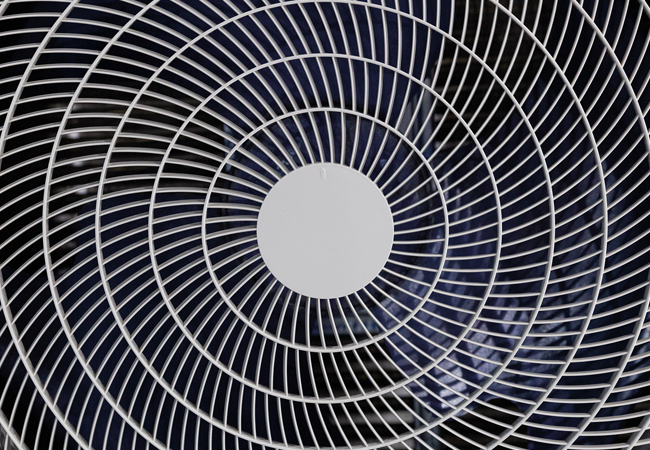
In the UK, and elsewhere around the world, there are significant incentives for owners and operators of institutional and commercial buildings aimed at encouraging the adoption of heat pumps in new and refurbishment projects. This CPD will focus on the application of simple, single-stage air source vapour compression monobloc heat pumps, particularly where they are employed in conjunction with an existing (or new) gas-fired boiler to meet year-round heating demands in existing buildings in order to reduce operational environmental impact.
The growing demand for the installation of heat pumps is driven by environmental requirements and financial considerations – in terms of both lower operational costs and subsidised, or grant-aided, capital cost and installation. In existing buildings, financial assistance is typically provided to upgrade existing heating plant and, in recent years, several UK government incentives have focused on educational and other institutional facilities.
Many such buildings are decades, or centuries, old and use high-temperature narrow ‘delta T’ systems, often designed to the historic low temperature hot water (LTHW) 82°C flow, 71°C return water temperatures that are now considered archaic, as well as wasteful of resources in both capital and operational terms. The current widely employed and commonly available simple heat pump technologies cannot reach those temperatures effectively; the thermodynamics of the vapour compression cycle and the properties of many of the commonly employed synthetic refrigerants make it impossible – or at least inefficient – to do so. Many heat pumps also require a narrower temperature difference across the condenser (which is used to heat the returning LTHW) than the historic 82/71 systems were designed for.
There are a variety of solutions available that can effectively produce higher temperatures and, in some cases, operate with wider temperature differences across the condenser. These include high-pressure, transcritical CO2 systems, ammonia and hydrocarbon (HC) systems, bivalent systems (which typically include a gas boiler, as well as a heat pump), and cascaded refrigerant cycles.
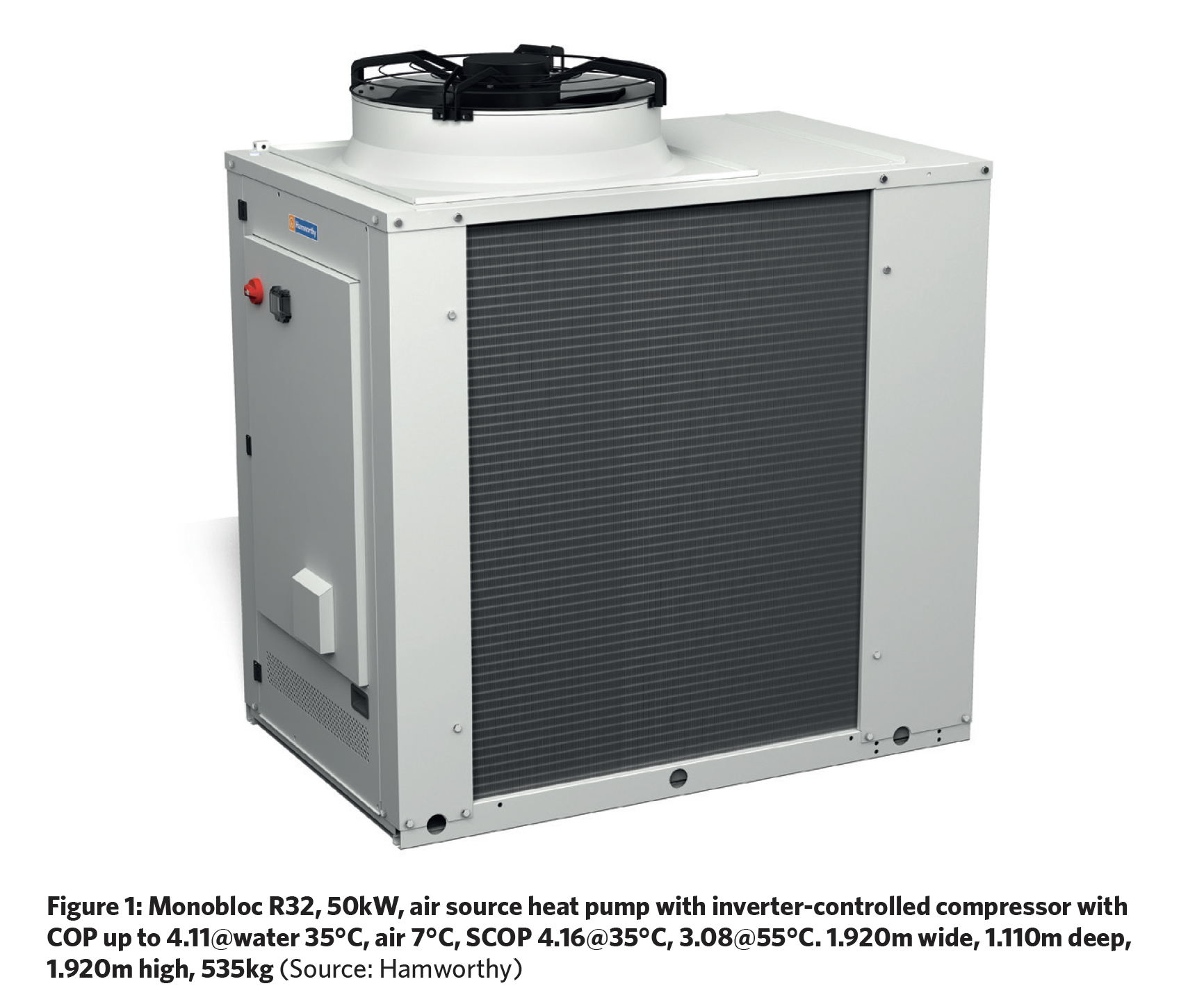
As noted in Heat pump retrofit in London,1 before any systems are designed or installed it is preferable to maximise the energy efficiency of the building. Aside from the direct benefit of reducing the overall demand for heating, this will reduce the capital investment required for the heat pump systems, reduce the required LTHW flow temperatures, and potentially improve the useful building thermal capacity in order to store heat that can provide benefits from time-shifting peak loads.
