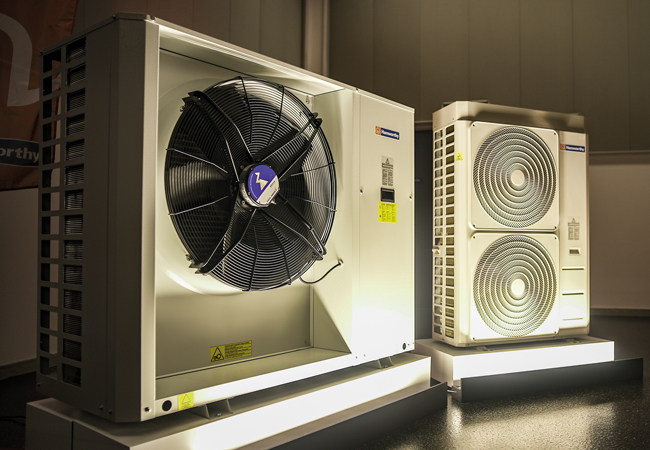
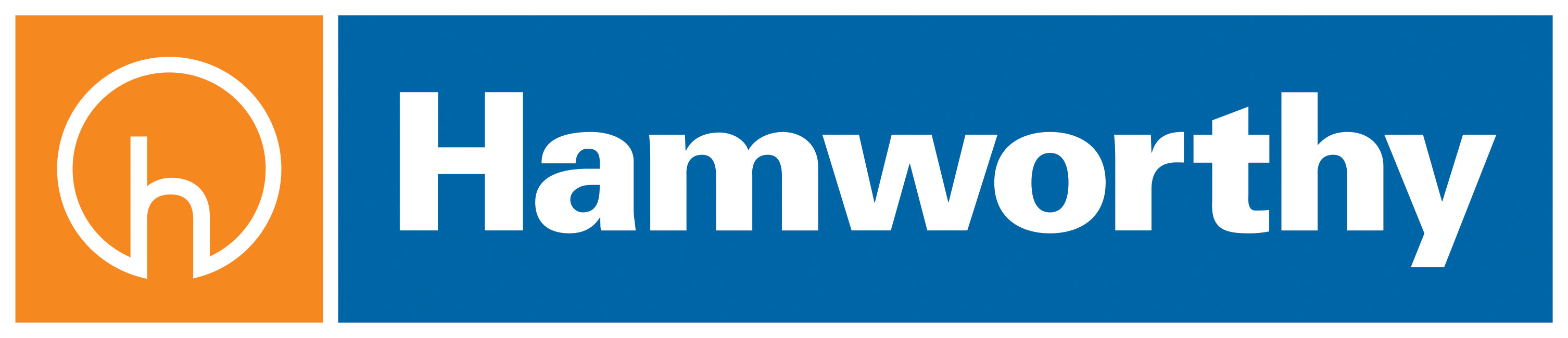
Reliable building services systems are key to building user and occupant satisfaction, health and safety, energy efficiency, operational dependability and longevity, as well as delivering environmental performance. Reliability will also afford more intangible impacts on business reputation, client approval and the wellbeing of the wider population affected by the success of the building’s integrity and dependability.
Such reliability is contingent on numerous factors throughout the gestation and creation of the built environment as, come practical completion, the onus will shift to the facilities management (FM) team to maintain the high standards that were envisaged by the building design team.
The majority of decisions that determine the maintainability of a building’s systems are made long before the building is finished. In the 1990s, Geoff Prudence of the CIBSE FM Group coined the phrase ‘designing for maintenance’ to highlight the importance of actively considering maintenance requirements at the earliest stages of a building project.
As noted in last month’s CIBSE Journal article1 by Joanna Harris, lead author of the recently revised CIBSE Guide M Maintenance engineering and management2, the guide is considered the ‘go to’ reference for providing industry guidance to ensure appropriate building services maintenance management.
The recent revisions provide a significant update and restructure to the previous versions, particularly reflecting recent changes in building use and performance expectations. This article has drawn on some of the key aspects of the guide that are most relevant to designers. However, the full document – which is freely downloadable to CIBSE members – covers these and other topics in greater depth, providing a comprehensive guide to successful building services systems maintenance engineering and management.
