Offsite fabrication has been the norm in many industries where ‘just in time’ supply chains allow the construction of near-identical complete products, making savings through: reduced holding of stock; smaller warehousing requirements; reduced waste; improved recycling of materials; faster response to innovation; and lower cost. But, of course, the building services world has historically had its roots firmly based in delivering a bespoke system, created on site to meet an often imprecisely defined building shell – potentially where prefabrication would have been impractical (and require significant site adjustments) or impossible. However, with improved building definition earlier in the design phase, offsite construction is becoming increasingly common – for example, with ductwork fabrication; pre-assembled and pre-wired pump sets; bathroom pods; pre-assembled and pre-wired fan coil cooling units with controls; integrated boiler/control/piping assemblies; and complete boiler plantrooms.
Offsite construction – the part of the construction process that is carried out away from the actual building-site location – is a growing sector, with rapidly changing technology. It now accounts for at least 3-4% of the UK construction sector and can represent up to 80% of the construction cost for some projects.1
Investigations undertaken by the Waste and Resources Action Programme (WRAP)2 – as reported by BESA1 – indicate that the material waste on a typical ‘conventional’ construction is 10-times that of an industrialised factory, and that factory CO2 emissions and embodied energy for the same built process can be more than 55% lower.
Offsite symbiosis
A key benefit of intention to use offsite construction methods is that it converges with the timescale introduced with projects that are delivered using the concepts associated with building information modelling (BIM). It is widely acknowledged that for BIM to deliver benefits throughout the construction process, the design must be brought further forward in the overall process than has been traditionally the case – this is also often a prerequisite for successful offsite prefabrication. As offsite construction will inevitably bridge disciplinary boundaries – for example, mechanical, electrical, lighting, civil, structural and architectural – it, by necessity, promotes multidisciplinary working.
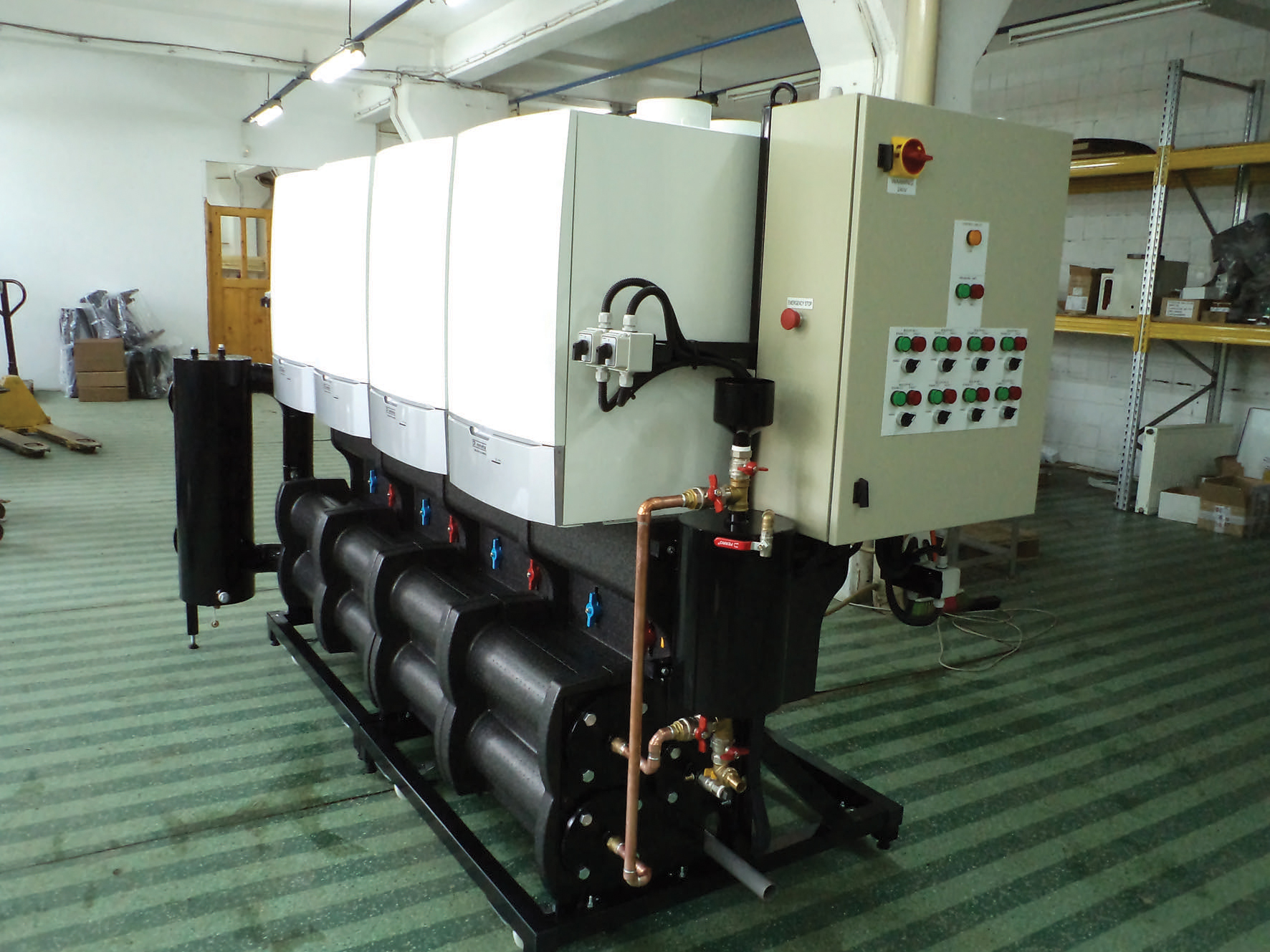
