation provides the mechanism to reduce this if, as CCC notes, it is successfully enforced.
The CCC also recognises the risk that emissions may increase with the roll-out of heat pumps, which currently mostly use F-gas refrigerants, unless the UK government takes action to ensure that there is a shift to non-F-gas refrigerants (such as propane, R290 and CO2, R744). Although the UK government has committed to reviewing the UK implementation of the F-gas regulation, there is, as yet, no clear legislative timeline, and no indication as to whether it will follow the lead in the recent provisionally agreed changes to the EU F-gas regulation
However, industry has not stood still. There has been a significant transition away from the use of R-410A (that was originally developed to displace the high-ODP refrigerants, such as the lower-pressure HCFC R22, chlorodifluoromethane) to HFC R32 and the HFO/HFC blends, such as R454B.
The synthetic HFOs typically have a 100-year GWP of between just 1 and 4. R32 (difluoromethane) had a previously accepted GWP of 675, but this has recently risen to 771, while R454B has a GWP of 467. One of the key goals is to produce refrigerants that have favourable thermodynamic properties, including relatively low saturated vapour pressures. Many very closely emulate the historically favoured refrigerant HCFC R22, as illustrated in Figure 1.
The changing GWP
The recent IPCC Sixth Assessment report11 (AR6) includes the official GWP figures for R290. The 20-year GWP20 of 0.072 and the 100-year GWP100 of 0.02 are somewhat lower than the traditionally applied GWP of 3 that had been assumed. Previous estimations were related to the formula for propane (C3H8) that assumed the three carbon atoms would combine with oxygen (O2) in the atmosphere to produce three CO2 molecules, hence a GWP of 3.
However, the much lower GWP now estimated by IPCC results from propane’s short atmospheric lifetime, with a temperature dependent half-life of about 14 days, as it breaks down into carbonyl compounds (carbonyl compounds do not, in themselves, contribute any significant GWP). The decomposition of propane into carbon dioxide is a lengthy procedure and would take many weeks to complete,12 by which time most of the propane would have already broken down.
In that same report, R32 had its GWP100 updated to 771 (from 675) by the IPCC. This will also make a small impact on the GWP of HFO/HFC blend refrigerants.
Although these are all energy-efficient refrigerants, most have other less welcome attributes that are likely to limit their eventual application in building services. The recent report13 from UK government confirmed that there has already been a significant transition away from the use of R410A to R32 and HFO/HFC blends, noting that R32 has proved to be an important alternative, with similar characteristics to R-410A, apart from it being a ‘lower flammability’ refrigerant – designated as A2L under BSI ISO 817.14
(R410A is designated as an A1, non-flammable refrigerant.) The F-gas regulation contains an upcoming ban on small split air-conditioning systems with less than 3kg charge using F-gases with a GWP of 750 or more, from 1 January 2025.
Although the UK report indicates there is already some use of propane, it is very limited. However, there is a significant upturn in major manufacturers’ interest in ‘natural’ refrigerants – which includes propane, as well as CO2 and potentially ammonia (R717) – for use in new air conditioners and heat pumps. This is motivated by the deleterious environmental impact of many synthetic refrigerants and the lower GWPs of propane and CO2 and, pragmatically, has been accelerated by regulatory requirements.
As discussed more fully in the CIBSE Journal CPD Module 99 from December 2016, propane (as well as other HCs) typically exhibits low pressure drops and achieves system efficiencies that are equal to – or exceed – those of synthetic alternatives. The latent heat of vaporisation of propane is twice that of the most common HFC refrigerants, so providing a higher cooling/heating effect for the same refrigerant mass flow.15
Work by the Fraunhofer Institute and a group of manufacturers16 has determined that heat pumps are practically operable with a refrigerant charge of about 10g of propane per kW, as compared with about 100g of propane per kW required with typical designs. Systems are already evolving to reduce refrigerant use – the example of the monobloc heat pump in Figure 2 has a 14.3kg charge to provide up to 195kW of heating and about a quarter of the refrigerant mass required for comparable R410A units.