The design team needs to create systems that not only work well, but which can also be easily maintained within the physical, financial, and ethical constraints of the building operator. And – as noted in the recently updated CIBSE Guide M – they must meet the primary interest of most clients, which is to have a building that works without any problems. While most people accept that engineering services need to be operated safely and efficiently, they also expect that the building operator will have trained, competent staff to do this.
Designers should consider designs that avoid the need for a proliferation of specialist service companies, as this can improve the overall cost of the facility over its lifetime. Designers must, in any case, ensure that their designs can be safely installed and maintained, and should identify any areas where there is any risk associated with these activities.
Designers play a critical role in the performance of building services systems and, regardless of project size, will be well advised to start by considering the questions in Table 1, which are taken from CIBSE Guide M. These questions aim to promote inquiry that is contextualised to the particular project and help ensure that the final installation meets its goals. Designers should maintain a good understanding of other construction disciplines, and be willing to share ideas with other specialists and relevant stakeholders early on in the process to get input before designs are finalised.
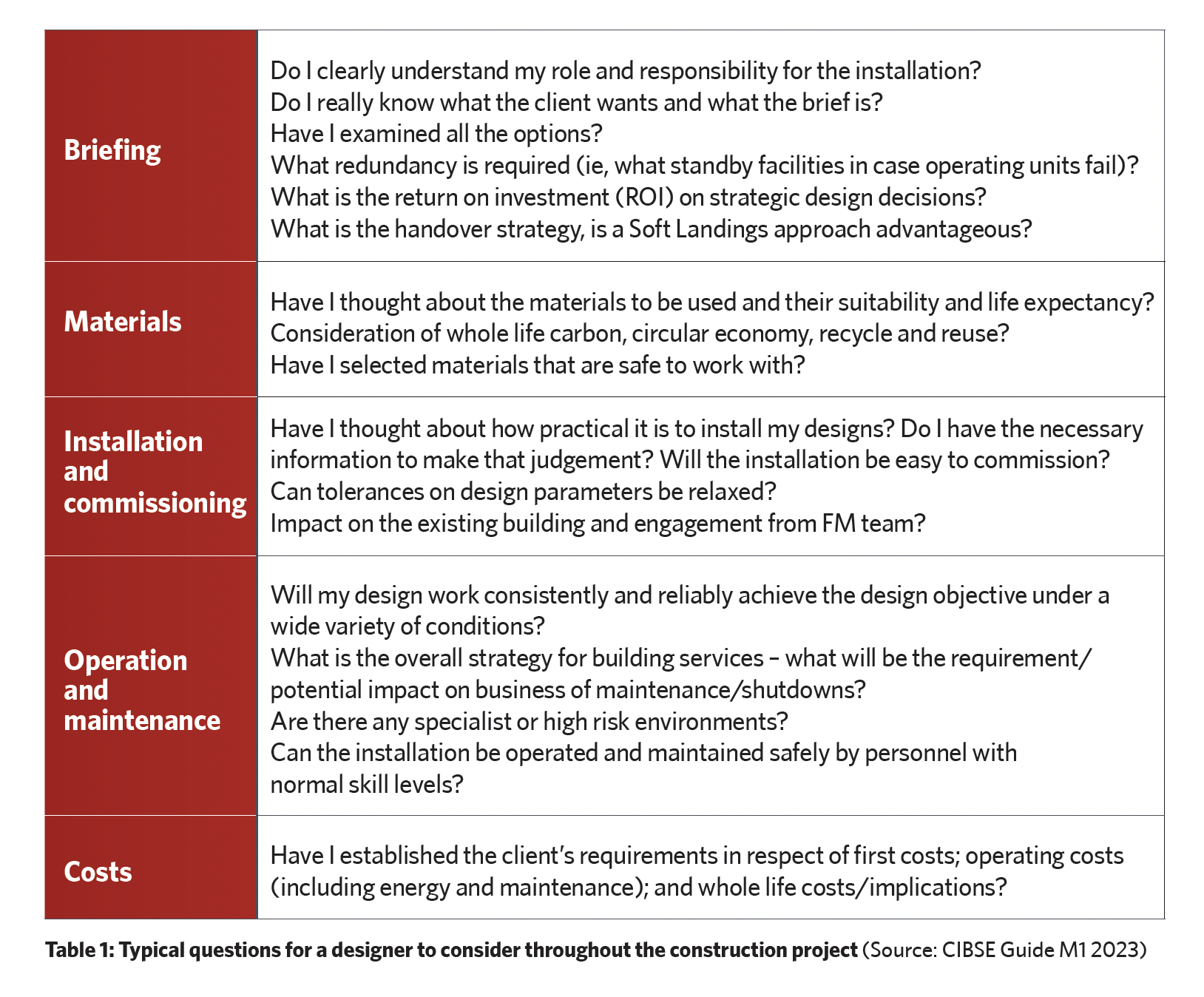
Clients may view running costs as being marginal when assessed against accommodation costs and staff wages, and simply accept operation and maintenance (O&M) expenditure. However, some may challenge even modest running costs to keep these under continuing review, and to seek cost-effective means of improving efficiency and reducing expenditure. In any case, they will not expect the maintenance demands to infringe unduly on their usage of the facility. Client attitudes to the environmental impact of buildings and their services can also vary widely.