Figure 1: A fully assembled boiler skid including controls delivered to site
The enhanced planning and collaboration delivers productivity gains on and off the site, and reduces the dependence of site supervision and high-level site skills. This can increase site productivity, as well as enhance the quality of installation – thereby reducing subsequent snags and consequent maintenance issues.
Effective use of offsite construction requires a programme rather than a project-management approach, as strategic resource management across the various work packages is essential to achieve a common aim. It is a more holistic and strategic approach that integrates the supply chain within construction. For a successful implementation, manufacturers and installers need to be consulted at the design stage, because the earlier in the process offsite construction methods are specified, the greater both the time and cost savings, and the environmental benefits. For example, insulation and surface protection can often be added in the factory rather than on site.
Reduced time on site is a major benefit, and savings in the range of 50-75%1 have typically been reported. The number of people working on site at any one time is also reduced, giving a potential total reduction in site hours of 60-80%.1 Programme certainty will be improved, because of the removal of some of the site-based uncertainties, with reduced abortive work and defects, prelims and site overheads.
Offsite applications can be categorised in many different ways and, when considering the mechanical electrical prefabricated assemblies, a term that is often adopted is ‘non-volumetric preassembly’3 – such as the domestic hot water pressure booster ‘skid’ of Figures 1 and 2 – where the factory-assembled system is not considered as enclosing usable space.
A prefab culture
For offsite to succeed, there must be timely supply-chain engagement, and collaboration between consultants, contractors and manufacturers. Some may be unwilling to commit to offsite delivery at early design stage, as they are not sure that this approach will be cost effective. Comparison cost advice on traditional versus offsite is not readily available to inform early decisions, so it is important for clients, designers and contractors to understand that designing for offsite delivery does not preclude traditional construction, while the opposite may not equally apply.
