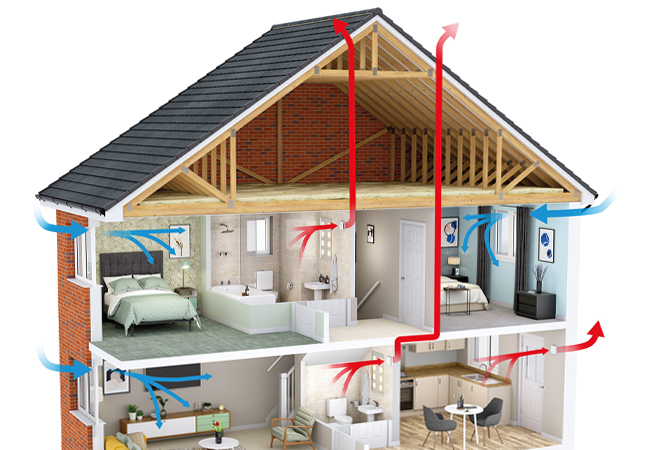
Following the recent consultation document on the England Future Homes Standard, the UK government introduced revised England Building Regulations in December 2021, with the interim aim that new homes planned from mid-2022 will include adequate ventilation as well as producing 31% fewer emissions. As part of the package of new regulations, there was a separation of the previous Approved Document (AD) F into a new volume 1 for dwellings and a new volume 2 for buildings other than dwellings. This CPD will focus on the provisions developed to help ensure suitable ventilation for new homes.
Inadequate ventilation in homes will produce a miscellany of effects, ranging from the immediate manifestations of condensation, through to the undesirable impacts on the occupants from a cocktail of airborne contaminants.
These may be emitted from the fabric and furnishings, as well as resulting from the everyday processes and products used when living in the space. Many impacts will be challenging for building occupants to identify, but a poorly ventilated home can directly adversely affect health through poor indoor air quality (IAQ) and create delayed, possibly long-term, problems such as mould.
This is starkly illustrated in Figure 1, and frequently cited in cases considered by the Homes Ombudsman1 (although significant numbers of mould cases result from, in part, deficiencies in the building construction or maintenance procedures).
There have been many studies and reports that have contributed to the knowledge and understanding of the role of building air tightness and ventilation strategies on building performance. Work undertaken by Crawley,2 based on the airtightness of newly constructed UK dwellings (investigating a large dataset collected to meet the requirements in the Part F 2010), found that the ventilation strategy appeared to make little difference to the airtightness of homes.
For dwellings featuring mechanical ventilation with heat recovery (MVHR), the results suggested that infiltration levels are too high to maximise the energy savings; and for those naturally-ventilated homes, there may be air quality issues. The overall data indicated little practical difference between houses built for MVHR and those for natural ventilation – with both sets hovering around the air tightness figure of 5m3.m-2.h-1 @ 50Pa.
In that same work, there were some disappointing findings (drawn from an earlier dataset) that might be reasonably interpreted as indicating that many new homes were ‘caulked up’ for the purposes of meeting an airtightness test rather than being inherently designed and constructed to perform effectively. Crawley concluded that ‘coupling airtightness design and ventilation strategy can reduce a dwelling’s energy demand and can support achieving the required energy performance rating’.
In 2016, Zero Carbon Hub (ZCH) published3 an informative catalogue of real-world observations that, despite the sad demise of ZCH, lives on as record of deficient home ventilation installations. This includes examples of the number and performance of installed trickle ventilators not working in harmony with the installed systems (that is, natural, mechanical or MVHR); illustrations of excessively long, poorly supported, flexible ducting that inevitably leads to higher system pressure drops and increased noise; inappropriate and inadequate commissioning of ventilation systems; and poorly labelled controls and inadequate handover instruction for end users.
The report highlighted that a lack of detailed specification and detailing had resulted, in some cases, of ‘improvising on site (with no consultation back to the designer)’ and some checking of systems being done ‘by ear’, using noise levels as the guide to performance, not flow rates.
