As the impact of climate change1 becomes increasingly evident across the globe, with unseasonable weather patterns driving droughts and storms, and scenes of uncontrollable fires and flooding become more common, there is growing public concern2 that action is needed. In just over a month’s time, high-level negotiations will take place at the 26th Conference of the Parties (COP26) of the United Nations Climate Change Framework Convention in Glasgow, that will set trajectories for long-term change. This will further heighten public awareness and undoubtedly accelerate governmental activity. This is, of course, not news to the building services community who – partly driven by regulatory requirements (such as the Energy Performance of Buildings Directive) – have already seen significant reductions in the potential environmental impact of buildings, equipment and consumables. However, increased public – and client – awareness of both climate change and the need for well-ventilated spaces is likely to further raise interest in inspecting and maintaining air conditioning systems.
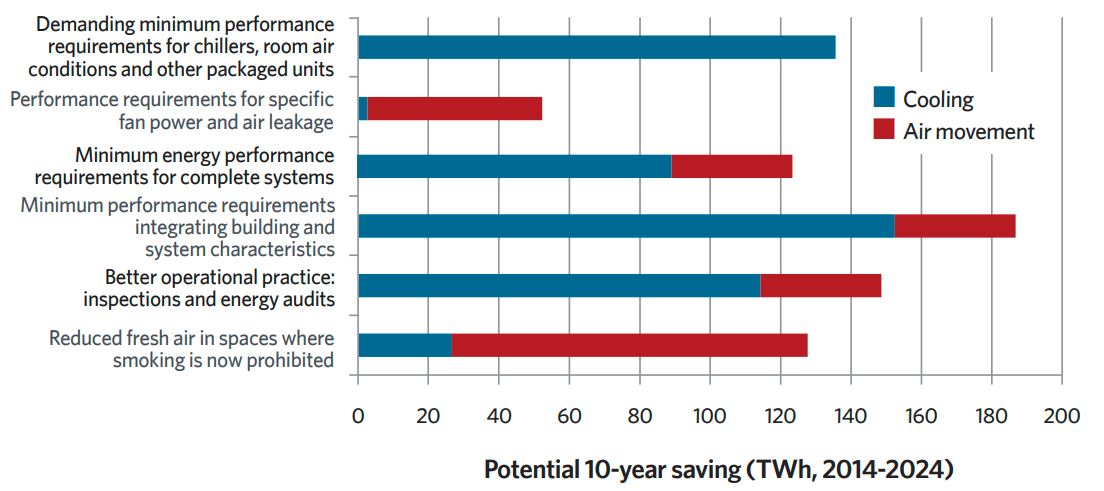
Figure 1: Realisable 10-year savings, 2014-24, from interventions to ‘business as usual’ in European energy consumption for air conditioning3
Analysis undertaken, and reported in the detailed paper by Hitchin et al,3 that was produced from extensive research and modelling in 2014 – and is illustrated in Figure 1 – predicted that the largest realisable energy savings would be from adopting integrated minimum performance requirements for buildings and systems.
These may be enacted through the demands of building regulations and standards, and require realistic simulations to optimise the building and system at the design stage. The second largest potential saving was predicted to come from better operational practices deriving from inspections and energy audits. This was closely followed by the minimum performance for equipment that has been driven by the various global ‘ecodesign’ standards, resulting in manufacturers producing higher performing equipment such as the variable refrigerant flow (VRF) system shown in Figure 2.
Across the whole of the UK (and the EU) there are statutory obligations and duties of care relating to the operation and maintenance of air conditioning systems. As outlined in the recently published guidance material4 for the Energy Performance of Buildings (England and Wales) Regulations 2012 (amended in 2020 to incorporate into post-Brexit non-EU dependent regulations), the air conditioning system inspection by an accredited air conditioning energy assessor is designed to improve efficiency, reduce energy consumption, reduce operating costs and reduce carbon emissions.
‘Air conditioning’ in this context is considered as being where refrigeration is used to provide cooling for the comfort of the occupants of the building and is for systems in buildings that have an effective combined rated output of at least 12kW. The 2012 revision to CIBSE TM44 – Inspection of air conditioning systems: a guide to EPBD compliance, was originally written to meet the compliance needs of conducting an air conditioning inspection to satisfy the requirements of the EU Energy Performance of Buildings Directive. TM44:2012 still provides a standard reference for the various regulatory authorities across the UK.