When offering recommendations to clients, designers should employ clear, non-techy language. They should present various courses of action, highlighting both pros and cons. A preferred choice should be suggested along with the rationale and cost estimates for each option, encompassing total ownership expenses and expected replacement cycles.
Additionally, designers should indicate direct environmental effects and, if appropriate, ways to mitigate them. In cases where the client hasn’t specified their project requirements, the designer must clarify their assumptions and design parameters, and secure the client’s approval. This especially pertains to redundancy levels for engineering components. There should be a conversation about standby capacity, ensuring the client understands how failures could affect their operations and align expectations with their business strategy.
Where designers are encouraged to consider alternatives, they should clearly specify their requirements and make sure that clients understand the potential consequences. Similarly, it is the designer’s responsibility to provide the installer with enough information to make informed choices so that procured materials and equipment do not subvert the design intent.
Building information modelling (BIM) can be used to reduce the cost of changes during the concept, outline, and detailed design stages. This provides a significant opportunity to help ensure that clients and operators remain informed of maintenance and asset information throughout the building’s life-cycle, minimising maintenance and life-cycle costs, as well as the total cost of ownership.
Sustainability and net zero requirements are key considerations, and designers can play a significant role in this area, particularly by designing for flexible operation, maintainability and energy efficiency. Eliminating maintenance concerns, known as ‘designing-out’ maintenance, is increasingly common with the advent of ‘maintenance-free’ assets such as pumps and motors. The careful assessment of the impact of such assets on system level reliability is far more effective than attempting to integrate them post-installation.
While manufacturers may tout component reliability, the focus should remain on overall system reliability. This involves integrating support systems for cost-effective operation and maintenance, considering factors including the layout and accessibility of plant rooms; asset reliability; redundant systems; specialised maintenance knowledge; spare parts availability; after-sales support; and asset standardisation.
Built-in monitoring systems – typically referred to as computer-aided facility management (CAFM) – for real-time feedback on systems status often incorporate features for scheduling maintenance tasks, managing work orders, tracking asset information, and generating reports to aid in decision-making and efficiency improvements.
The decision as to the best design solution to fit maintenance and other organisational needs is often a subjective judgement based on a comparison between qualitative and quantitative aspects. The starting point for a maintenance strategy should always be at the client’s briefing stage, when the operation of the building is being defined. It is crucial to involve experienced O&M professionals early in the design process to ensure that practical and effective solutions are developed.
While this may be seen as an additional cost, it can add significant value by resulting in a more effective final design that may also reduce life-cycle costs. For projects within an existing facility, feedback should be sought from the local FM. For new developments, it may be possible to identify locations with similar requirements and discuss the design implications with an experienced FM. Early engagement with the facilities management team can significantly reduce the costs of poor designs, since the cost of making changes increases dramatically as the project progresses towards detailed design and construction.