Homes in occupation and operation have been similarly found wanting in the practical operation of ventilation. A key preparatory study undertaken by Aecom4 that contributed to the development of the Future Homes Standard covered 80 occupied homes – 55 naturally ventilated and 25 with decentralised mechanical extract ventilation – that had been constructed after 2010 to meet the requirements of Part F 2010, and which were studied across the winter period 2015-16.
Although considering a relatively small sample of homes over a single quarter of a year, the findings were able to reveal some significant concerns; 30% of the tested homes with continuous mechanical extract were not maintaining recommended IAQ performance standards.
Further analysis suggested that this resulted in part from the relative position of trickle ventilators causing short circuiting of airflow to the room extract grilles, and that the standards set by Part F were not, in themselves, inadequate. In the naturally ventilated homes, the location of trickle ventilators was again identified as being a significant contributor to poor performing ventilation and the resulting poor IAQ. Trickle ventilators that were obscured – often at night – behind closed curtains were considered as being the likely culprit leading to relatively high levels of carbon dioxide (CO2) and total volatile organic compounds (TVOC), particularly in bedrooms, driven by the relatively low air-change rates.
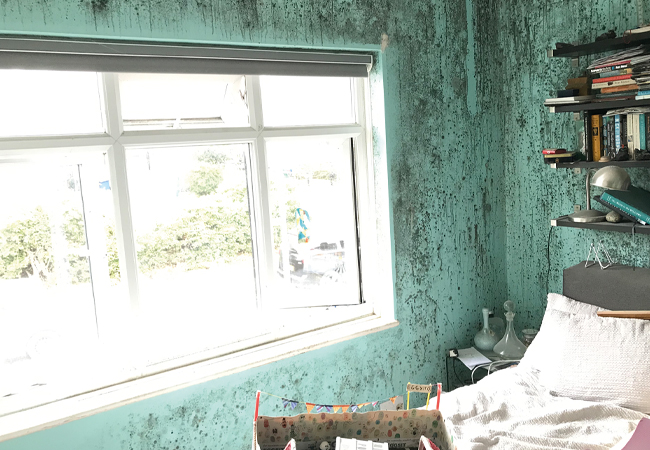
Figure 1: Extreme example of the consequences of poor ventilation in frst-floor bedroom when room was closed up for 12 weeks during ground-floor building works in winter 2021-22. A trickle vent in the top corner had been previously plastered over (Photo source: Martin MacDonald)
Additionally, the report highlighted that noise from extract fans resulted in occupants choosing not always to switch them on when they were needed, which could potentially lead to the consequences of long-term under-ventilation. In locations with high external sound levels, there was a tendency for occupants to close (or obscure) trickle ventilators to reduce the ingress of noise, so reducing the home ventilation rate.
The development of the new AD F volume 1 20215 (AD F1) was driven, at least in part, by such deficiencies described above, with an overall aim ‘to protect the health of occupants of the building by providing adequate ventilation’. It was widely considered that the ventilation rates of the previous Part F would have likely been adequate if the installation and operation had followed through the intent. (See boxout ‘Understanding AD F1 2021’.) The important, relatively discreet, updates in AD F1 integrate with the desire to make the requirements clearer and more useable, and to align with the demands presented in the complementary ADs. So, for example, AD F1 ensures sufficient levels of ventilation are provided despite the more stringent building airtightness requirements of AD L1.
The categories of ventilation are now simplified into three main types. Passive stack ventilation and natural ventilation without the use of mechanical extract are no longer specifically included. The first system type described in AD F1, natural ventilation with background ventilators and intermittent extract fans, might be considered as reasonably traditional for UK housing but is deemed as only applicable for new dwellings with a design air permeability higher than 5m3.m-2.h-1 @ 50Pa (or 3m3.m-2.h-1 @ 50Pa as built), referred to as a ‘less airtight dwelling’. (Practically, this means that it will not suit most new homes, as otherwise they are likely to struggle to comply with energy-related regulations.)