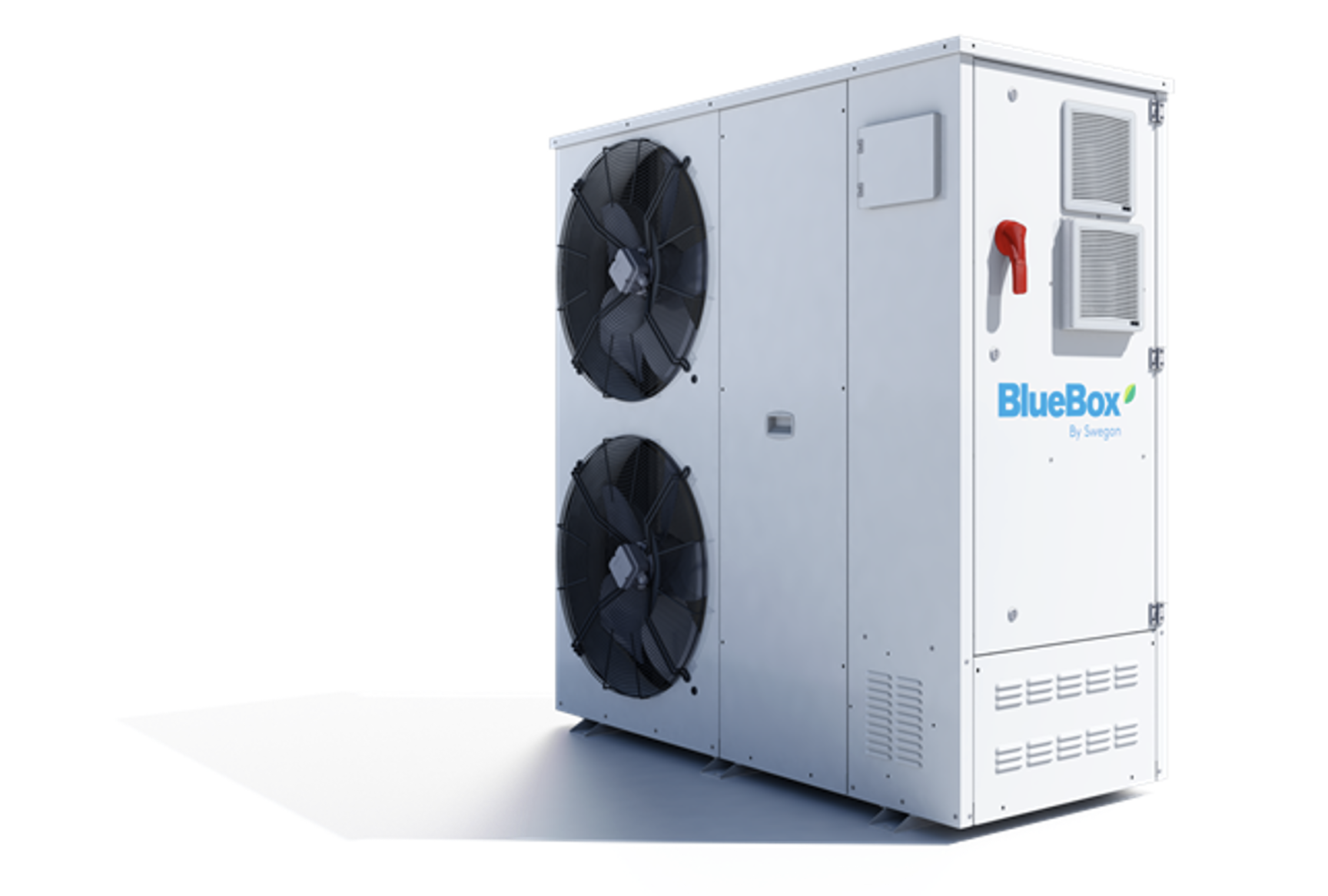
Figure 2: Commercial, monobloc heat pump with a 14.3kg charge of R290 (propane), to provide up to 195kW of heating (Source: Swegon)
The thermodynamic qualities of propane enable operation at low evaporating temperatures and high condensing temperatures, allowing it to provide water temperatures beyond 65°C (at sub-zero external temperatures) with COPs that could go as high as 4.5 (but are practically somewhat lower than that at the higher temperatures).
Propane is a colourless, odourless gas with a very low GWP (see boxout ‘The changing GWP’), an ODP of 0, and low toxicity (designated ‘A’ under BS ISO 817). Most propane is produced from liquid components recovered during natural gas processing and during crude oil refining (alongside other chemicals including ethane, methane and butane).
Although the amounts are relatively small, ‘renewable’ propane is also produced from biomass-based feedstocks, including used cooking oil, animal fats, or dimethyl ether (which is also one of the original 19th-century refrigerants). At atmospheric conditions, propane is a gas that is denser than air.
