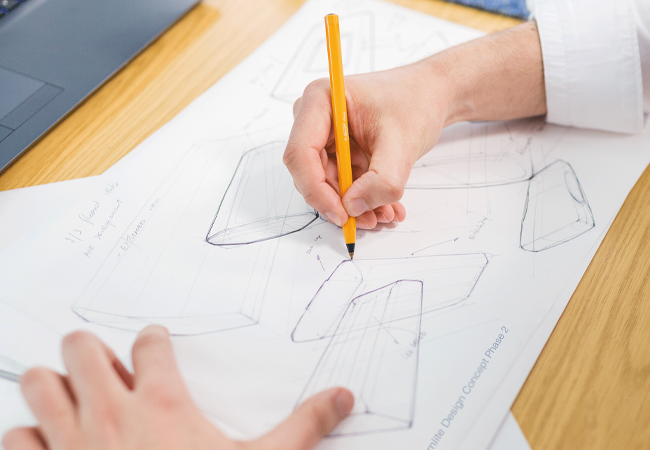
Driven by the global evidence of ‘climate crisis’ and, more domestically, by rising energy costs and the impact of inflation on building operation, building users, owners and designers are increasingly appreciating the need to improve effectiveness and reduce the environmental impact of building systems. To succeed in engineering built environments that are more efficient – both in terms of resources and performance that will be less detrimental to future generations – requires a holistic consideration of the provision of the whole building, not least the luminaires that are employed in the lighting designs. This CPD will reflect on the recent guidance that points towards a more effective circular economy, and introduce an innovative methodology to rate products for circularity.
Recent CIBSE publications have outlined the concepts and practicalities of assessing embodied carbon and creating a circular economy for building services systems. CIBSE TM65 Embodied carbon in building services: a calculation methodology, published in 2021, provides an introduction to whole life carbon and embodied carbon, and delivers guidance on actions that can reduce the embodied carbon emissions of mechanical, electrical and plumbing (MEP) equipment. As well as providing guidance on standardised environmental product declarations (EPDs), it includes a method to assess the embodied carbon of MEP products where there is no reliable published information.
The 2022 CIBSE TM66 Creating a circular economy in the lighting industry provides a background to circular economy principles and sets out the drivers and barriers to its adoption. It notes that previous practices and models have involved ‘take, make, use and waste’ – a linear economy with no real way of recycling or recovering materials at end of life. The model has developed to incorporate recycling at the end of the line; however, practically, this just results in delaying the point at which luminaires are disposed of.
The commentary in TM66 explains that a product’s embodied carbon and its circular economy performance are separate but linked. A luminaire with low embodied carbon is not necessarily circular economy-capable; however, by adopting the tenets of the circular economy it will very likely reduce carbon emissions. TM65 reports that a large proportion of embodied carbon from building services engineering systems is associated with the product stage (designated as sections A1–A3 by BS EN 15978:20111) because of the constituent metals, electronics and plastics involved, as well as a complex supply chain – this is wholly apposite for many luminaires. This product stage includes the carbon emissions associated with extraction, transport and processing of materials, and the energy consumption used to manufacture the product. The Ellen MacArthur Foundation2 has popularised the pressing need for action, in part with the much-copied butterfly diagram – a part of which is shown in Figure 1 – that indicates the various paths that may contribute to a product’s circularity.