UNDERSTANDING AD F1 2021
As with all regulations and standards, there will be some interpretation required for the new AD F1, the need for which may not become obvious until the new ADs are applied to design, installation and operation. It is important to review the ADs directly to understand the detail (and they are freely available at www.gov.uk/government/collections/approved-documents). However, a
useful general side-by-side comparison of the requirements of AD F1 2021 with the previous requirements may be seen at www.titon.com/uk/building-regs-update.
Background ventilators are required with significantly greater equivalent area than in the previous AD F, which – together with higher whole dwelling ventilation rates, and more specific requirements for room by room ventilator distribution and position – should make compliance more straightforward.
The opportunity for cross-ventilation should be taken, if available, and noise attenuating background ventilators are recommended where there are high external noise levels –previously the problems of noise were focused on mechanical systems.
Highly airtight buildings require one of the remaining two system types. The first of these is continuous mechanical extract ventilation (MEV), which comprises a central extract system or individual room extract fans or a combination of the two, with a prescribed minimum equivalent area of background ventilators for each habitable room (except wet rooms). The required area for background ventilators has been significantly increased in this revision.
The intermittent and continuous extract rates remain the same as the previous AD F; however, there is a 50% increase in the required minimum whole-dwelling ventilation rate.
The final system, MVHR, explicitly rejects the use of background ventilators (to prevent uncertain airflows).
Beyond those systems described in AD F1, alternative means of ventilation are allowable, but they need to be demonstrated to be meeting the requirements of AD F1.
Additionally, the requirement for purge ventilation, used to rapidly dilute indoor air pollutants and extract water vapour where necessary – often done by opening windows, but which can also be provided mechanically – remains unchanged. However, the new AD O6 may require a higher purge ventilation rate to control overheating and so will need cross-checking.
There is now a complete section devoted to commissioning and the provision of record information. Key administrative inclusions are the provision of a permanent evidence of performance, and to produce a record of the operational system intent, methods of use and maintenance. In addition to the operating and maintenance instructions a ‘home user guide’ will need to be prepared and provided for new dwellings.
This will contain a section on ventilation that gives non-technical advice on the ventilation systems, including some basic details on how to operate and maintain the home in a healthy and energy-efficient manner. A basic template7 is provided for this guide, and is described more fully, in AD L1.8
There are subtle changes in performance requirements, such as the change in the reference value in allowable noise to 45dB LAeq,T in less noise-sensitive rooms (for example, kitchens and bathrooms) when a continuous operation system is running at the minimum high rate or an intermittent operation system is running (previously it was 35dB LAeq,T for a mechanical ventilation system on its minimum low rate).
AIR BRICKS FOR CONTROLLED VENTILATION
The humble ‘air brick’ – which has typically been associated with the ventilation of otherwise unventilated and unoccupied spaces such as underfloor voids, cavity walls and disused fireplaces – is increasingly being employed as a mechanism to enable intakes and discharges for designed natural ventilation, mechanical ventilation or MVHR applications. As the name suggests, the air brick typically fits into one or two courses of bricks, often keyed to ensure a robust bond with the brickwork. Air brick materials have evolved from the traditional terracotta (with its practically limited dependable equivalent ‘free’ area) to cast iron, plastic, and, most recently, powder-coated steel (such as those shown in Figure 2).
Although these may be used simply as background (or trickle) ventilators, the steel ‘mechanical air brick’ is designed as a robust, low pressure drop ventilation grille, so that it can connect soundly with matched ducting, as in the example in Figure 3, to provide an air path for natural ventilation or for any form of mechanical ventilation, including ducted MVHR, central MEV and purge systems. As with any properly installed air brick, they will restrict the ingress of external insects and animals and provide weather protection. To comply with England Building Regulations for fire safety, appropriately powder-coated (fire-rated to A2-s1, d0 – non- or limited combustibility, little or no smoke, with no faming droplets), non-combustible (A1) steel constructions will meet requirement B4 of AD Part B9 for external walls (and AD Part 710 for materials and workmanship) regardless of whether they are employed in walls above or below 18m from ground level. Steel air bricks are available as single bricks, brick-and-a-half and double bricks, with a variety of depths to accommodate a range of wall thicknesses.