It includes methods, checklists and schedules to inform the completion of a standardised set of reporting templates that may then be used to formally lodge a record of the inspection with the appropriate authority.
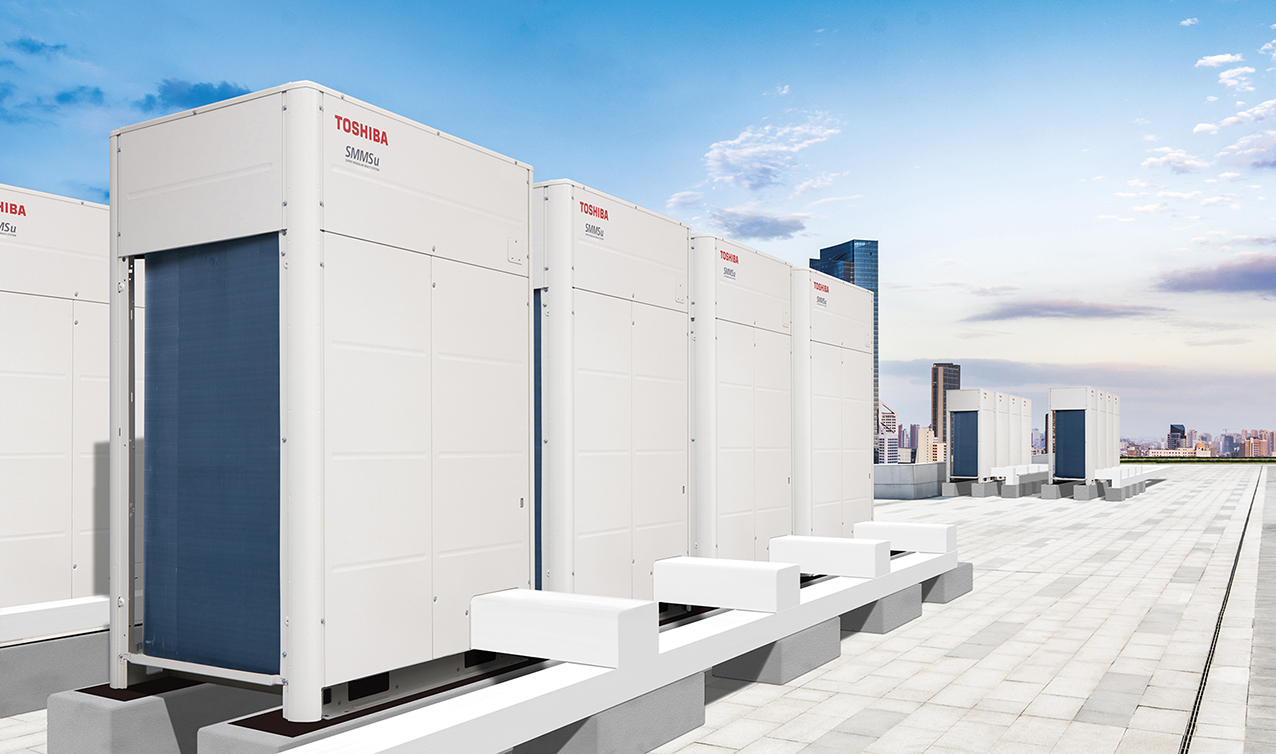
Figure 2: An example of a contemporary variable refrigerant flow (VRF) air conditioning system with a seasonal energy efficiency ratio (SEER) of up to 7.7, and seasonal coefficient of performance (SCOP) up to 4.8 (based on European ratings)
TM44 provides methods for two levels of air conditioning assessment, known as levels 3 (simple packaged) and 4 (complexed central), that are tied to the accredited competence of the air conditioning assessor. Level 3 assessors would broadly be expected to have the capability to inspect packaged air-to-air heat pumps; unitary packaged units, such as ‘through the wall’ units; split units (single indoor unit), and multi-splits (with several indoor units) connected by refrigerant pipework to a single outdoor unit; and VRF systems. Any systems that include a significant distribution of air or chilled water are likely to be categorised as ‘complex’ and require the services of a level 4 assessor.