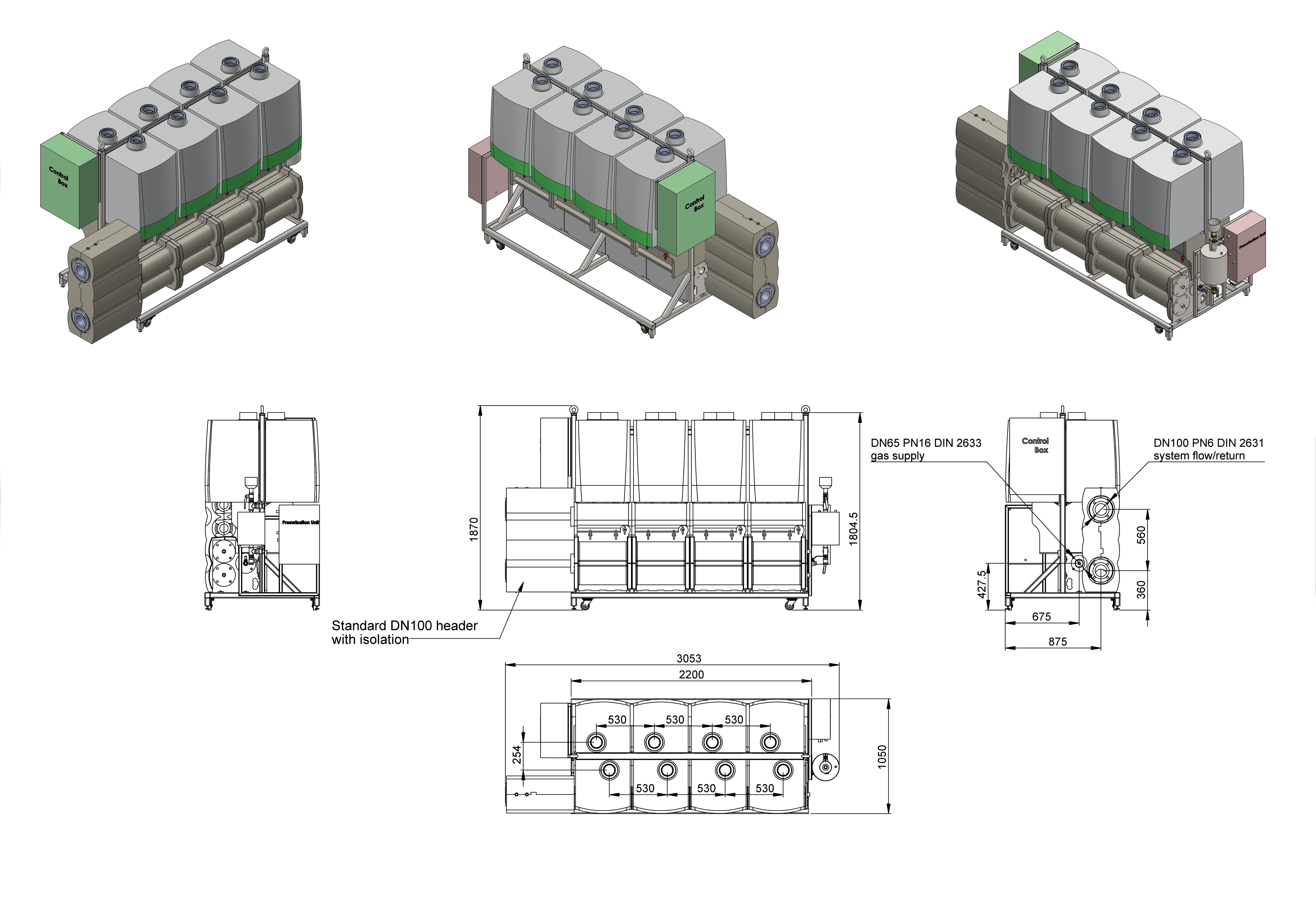
Figure 2: The model and construction drawings for the boiler skid for figure 1
Traditional design processes tend to result in the late development of building services designs, not allowing adequate time for detailed design before fabrication. A late decision to adopt offsite solutions can lead to inappropriate procurement strategies, such as the lack of consideration for how the building services packages are going to be delivered early enough in the design process. A procurement strategy that separates elements of building services into packages may, for example, prevent the delivery of offsite solutions where a number of services that share the same physical zone are split between distinct supply packages.
Designs need to be completed and set at an early stage to allow effective use of offsite construction. Late design changes or variations could have undue cost and time consequences that can outweigh the benefits of using an offsite approach.
Refurbishment projects do not preclude this approach. However, modules are likely to be smaller, as they will need manoeuvring through existing structures. At a basic level, even premanufacturing small subassemblies – such as boiler/control/valve sets and support bracketry – can provide significant benefits.