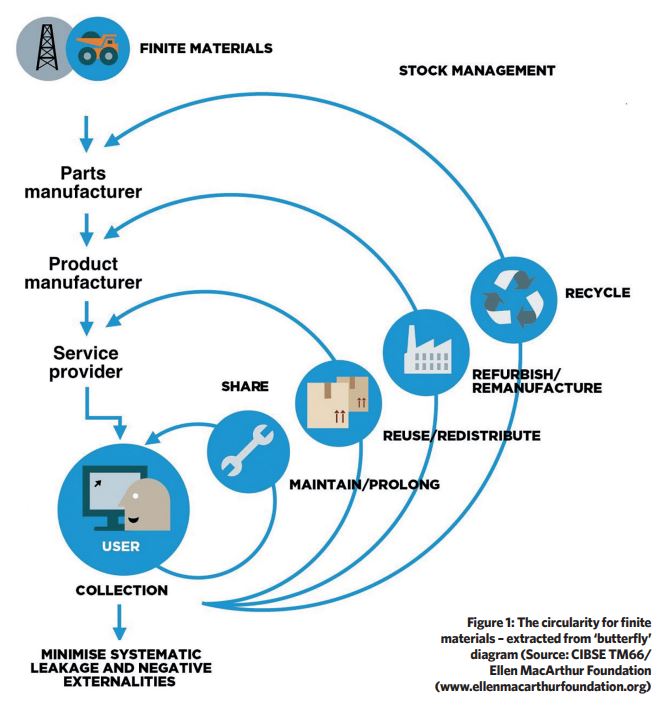
TM66 notes that a ‘product that is manufactured thousands of miles away, in fossil fuel-powered factories, and air freighted to site may have high [embodied] carbon but, providing it is designed and supported so that it can be reused, remanufactured and repaired, then it may be circular economy-capable’. As with any commodity, reducing consumption will reduce direct carbon impact – so, at its simplest, using fewer luminaires through properly considered design may provide the most effective method of lessening the environmental impact of a system. Luminaires should extend beyond their traditional life-cycle, which, ideally, will include opportunities for reuse. If not complete reuse, then parts need to be able to be recovered and used either in the next installation or kept in situ, with a few updated parts added. If not recovered, then, at the bare minimum, there needs to be proper opportunities to recycle – meaning that the materials (and components) used to manufacture luminaires should be readily recyclable. Products should be designed such that they can be repaired, modified, upgraded, reused or, at the very end of life, disassembled for component recovery. It is vital to understand that design is not limited to product design alone —systems, services and platforms are required to allow a luminaire to be repaired, modified, upgraded, reused or, at the very end of life, undergo component recovery. For example, if there are logistics in place to deliver the luminaire to site, reverse logistics must be in place to recover it.
Markedly, in his article3 providing an overview of TM66, Bob Bohannon, immediate past president of the Society of Light and Lighting, remarks that, although the waste electrical and electronic equipment (WEEE4) recycling regulations have been in force for more than 15 years, the vast majority of lighting marked as recyclable is sent to landfill, with only an estimated 7.5% recovered under WEEE. He bemoans that any value in the old luminaire is literally shredded to recover materials – a process that requires energy to melt them down for reuse. TM66 provides a simplified, notably circular, development of the circular economy model – as shown in Figure 2 – that it notes as a much truer model of the circular economy: ‘make, use, return’, where luminaires go back to the manufacturer to be refurbished, upgraded or remanufactured as more luminaires or, at worst, for component recovery.
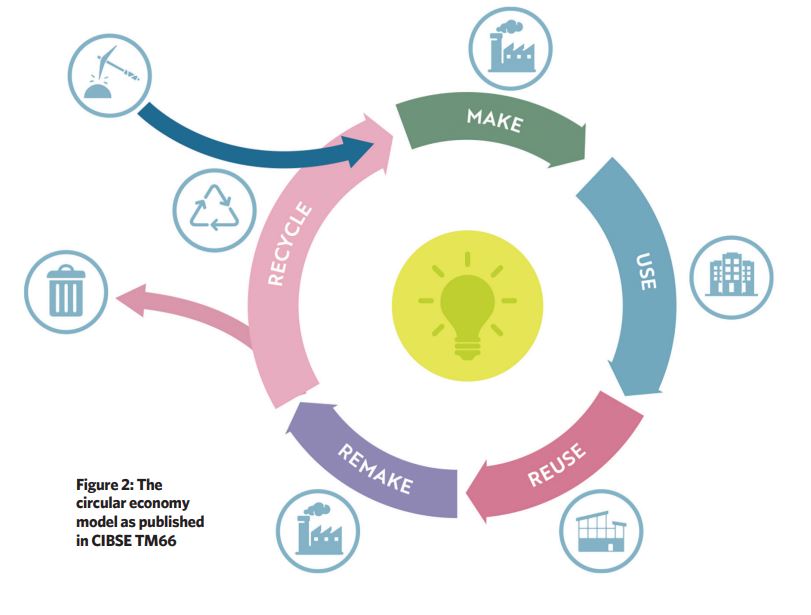
The luminaire marketplace has been transformed in the past 10 years with the advent of low-cost, high-efficiency LEDs. LEDs undoubtedly provide great opportunity to deliver lower operating energy use and cost, and increasingly lower capital cost compared with predecessor technologies. They also have extremely long claimed lifespans compared with other lighting technology. New LEDs might last from 50,000 hours up to 100,000 hours, compared with, for instance, fluorescent lamps at approximately 10,000 hours. However, this will be highly dependent on the design and quality of the LED, and the heat sinks and driving electronics. For example, the life of the capacitors in the power supply can be foreshortened with increased temperatures and so the failure of an LED luminaire may be ultimately down to a component that costs a few pence and, in itself, has a small carbon footprint. The popularity and promise of integrated LED luminaires has provided the opportunity for novel, compact and high-performing products. However, the disadvantage of such products is that when the LED – or any of the integrated components – fails, the whole unit needs to be replaced. Designers need to carefully assess the benefits – normally, extended lifetime, efficient, simple replacement, and novel (and often compact) design – against not being able to reuse the components (such as drivers, optics and LEDs), potential increased waste, and the likely higher capital cost. BS 8887-220:2010 Design for manufacture, assembly, disassembly, and end-of-life processing (MADE) provides the standard for remanufacturing to change a used product into an as-new product. While BS 8887-220 states that ‘the new product must have equivalent performance and warranty of a comparable replacement product’, TM66 notes that there may be occasions when the reuse of a mid-life LED fitting will be acceptable even when its lumen output may have depreciated, making it of lower output than new, but still fit for purpose when used in a considered way.