Guidance for both level 3 and level 4 systems include inspections of refrigeration equipment and associated heat exchangers to ensure appropriate operation and effective heat rejection and distribution. Air moving systems – for example, fan-powered, ducted ventilation systems – are likely to take a more significant place in a level 4 assessment.
This includes all components, starting from the external intake grilles through to the registers (such as grilles and diffusers) that deliver the conditioned air into the space, and embraces all the principal components along the way. The operational procedures and system controls, which may be integrated through building management systems, are assessed in some detail, since they are likely to have a significant influence on the operation of the air conditioning systems.
The building owner or operator would be expected to provide any available documentation for the systems in readiness for the inspection. The quality, extent and accessibility of relevant information provided prior to an inspection of the system has important consequences for the effectiveness and cost of an air conditioning system inspection.
TM44 provides more detailed examples of what information can usefully be provided. Part of the assessor’s work will be to gauge whether the information properly reflects the installed system. Documentation that clearly evidences that equipment and systems are already subject to regular good practice and appropriate checking and maintenance procedures, will potentially allow the assessor to reduce the extent of the inspection.
For the building owner and operator, an inspection should deliver more than simply meeting the statutory requirement, with significant benefit deriving from the knowledge and expertise of the assessor as they highlight how the operation of existing systems can be improved, or identify opportunities to replace older, less energy efficient, or oversized systems. The inspection report would typically include:
- The likely efficiency of the system and any suggestions for improvement
- Any faults identified during the inspection and suggested actions
- The adequacy of equipment maintenance and any suggestions for improvement
- The adequacy of the installed controls and control settings and any suggestions for improvement
- The current size of the installed system in relation to the cooling load and any suggestions for improvement
- Consideration of the capabilities of the system to optimise its performance under typical operating conditions.
Advice may also be given on systems that operate with refrigerants that are being phased out, or may have their use and supply restricted owing to environmental regulations. In these cases, the energy assessor may give advice on possible options for future system adaptation to use other refrigerants, or the need for refurbishment and replacement.
Before enrolling a lay inspector
Before considering site access by a lay inspector, an appropriate health and safety risk assessment should be undertaken and training provided that is appropriate to the site and the expected activity. It is vital that the lay inspector properly understands that access to some areas may require authorisation or specific training because of factors such as exposed moving parts, extreme temperatures, high pressures, noxious gases and other hazards, as well as the direct or indirect risk they pose to others through their actions.
Appropriate personal protective equipment (PPE) would need to be supplied and worn. Lay inspectors must be properly trained so as not to be tempted to open (or potentially make contact with) certain pieces of equipment while they are still operational and, since most systems are automatically controlled, be aware that equipment may suddenly switch on.
The building operator would need to ensure that such activities do not compromise insurance and statutory requirements.
Only air conditioning inspection reports that have been produced and lodged on the register by accredited energy assessors are accepted as valid by the UK authorities. The intent is that the building operator will act on the advice and key recommendations and, by rectifying faults or by making the appropriate improvements, will contribute to the efficient running of air conditioning systems. This will reduce carbon emissions as well as building operating costs, and the resulting well-run, energy-efficient site could also save on maintenance and reduce the likelihood – and the resulting consequences – of unexpected systems failures.
Air conditioning systems and sensors interrogated and analysed by condition- based monitoring software, increasingly employing machine learning and ‘big data’, can provide intelligence on the need for preventative maintenance to reduce the opportunities for failure. In larger installations, there will be onsite maintenance teams who will work to a planned preventative maintenance (PPM) regime.
However, in many commercial applications, there will be no permanent maintenance presence, so system deterioration can still occur, remaining unobserved; this can result from the gap of up to five years between statutory air conditioning inspections or, in the absence of PPM, irregular and partial intermediate visits by maintenance contractors.
