The 2019 revision to CIBSE Guide E Fire safety engineering encompasses ‘smoke control’ as one of the engineer’s responsibilities when designing the fire strategies for a building. Writing about that revision in CIBSE Journal, chairman of CIBSE Guide E Steering Committee Martin Kealy explains:1 ‘Smoke is the major risk to occupants in a high-rise building fire. The toxic products of fire include irritant and narcotic components, so, as well as preventing escape routes from being used because of poor visibility, smoke also causes disorientation, incapacity or death.’
Successfully implemented, smoke-control design extends the amount of time available to evacuate a building safely, without occupants being overcome by the effects of the smoke. A preconception held by some is that ‘smoke control’ is a single standalone item. As with many of the design and operational aspects of delivering a successful building, however, it encompasses many elements, including a whole set of building design decisions, products, processes and procedures, installation, final test, and sign off. It might be considered as a ‘system’ in its own right, as all these areas need to work together as part of the smoke-control system, properly documented as part of a ‘golden thread’ so that the ‘original design intent is preserved and recorded, and any changes go through a formal review process involving people who are competent and who understand the key features of the design’.2 This should, ideally, be reflected in a single holistic smoke-control specification, drawing together all the requirements. Historically, however, detail has been spread across a number of areas in the documentation, including diverse sections such as those notionally covering smoke ventilation, controls, wiring, product specifications and the building’s acoustic requirements.
Smoke control has become more challenging with the increasing prevalence of complex multi-use buildings – including combinations of commercial, institutional, residential and recreational – that are reaching higher into the sky. Globally, there are many hundreds already existing, particularly in locations such as Hong Kong, New York City, Shenzen and Dubai, and it is thought8 that, in London, nearly two-thirds of the 250 skyscrapers taller than 100m (conceived, planned or completed) will include residential use.
There is already a great deal of guidance, standards and regulation on the implementation of fire and smoke products, and there is a shifting emphasis in upcoming UK legislation to ensure that there is a proper ‘whole building’ approach to building safety legislation. When designing a smoke-control system, there are several routes – all of which are likely to intertwine – that may be informed using publications such as CIBSE Guide E; state guidance such as England and Wales Approved Document B: Fire Safety,3 the Scottish Technical Handbook Section 24 or Northern Ireland Technical Booklet E5; employing information from appropriate standards such as BS 9999:20176 and BS 9991:20157 Fire safety in the design, management and use of buildings/residential buildings; or by applying a fire-engineered solution that is based on guidance from experts and institutions.
The multiplicity of guidance can, itself, obfuscate the path to an appropriate smoke-control solution.
Smoke-control design is often developed, evaluated, demonstrated and proved by modelling and computational fluid dynamics (CFD). CFD can be an extremely useful tool to assess the potential impact of a smoke-control system, which is particularly valuable when assessing fire-engineered solutions for high-rise buildings and those with complex arrangements, including extended corridors. CFD modelling of smoke movement is a specialist activity, and may be outside of the competence of the company responsible for the design – or, at least, it might benefit from being independently checked by an expert third party. As with all modelling activities, the output is highly dependent on inputs and assumptions, and outsourcing to modelling specialists – or product suppliers – requires careful consideration and information management, to ensure that the modelling activity closely reflects the designer’s intent, as well as being supported by the appropriate knowledge and expertise.
Fire engineering provides a route towards a successful smoke-control solution for increasingly complex applications; however, if smoke control has been designed and modelled before being tendered, the project tender document would benefit from including the specification as a single clear section. In some cases, details can be clouded by a general project specification that may state that the design must also meet the requirements of, for example, approved statutory guidance documents or other standards that may contradict elements of the fire-engineered solution. So, it is essential, at the design stage, to ensure the general specification does not conflict with specific details of the project’s smoke-control specification, and that the final documentation is explicitly clear.
Natural and mechanical smoke shafts are used as part of the smoke-control system to protect adjoining staircases and keep them clear of smoke by ventilating the corridor or lobby that gives access to the escape route. There are basic parameters prescribed by local and state fire regulations that encompass the fire resistance of the construction materials; the geometry of the smoke shafts; the provision of the inlets and outlets; and the restrictions on services that otherwise may share the shaft. When construction takes place, the builder may make changes to the smoke shaft ‘to fit’ the building, or possibly suggest that other services make use of the shaft, or potentially want to deviate from the specified materials and construction details. These will all create the need for a potentially significant redesign and additional costs that, depending on when the changes are realised, can impact commissioning and practical completion – a poor-quality, or leaking, smoke shaft is likely to seriously impact the commissioning effort and would probably delay building handover.
It would be appropriate to note clearly in the specification that no other services can be fitted into the smoke shaft without explicit approval, and highlight that, as a life-safety component, the specific scheduled details of the smoke shaft are critical, and not candidates for unapproved adjustments.