The guidance explains that, compared with gas boilers, heat pumps require a more detailed and accurate understanding of the heating and cooling demand. Oversized heat pumps can suffer from lower efficiencies, so correct sizing is essential for efficient operation that meets the building’s needs. This requires appropriate investigation, preferably from contemporaneous records or measurements of the thermal loads. Among the comprehensive and accessible coverage of heat pumps the recently published – and freely downloadable – CIBSE AM17 Heat pump installations for large non-domestic buildings notes that a load survey would ideally be based on continuous metering data.
Unlike gas-fired boilers, the performance of air source heat pumps (ASHPs) will be highly dependent on the source temperature – typically the outside air – and the LTHW flow temperature. So, for example, the monobloc heat pump shown in Figure 1 has a performance as described in the chart of Figure 2.
Monobloc heat pumps
A monobloc air source (to water) heat pump has all its components in a single enclosure, as shown in Figure 1, which is typically located outdoors. It includes the compressor, condenser, expansion device, evaporator and controls. Hot water is produced as return LTHW counterflows with the high-pressure, high-temperature refrigerant across the plate heat exchanger, which forms the condenser.
Insulated LTHW flow and return pipework, power, and control connections need to be made to the heat pump. All refrigerant components are part of a closed pre-charged circuit, all within the enclosure of the unit, and do not require F-gas-qualified technicians for installation
The range in the coefficient of performance (COP) is such that, even at the lowest outdoor temperatures, it would indicate that, in carbon terms (based on 2022 UK carbon factors of 0.193kg of CO2e per kWh of electricity and 0.183kg per kWh of gas), it is still more effective to employ a heat pump rather than a natural gas condensing boiler. Currently, commercial UK electricity prices are approximately three times that of natural gas per kWh. This would mean that, in simple terms, for this example heat pump to be cheaper to operate than a 92%-efficient condensing boiler, the outdoor temperature would need to be higher than around 7°C.