In such cases, there can be some benefit in considering enrolling a responsible person – such as the building manager, security personnel or caretaker– as an informed lay inspector who would then undertake a regular ‘strolling survey’, not only to ensure effective building operation, reduced energy use and lessened environmental impact, but also help to prevent disruptive system failures.
The lay inspector would effectively provide an additional diagnostic resource to the person who has engineering responsibility for the building, although the lay inspector would not be responsible for any rectification work. Prior to enacting a programme of lay inspection, the responsible building operator should ensure that appropriate training and checking takes place (See panel, ‘Before enrolling a lay inspector’).
Example visible symptoms of performance issues on external coils
Restrictions to outdoor airflow through the external coils will prevent the system operating at design conditions and optimum efficiency. This can lead to increased condensing temperatures, and each increase in 1K can add approximately 3% to the refrigeration energy consumption. Significant consequent increases in operating pressure can trip the high-pressure compressor cut-out that, for safety reasons, is not automatically reset but requires the manual intervention of an operator – which can potentially result in a loss of cooling for prolonged periods.
Restricted performance will commonly be caused by waste material or other items (such as packaging or tools) piled around an external unit cabinet; a shrub growing too close or too large; grass cuttings or other fora obstructing the coil; new constructions unintentionally corralling a previously well-ventilated space; and inappropriate shields being added to reduce noise breakout.
All coils will become dirty in use. As well as impeding airflow, this will act to reduce the heat transfer and adversely impact performance. The rate that dirt accumulates will be very site-dependent, but conditions can swiftly change, with unexpectedly high levels of dust resulting from sources such as local building works; agricultural processes; and climatic conditions depositing wind-conveyed sand and dirt particles.
Damage or erosion/corrosion to the coil surfaces will impact performance. This may be caused by, for example, accidental collisions with vehicles/people/falling items; chemical interaction with local pollutants; vandalism; or hailstones.
Evidence of icing or excessive standing water can be symptomatic of one of several issues including obstructed/insufficient airflow (possibly a faulty fan) and insufficient refrigerant (possibly resulting from leakage).
There are many problems that impact the successful operation of air conditioning systems where symptoms may be readily identified by a trained lay person. Most of these require observations of changes from the normal, or maybe optimum, conditions, so tours of inspection should be undertaken on a regular basis – the actual frequency will depend on the availability of the lay inspector and the size and complexity of the site.
In a small installation – for example, a small office, boutique shopping complex or health centre (typical level 3 applications) the tour of inspection might take place on a weekly or even daily basis. In larger, more complex applications, where the access issues are more demanding, it may not be feasible to undertake such frequent inspections without impacting the normal role of the lay inspector.
There are many observations that may be undertaken, some of which may be derived from the assessor lists in TM44, which require no specific engineering understanding but will require an engineer or technician to set up the scope for observations and interpret the findings. The panel ‘Example visible symptoms of performance issues on external coils’ provides an example of how simple observations of the external refrigerant coil can aid in identifying performance issues.
Lay inspectors will benefit from a simple set of information sources and relatively low-cost devices that, with appropriate training, can help inform their observations – their role being to assist in identifying deviations in normal operation that may, in turn, cause loss of performance. These may include:
- Basic performance specifications for the building environments
- Environmental meters (for example, measuring temperature, humidity, noise or lighting)
- Simple dataloggers
- Information derived from building management systems
- Bills from utilities and contractors
- Records of consumables use, such as filters and lubricants
- Building operating logbooks
- Maintenance requests and logbooks
- Patterns of staff sickness
- Building use studies and post-occupancy evaluations.
The use of non-expert inspectors is no substitute for a proper maintenance and inspection routine. More detailed information about the inspection process may be found in the CIBSE TM44, as well as in the literature provided by equipment manufacturers.
REFERENCES:
1 AR6 Climate Change 2021: The Physical Science Basis – accessed 10 August 2021.
2 World’s largest survey of public opinion on climate change: a majority of people call for wide-ranging action, UNDP – accessed 31 July 2021.
3 Hitchin, R, et al, Realisable 10-year reductions in European energy consumption for air conditioning, Energy and Buildings 86 (2015) 478–491.
4 A guide to air conditioning inspections in buildings – accessed 31 July 2021.
© Tim Dwyer, 2021.