The required acoustic performance of smoke shafts will be determined by whether they incorporate day-to-day ventilation or are dedicated smoke shafts. When the smoke shaft is part of the main ventilation distribution, the acoustic performance would need to be considered alongside that of the ventilation system. (If solely used as a smoke shaft, the operational noise impact is practically irrelevant.) Accordingly, the specific noise criteria, as required to meet local requirements, need to be explicitly included in the specification. This should account for the regular post-occupancy testing of any fans and include appropriate requirements in the noise specification. If it is unclear, then there is a greater risk that, after completion of the main design, there is additional – or possibly remedial – action required to deliver appropriate acoustic performance. This will add time and cost to the development and, for example, if attenuators are subsequently required, there may be knock-on impacts in the system space requirements, additional fire protection and increased airflow resistances that will, in turn, impact fan performance and ventilation effectiveness.
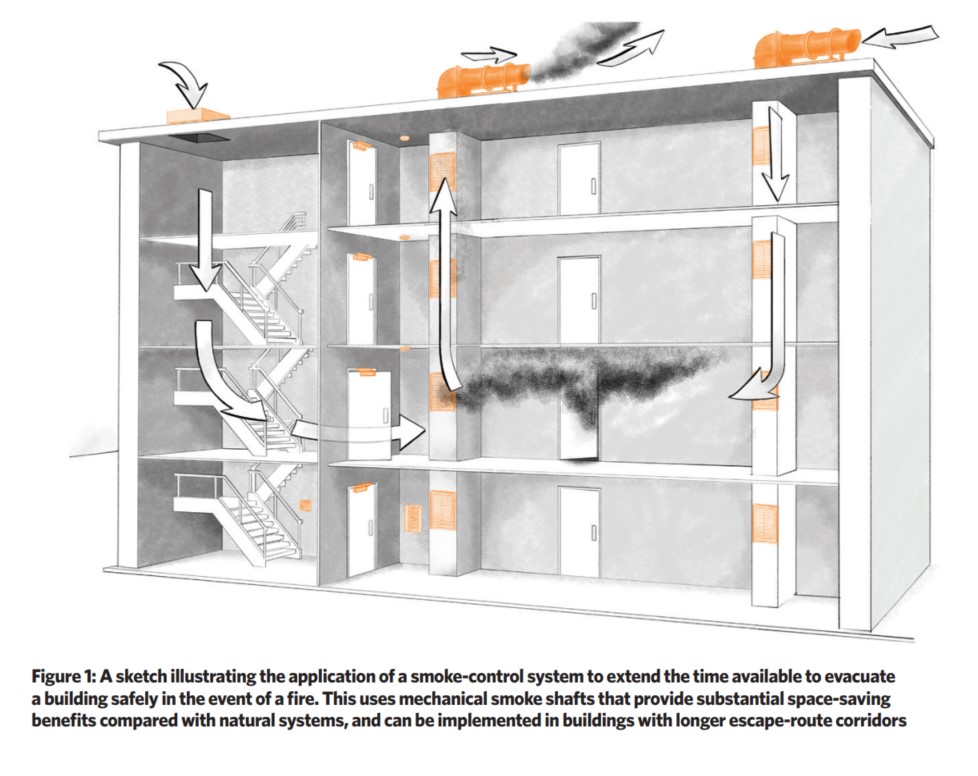
An approval process could usefully be added into the specification that ensures that the smoke shaft has to be approved, and signed off, before the smoke specialist is required on site to undertake the commissioning tests.
There is increasing use of full-height internal doors as part of the building design. As the area above the door is often used as a potential reservoir for the smoke, its unexpected absence can present a challenge when evidencing smoke-control regimes. If full-height internal doors are proposed, their use – and impact on the smoke-control regime – needs to be assessed by appropriate analysis (which would normally include computer modelling). If the client or designer changes a design subsequently to include full-height doors, it is very likely that the original smoke-control design would not function appropriately without some changes to the systems or the building, so adding to design time and project costs.
BS EN 121019 Smoke and heat control systems, divided into 10 parts, provides a suite of guidance for system components. Smoke ventilators should be designed, tested, and manufactured as a single entity to ensure compliance with BS EN 12101-2, which covers smoke- and heat-control systems. However, other guidance – notably including Approved Document B – specifies a minimum free area, which is not a defined entity in BS EN 12101-2, and this can lead to unrealistic expectations of ventilation performance in some product categories. To remove ambiguity, the Smoke Control Association10 suggests that the area used is taken as the aerodynamic free area as defined and tested characteristic under BS EN 12101-2. This is different from the geometric free area, so it is important to ensure products are clearly and correctly specified – and subsequently fitted – so that the actual clear area for smoke movement coincides with that used in the smoke-control design.
If a window is specifically employed for smoke clearance, so as to admit light during normal use and then motor open in the event of a fire, a bottom-hung window is often used, as it is safer than a side-hung window, as there is little chance of somebody falling from the window opening. However, the free-area calculation must include only the area at the top of the window opening and not the sides. An incorrect calculation of available area that includes the sides is a tempting mistake, as it reduces the required window size, which otherwise can become incongruously large. Larger windows will require a larger motor (with inherent maintenance) to compensate for the weight of the window. An alternative solution is to use a glazed louvre that has been tested to BS EN 12101 – there are many manufacturers’ options for this, such as the example in Figure 2.