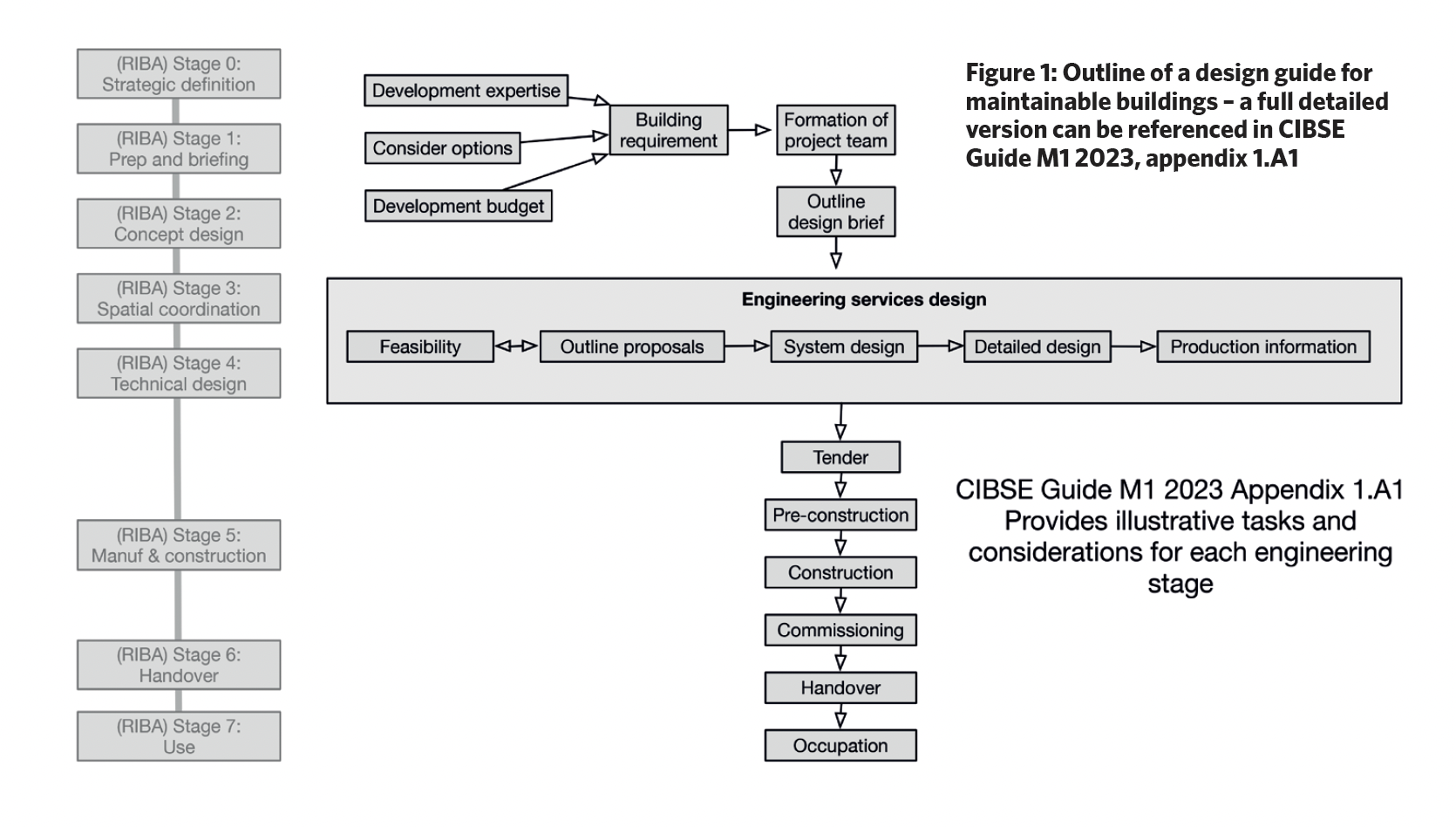
The choice of technology in the design will also be influenced by the maintenance policy, encompassing techniques that might include advanced building management system (BMS) monitoring, data analytics, protection of critical systems, and alarm monitoring. One of the fundamental principles in designing for successful maintenance is ensuring that all active system components are readily and safely accessible.
Accessibility simplifies and encourages routine inspections, repairs, and component replacements, reducing labour costs and minimising disruptions to building operation. It is important that designers ensure that they keep aware of decisions being taken on other constructional elements during the design process, to ensure that the building services systems design can be effectively installed in the final building, which is likely to have evolved significantly throughout the design process.