Healthy and sustainable
The reduced time on site is also likely to reduce accidents; in manufacturing, accident rates are 29% less for major injuries and 52% less for fatalities4, so if construction were to become more like a manufacturing exercise as a result of the widespread take-up of offsite methods, there could be a reasonable expectation of a significant reduction in recordable incidents.
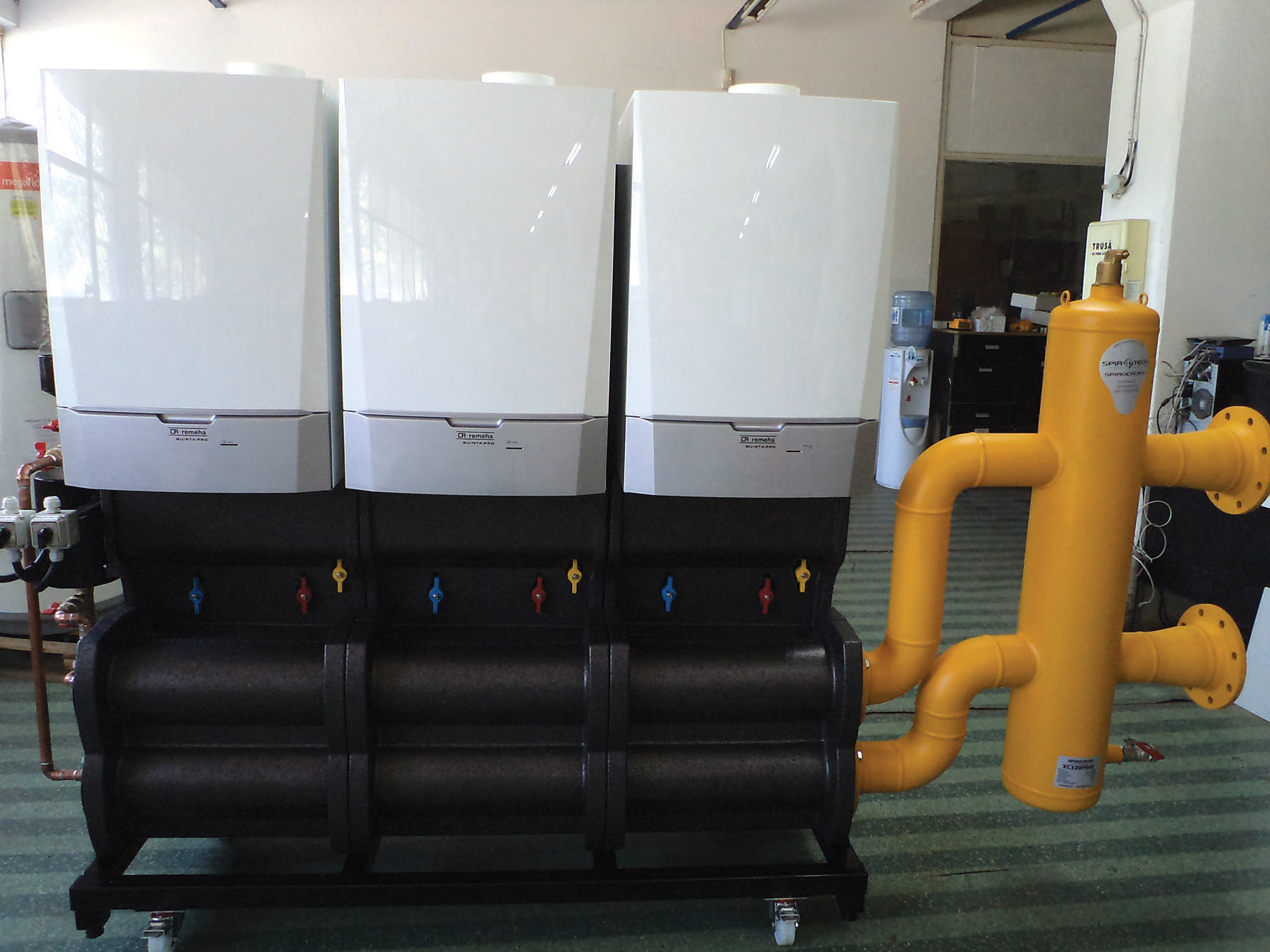
Figure 3: The packaged boiler skid
Offsite can provide cleaner work conditions, with lower risk of trips, slips and falls, particularly as working at height is reduced. Manual handling and lifting is reduced too, as materials are mechanically moved to the safe, controlled, weatherproof production space. The factory environment can be properly designed, with purpose-made workstations, appropriately maintained protective equipment and the correct tools to hand, rather than working in often confined site spaces. As there will be a reduced need for onsite commissioning, the risk of electrocution, scalding, and other injuries is reduced, with appropriately controlled sources of heating, power, air and water for testing being provided at the factory workstation.