Propane is easy to procure and relatively cheap in price; however, the greatest weakness of propane, as with all HCs, is that it is highly flammable and so designated a ‘3’ under BS ISO 817. Flammable hydrocarbons require careful consideration of safety when applied in systems, and any installation should meet the requirements of standard BS EN 378-3.17
Units are constructed to stringent guidelines, employing ATEX (‘Atmosphere Explosive’ EU Directive 2014/34)-rated components and segregated electrical compartments to prevent spark risks. Dedicated leak-detection systems are used to monitor levels of propane that provide purging to outdoors, employing ATEX-rated extract fans, to ensure that the levels do not rise to approach the lower flammable limit (LFL) of propane (2.1% by volume of air – compared with 1.4% for petrol and 5% for natural gas). Being denser than air, any leaked gas has the potential to pool at low level and so systems should not be sited near drains or pits. Although not toxic, propane has caused deaths through asphyxiation.
Igniting propane
Propane does not spontaneously ignite below a temperature of about 470°C. Assuming the presence of air (and hence oxygen), three conditions must coincide to ignite R290:
- The concentration of the R290 in the air must range between the LFL and upper flammable limit (UFL). As an indication, in a fully enclosed room of 30m2 this would mean leaking between approximately 1kg and 6kg of R290, which equates to a concentration in volume ranging between a LFL of 2.1% and UFL of 9.5% (it’s unlikely to mix fully and ‘pool’ at low level). Outside this range, the mix does not propagate the flame: it is not flammable.
- The refrigerant must be introduced into a flow of air with a velocity three or four times slower than the burn velocity, as greater air velocities prevent the flame from getting ignited. As its burn velocity for R290 is 46cm.s-1, combustion will not occur if introduced into an air velocity above 15cm.s-1, even if the refrigerant concentration is correct for combustion. For comparison, the average walking speed of a person is 134cm.s-1 (approximately three miles per hour), air in a ventilated room is considered ’stagnant’ at under 50cm.s-1, and air speed in ‘light wind’ conditions is greater than 300cm.s-1.
- A source of ignition must be available, as referenced in the information in standard BS EN 378-2,19 Annex K. The minimum ignition energy (MIE) for propane20 is tiny at 0.48MJ, which could readily be produced by an arcing electrical switch, static discharges or potentially the dropping of a steel tool onto a hard surface.
Combustion products are mainly carbon dioxide and water and are, in themselves, harmless.
Following an extensive review process, IEC 60335-2-4018 – which deals with the safety of heat pumps – was revised in 2022 to increase the refrigerant charge limit in standard split air conditioning applications for use inside the buildings (it is currently under BSI review). The limit for R290 was increased from 340g to 988g in new equipment so long as it incorporates additional safety requirements to provide the same level of safety as equipment using non-flammable refrigerants. The new limits could allow more than 13kW of heating from split units.
