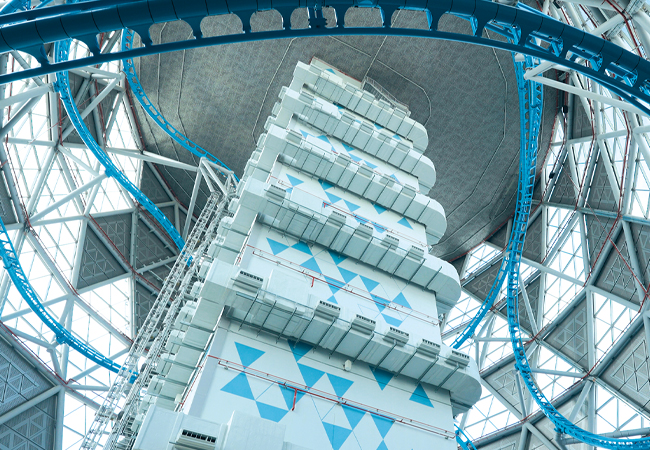
The AHU stack has a staircase and lift so maintenance teams can access the upper track
Dubai has so many retail malls that anchor attractions have become an essential accessory in competing for the attention of the shopping public. The Mall of the Emirates, for example, has an indoor ski slope, while an aquarium and indoor ice rink can be found in the Dubai Mall. Now, the Dubai Hills Mall has opened, and its novel attraction is a spectacular indoor rollercoaster.
Looping a rollercoaster through a building in the heat of the Arabian Desert meant maintaining a comfortable indoor temperature was fundamental to the success of the project. ‘Indoor rollercoasters of this magnitude and speed are very rare, so there were no defined environmental design criteria. Fundamentally, our approach had to be about the user experience,’ says Richard Stratton, partner and managing director Cundall MENA, the lead design consultant, with responsibility for MEP, architecture, structure and lighting.
Called The Storm, the rollercoaster features a 670m long track, coiled to fit inside a cylindrical building measuring 44.5m in diameter and 62m high.
Designed by rollercoaster specialist Intamin, the ride lasts one minute 20 seconds. It starts with a thrilling vertical launch; in just five seconds, a linear synchronous motor propels a 12-person car from below ground to the top of the ride, 50m up. From here, gravity pulls the car earthwards, round a twisting, turning track and back to a ground-level station.
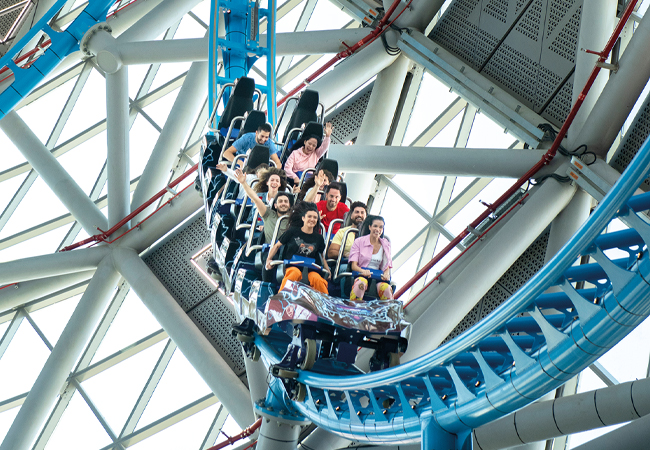
The cars are propelled 50m to the top of the ride, before gravity speeds them back down to ground level
The circular building that houses the rollercoaster is supported on a diagrid of tubular steel, a rigid structural exoskeleton. Impressively, Cundall’s engineers have designed the structure to support both the building and the rollercoaster track, so it can deal with the conventional building loads and the dynamic loads imposed by the two cars and their passengers hurtling around the track.
This diagrid is clad in a combination of triangular, composite-insulated aluminium panels and solar-controlled, vibration-isolated double-glazed panels. The glazed panels are positioned in line with the track, to give passengers views out, while the solid panels reduce solar gain. The building is capped by an insulated standing seam roof. To enhance the ride experience, the solid elements of the walls and roof incorporate an acoustic lining, helping to absorb sound.
‘There is almost 9,000m2 of building envelope for the roof and the façades, which equates to a peak cooling load of about 1.35MW,’ Stratton says.