As noted in Heat pump retrofit in London,1 the LTHW flow temperatures required to meet the building heat loads can be reduced through a combination of reducing heat loss through energy efficiency improvements and upgrading heat emitters – for example, through larger or fan-assisted heat emitters. Every 1K reduction in flow temperature can increase heat pump efficiency by approximately 1.5% to 3%. This water flow temperature is a key variable, and there can be great benefit from careful consideration of the real needs of the building and the actual flow water temperature required – which might be quite different from the historic use.
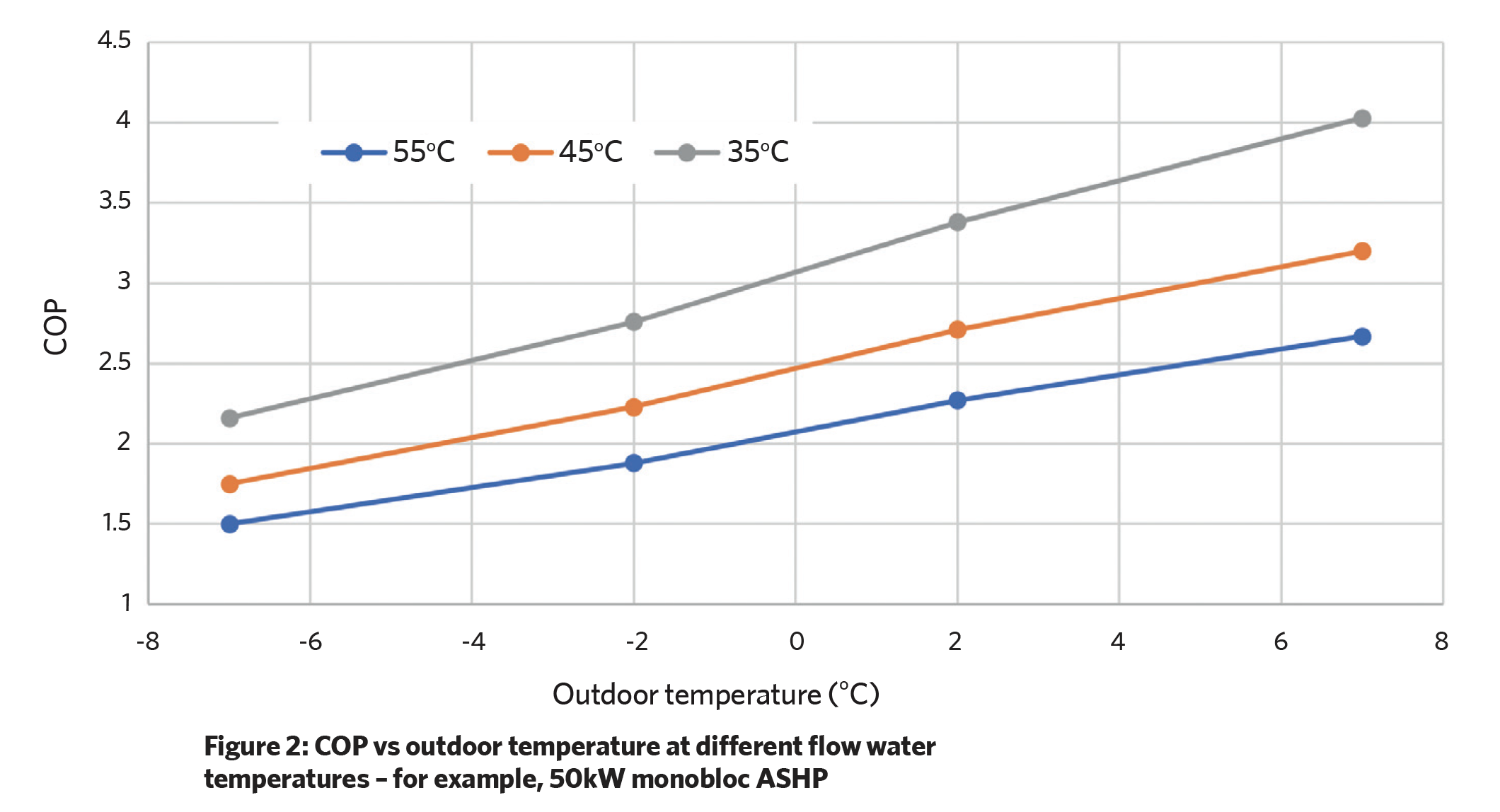
On the refrigeration side of the heat pump, the refrigerant condensing temperature is likely to be 2K to 4K warmer than the flow water temperature, and the evaporating temperature likely to be 5K to 8K cooler than the outdoor air temperature. For ASHPs, there are limited opportunities to provide sustained increases in the source temperature, although there may be a chance to benefit from a local warm air discharge from a process or other environmental system. AM17 highlights that ASHPs using common refrigerants (such as R32 with a relatively low global warming potential [GWP] of 675) typically produce water at a maximum of between 55°C and 60°C, with an outdoor temperature of -5°C.