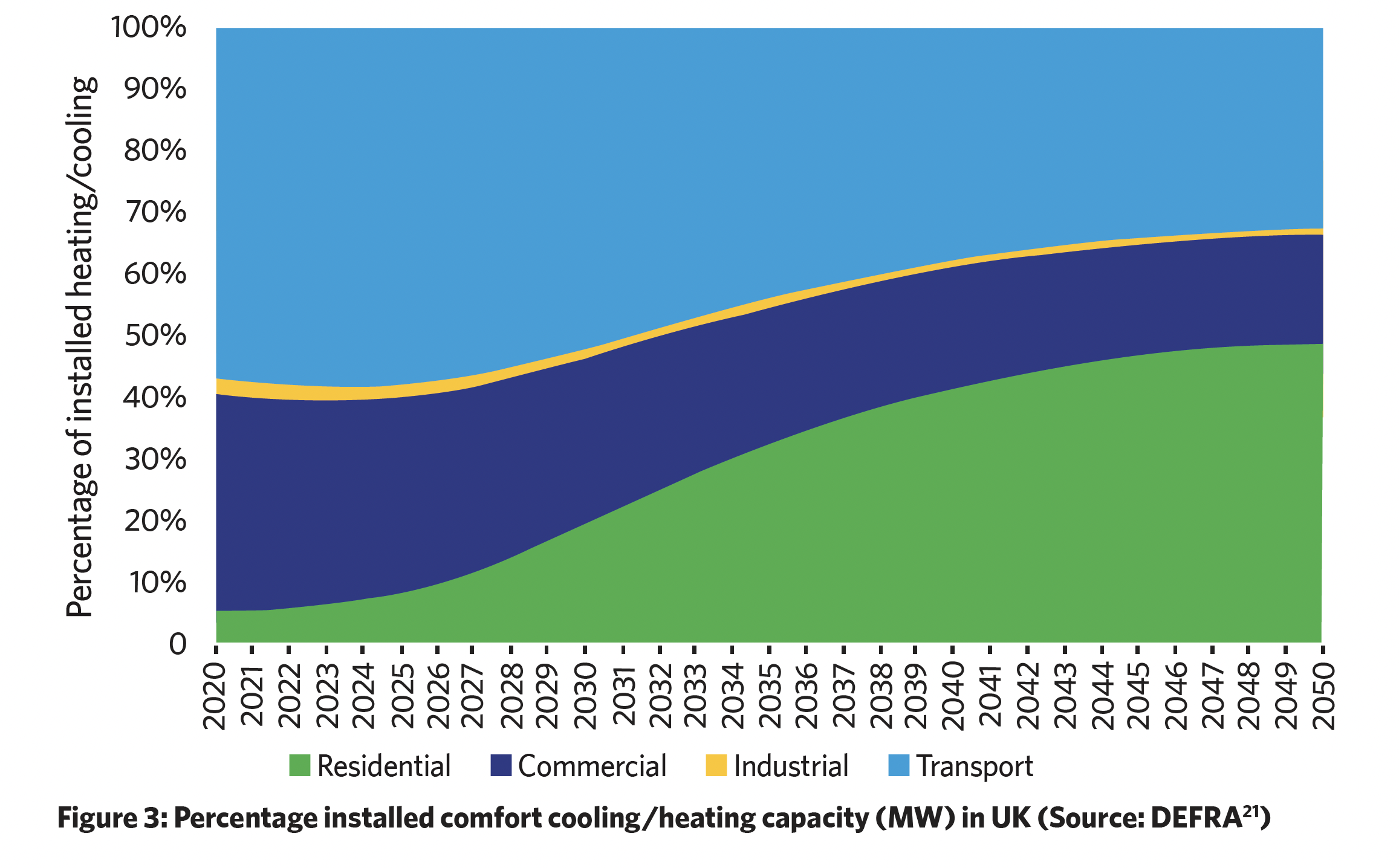
The UK government’s assessment of the HFC phasedown21 suggests a struggle to meet the required reductions and timeframes. The marketplace for air conditioning and heat pumps is predicted to change significantly over the next 25 years, as shown in Figure 3. This emphasises the importance of a swift roll-out of efficient, low-GWP refrigerants for residential and commercial applications.
The regulatory authorities are enthusiastically promoting the practical use of R290 with increases in allowable refrigerant charges, while researchers and manufacturers are creating systems with increasing efficiencies and reducing refrigerant charges. With installations designed, installed and operated to meet stringent safety requirements, prospects appear to be good for a massive expansion in the number of propane heat pumps and air conditioners that can provide increasingly effective systems with low operational environmental impact.
References:
- bit.ly/CJDec23CPD1 – accessed 1 November 2023.
- bit.ly/CJDec23CPD2 – accessed 1 November 2023.
- Regulation (EC) No 842/2006 of the European Parliament and of the Council of 17 May 2006 on certain fluorinated greenhouse gases.
- bit.ly/CJDec23CPD8 – accessed 1 November 2023.
- bit.ly/CJDec23CPD3 – accessed 1 November 2023.
- bit.ly/CJDec23CPD4 – accessed 1 November 2023.
- bit.ly/CJDec23CPD5 – accessed 1 November 2023.
- Progress in reducing emissions – 2023 Report to Parliament, UK Climate Change Committee, June 2023.
- bit.ly/CJDec23CPD6 – accessed 1 November 2023.
- 21st Conference of the Parties (COP 21), Paris, 2015.
- Intergovernmental Panel on Climate Change (IPCC), Climate Change 2021 – The Physical Science Basis Working Group I contribution to the Sixth Assessment Report
- bit.ly/CJDec23CPD7 – accessed 21 October 2023.
- F-gas regulation in Great Britain Assessment report, DEFRA, December 2022.
- BS ISO 817:2014+A2:2021 Refrigerants. Designation and safety classification, BSI 2021.
- bit.ly/CJFeb23R2901 – accessed 1 November 2023.
- Propane-based refrigeration circuit for heat pumps achieves new efficiency record, Fraunhofer ISE, 2022, bit.ly/CJFeb23R2902 – accessed 1 November 2023.
- BS EN 378-3:2016+A1:2020 Refrigerating systems and heat pumps. Safety and environmental requirements – Installation site and personal protection, BSI 2020.
- IEC 60335-2-40:2022 Household and similar electrical appliances – Safety. Part 2-40: Particular requirements for electrical heat pumps, air-conditioners and dehumidifiers, IEC 2022.
- BS EN 378-2:2016 Refrigerating systems and heat pumps. Safety and environmental requirements – Design, construction, testing, marking and documentation, BSI 2016 (under review).
- Eckhoff, R, et al, On the minimum ignition energy (MIE) for propane/air, Journal of Hazardous Materials, March 2010.
- F gas regulation in Great Britain – Assessment report, UK DEFRA, December 2022.