examples of practices that can improve luminaire's circularity
LED luminaires should be designed to be repairable and capable of remanufacture, to allow easy access and replacement of components that are likely to fail during the life of the luminaire. Ideally, unless specifically required, superfluous detail should be minimised to avoid impact from changes in fashion and to improve opportunities for eventual reuse.
Individual products can be allocated a unique identifier that should be permanently affixed – for example, employing QR codes, near field communication (NFC) or simply a readable URL on each luminaire (or major component). This can provide a link to access a myriad of internet-connected resources, such as component drawings, manufacturer upgrades, and sources of spares and enhancements.
Products can be manufactured with extra fixing holes to allow subsequent use of different component types as technologies evolve.
Where feasible, a local resource ecosystem for design and component manufacture can significantly reduce the carbon footprint of a product, as shorter distances mean reduced transport-related energy consumption and greenhouse gas emissions. TM66 reports on a building refurbishment where the manufacturer transported linear fluorescent luminaires fewer than 40 miles to the factory and upgraded them to LED without compromising light quality and efficiency, and each luminaire was significantly cheaper to manufacture than new light fittings.
Intelligent use of materials, such as by using hollow extrusions (or, potentially, additive manufacturing techniques) rather than subtractive machining, can reduce resource use. The increasing availability and greater variety of bioplastics, including corn starch-based polycarbonates with excellent optical properties, can provide a lower environmental impact and higher performance than traditional materials.6 It is also available as a feedstock for additive manufacture.
Additive manufacturing (3D printing) can be employed (using ‘STL’ or ‘OBJ’ descriptions sourced through product IDs and internet resources) to create components that are no longer stocked by the supplier, or possibly used to provide a transformation element for new components. The utility and flexibility of additive manufacture has been shown7 to reduce the carbon footprint of a ‘typical 3D-printed luminaire’ (excluding electronics and optics) by 75% compared with a conventionally manufactured metal luminaire. This is because of their modular design that employs fewer and less-complex parts that are made from a single, low-mass material.
For components that are unlikely to be reused, materials such as aluminium can be used, which can eventually be recycled without losing any of its properties.
By employing networked control for lighting installations, luminaires can self-report their condition so that maintenance can be optimised and residual life logged, which can inform the opportunity for reuse when building systems are refurbished.
The Circular Economy Assessment Method (CEAM) illustrated in TM66 employs accompanying Excel spreadsheet tools to steer manufacturers towards improved product circularity, as well as providing specifiers and clients with understanding of the questions they need to ask. The Circular Economy Assessment Method for manufacturing (CEAM-Make) employs an Excel spreadsheet comprising 66 questions under four tabs – product design, manufacturing, materials and supporting ecosystem – to assess a luminaire’s circular economy performance. By adding the specific product answers, products are given a rating of zero to four, as shown in Table 1, with the spreadsheet tool allowing iterative inputs to encourage and enable manufacturers to improve the rating. The baseline for a product is zero, with the intent to encourage and enable products and supporting ecosystems that score three or four.