Offsite production is reported to deliver a significant reduction in waste compared to traditional construction. Fewer components need to be delivered to the site, so there is likely to be a 60%1 reduction in vehicle movements, as one truck that can contain substantial prefabricated, complete modules is equivalent to around 38 white van deliveries. The impact on the local environment – both on the site and within its environs – is reduced, as there is less packaging, noise, and general emissions. These will have been moved back to the ‘factory’, where the scale of production will allow for far greater efficiencies in environmental control measures, materials and staff management.
Handling and installation
Large prefabricated sections require heavy-duty cranes and precision handling to be placed in position. The predictability that offsite brings enables better planning of site activities, including the equipment and timing required for installation. With good planning, the use of heavy equipment – as well as other specialised tools – can be adopted with greater efficiency. The availability of the type and capacity of cranes and other lifting devices will vary through the project programme, and be affected by site constraints.
Integrating services modules into the main construction programme can take advantage of tower cranes’ increased site coverage and capacity. This will provide the opportunity to allow multistorey riser modules that – when used with temporary (removable) roofing and weather-protection systems – can even be craned in after the main structure is completed. The structural loading of floor and roof slabs needs careful consideration, as modules are routed into position. Roof plantrooms are usually completed after tower cranes have been removed, and can use mobile or crawler cranes. The space between the building’s structural components may determine the maximum size of prefabricated modules that may fit safely without risking damage to the plant or the building. So, for example, incorporating a boiler header assembly in two parts may allow it to be included in modular plantrooms rather than being built in situ. The packaged boiler and domestic hot water (DHW) module of Figures 3 and 4 can be separated on site, so that it can be moved through standard door openings.
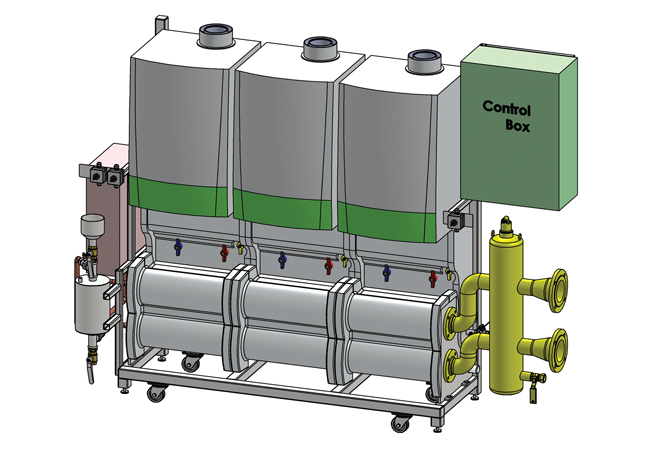
Figure 4: The model of the packaged boiler skid
In the increasingly collaborative environment being encouraged by BIM, computer models can be developed in such a way that the offsite modules are individually brought into the model in the sequence that the construction process intends. BIM can drive the project plan and visualisations of module deliveries and installation, which might include crane operations and tracing the route that modules will take through the facility to reach their final destination.
Commissioning and operation
While distribution systems will need to be connected on site before they can be commissioned, more complex plantrooms and passenger-moving systems may, largely, be commissioned before delivery. For example, pumps can be run/flow-tested on test rigs, and controls can be proven. It may be feasible to start commissioning on a zone-by-zone basis once sufficient modules have been installed and the building envelope is made weather-tight. Offsite manufacture in a controlled environment enables the supplier to maintain the cleanliness of pipework, reducing the need for flushing during commissioning. With modular wiring, it is advisable to test the whole system once connected, rather than its sub-elements.