While the building is partly shaded by the adjacent mall, in unshaded areas the fabric heat load peaks at about 300W·m2, with an average heat load of approximately 155W·m²
To enhance the experience of the ride, solid elements of the walls and roof incorporate an acoustic lining, helping to absorb sound
The launch system and rollercoaster equipment add another 255kW to the total, while lighting, fresh air and people loads add a further 290kW. ‘You can see that the fabric load is the main driver for cooling, but it’s also the biggest variable because, in the evenings and during the winter, the vast majority of the load will disappear completely,’ says Stratton.
The client initially wanted to maintain the interior at 24°C, the same temperature as the mall’s retail spaces, but this would have required a significant amount of cooling. Instead, Cundall successfully argued that temperature control within the space could be relaxed, as the rollercoaster equipment is either direct liquid cooled or housed within contained equipment rooms. Examples of external rollercoasters in the United Arab Emirates that operate through peak summer conditions with only the loading/unloading areas enclosed were also highlighted.
Stratton says: ‘Relaxing the temperature allowed us to be more creative with temperature gradients and humidity levels within the ride volume, so we could focus more on building needs to avoid condensation and large temperature variations and less on people needs’.
Cundall MEP’s solution was to concentrate on what Stratton refers to as ‘a temperature gradient arrangement’. This sets out to maintain temperatures of 24°C in the basement, where the maintenance team is based, and at ground-floor level, where the ride is boarded. Above the occupied zone, the temperature is allowed to increase gradually, to a peak of 30°C beneath the roof.
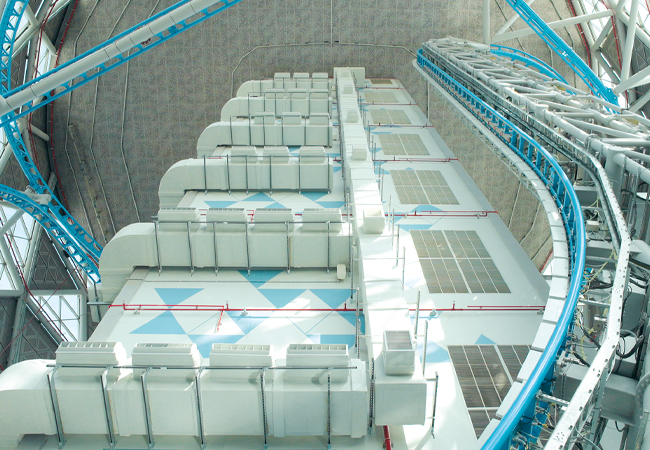
The temperature gradient approach leant itself to a displacement ventilation solution. This would have worked ‘in principle’, says Stratton, but there was insufficient space at the base of the building because of the track, station and other ride demands.
Instead, Cundall made use of the building’s central core to house a stack of air handling units (AHUs). This non-structural element was needed by the maintenance team to access the upper levels of track, and includes a staircase and lift. The core’s six floors now house a series of double-stacked AHUs, mounted one above the other.
Maintaining the coaster clearance zone was critical, so HVAC distribution is confined to the core. Only electrical cabling and containment was coordinated with the track and either followed the track route or was confined to designated containment routes. BIM 360 was employed throughout the design and construction to facilitate coordination and integration of the various building and track elements.
‘If you consider the building in plan as a doughnut, the solid part contains the ride while the central section contains all the plant and equipment,’ explains Stratton, who describes the air supply system as ‘simple’.
Allowing the temperature to rise from 24°C to 30°C at the upper levels reduced energy demand by 11%
The supply air duct leaves each AHU and immediately wraps around three and a half sides of the core. The duct incorporates drum louvres to blow cooled air 16m from the core towards the façade, which is where the bulk of the heat is generated. ‘The drum louvres allow a bit of flexibility in where we direct the airflow and help create a bit of mixing, which is enhanced by the turbulence from the car charging through,’ says Stratton.