ASHPs are designed to operate within a specific range of load flow-return temperature difference that, for many mass-produced heat pumps, is about 5K. At higher differences, the counterflow plate heat exchanger, which is used as the condenser in the heat pump, can become less effective. Specialised heat pumps, larger-scale industrial heat pumps, and heat pumps using ammonia or CO2 are all capable of working at a greater difference. The manufacturer’s recommendations will determine the most effective flow-return temperature difference.
As the outdoor air temperature rises, so does the heating efficiency and the capacity of an ASHP; at the same time, the space-heating loads will decrease. If an ASHP is sized for peak load it will be oversized for the majority of the operational life. In capital terms, heat pumps are significantly more expensive than direct electric solutions, such as electrical backup heaters, or – possibly already existing – gas boilers.
In many cases, there is a good case to employ a ‘bivalent’ system where a complementary heat source will be used in conjunction with the heat pump to provide additional heat during the relatively few periods of peak load, or to lift the temperature of the LTHW beyond the efficient limits of the heat pump. In building refurbishment projects, this could be the existing heat source, such as a gas boiler.
The heat pump would normally be the primary system that contributes a larger part of the annual load, with the secondary system – the gas boiler, direct electric heater, heat network or other renewable source – supplying the remainder of the peak load or increasing the flow water temperature when required. Relatively low-cost thermal stores can also be employed to spread the load across the day, so reducing the required peak output from the heat pump – but, in themselves, they cannot increase the LTHW flow temperature.
AM17 provides guidance on control systems for heat sources, suggesting that they can be configured to prioritise heat sources based on carbon intensity or operating cost. It is crucial for the control strategy to ensure that the bivalent system operates as intended. The recommended approach is to activate the priority heat source first – typically the heat pump with the highest efficiency and lowest operating cost – to meet the heat demand.
The secondary heat source should only be activated when the priority heat source cannot adequately meet the required load. This trigger point can be determined, for example, by monitoring the temperature sensor of a thermal store to detect if stored heat is depleted.
As soon as the priority heat source is capable of meeting the load, such as when the thermal store is suitably charged, the secondary heat source should be deactivated. Depending on the load profile and emitter requirements, certain heat pump configurations may benefit from adjusting the temperature at the condenser.
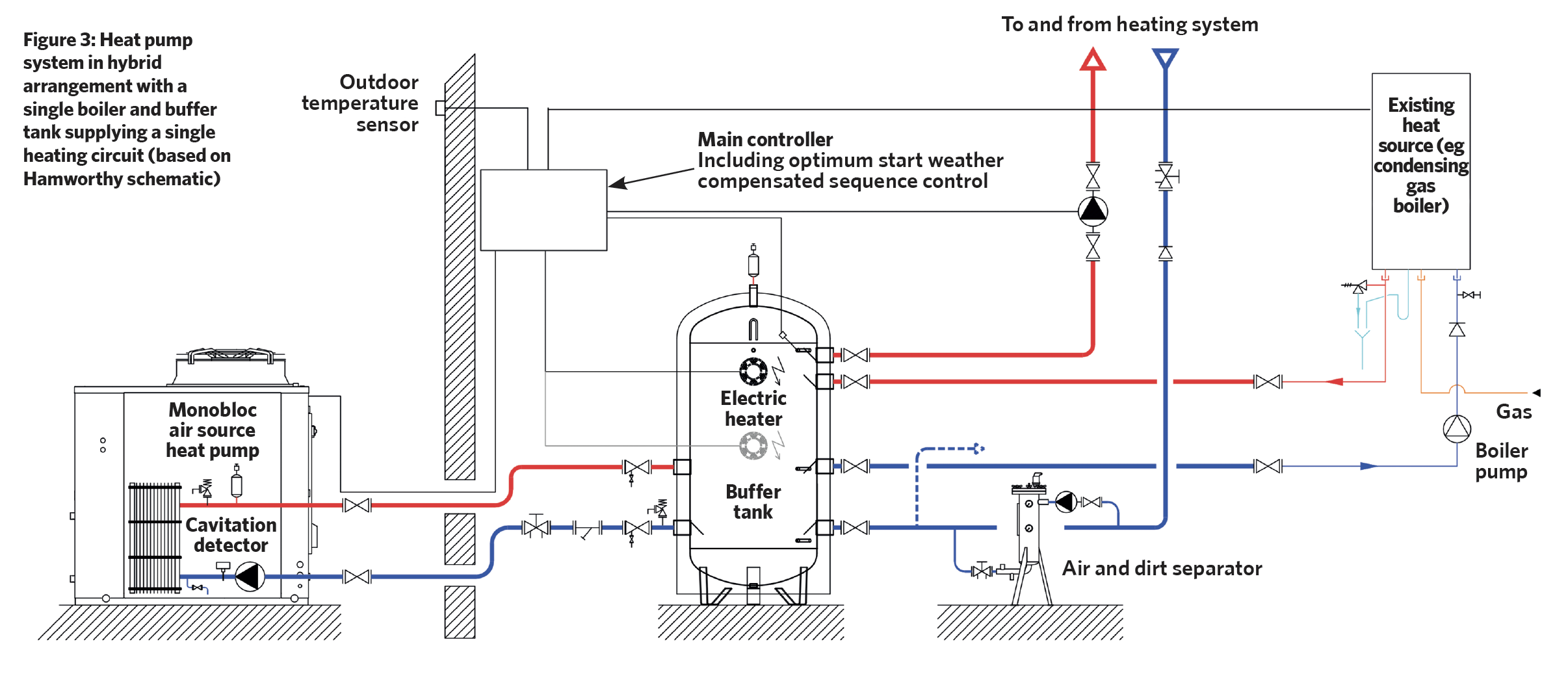
For instance, during periods of low load, heating emitters may be able to function effectively with a lower LTHW temperature, which may be controlled by weather compensation. On the other hand, higher LTHW temperatures might be necessary only for short periods, such as when charging or pasteurising a domestic hot water (DHW) store.