Designers must consider the suitability and life expectancy of materials being proposed and, where appropriate, should carry out whole-life costing studies. As well as operational performance, analysis should also include environmental dangers, risks and safety issues associated with the installation or maintenance. Thoughtful system design is crucial for both system efficiency and maintenance. This should not only focus on high-profile ‘normal’ maintenance items of equipment or front-line services exposed to the day-to-day user, but also include all the underlying systems.
A truly holistic approach should consider granular items. So, for example, when considering a ducted air system, this should include appropriate consideration of materials, fabrication and jointing techniques that provide cost-effective, suitably insulated ductwork that minimises air leakage but also creates a system that is internally smooth, accessible and readily cleanable. Unobstructed, labelled, suitably gasketed access panels and inspection points should be included at strategic locations, appropriately and safely accessible to simplify inspection, cleaning and maintenance tasks.
Appropriate inclusion of sensors and monitoring systems can enable predictive maintenance systems, track the performance building services components in real-time and provide alerts when maintenance is needed. Predictive maintenance helps prevent unexpected breakdowns and optimises the timing of service interventions – an area that will undoubtedly be enhanced with the further development of artificial intelligence (AI) tools. Remote monitoring and predictive diagnostic capabilities enable on- and off-site technicians to assess system performance, identify issues and make adjustments, reducing the need for physical visits and minimising disruptions.
Designers need to establish maintenance expectations for their installations, whether through specifications or written guidance. Additionally, they should factor in warranty maintenance in the construction contractor’s agreement. This could involve citing recognised maintenance standards or procedures, such as the UK’s SFG20: Standard Maintenance Specification (SFG203), to ensure comprehensive attention to critical maintenance concerns.
A designer’s involvement with O&M is often limited to specifying and reviewing O&M manuals delivered to clients upon project handover. However, it is essential to provide information that enables building operators to run facilities efficiently, incorporating expected operational energy standards for individual systems and the facility as a performance benchmark. It is considered best practice to define the projected replacement strategy for components throughout the facility’s life-cycle.
This entails creating an ‘asset replacement strategy’ as part of the design requirement, particularly for substantial essential equipment such as chillers, generators, and electrical switchboards. Additionally, during the design phase, designers should consider repair and reuse approaches, as well as contemplate decommissioning and replacement methodologies for installed assets. This is not always a straightforward reversal of the installation process, so an asset replacement plan with a method statement should be developed and documented.
The main contractor or building services contractor is usually responsible for producing and coordinating the handover information, which – in terms of O&M – include the operation and maintenance manual, and statutory and other prescriptive requirements, including those related to health and safety. The design and operation strategy should be clearly explained to communicate the rationale behind decisions made during the design process, including the software algorithms underpinning the building control system, as these define how the systems are to operate.
Handover information in the form of ‘as-built’ records are vital information assets that owners and FMs require to establish baseline facility performance benchmarks and reference information to maintain and optimise performance. Requirements for handover information will need to be agreed well in advance of the expected date of completion and must identify individual responsibilities for producing information.
Guidance such as BSRIA Soft Landings Framework4 can be applied by the whole building delivery team across all project phases to ensure that buildings not only meet the needs of their occupants, but are also documented and commissioned in a timely manner so that they may be operated and maintained effectively.
Where BIM has been implemented, some or all the information, including the model, can provide a useful resource for the building owner and operator. In the UK, the Building Safety Act 20225 requires information around building safety to be provided – referred to as ‘the golden thread’. The intent is to provide a robust trail of key information across to future owners to underpin more effective safety management throughout the building life-cycle.
Cost, space constraints, and the pressure to reduce project delivery times can lead to ‘value engineering’ of maintenance considerations and resilience aspects, which can have long-term consequences when the building is in use. An appendix to CIBSE Guide M1 provides a design guide to maintainable facilities, summarised by the section headers in Figure 1. This checklist can be used to ensure that essential steps are maintained, and key items identified and addressed, moving towards Prudence’s vision of ‘designing for maintenance’.
References:
- Harris, J, Maintaining performance, CIBSE Journal, October 2023.
- CIBSE Guide M: Maintenance engineering and management, CIBSE, 2023.
- bit.ly/CJNov23CPD21 – accessed 10 October 2023.
- Agha-Hossein, M, BSRIA BG54/2018 : Soft Landings Framework, BSRIA, 2018.
- bit.ly/CJNov23CPD22 – accessed 10 October 2023.