Air pressure drops through the steel air bricks are commensurate with metal louvres of similar dimensions.
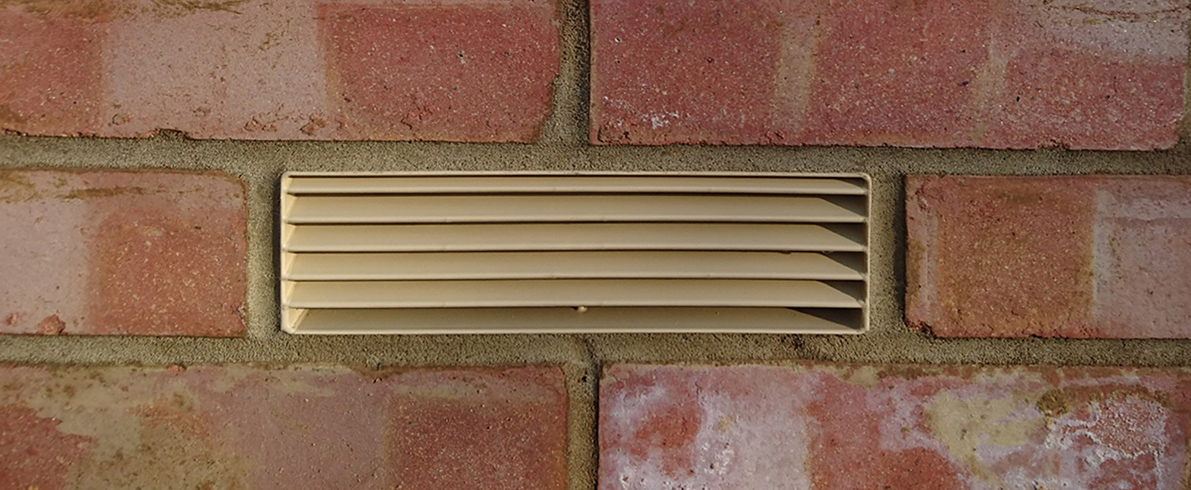
Figure 2: Examples of powder-coated steel ‘mechanical airbrick’ (Source: Titon)
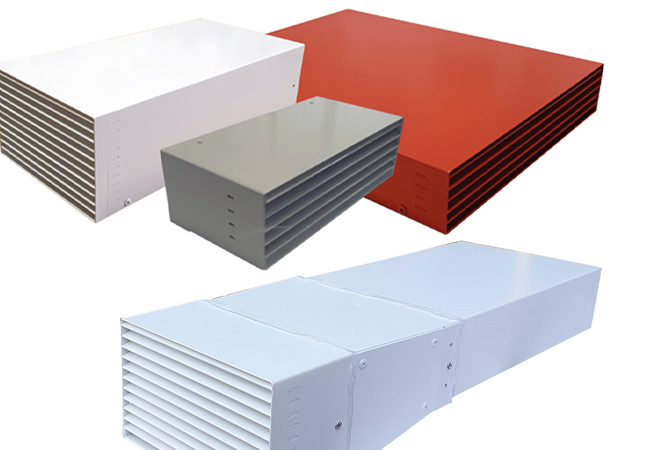
Figure 3: Steel double air brick with extension to connect to ductwork system (Source: Titon)
Ventilation ductwork is now required to be constructed of rigid ducts, wherever possible, to reduce noise and energy consumption (compared with flexible ductwork). Flexible ductwork, where installed, should only be used for final connections and have a maximum length of 1.5m – this is a significant change.
AD F1 2021 provides a useful tool to help deliver homes that are appropriately ventilated and, so far, has not excited the same heated debate as recent changes to other ADs. The clarified and enhanced interpretation of prescriptive requirements, as well as the more explicit description of ventilation performance, will – it is hoped – lead to more robust system designs that are installed appropriately and that can be operated reliably to deliver good dwelling air quality.
© Tim Dwyer, 2022.