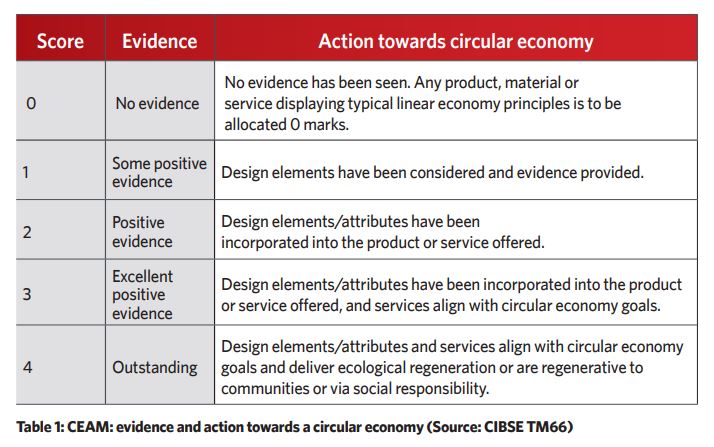
However, manufacturers or suppliers may make generalisations, ‘greenwash’ products, or deliver unintended outcomes. The CEAM-Specify is a specifier support tool that may also be useful for manufacturers at the early stages of product design, providing a triage tool that highlights key issues with a product. The tool references the CEAM-Make tool, but provides a less-detailed set of 24 questions that, for example, can allow a relatively swift comparison of two or more products.
This can be applied to support decision-making when embarking on a new or existing project that is seeking to implement circular economy principles and products. It can also be used as a checklist to inform understanding and change.
There are several case studies included with TM66 that illustrate that the realities of a circular economy are not simply lofty ambitions for a better future world, but provide examples that are already taking place. Drawing on those case studies and from other industry documents, it provides some examples of good practice that contribute to a product’s circularity, as shown in the boxout, ‘Examples of practices that can improve a luminaire’s circularity’.
The accelerated adoption of circular principles is likely to be informed from the large body of work that is being developed to advance the EU’s Sustainable Products Initiative.5 The UK government’s 2021 strategy document Net zero strategy: build back greener clearly lays out a future where a circular economy will be part of everyday life: reusing, repairing and remanufacturing goods will be standard practice, with producer responsibility schemes embedded across the economy. The government’s worthy intention will undoubtedly need the ingenuity, engineering acumen and organisation of an enthusiastic and well-informed lighting industry to have any real prospect of success.
About the author Tim Dwyer 2022.
Further reading:
BS 8001 Circular economy provides a practical guide to the implementation of the principles of the circular economy in organisations.
References:
1 BS EN 15978:2011 Sustainability of construction works. Assessment of environmental performance of buildings. Calculation method, BSI 2011.
2 bit.ly/CJOct22CPD21 – accessed 6 September 2022.
3 Bohannon, B, ‘Virtuous circle’, CIBSE Journal December 2021 p44.
4 bit.ly/CJOct22CPD22 – accessed 6 September 2022.
5 bit.ly/CJOct22CPD23 – accessed 6 September 2022.
6 bit.ly/CJOct22CPD24 – accessed 6 September 2022.
7 bit.ly/CJOct22CPD25 – accessed 6 September 2022.
By participating in this CPD module, you consent to sharing your details with Tamlite. Tamlite may contact you via email and/or telephone with further information and technical insight on its services. You have the right to opt out from such communications at any time.
I understand that I will receive marketing communications from Tamlite after completing this module (please tick here):
By entering your details above, you agree that CIBSE may contact you with information about CPD and other training or professional development programmes, and about membership of CIBSE, if you are not a member.
Go to www.cibsejournal.com/cpd to complete this questionnaire online. You will receive notification by email of successful completion, which can be used to validate your CPD records. Alternatively, fill in this page and post it to: N Hurley, CIBSE, 222 Balham High Road, London, SW12 9BS.