Cost savings
The biggest financial benefits can come from the shorter construction programme that should be achievable with offsite construction, giving reductions in financing costs as well as delivering greater control over the cost of equipment. For example, the flow diagram of Figure 5 indicates a process that takes just five weeks – from initiation to delivery and commissioning – of a tailor-made offsite modular boiler skid, incorporating headers, controls, pumps and primary pipework.
The storage required on site (and its inherent costs) will be reduced, as modules can be delivered directly to their final position. Significant cash-flow benefits can arise from early completion and, consequently, early occupation. This can also offer considerable financial benefits for clients, as early guaranteed handover and occupation could be crucial in sectors where business is time-critical, such as airport, healthcare, educational or retail buildings, where site availability, or space for storage, may be limited. Offsite is likely to improve cost certainty and reduce risk – both in terms of time and cost – and if the same module can be repeated across a project (or multiple projects), this will benefit capital expenditure (capex) and operating expenditure (opex), as the modules can be more readily integrated into the operation and maintenance procedures.
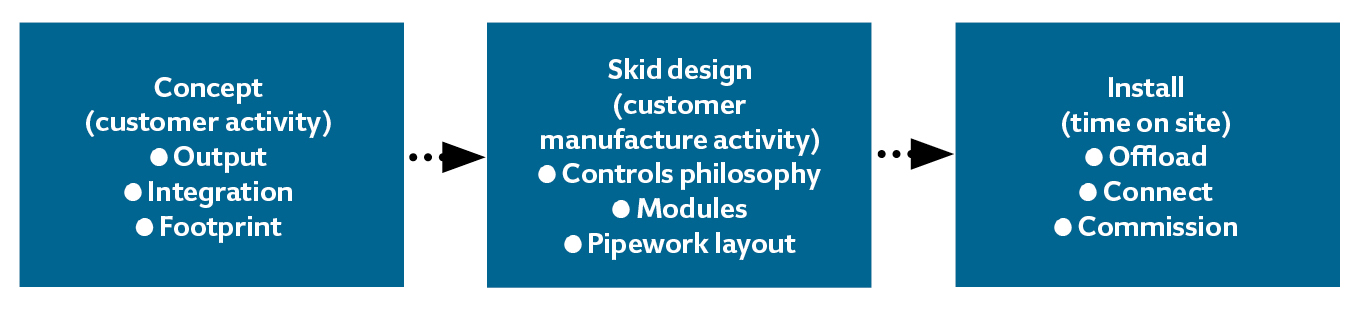
Figure 5: An illustration of a five-week process to deliver a prefabricated boiler assembly to site (Source: Remeha)
The financial benefits may not always be obvious – for example, an airport operator, by adopting offsite prefabrication, aimed to take 80% of the mechanical and electrical labour offsite, as security checks were taking up to two hours at peak start times.
Maintaining a close collaborative relationship between consultants and the manufacturers can achieve great improvements in productivity, by optimising offsite solutions through innovations in manufacture and site operations – including product and process standardisation, mass customisation and continual improvement. ‘Documentation’ – through BIM-enabled links or in traditional digital or paper format – for handover can be rather more precisely developed for modules that can then enable improved facilities management and enhanced life-cycle operation.
© Tim Dwyer, 2016.
Further reading:
Limited guidance has been produced relating to offsite for the building services industry. BESA, however, has an offsite guide1 that has been used (with permission) as the foundation of this article – and where data and information is quoted without further reference, it will have been drawn from that publication. The buildoffsite website (www.buildoffsite.com) has several useful publications, including Offsite Construction: Sustainability Characteristics and Building Offsite – An Introduction.
References:
- An offsite guide for the building and engineering services sector, BESA (formerly B&ES), 2015
- The Waste and Resources Action Programme
- Gibb, A, Offsite Fabrication: Prefabrication, Pre-assembly and Modularisation, Wiley 1999
- Krug, D et al, Offsite construction: Sustainability Characteristics, buildoffsite, 2013