When windows are being used for smoke extract, BS EN 12101 requires that a product should be tested as a complete unit, which means window and actuator together. This precludes the supply of a window from one manufacturer and a motor from another, whether fitted together on site or off-site. It is not permissible to claim, because both items are tested to BS EN 12101, that, combined, they make an appropriately tested product. The unit must be tested together and assembled in a factory-controlled environment – there are products that offer this, although they are more expensive. It is not inconceivable that the building designer may prefer the appearance of a ‘standard’ window. However, as this is a life-safety product, it should be installed as such, and so comply with the appropriate standards.
The Construction Product Regulation has a mandatory requirement that manufacturers should only market products that comply with the relevant harmonised standard. Compliance is demonstrated by the manufacturer through issuing a declaration of performance (DOP). This DOP will be based on the type-testing of the product, initial inspection of the factory production control, and continuous surveillance and assessment of the factory production control. All specifications of smoke-control system elements should ask for DOP certification. It is not sufficient for companies to claim that products are in accordance with, or designed to meet, requirements. The specification should clearly require that every manufacturer must supply appropriate product DOP documentation that should form part of the certification pack to be compiled at building handover.
Control systems are a key integrator in providing a suitable smoke-control solution. The responsibility for the complete system, particularly when on site, can be unclear. For example, it might be considered as part of packages provided by the ‘smoke specialist’ or the fire alarm company, or it might be thought to fall under the purview of those responsible for the digital building management system. The responsibility should clearly be with one named party, and the most appropriate one is most likely to be the smoke specialist.
An example of a potential consequence of the smoke-control system being specified in isolation from the building controls might result from the need to meet the requirement for the ‘form of separation’. This is the type of subdivision provided within the electrical switchboard by means of barriers or metallic or insulating partitions, ranging from ‘form one’ to the more exacting, and expensive, ‘form four’. A smoke system normally employs a ‘form two’ separation.
However, it is not uncommon that, within the building controls section of the specification, it will ask for ‘form four’ separation for other types of controls being employed on the project. The cost is typically several times that of a ‘form two’, as the whole switchboard – which includes the supply to the smoke-control systems – would have to be the more stringent ‘form four’.
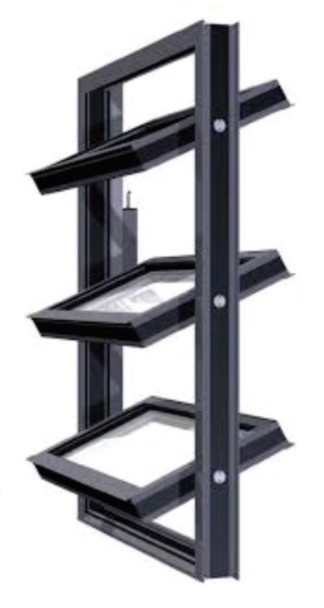
Figure 2: Glazed louvred ventilator suitable for natural day-to-day building ventilation, as well as smoke control (conforming with BS EN 12101-2
It is important to identify the necessary feedback to the supervising control system from items such as fire dampers, motorised windows and louvres, and to ensure that there is coherence between the building controls specification and that required to meet the demands of the smoke-control system. Any requirements for the provision and monitoring of primary and secondary power supplies should be explicit within the specification.
After the tragic losses of life in recent building fires, the Fire Safety Bill11 – which is currently making its way through the deliberations of the UK parliament – will change the scope of the Fire Safety Order (which covers general fire safety in England and Wales) to clarify the role of the ‘responsible person’ for maintaining the safety of building occupants. As illustrated by the examples in this article, it is critical that smoke-control design is considered with a similarly holistic approach led by appropriately competent engineers. This, in part, is driving calls for competence schemes to ensure that practitioners may be appropriately identified as being competent to develop solutions that are informed properly, and based on best procedures and up-to-date knowledge.
© Tim Dwyer, 2020.
- Developed by Tim Dwyer from practitioner experiences.
References:
- Kealy, M, Preview: Smoke control, CIBSE Guide E Fire Safety Engineering, CIBSE Journal, accessed 1 July 2020.
- Hackitt, J, Building a safer future – independent review of building regulations and fire safety: interim report, UK Government, 2017.
- England and Wales Approved Document B: Fire Safety, volumes 1 & 2, accessed 3 July 2020.
- Scottish Technical Handbook, Section 2, accessed 3 July 2020.
- Northern Ireland Technical Booklet E, accessed 3 July 2020.
- Fire safety in the design, management and use of buildings. Code of practice, (BSI, 2017).
- BS 9991: 2015 Fire safety in the design, management and use of residential buildings, BSI 2015.
- Where will London build its skyscrapers, accessed 3 July 2020.
- BS EN 12101 Smoke and heat control systems, multi-part document, BSI.
- Guidance on smoke control to common escape routes in apartment buildings (flats and maisonettes) rev 3.1, Smoke Control Association, July 2020.
- Fire Safety Bill 2019-21 (England and Wales), accessed 3 July 2020.