Manufacturers’ tests to BS EN 14825:20182 provide information to compare products and evaluate the performance of various technologies under part-load conditions. However, it is important to note that these seasonal efficiencies should not be used for calculations specific to a particular building application, as the building loads often deviate from the standard assumptions of BS EN 14825.
Designers are advised to compute the seasonal efficiency by taking into account the particular building load and heat pump choices. To determine the portion of the load that can be fulfilled by a heat pump, an hourly model can be employed.
It is important to conduct a thoughtful evaluation of factors that may introduce uncertainty in the projected loads. The manufacturer’s published COPs should be combined with the building load profile and local weather data to obtain an accurate understanding of the heat pump’s seasonal efficiency for a given application.
If a gas boiler is chosen as the secondary system, fluctuations in fuel prices or future price changes could make the secondary system more cost-effective to operate than the primary system. This requires diligent monitoring and policy decisions to strike the right balance between cost and emissions. Adding excessive safety margins to load calculations can result in oversized heat pumps and, particularly where there is no thermal buffer, this can result in short-cycling (frequent on-off switching) of the heat pump, leading to reduced efficiency and accelerated equipment deterioration.
An example of a simple refurbishment application is provided in Figure 3, where a buffer tank is employed to allow the heat pump to act as the lead heat provider for a weather compensated LTHW system that supplies a thermally upgraded building and heating system. A key role of the buffer tank in Figure 3 is to hydraulically decouple the heat pump from the remaining LTHW heating system, as well as providing a thermal buffer to prevent excessive cycling of the heat pump.
Although often identical in shape and form, a ‘thermal store’ would be larger than a buffer vessel and is used to enable a relatively small low carbon heat generator, such as a heat pump, to meet a larger proportion of the annual load (and usually incorporates the functions of a buffer vessel within it).
As noted by Palmer in CIBSE AM15,3 the important distinction between these two terms is often blurred, with the term buffer vessel frequently being indiscriminately used to describe any form of water vessel attached to a heating system
Any hybrid system where the requirement is for a higher flow temperature than the ASHP can provide must be carefully controlled so that the system return temperature from the boilers does not exceed the heat pump maximum flow temperature. The gas boiler may be used at times when peak loads cannot be satisfied by the heat pump or where higher temperatures are needed for DHW calorifier pasteurisation. The electric heater provides backup in case of failures.