Varied in capacity, the AHUs are typically between 4.5m3·s-1 and 7m3·s-1, based on vertical location and heat load. The overall supply air volume is 81m3·s-1, which is sufficient to deal with the diversified load. Stratton says supply and return conditions are ‘pretty standard’; the supply is 13°C, with the return air temperature dependent on where on the building’s vertical temperature gradient unit is located. Stacking the AHUs vertically enables the system to control the rollercoaster space air temperature in horizontal slices. Variable speed drives enable the supply air volume to be increased or decreased to regulate the temperature of each slice. ‘The beauty of this solution is that you can change the setpoint of each slice to play with the temperature gradient,’ explains Stratton.
Adopting a strategy that allows the temperature gradient to rise from 24°C to 30°C at the upper levels reduced energy demand by approximately 11%. To lower energy demand further, operators could let the temperature in the upper portion of the building rise to 40°C, which, in the cooler months, would mean ‘they would probably only need to condition the lower levels’, says Stratton.
The heat-load modelling carried out to establish viability of the layered approach meant that computational fluid dynamics modelling was not needed to predict airflows. Stratton says Cundall did not worry too much about rider comfort from an air-mixing point of view. ‘The main thing was that there was a bit of air mixing and a bit of flexibility to control the direction of the air.’
All of the space conditioning AHUs operate on 100% recirculation. In a clever piece of coordination, the vertical AHU return air grilles are stacked adjacent to the ride’s vertical launch. The launch system is liquid cooled by packaged cooling units provided by the rollercoaster supplier. The proximity of the return air grille ensures that heat rejected by the system is sucked immediately into the AHU before it can enter the space.
Internal lighting is themed and coordinated with the ride; external lighting is focused for attraction and branding…
At the top of the AHU stack is small fresh air supply unit. ‘Fresh air is not a big issue because there are only about 40 people inside the ride area,’ says Stratton. The unit pulls fresh air into the space from an intake on the roof, based on an allowance of 15L·s-1 per person in rollercoaster space. Stratton says humidity is ‘managed’ by the fresh air system; ‘because this is not a close-control environment, we don’t need fine control’.
The rollercoaster building is illuminated by four kilometres of linear strip LED lighting. Cundall was responsible for designing the lighting scheme for the inside and outside of the building. Internal lighting is themed and coordinated with the ride; external lighting is focused for attraction and branding, and is customisable by the operator. ’There is a day and night experience, with the lighting designed to enhance the experience at night,’ Stratton says.
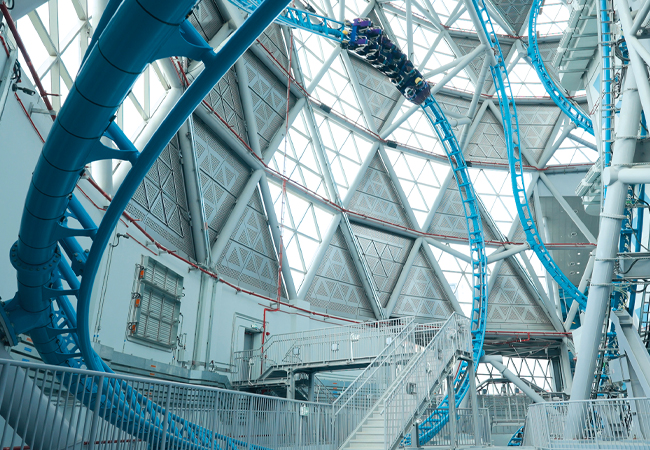
The circular building housing the rollercoaster is supported on a diagrid of tubular steel
Cooling, power and other utility services are all from the mall’s centralised energy systems. ‘All energy provisions are from the mall, so we had to ensure there was enough capacity in the district cooling, power and other utility services, such as fire protection systems.’ Fire protection, firefighting and water services all extend from the mall central systems. Cooling is from the mall district cooling system based on a peak cooling load of 1.66MW.
Because of the magnitude of peak electrical loads, the associated operational harmonics, and compliance with local electricity regulations, a dedicated sub-station had to be constructed directly adjacent to the rollercoaster building.
Passengers start their journey in the mall, where they buy tickets and enjoy a short audio-visual show. From here, they pass into the main building, ready to be thrilled by the ride and not by Cundall’s clever environmental control solution. ‘If people are worrying about comfort conditions, that probably means the rollercoaster is not very exciting,’ says Stratton, who knows this is not the case, having been on the ride three times already – just to make sure!